Dashpivot article – Are toolbox talks required by OSHA
Are toolbox talks required by OSHA?
This article answers the question, "Are toolbox talks required by OSHA?" and explains why they’re a key part of workplace safety. You'll also find a number of free and usable resources in the article to improve your toolboxes.
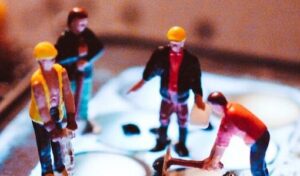
Does OSHA require you to run toolbox talks?
If you are doing toolbox talks in your company regularly then it is likely that you are with an employer who cares for your safety and health in the workplace, and if you’re here to verify if toolbox talks are done for the compliance of Occupational Safety and Health Administration (OSHA) standards, then we will save you the time and give you the short but slightly complex answer – it is not explicitly required by name– meaning that while the principles of toolbox talks are there it doesn’t have to be ‘Toolbox Talk’. Toolbox Talks have been around as a regular practice in the workplace because more and more companies are seeing its benefit in terms of incident prevention and it gets the workers more involved in safety initiatives in the workplace.
Let’s deep dive on what we meant by not explicitly required by name and what does OSHA require anyway? OSHA under ‘Safety and Health Regulations for Construction 1926.952 requires Job briefing which essentially is like toolbox talk, it is requiring all employers to provide the employee in charge of the job with all available information that relates to the determination of existing characteristics and conditions required or ‘job briefing’. According to OSHA, job briefing should cover at least the following subjects: Hazards associated with the job, work procedures involved, special precautions, energy-source controls, and personal protective equipment requirements and should be done before work begins to an extent of having a short or detailed discussion which is quite similar to toolbox talk. Therefore, when companies are doing toolbox talks, they are also complying to the OSHA standards of employers providing job briefing to their workers.
However in this article, we are targeting that you would see toolbox talk beyond just for compliance but also acknowledge it as a safety practice by recognizing its potential impacts to the work and if there are areas in your toolbox talk that needs improvement we will give you recommended ways on how to make it more engaging.
Impact of Toolbox Talks
It is already an advantage that running toolbox talks in your companies is complying to OSHA in a way, but Toolbox Talks is more than that. Toolbox talk is essential and important and if done right, toolbox talks are able to achieve much impact to the team. How? The following are how toolbox talks are impactful to your industry:
Toolbox talks help the workers comply to safety policies
In a case study, to a steel shop company that has never integrated toolbox talk in their safety program, after 5 weeks of regular toolbox talks before starting their work, workers are seen to be diligently wearing their personal protective equipment properly like dust masks, face shields and protective clothing. Because of the toolbox talks workers became much more aware of the threat of dust and how it can affect their bodies, causing most of the workers to start wearing respirators. Toolbox talks enables the worker to follow safety policies not forced or scaring them with sanctions for not following but because it emphasised that it was done for their safety it’s easier for them to follow. In this case, there can be safety trainings or job briefings annually or when they first started working a few years back but toolbox talks are able to create an impact because it’s a daily talk to the workers.
Toolbox Talk gets your workers to talk
When designing safety measures in the workplaces, how many companies have actually cared what the workers think? It might be that they would imagine workers would just comply because it’s for their safety anyway right? But on a much conscious approach, if you’re designing a safety program – get your workers to talk. And, toolbox talk is a way to do that sure, it might be awkward at first, you might get a nod and a respond of “all good, no questions” but have you heard about “repetition is a mother of learning”? Because toolbox talks are designed to be more frequent and ideally done daily, it means when we keep doing these talks it would eventually get them to learn and talk about it.
Toolbox Talk improves employee morale
Simply put, holding toolbox talk gives the impression “if my supervisors kept asking what do I think, he cares about the work that I do” and this would make Toolbox Talk go beyond just for compliance because it improves employee morale and therefore impacts the working improvement. The regular informal open discussion and communication reinforces a positive safety culture because when the employees raise a question or address a safety concern, the avenue itself would make them feel valued and heard and don’t we all appreciate that? Added advantage is that it is also a great way to update if there are any changes on the working condition or site since the last shift which would minimise miscommunication among workers.
Five effective ways to make toolbox talk more engaging
If you’re in a position to do toolbox talk to your team and find it difficult to go around with and can’t see the impact yet perhaps the toolbox talk you’re doing is not engaging. We also acknowledge that toolbox talk can be ineffective especially if it’s not engaging to your workers and when this is the case, workers are not able to open up, share their thoughts and the effects of good communication like improving employee morale will also not be observed.
There are many reasons why toolbox talks are not engaging, it could be because of the poor delivery, or that it is too long and took too much time that there’s not much time to ask and answers questions, or it can be that it has irrelevant topic or that the document itself is not well prepared. In the following, we narrowed down to 5 ways to make it more engaging:
- Make it short and focused – toolbox talks are designed to be short, it’s supposed to last less than 15 minutes but if you’re spending more than 30 minutes of the time of your workers, then that’s probably not toolbox talk, especially if you’re the only one talking. Toolbox Talks should not be treated as a safety seminar where you need to cover everything having no room for discussion, in the first few minutes share the first topic then ask workers what they think.
- Hold a better delivery – toolbox talks can be formal but it’s mostly informal to have the workers be more comfortable in that short time you get to discuss with them a safety topic, so it’s important that you consider your method of delivery, this could be that if you convey a topic like ‘safe lifting techniques’ try demonstrating it rather than just saying it.
- Avoid repetition – When selecting toolbox talk points, resist the urge to repeat the same topic every day, of course you can choose topics required by OSHA and you can be more intentional about this by observing on site and then the next day talk about your findings like if you noticed an unsafe condition, talk about why it’s unsafe. Integrate as well in the toolbox talk recent changes in the workplace to get your workers up to speed ensuring a new topic the next day. This can make your workers look at toolbox talk as a helpful time to get updated and would increase their interest to engage.
- Include your workers – one of the best ways to make it more engaging is ensuring there is a time to shine for your workers, you can have them take turns in demonstrating and discussing. You can also have them inspect PPEs and discuss their findings. This makes the toolbox talk more engaging and not intimidating.
- Plan ahead by preparing a better format – the format of toolbox talk should not be neglected. OSHA has suggested safety topics and toolbox talk ideas but also considering the 4 other items above, this must be well planned in the form to ensure it’s engaging and considerate of the time.
With all this pointed out, take a look at this toolbox talk form pre-built below. This toolbox talk was designed and sectioned with all the necessary parts, you can customise it to your liking and according to the additional topics you might want to include.
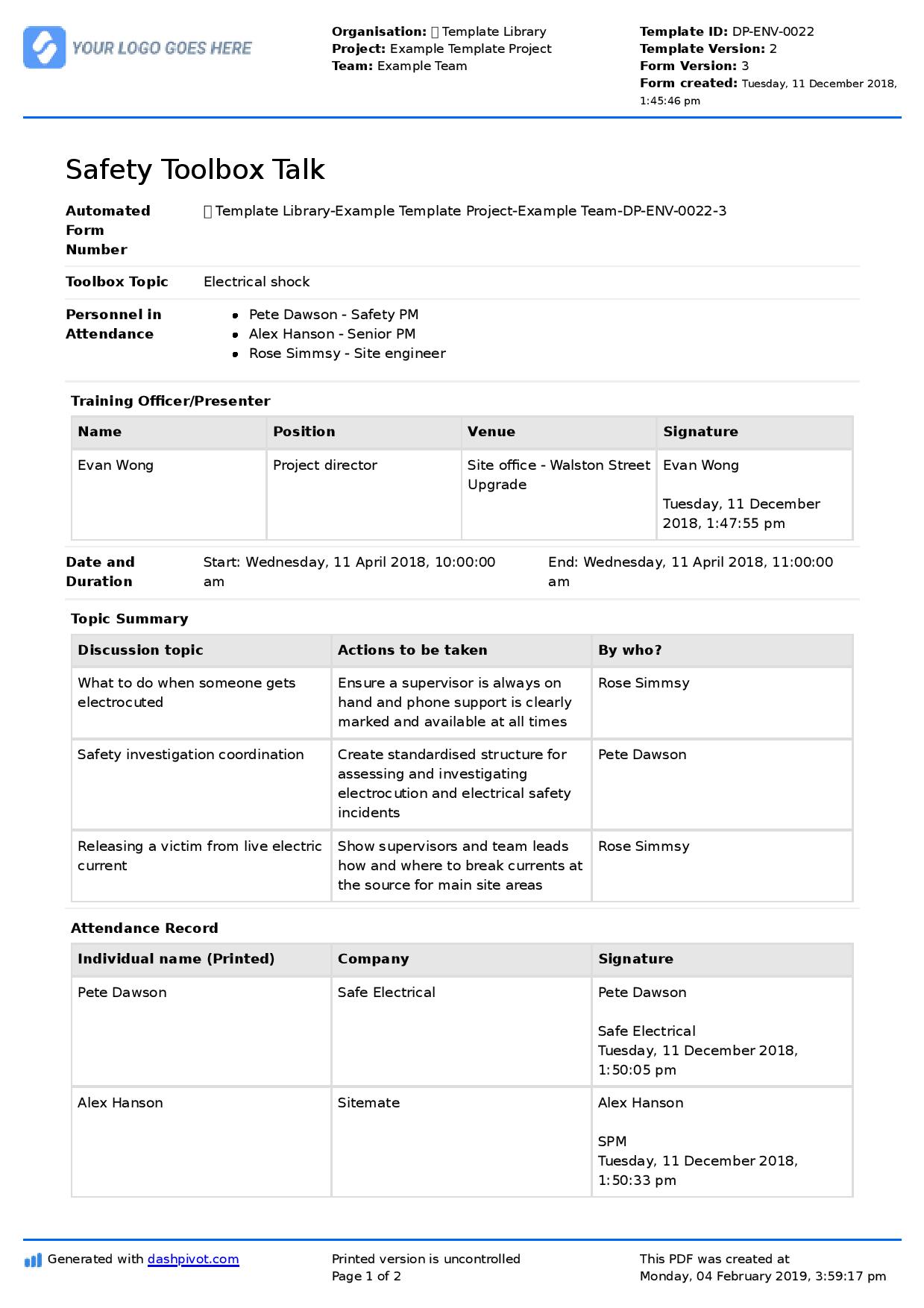
Use and customise this digital toolbox talk template for your OSHA-compliance
Standardise your digital toolbox talks for easy OSHA compliance
While OSHA might not require you to do toolbox talk specifically, you can develop toolbox talk according to OSHA standards and with that it would be great to transition to digital toolbox talks. Upgrading to digitise toolbox talk would get you to achieve the 5 ways to get your team engaged.
How digital toolbox talks can help your talks more engaging
Wrapping up this article with a final recommendation: As a project manager or presenter you might dread the idea of holding a meeting especially with how busy you already are and with the 5 ways presented above, it might be a little overwhelming and requires too much effort, right? So, we suggest using a digital toolbox talk instead that is using a toolbox talk app. Yes, there is one and it can help you plan ahead and prepare a better format rather than printing toolbox talk every day you can access your toolbox talk with your phone or tablet – and can check that one off your list. Also, if you need to update the format, add topics to avoid repetition and also integrate an OSHA compliance topic to hit two birds in one stone, digital toolbox talk would be a convenient tool for you since you will be using the best software that you can easily customise your previous form and that has a drag-and-drop feature to add sections like notes, photos. The good news is that it’s all stored up in the cloud, making it easy to access and trace to purposes like evidence of compliance for OSHA or relevant audits or even reviewing discussion points for incident investigation. This will greatly affect your efficiency in holding toolbox talk and help you make it short and focused. Do you want to know one of its best feature? This toolbox talk form would get you to do your attendance as quick as scanning a QR code making it contactless and fast – yes, there’s no need to have the team line up and sign off. So what are you waiting for?
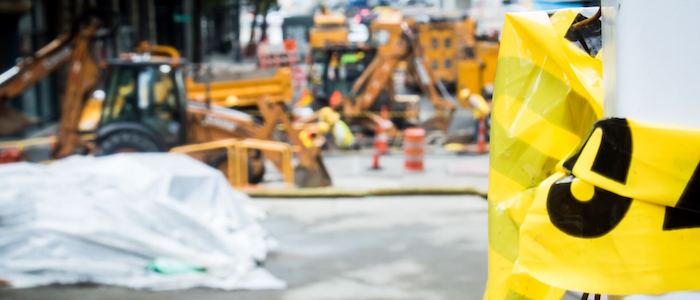
OSHA form 300 and 300a template
Maintain your log of injuries and illnesses and your 300a summary with this free template.
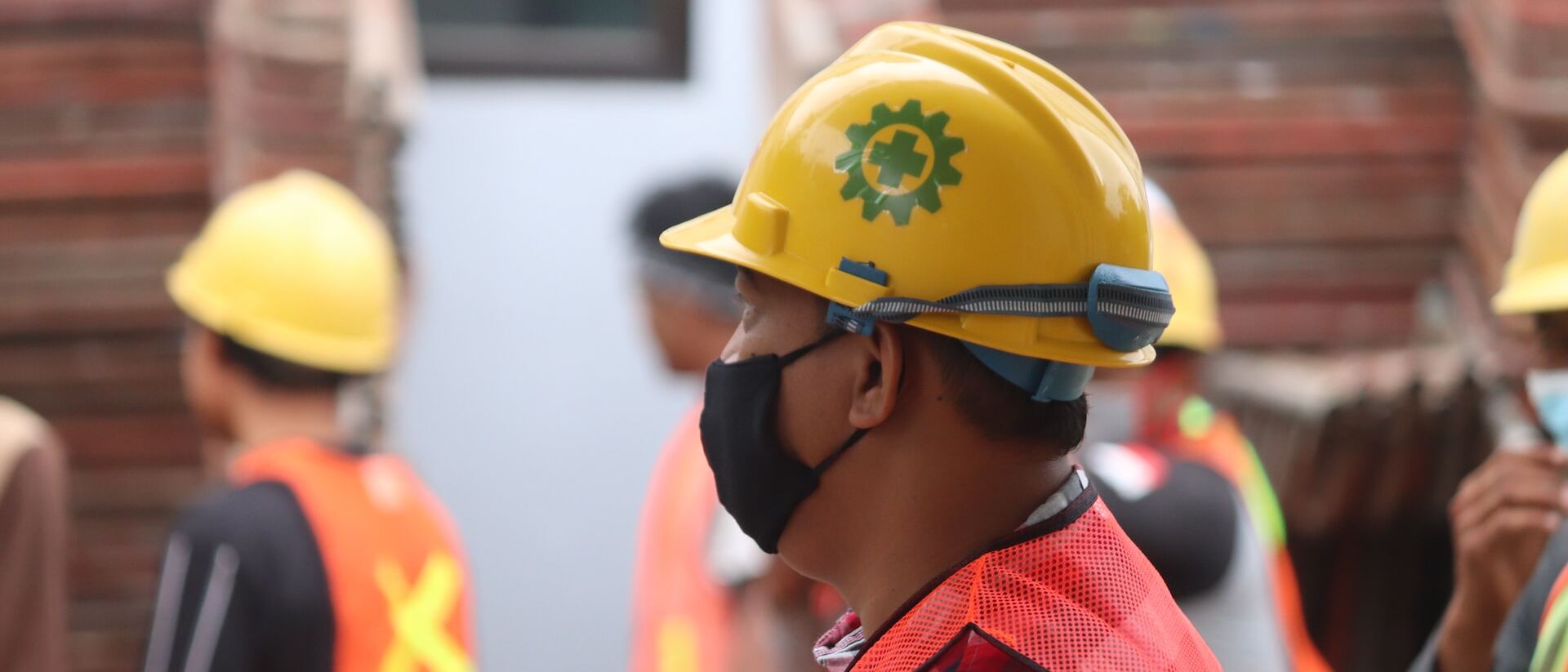
OSHA Job Hazard Analysis template
Ensure you're meeting OSHA regulations with the OSHA JHA template.
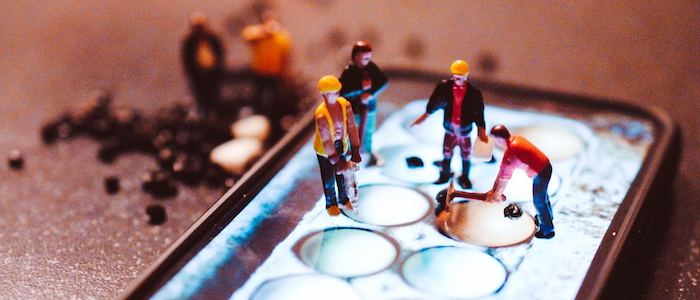
OSHA Incident Report form 301 template
Properly document your injury and illnesses on site with this OSHA Injury and Illness Incident Report form 301 template.