Corrective Action Report Template
Start with a free 30-day trial. No credit card required.
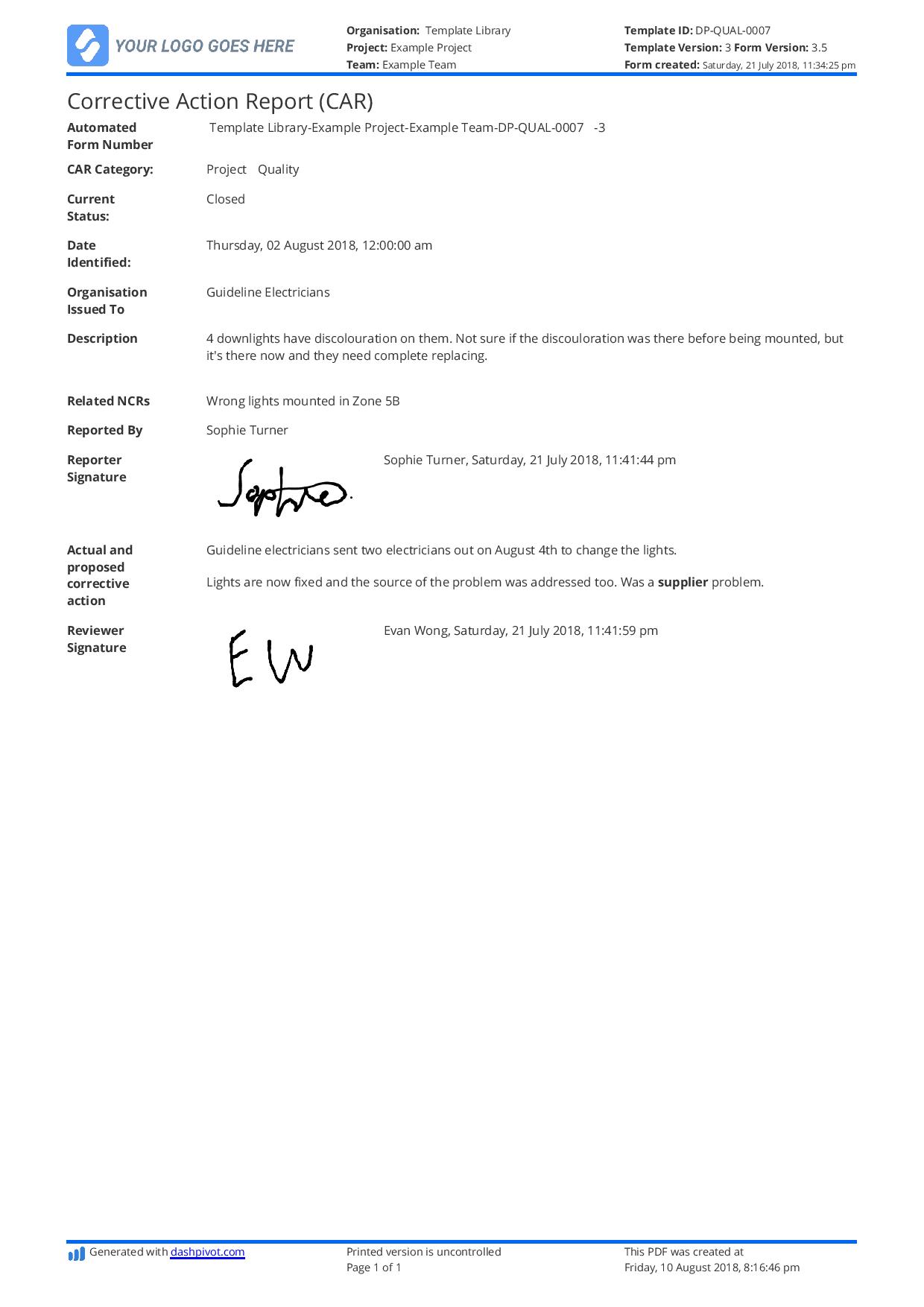
~10,000 employees
~500 employees
~25,000 employees
~20 employees
~50 employees
~1,500 employees
~20 employees
What is a Corrective Action Report (CAR)?
A corrective action report outlines the remedial actions necessary to rectify whatever has gone wrong or will likely go wrong as per the current situation during construction.
A CAR can be created by the contractor or demanded by the client. Its contents will differ depending on the observations made and the discrepancies selected for mandatory correction. Here, non-conformity is when a product or service does not conform to a certain specification of the prescribed standards.
Compare this digital Corrective Action Report to Word Doc, Excel, and PDF formats
Use this Corrective Action Report Template for free.
Why do companies need Corrective Action Reports?
No company is perfect, and issues are always bound to happen no matter how they are controlled. When these issues arise, the goal is to provide solutions or corrective actions to make the processes even better.
The Corrective Action Report (CAR) seeks to define the following:
Root causes identified
The first step of doing a corrective action report is to identify those root causes that contribute to defects or the non-conformances. When a problem's root causes are carefully identified, the right solutions or corrective actions will eventually follow.
Corrective actions to eliminate the root causes with an action plan
The next step is to provide the corrective actions that address and eliminate the root causes identified above. These corrective actions can range from simple ones to the most complex ones that require the management's attention.
Verification and validation of corrective actions
The last and most important step is to verify and validate whether the corrective actions implemented are working well to mitigate the root causes of the problems.
What are the critical elements of a Corrective Action Report?
This corrective action report template comes pre-built with all the fields you need to accurately capture the defect or non-conformance quickly so that projects can move forward:
- Automated form ID number
- Corrective Action Report (CAR) category and current open/closed status
- Date identified and organisation issued to dropdown
- Description of defect or non-conformance
- Reported by the person and digital signature for reporter
- Proposed and actual corrective action description
- Reviewer digital signoff
- Form attachments if needed
How often should we do corrective action reports?
The number of corrective action reports that should be done largely depends on your company's processes, needs, and requirements. There is no definitive number of corrective actions to be reported, but there are considerations when to issue one. Here are the times when a CAR is needed to be done:
1. After non-conformances
In manufacturing settings, a product may show a significant defect or a compliance issue that comes out during audits, inspections, internal reviews, or even customer complaints.
2. Recurring issues or problems
Some problems or issues happen more than once or even repeatedly, and a corrective action report should be issued immediately to prevent recurrence in the future.
3. Findings from regulatory bodies
Nothing beats the eyes of external auditors such as the FDA, ISO, OSHA, and HSE when it comes to nonconformances and issues found that can be counted as violations. A CAR can do the job to rectify these violations and monitor accordingly to keep these from occurring.
Remember, corrective action reports are done as needed whenever these issues arise and not on a fixed schedule. Periodic reviews, such as monthly or quarterly, are also necessary to make sure the corrective actions are effectively implemented.
Should you still be running corrective actions via a Word or Excel template?
Historically, in industries where corrective actions are common, like construction and manufacturing, corrective actions have been documented and then managed via paper forms, Word documents and Excel spreadsheets for tracking. While these methods made sense for a period of time because they were the best technology, those times have changed.
All companies now have access to affordable solutions which dramatically streamline the corrective action process, and basically ensure ISO 9001 and other standard compliance through automated workflows, version control, proper actions tracking and other functionality.
If you haven't explored levelling up your corrective action process beyond Word and/or Excel, then scroll down to see a couple of proven quality management solutions which handle corrective and preventive actions, largely for you.
Other popular templates you can use and edit for free
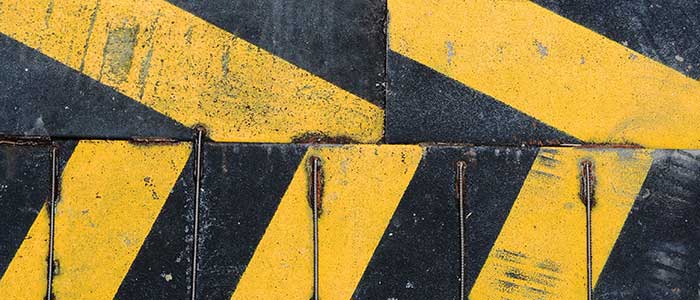
Snag list template
Don't let snags get in the way of project completion.
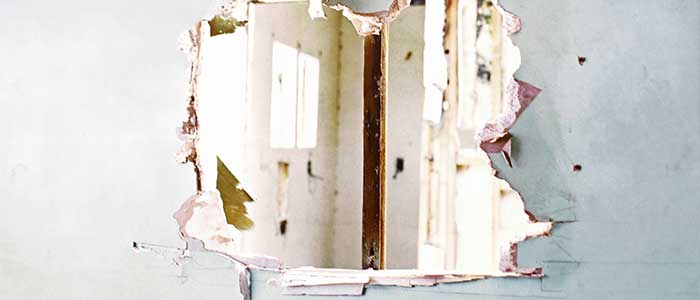
Construction Punch List template
Punch your way through those punch lists with this powerful template.
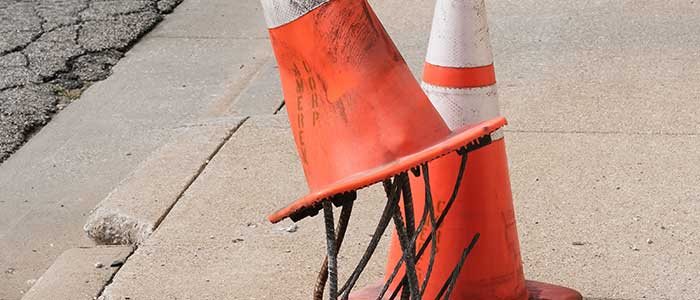
Defect Report template
Manage and rectify those inevitable defects with ease.
This ISO 9001 Corrective Action Report was generated with Dashpivot
Running your corrective actions via a proper quality management system has many advantages:
- Add or edit report fields with easy drag-and-drop functionality.
- Access and use your CAR report from anywhere - on a laptop, mobile or tablet.
- Instantly format your completed progress reports into workflow view or register view.
- Set up automated workflows for corrective action reports. Internal and external parties are notified when the CAR requires their digital sign-off.
- Download, print, or send your CAR's reports as custom-branded Excel or PDF documents.
- Get real-time analytics & insights on corrective action and general quality performance.
Sitemate builds best-in-class software tools for built world companies.