Dashpivot article page – Part L ventilation
Part L Ventilation
Read on to understand the Part L Ventilation requirements, and the ventilation rates required for various spaces within a commercial property e.g offices, shops, and kitchens to adhere to environmental regulations.
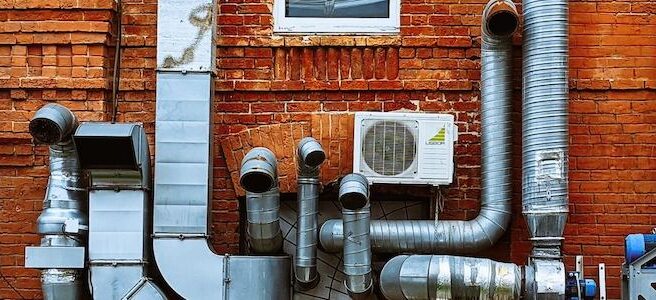
Ventilations role in Part L?
Ventilation prevents the buildup of moisture, carbon dioxide, and other pollutants that leads to poor air quality in a building, and eventually causes health issues to occupants. Part L requires buildings to have controlled ventilation systems that maintain adequate indoor air quality with minimised heat loss.
Ventilation Requirements in Part L Regulations
The ventilation requirements for Part L compliance is to simply design buildings that maintain overall energy efficiency and being a space that is healthy to occupy in.
The buildings must be designed airtight with controlled ventilation. There should be a balance between airtightness and ventilation. Buildings that have an air tightness score of 3m3/(h·m2) or below should have centralized or decentralized continuous mechanical ventilation integrated.
The Part F of the Building Regulations provides guidance on the minimum requirements for ventilation in the the different areas of a dwelling within three (3) methods: (1) Natural Ventilation; (2) Continuous Mechanical Ventilation, and; (3) Mechanical Ventilation with Heat RecoveryThese four methods are suitable for specific types of buildings and should be correctly chosen during the design stage.
Natural Ventilation - Minimum Extract Ventilation Rates (L/s)
-
Kitchen (cooker hood extracting outside) - 30
-
Kitchen (no cooker hood or cooker hood does not extract to the outside) - 60
-
Utility room - 30
-
Bathroom - 15
-
Sanitary accommodation - 6
Continuous Mechanical Ventilation - Minimum Extract Ventilation Rates (L/s)
-
Kitchen - 19
-
Utility room - 8
-
Bathroom - 8
-
Sanitary accommodation - 6
Mechanical Ventilation with Heat Recovery - Minimum Extract Ventilation Rates (L/s)
1 bedroom - 19
2 bedroom - 25
3 bedroom - 31
4 bedroom - 37
5 bedroom - 43
Note: If the dwelling only has one room, use a minimum ventilation rate of 13L/s. For each additional bedroom, add 6l/s.
The type of ventilation system highly encouraged is the Mechanical Ventilation with Heat Recovery (MVHR). It improves indoor air quality by extracting unpleasant air from bathrooms, kitchens, and other “wet” areas. It will then bring in fresh air from the outside, heat it, and pump it inside the home. The reason being it’s highly suggested in Part L regulations is because it can retain up to more than 90% of the heat that would just likely be lost through gaps in the building. The system also provides continuous supply of filtered fresh air. Integrating MVHR systems in the design stage already shows its contribution as it usually highly improves SAP ratings and it’s a sustainable system for future-proofing.
Testing and commissioning the ventilation system should always be observed and the readings are mandated to be submitted to a Building Control body. Accredited testers and UCAS accredited flow test instruments should be used to test the ventilation rates as well. The Building Control Body will then issue a certificate to the building owner indicating the recorded ventilation rates.
For non-dwellings, it’s encouraged to use complex ventilation systems that use Air Handling Units (AHU). These are the minimum extract ventilation rates (L/s) for non-dwellings:
Toilets - 6
Showers/baths - 15
Kitchens (only a microwave) - 15
Kitchens (cooker with fan adjacent) - 30
Kitchens (cooker with fan not adjacent) - 60
Fresh air supply - 10/person
Installation and Maintenance of Ventilation Systems Best Practices for Part L Compliance
Proper Design and Planning
It’s important to ensure that the ventilation system is designed according to the building’s volume and occupancy in order to provide adequate airflow. Also choose the appropriate ventilation system type accordingly.
Ventilation Installation Techniques
Ensure that proper sealing is practiced in all ducts and joints with proper insulation. Supply and extract vents should be placed in areas where they can easily function, where supply vents have access to fresh air, while extract vents have areas they can properly extract stale air. Avoid any potential obstructions through the airflow such as furniture or other building parts.
It is essential that installers follow the manufacturer’s guidelines and installation procedures, and that they are equipped with the proper tools and knowledge to perform as intended.
Ventilation Testing & Maintenance Practices
Ventilation systems should be tested after installing to ensure they comply with the minimum required ventilation rates including all vents being tested for correct airflow direction. A test or commissioning report should be prepared including all performance data, flow rate measurements, etc to be submitted to a Building Control Body. It’s important that the document also includes photos and proof of installation in order to comply with Part L.
Regular inspections and filter changes should be conducted especially for mechanical systems. Clogging may cause flow blockage which may compromise the overall building energy efficiency. Inspections must include checking if there are any damages to the ventilation system, issues with the fans and controls, or for any air blockage. Along with inspections, regular cleaning should be practiced.
Another important thing to take note is regular calibration of the sensors, timers, fans, and other types of controls.
Documentation for Part L ventilation
Streamline your process for monitoring, documenting, verifying compliance, inspections, calibration procedures, and more by using digitized documents and forms saved in your very own database. Track and manage your data efficiently by ensuring all the installation, testing and maintenance procedures and recorded.
Use checklists for every part of the installation, inspection, calibration, and more. You can create your own checklist from scratch or use the existing ones from our public template library. Ensure that every step during installation is recorded and approved under Part L standards.
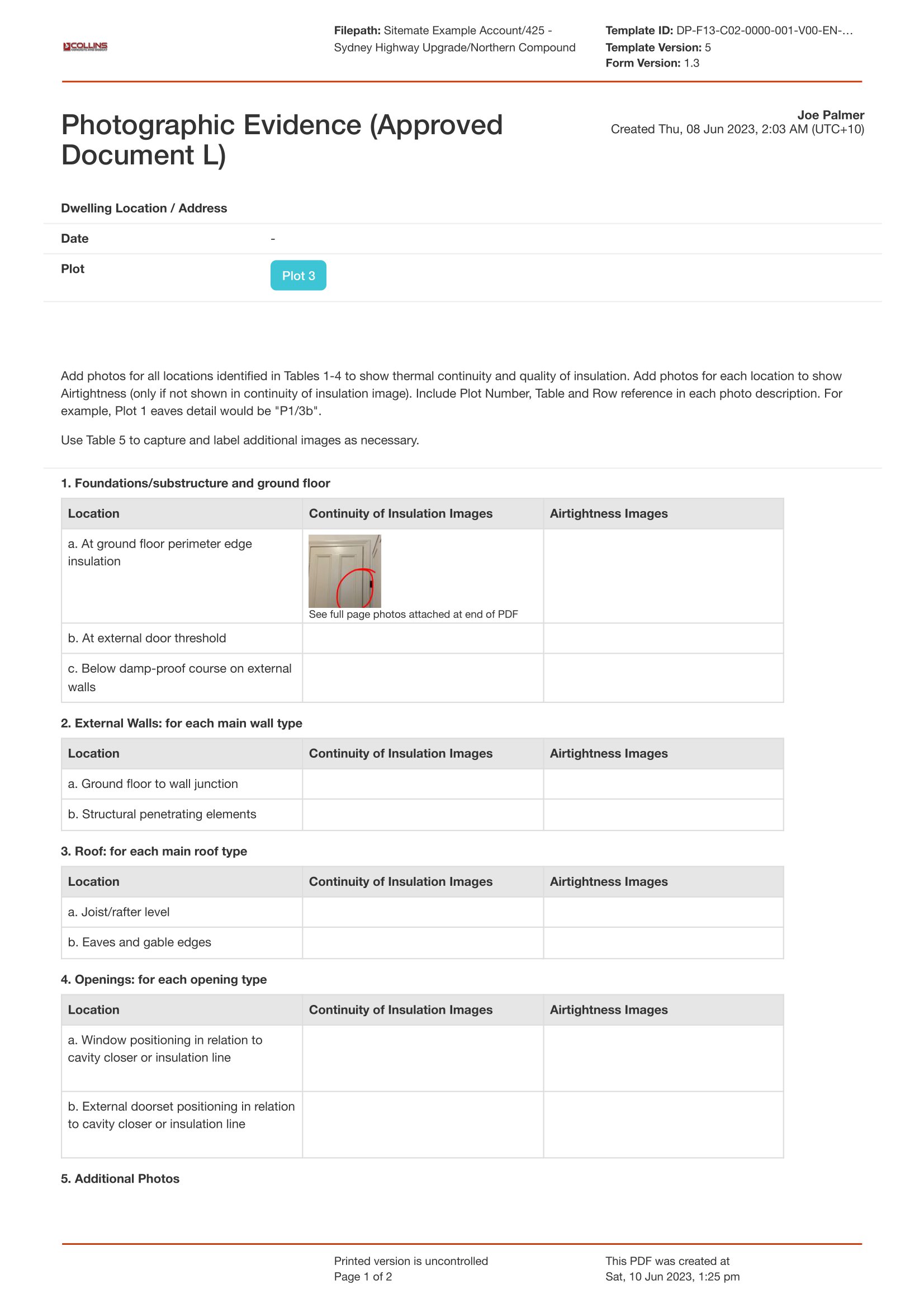
Better document ventilation for Part L with this form
Make it easy for your team to capture Part L Photographic Evidence
Easily conduct inspection using your mobile or tablets and input the necessary data in real time, and have your team members access the data remotely. You can even record in offline mode if the area isn’t accessible to an internet connection and you don’t have to worry about losing the data. They will be automatically uploaded into your database once you connect to the internet.
Attach photos in all of your inspections and maintenance checks with data like GPS, comments, tags, and markups.
You can include the material specifications and performance tests. Include checkboxes, note sections, photo uploads, and corrective actions. Create your own forms to easily conduct flow rate tests. Additionally, you can also create dashboards and easily make reports.
Easily submit your forms electronically to Building Control authorities to speed up the compliance process. Don’t miss deadlines by keeping everything digitally and organized.
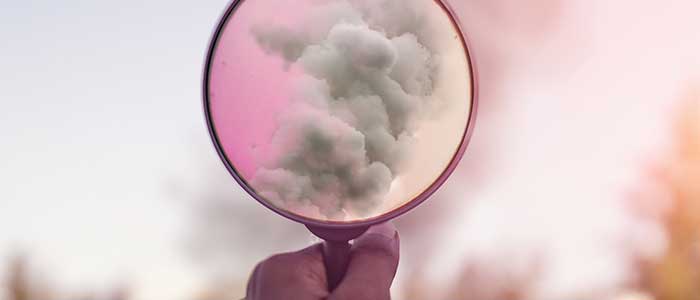
Inspection and Test Plan (ITP) template
No one plans to fail, they fail to plan. Ensure your projects are a success with this ITP.
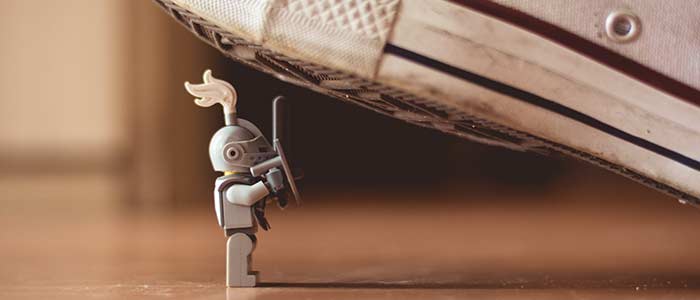
Non-Conformance Report template
Document those painful non conformances with this powerful template.
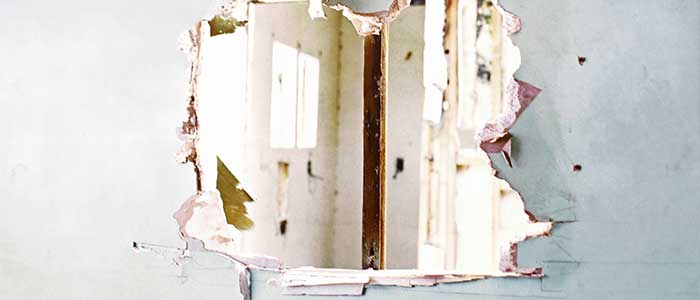
Construction Punch List template
Punch your way through those punch lists with this powerful template.