Dashpivot article – 5 minute toolbox talks
5 Minute Toolbox Talks
This article explains how to conduct efficient and effective 5-minute toolbox talks so that you can keep your teams engaged during safety discussions. It also includes some free resources to help speed up the processes around toolboxes.
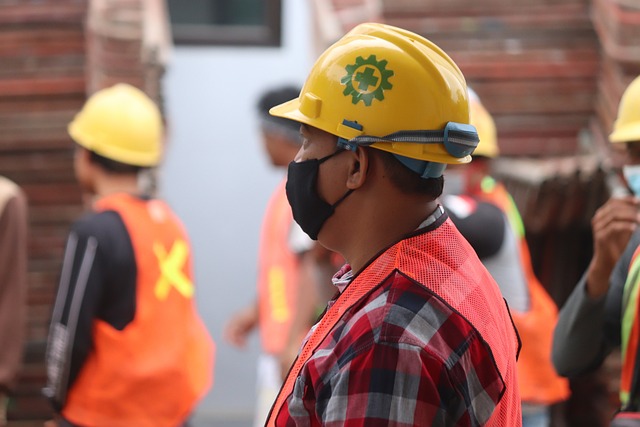
What are 5-minute toolbox talks?
5-minute toolbox talks are brief safety discussions intended to reinforce key safety practices, address recent incidents or concerns, and promote a consistent safety culture among workers.
Due to their short duration, the content needs to be concise, relevant, and engaging.
But why just 5 minutes on Toolbox talks?
Toolbox talks are typically kept short for several reasons:
Attention Span
On the first hour of work, workers tend to lack focus due to the reason that they might be groggy because it is still early in the morning or the caffeine from the coffee hasn't fully kicked in. The same situation might also happen after work. Workers tend to have little or no energy to stay focused on long discussions. During these times, doing short talks can help maintain focus and ensure that the primary message is received and retained.
5 Minute Toolbox Talks Need Efficiency
In a single day, a lot of activities might need to be done, and a lot of energy might be needed to complete these activities. Long meetings can disrupt the flow of these activities and might cost the energy of the workers to complete these activities. Not only that, but these might have consequences for the quality of the output of the workers, which might have an effect on production or construction. Keeping the meetings short keeps the efficiency and avoids delays in the days work.
Frequency
Toolbox talks are typically held more frequently than formal training sessions. Because they occur regularly (often daily or weekly), each talk can focus on a specific topic, allowing for more in-depth discussions over time without overwhelming workers with too much information at once. These specific topics are also arranged where the strong and relevant points are highlighted. By doing this, the toolbox meetings are maintained to be short and provide the information needed for the day.
Relevance
Toolbox can be anything relevant to the work. It could discuss the specifics of the safety measures needed for the day; it could also discuss current world issues and how it could affect the organisation financially. Anything could be brought to the table as long as it benefits the workers in their work attitude, especially when it comes to safety. Keeping it on a level where workers can relate can also improve retention of the topics in talks. People mostly relate on a personal level, so integrating something individuals can relate to into the relevant topics of the day can really help with keeping the lessons by heart.
Flexibility
One of the best things about toolbox talks is that you don't have to stick to the same structure of agenda. Toolbox talks are flexible from the way they are structured to the topics they contain. Toolbox talks are informal, making this meeting more comfortable for the workers to open up to issues or concerns. Meetings that are rigid are usually more tense in nature, which sometimes intimidates the workers into sharing, which defeats the purpose of having an open environment where people can share personal findings that can help improve safety measures.
Reinforcement
Since toolbox talks are more frequent and regular, important topics are effectively reinforced. The repetition of discussing important topics, like all necessary safety measures that need to be implemented daily, can be a routine discussion on toolbox talks. Having it this way can really inculcate the importance and need of these safety measures. This will also improve worker retention on these safety measures and execute them perfectly once they are needed to be implemented. To put it into a simple perspective, Toolbox talks are an avenue for reinforcement training.
5 Minute Toolbox Talks Require a Reduction in Complexity
Since topics are specific, understanding them wouldn't feel like solving a math problem. Long topics could be divided into subtopics to make them easier to understand. This could also save meeting time and provide more time for more important and relevant topics. This could help workers understand what's more important to do and what's less important to do. This will iron out the procedure to be more simple and more understandable. Making the topics easy to understand eliminates the possibility of human error, making the area more safe and sound for workers.
How should you run a 5 minute toolbox talk?
Running a 5-minute toolbox talk effectively requires careful preparation, clarity, and engagement. Here's a step-by-step guide to ensure your short talk is impactful:
Choose a Relevant Topic for your 5 Minute Talk
The subject should be pertinent to the current work environment or task. It could be based on a recent incident, a new procedure, or a recurring safety concern. Relevant topics help workers be aware of what is a necessity and what actions are prohibited to keep themselves healthy and safe in doing a procedure.
Prepare in Advance
Given the short time frame, preparation is crucial. Understand your main points and strive to simplify them to the essentials. If possible, rehearse your talk to ensure you stay within the time limit. A well-thought-out toolbox meeting only brings you halfway on what you are trying to impart. A well-thought-out and well-prepared toolbox talk can delve into the most profound aspects of a worker's mind.
Gather Necessary Materials
Using materials like visual aids gives workers a clearer picture of the message you are trying to convey and keeps the meeting interesting, gaining their best attention to the talk. If you're using visual aids, like images, equipment, or handouts, have them prepared and easily accessible. Visuals can be particularly impactful in a short presentation.
Be in a Conducive and Comfortable Space
To have effective communication, the words must be received clearly from the receiver. Having said this, it is essential that the workers fully hear you when you are doing a toolbox talk. Ideally, the location should be free from distractions, close to the work area, and able to accommodate all attendees comfortably.
Open with a Bang, You have 5 Minutes!
Start with a strong remark or question to grab people's interest right away. Referring to a recent incidence or statistic connected to your issue, for example, will help listeners pay closer attention. Start on great energy as well. Usually, people react to what they see, so beginning with great vitality increases their mood and allows their whole focus to you.
Easy to Understand
Focus on the key message or the primary action you want workers to take. Make it simple, and avoid jargon or overly technical language unless it's commonly understood by your audience. Less complex talks are the most effective talks. People understand them better and leave no room for errors in the field.
Use Real-world Examples
People usually remember things if they are relatable or have experienced seeing such events. Relatable anecdotes or examples can make the information more memorable and drive home the importance of the topic. This also magnetises the interest of the workers, keeping them engrossed and focused throughout the meeting and absorbing all important information.
Encourage Participation
Toolbox talks are an avenue for exchange learning. This means that the speaker and listeners have a mutualistic relationship in giving and receiving information. This helps the speaker learn things that organisations can improve on, which further enhances the safety of the workers. Having said this, it would be highly suggested to create a comfortable atmosphere in this talk to encourage participation amongst workers.
Reiterate Key Points
Given the brevity, repetition is beneficial. This will give the impression that the repeated points are a vital need to be remembered. You could repeat these points in the phase where you are concluding the meeting. With this, this will remind the workers of the topics that are crucial to be retained and listen to the important takeaways.
Document the 5 Minute Toolbox Talk for Future Reference
There are some nations, regions, and territories where Toolbox talks are regulatory compliance. It is highly recommended to have a sign-in sheet or some form of attendance record to document who participated in the talk, especially for compliance reasons. Below is an example of a 5-minute toolbox talk.
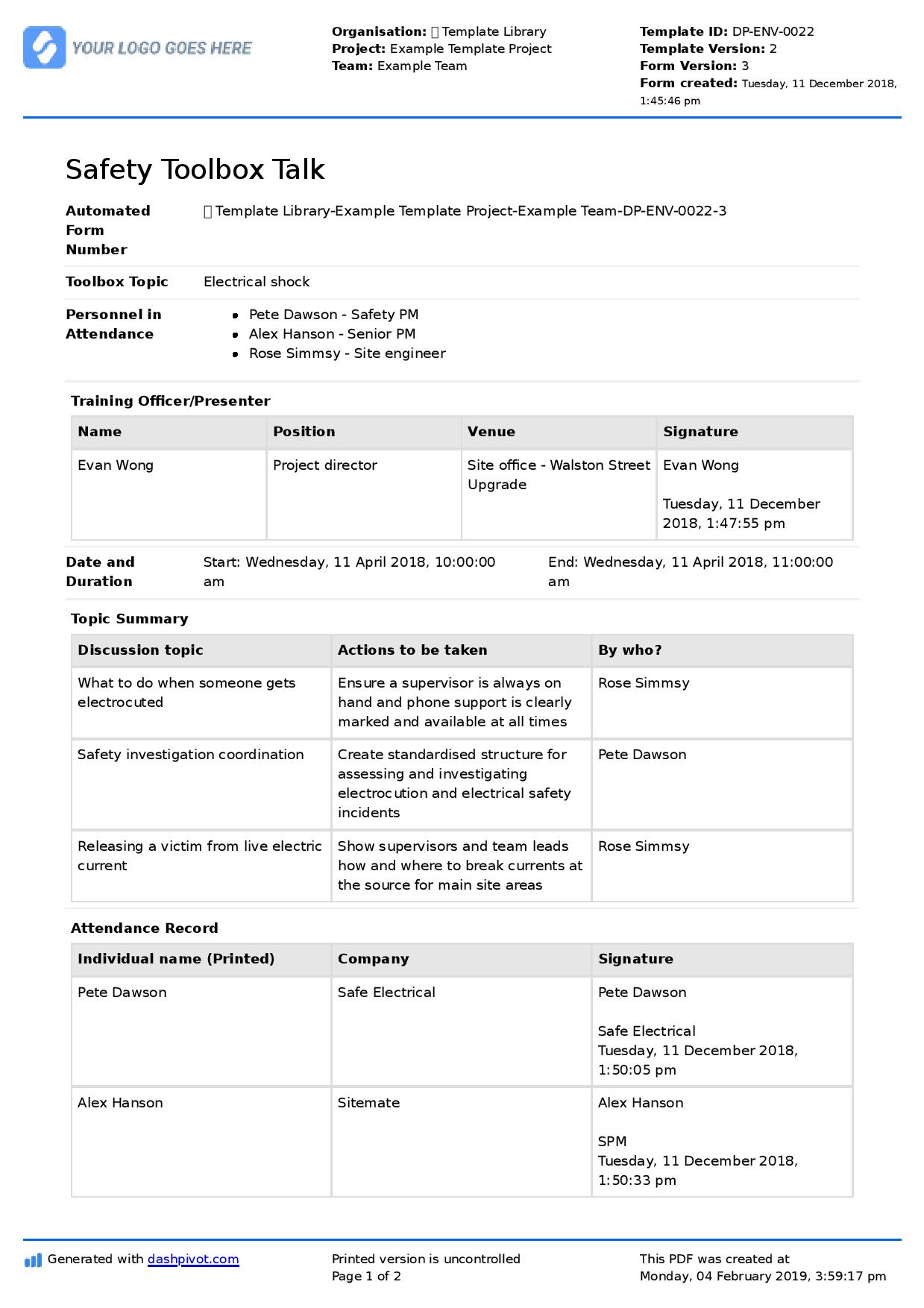
Use and customise this 5 minute toolbox talk form for yourself
Run standardised 5 minute digital toolbox talks
In this article, we ran through why you should run 5 minute toolbox talks, as well as how you can prepare and run them.
But there is a practical challenge component to running 5 minute toolbox talks as well, which is how is it possible to prepare for and run 5 minute toolbox talks when there is so much else to do, and when we are running toolbox talks with 20, 30, 50 people on site?
The answer to this question lies in having better safety systems in place.
If you have a proper safety system or dedicated toolbox talk app like Dashpivot in place, then you can access hundreds of free toolbox talk templates directly from the system, meaning you can easily pull them off the shelf each day or week without doing much work at all.
Using templates can save you hours of prep work each week.
Once you have the template, you can then run the toolbox talk itself via the app directly on site. With an app, you can have workers sign off electronically by simply scanning/swiping a free digital ID card - which takes the process of signing off on a toolbox talk from being a manual process which might take longer than the 5 minute toolbox talk itself, to taking a couple of minutes, no matter how many people you have in attendance.
Proper systems also take care of the storage of those toolbox talks, meaning that they are automatically stored once signed off in a digital database, where they can be reviewed and audited at any stage in future, ensuring site and safety compliance.
If you are still running toolboxes on paper, then it will be more challenging to run toolboxes in general.
In this article, we covered how easy and important it is to run at least 5 minute toolbox talks, as well as how you can optimise your toolbox talk prep and meetings as well, to make it all much more manageable for you and your team.
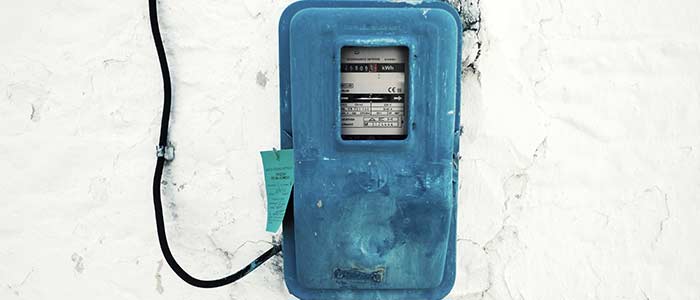
Electrical isolation safety
Improve electrical safety with this process framework
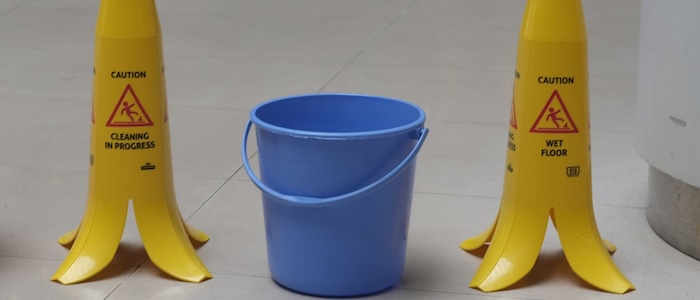
Slips, trips and falls toolbox
The perfect 5 minute toolbox talk topic
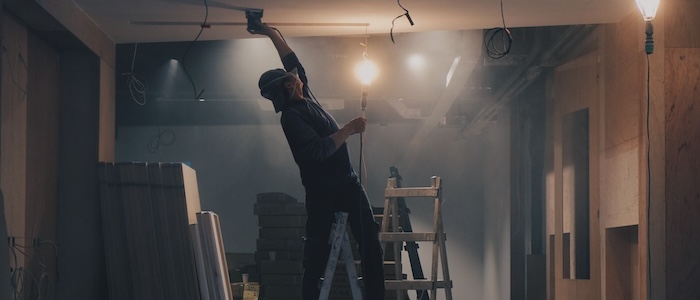
Ladder safety toolbox
Another great 5 minute toolbox talk topic, applicable to most sites