Dashpivot article page – How to make Near Miss Report
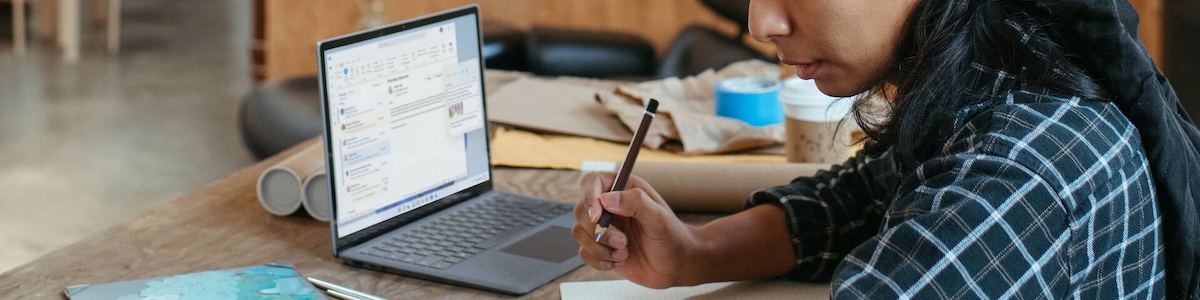
How to make a Near Miss Report
What needs to be in a near miss report?
This article outlines how to make a near miss report, and it's useful for any type of industry. This shows how to thoroughly document data from a near miss incident and input the necessary details relevant in formulating preventive measures. It’s important to have a structured approach in the near miss reporting process to ensure that organisations can utilise near miss data into safety improvements and analytics for future reference or study.
A proper structure enables workers to diligently report near misses. This structure simplifies the reporting process by using clear guidelines and showing the workers and employees what to include.
Take note that this article provides a general guide on how to make a near miss report. Contents may vary depending on the industry or preference of the organisation and company.
What Information Should You Gather Immediately After a Near Miss?
When a near miss occurs, it's best practice to report it immediately right after and persons involved should input the details to preserve the accuracy.
Inputting these details immediately right after is important because it’s still fresh. This reduces the errors in documenting the details. When a report reaches the supervisor or safety officers, they can address the hazard right away and be able to swiftly take corrective actions. A timely report leads to a quick resolution, therefore prevents recurrence or an actual accident.
Basic Details, Weather/Site Conditions that make up a near miss report
The basic details like the date and time when the near miss occurred, the exact location, and the type of operation that was performed.
People Involved and Witnesses
The persons directly involved, who were almost harmed, and the witnesses who saw the near miss.
Equipment and Tools Involved
These are the if there were any equipment or tools involved in or related to the near miss, including their condition such as defects, malfunctions, improper use, or damage that caused the near miss.
Detailed Description of the Event
This should thoroughly outline the proper sequence of events step by step and the immediate actions taken by the workers and safety officers present. This area also highlights the possibility if someone was actually harmed or a property was damaged.
Hazard (Type and Root Causes)
The particular type of hazard should be indicated and described, along with the potential root causes based on observations.
Visual evidence
It’s necessary to gather visual evidence like photos, videos, sketches, and diagrams to help the supervisors and safety officers fully understand what happened. There are instances where words don’t fully explain the event or outcome without visual evidence.
Observations From People Involved
This section is where the persons involved write their statements so the people reading the report can understand their perspective. It’s important to get their feedback so the management can know if there are any signs of unsafe practices in the workplace or if the SOPs should be updated.

Use this framework to teach you how to make a near miss report
How should contributing factors and root causes be documented?
Contributing factors and root causes should be documented by using a root cause analysis technique like the 5 Whys Method or the Fishbone Diagram (Ishikawa). There are also other ways to properly document factors and root causes as shown below when you make a near miss report.
5 Whys Method
Using the 5 Whys Method is when one keeps asking why until there’s no why left to ask within the power of the organisation.
For example:
A worker almost tripped over the cable. Why?
The walkway wasn’t cleared after the operations. Why?
Another worker forgot to remove it. Why?
Clearing procedure wasn’t followed through after work. Why?
There is no site inspection for housekeeping. Why?
The safety policy doesn’t include housekeeping.
Root Cause/Conclusion: The site supervisor should update the site safety policy to include housekeeping and inspections after operations.
Fishbone Diagram (Ishikawa)
The Fishbone Diagram (Ishikawa) on the other hand is a visual tool that makes use of categories for brainstorming. The main categories are Material, Measurement, Machine, Method, Environment, and Employee. The supervisor, safety officers, or anyone tasked for brainstorming will write causes of the event underneath each category and continue to ask “why” underneath each cause until the group runs out of ideas.
Thorough Observations with Evidence
The worker must describe the scene in specific details, like the environment, equipment involved, human factors, and others. The description should be based on facts not assumptions, and the worker must use clear words. Avoid using ambiguous terms.
For the analysis, it’s important, and as much as possible, to include statements from witnesses or those who had seen the event. Attach visual evidence to support claims and facts.
What immediate corrective actions should be noted when making a near miss report?
Firstly, it’s important to secure the area immediately right after the near miss takes place to avoid an actual accident from occurring. It could be by placing warning signs, pausing work in the area where the near miss occurred, isolating the involved equipment, clearing debris, or others. Install these temporary solutions for safety measures.
Next, workers involved must call upon the relevant site supervisor to inform them about the incident so that an investigation can be started. The supervisor may conduct a team briefing as well.
Next is ensuring if any of the workers involved have any potential injuries even if it’s just a near miss. They should be medically checked for safety. This time is also great to remind workers about the safety protocols.
Followed is the documentation of the near miss and this is where a near miss report comes in. This is the perfect time to document all the details, observations, types of hazard, photos, visual evidence, and others in the near miss report. It’s essential to document immediately because the event is still fresh and this ensures data accuracy.
With that being reported, the organisation can create long-term solutions and identify trends regarding that specific site or hazard. Short-term preventive measures should also be reinforced like reminding everyone of the safety policies and assigning people to monitor the area until the long-term solution is implemented. Corrective actions, preventive actions, or actionable steps should address each contributing factor and root causes that were laid out.
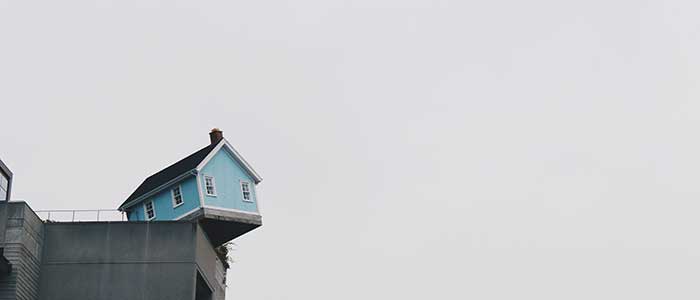
Hazard Report template
Document and report hazards quickly and thoroughly to keep everyone safe.

Safety Improvement Plan template
Create coherent, actionable and professional safety plans using this proven framework.
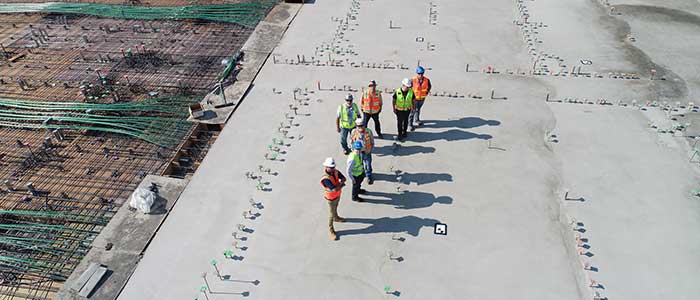
Safety Toolbox Talk template
This toolbox talk template is quick and easy to complete and signoff on site, and keeps all of your toolbox talks neatly organised and professional.