Safety – Electrical isolation procedure
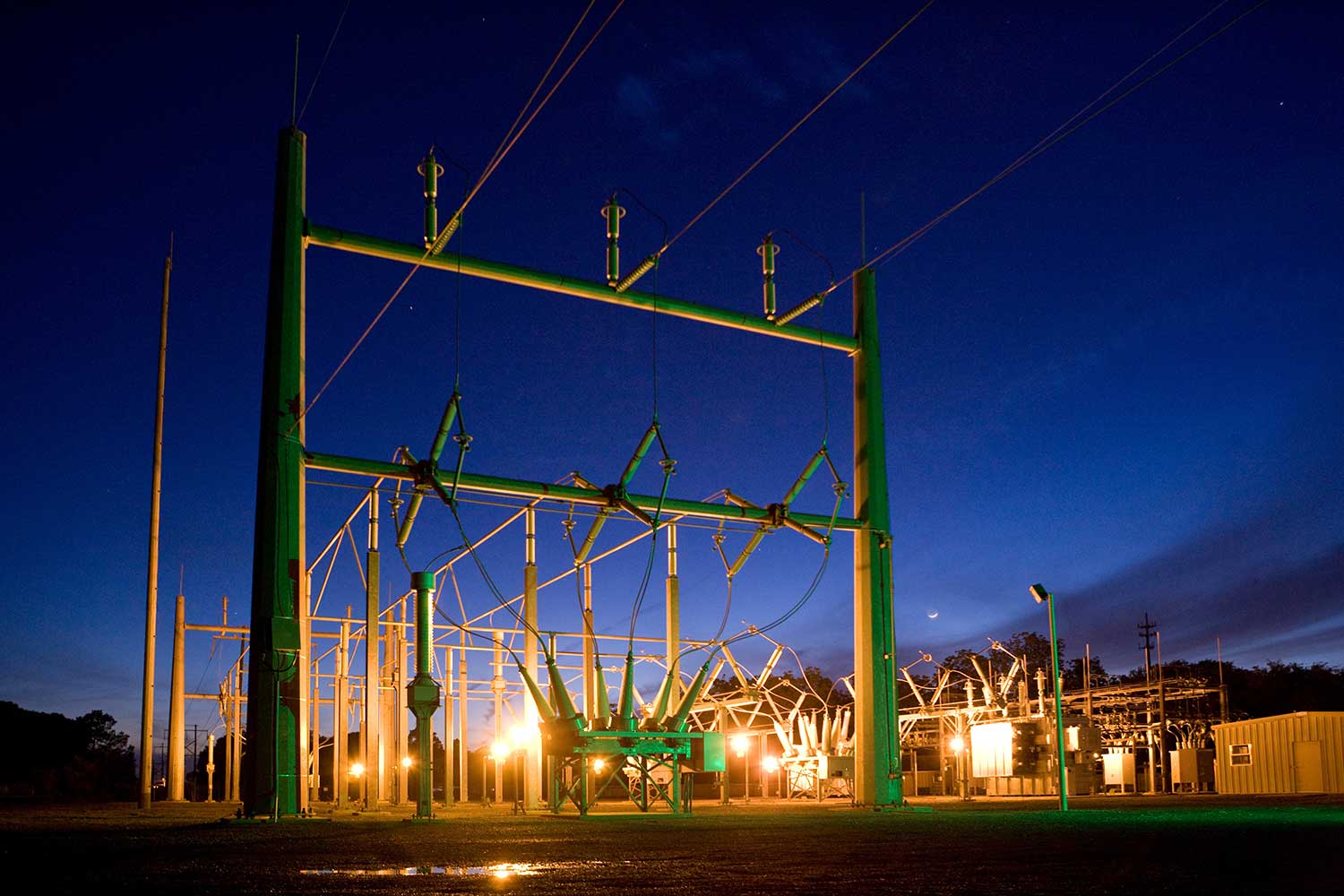
Electrical isolation procedure: Here's how to get yours right
Safe electrical isolation procedures
The correct electrical isolation procedure goes a long way to ensuring that the people working on and maintaining your electrical (and other energy-charged equipment) remain safe.
It's also a great way to ensure that the equipment and infrastructure being worked on is managed properly.
Before isolating any services or equipment, check with the relevant person and make sure that those services can be disrupted at that time - and for the duration of works. Once this is all cleared and you are complying with the permits to work and other activities, you can begin your electrical isolation procedure - before beginning work.
Where practicable, before any plant is inspected, maintained, cleaned or repaired, it's energy sources must be locked out and tagged.
The most common energy source is electricity, but other energy sources which can require isolating include hydraulic pressure, kinetic tension, other moving parts and compressed gas.
The purpose of isolating any and all of these energy sources and machinery is to ensure that an accidental 'release' of energy does not occur; to control the environment and other hazards associated with that work; and to ensure that entry or contact with restricted equipment or areas is regulated and controlled.
The right electrical isolation procedure
Creating a structured and systematic approach to electrical isolations - at the individual, project and organisational level enable you to reduce risk and mitigate the chance of accident occurring.
The more standardised and 'codified' your process is, the easier it is to constantly iterate and keep improving your isolation and safety outcomes.
Phase 1
Before the actual isolation begins, you must ensure that you have the permit to perform the isolation - or the permit to work. This permit is relatively straightforward. The permit should include some general instructions about the isolation, and feature the date and time of work, the scope of works being proposed, the location of work and the isolation purpose.
After this, your permit to work should document and explain which equipment will be isolated, before the permit applicant and permit authoriser signoff to begin work.
Once you have signed off on the electrical isolation permit, you are all systems go on beginning the isolation procedure.
The first parts of the actual lockout procedure involve shutting down the machinery or equipment which will be inspected, maintained or repaired.
This step should also include identifying all relevant energy sources as well as secondary sources, such as standby generators, uninterruptible power supplies and microgenerators.
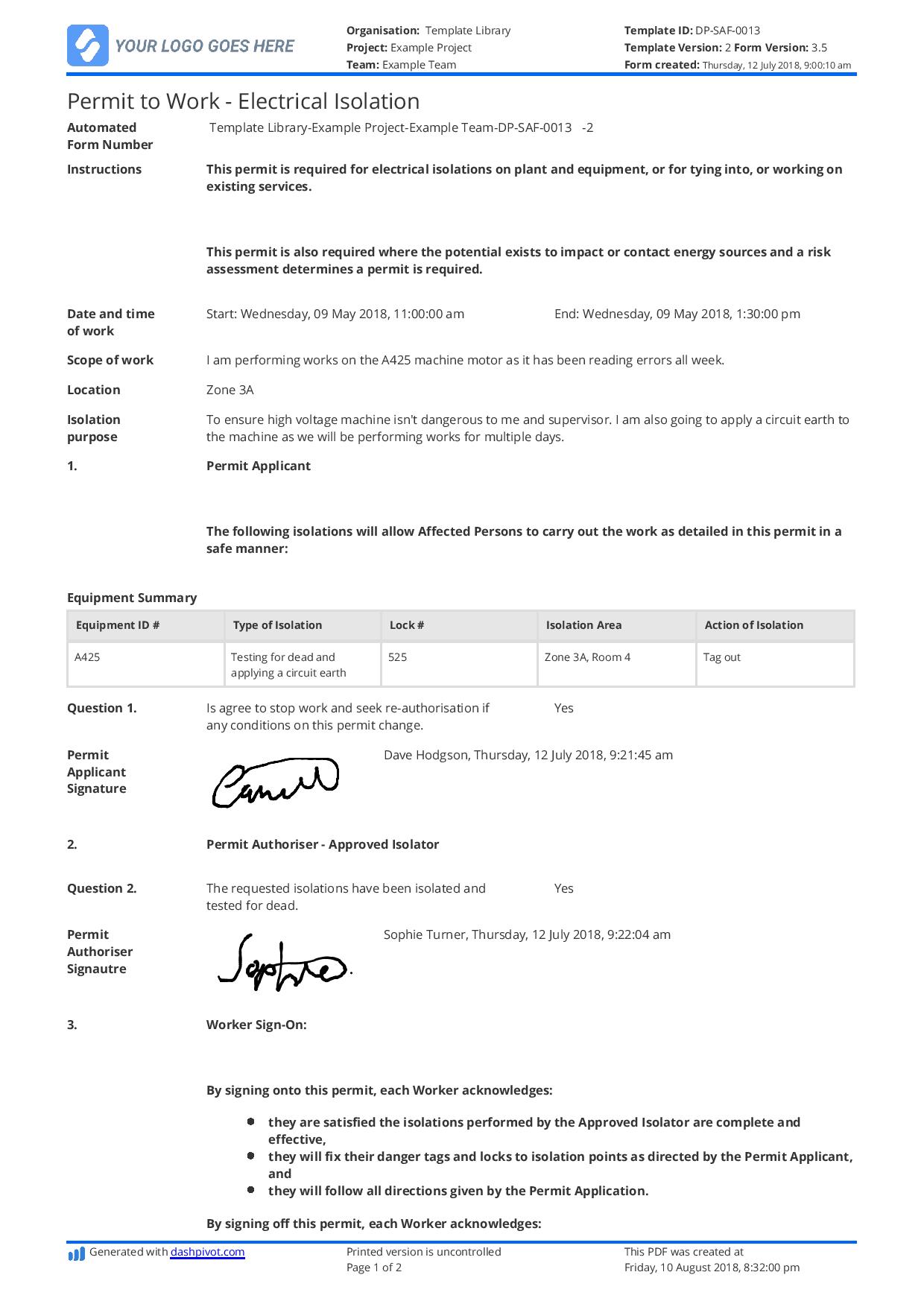
Use and customise this electrical isolation permit structure for free.
Phase 2
The next phase of isolation involves identifying the isolation points or single point of isolation for the system or circuit.
Once identified, you can isolate all the energy sources. Once the source is isolated, it's incredibly important that the point of isolation is locked off and tagged with the appropriate warning label. Every person working on isolated equipment should fit their own lock or danger tags, and every tag should be fit for purpose (locks and danger tags, out-of-service tags) and completely filled in with the appropriate details such as dates and signatures.
As insurance, it pays to keep the key to the lock on yourself to ensure that it can't be easily or accidentally unlocked.
If there is other or peripheral stored energy, it may be necessary to perform further controlled de-energising of the equipment or energy source before beginning any work.
Phase 3
The last phase of your electrical isolation procedure involves a final check and insurance test that the equipment is indeed properly isolated.
There are a number of ways to do this, and to some extent, the more checks the merrier.
You can test that the isolation has been performed properly be trying to reactivate the plant or equipment - safely of course.
You can also use mains approved testing equipment to make sure the equipment is 'dead'. Make sure to complete the right tests based on the type of supply you are dealing with.
Improving your electrical isolation procedure improves your safety outcomes
While there is no way to completely eliminate the risk associated with electrical isolations or working with and isolating heavy machinery, streamlining and standardising your isolation procedure is a sure way to manage and mitigate risk more effectively.
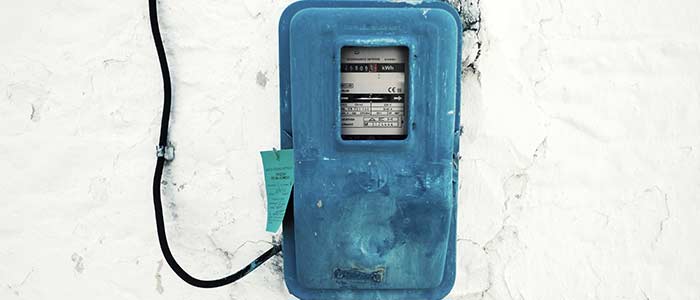
Electrical Isolation Permit template
Complete safe & proper electrical isolation procedures, every time. See the template →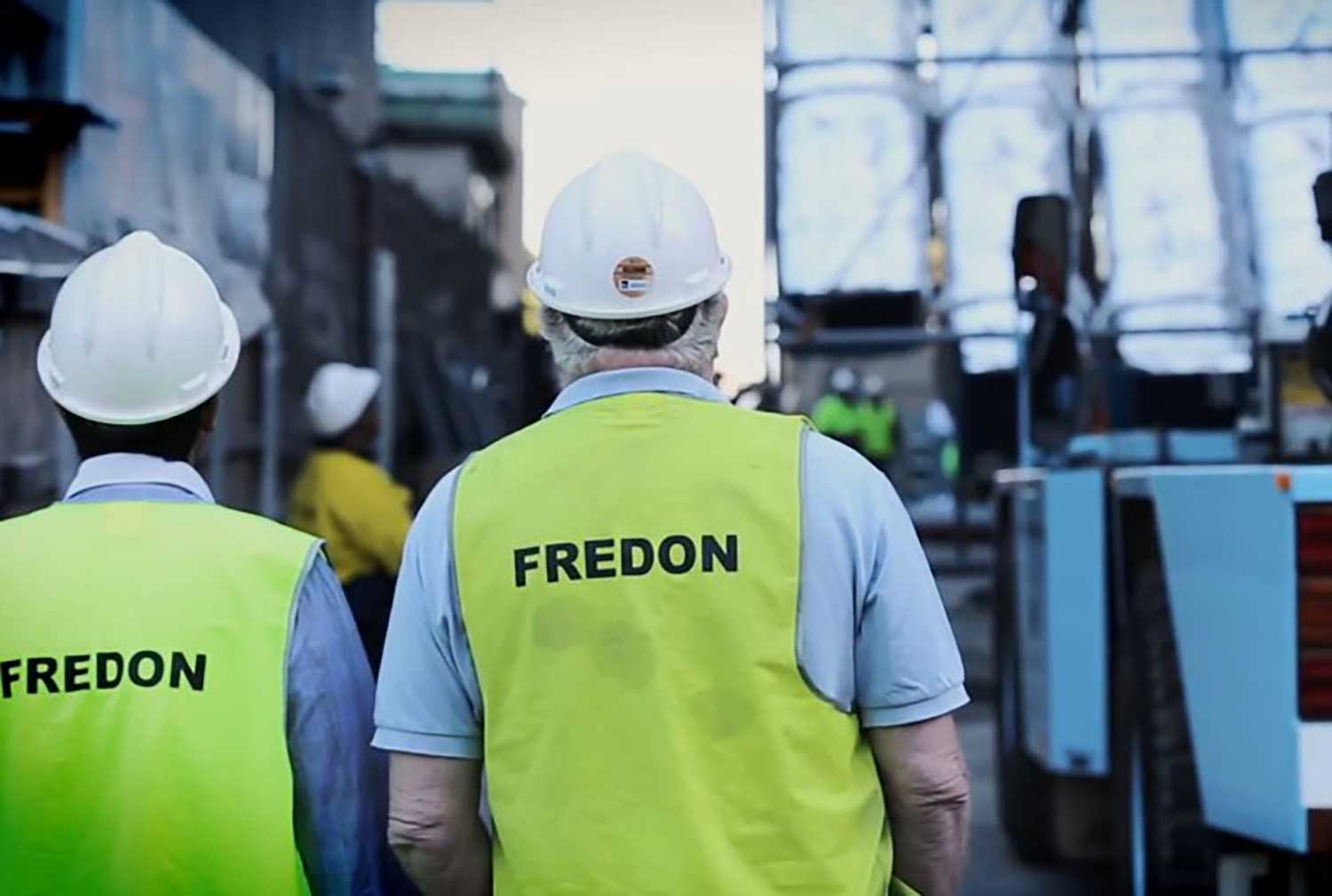