Safety – Hazard management

Hazard management
Hazard management definition
Before we look at the definition of hazard management, let's take a step back and define exactly what a hazard is:
A hazard is anything (situation, object, equipment) which poses a threat to life, health property or the environment.
As you can probably imagine, this means there are a lot of hazards in all walks of life, but there are a particularly high number of hazards in environments like construction and industrial sites.
Millions of people work in these industries and on these sites, and millions of dollars are spent on these projects to deliver infrastructure and other important works.
Because of this, hazard management is a top priority for thousands of companies - and when we refer to hazard management, we are talking about how these companies:
Hazard management is a holistic approach to defining problems and identifying hazards, gathering information about those hazards and assessing the risks, and then solving, controlling and mitigating those risks.
That is the true definition of hazard management, and one which does a great job of providing a practical framework and series of steps which we can engage with on an ongoing basis to properly manage hazards - which we will dive into later.
The general purpose of hazard management is to eliminate or at least control and mitigate risks. which then has a flow on effect to:
- Prevent the number of and reduce the severity of workplace incidents
- Improve worker wellbeing
- Create a safer environment where people can do their best and most productive work
In addition to a company having an internal and moral incentive to perform hazard management well, there are of course local and broad regulations around the type of hazard management which companies are obligated to perform.
The best way to look at hazard management is as a constant endeavour. It's an ongoing systematic approach to the ever-present problem of risk.
Types of hazard management
When it comes to hazard management, there are a few 'types' of hazards which we can generally put in 5 buckets or categories of hazard:
- Biological hazards
- Chemical hazards
- Physical hazards
- Psychological hazards
- Cultural hazards
In most work-related settings - where hazard management is more applicable to most people - we are mostly concerned with chemical, physical, psychological and some cultural hazards too.
There is some overlap between the types of hazard management required to manage specific types of hazard, and there are some unique approaches and processes to mitigating certain types of hazard as well.
Hazard management process
The hazard management process is well known and quite well understood. The process consists of:
Step 1 - Identifying hazards
The first hazard management step is arguably the most important. If you can't identify hazards properly, then you are going to have an extremely hard time managing hazards.
Identifying hazards typically consists of practices such as:
- Inspections
- Procedural hazard reporting
- Incident reporting and investigations
- Consultation with employees, toolbox talks and other forums of employee feedback
- Building risk assessment registers and risk response matrices
But different companies in different industries may have their own approaches which get identified hazards to the right eyes quickly.
A 'typical' hazard report from a construction site will look something like the sample below. In this case, a hazard has been identified on site, and this company has actually incorporated steps 2 and 3 into the same template to save time and mitigate hazards more effectively.
We'll dive into these next two critical steps below.

Use this hazard report framework for yourself.
Step 2 - Assessing and prioritising risks
Like most things in life, not all hazards were created equal in terms of their likelihood (of turning into an incident), the severity of the incident if it does occur - and the urgency of mitigating the hazard.
Because of these, one of the most important elements of hazard management is simply assessing each risk, and then assessing all of your risks against one another to prioritise what needs to be dealt with now.
It's impossible to place a huge effort on minimising every hazard, and it's not smart either. You want to focus your time and resources on the right kinds of hazards and the right kind of hazard management.
The 'standard' way to assess risks on a project or company basis is to create a risk register (here's a template). The purpose of a risk register is to document, organise and track all of your risks in the same way so that each can be assessed in the same way.
Step 3 - Selecting and implementing controls
Most of the third step of hazard management - selecting and implementing controls - also takes place in registers.
Within a risk register, each risk will be contained in a row, and each risk will get its own risk score. This standardised and objective score enables you person or project manager viewing the different risks to choose which hazards to address.
That person, project manager (and maybe a group of other stakeholders) will then put their heads together to select viable controls which can be put in place to control the hazard. They will of course be assessing and considering different controls based on cost, effort and other variables.
Another common and reliable framework for implementing safety controls is the hierarchy of risk control - which you can read more about here.
The person or team will then look to implement these controls when and where applicable. This may include altering procedures, changing processes or tweaking systems.
Step 4 - Monitoring and reviewing your controls
Hazard management is a full circle process, which brings us to step 4. We need to understand how the hazard management steps and controls we have put in place are performing.
Hazard management is about continuous improvement, and we can only improve what we can measure and monitor.
It's great to have some set processes and procedures around what monitoring and reviewing looks like to your organisation - so that there is a systematic approach to monitoring and review. This is the easiest step or phase of hazard management to forget or ignore, so being proactive about this step is crucial.
You can improve how you manage all of this data using safety dashboards which give you real-time insights into your data.
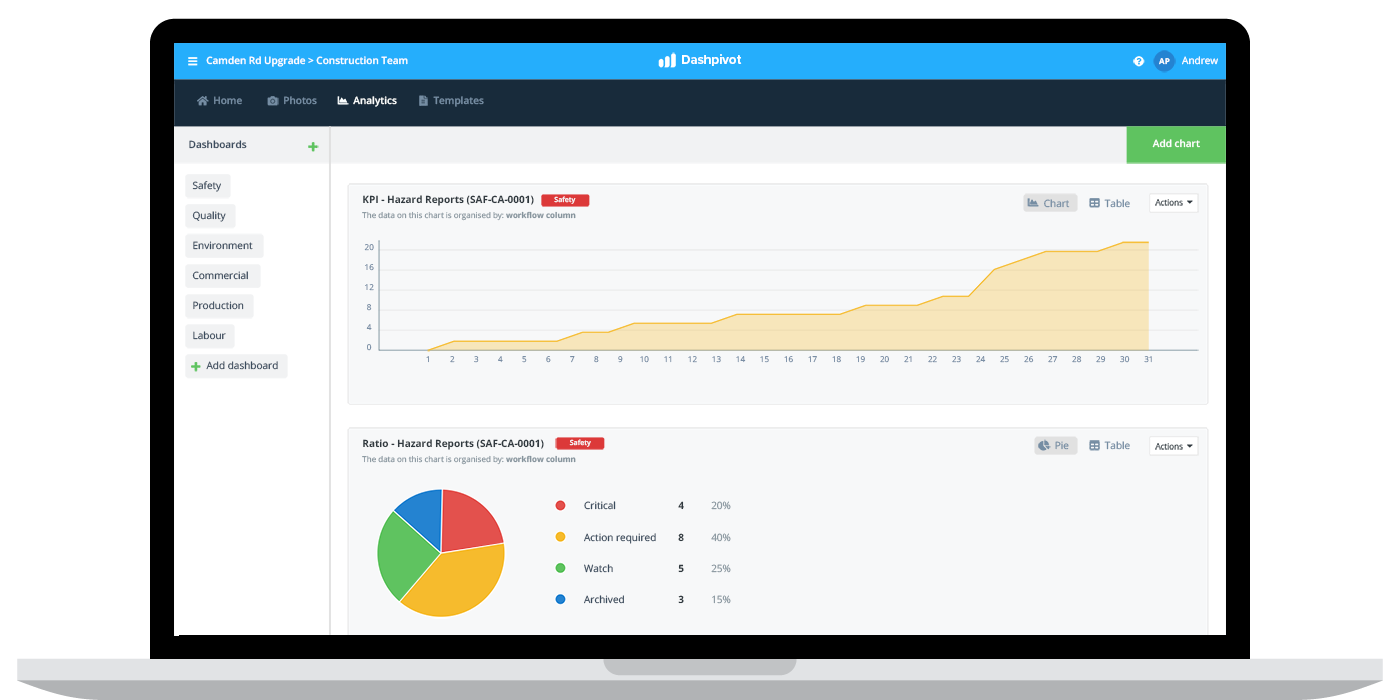
Hazard management tools
The four critical phases of hazard management do require some work, and when managing hazards manually, much of that work is time-consuming, admin-based and a bit panful.
Luckily for companies big (who have lots of hazard management to do) and small (companies who don't have the resources to focus on safety), there are some great hazard management tools available - which can really streamline how every step of hazard management is 'managed'.
These tools help with hazard identification in the field or on site, with reconciling that information into registers, and tracking the outcomes and performance of those measures too.
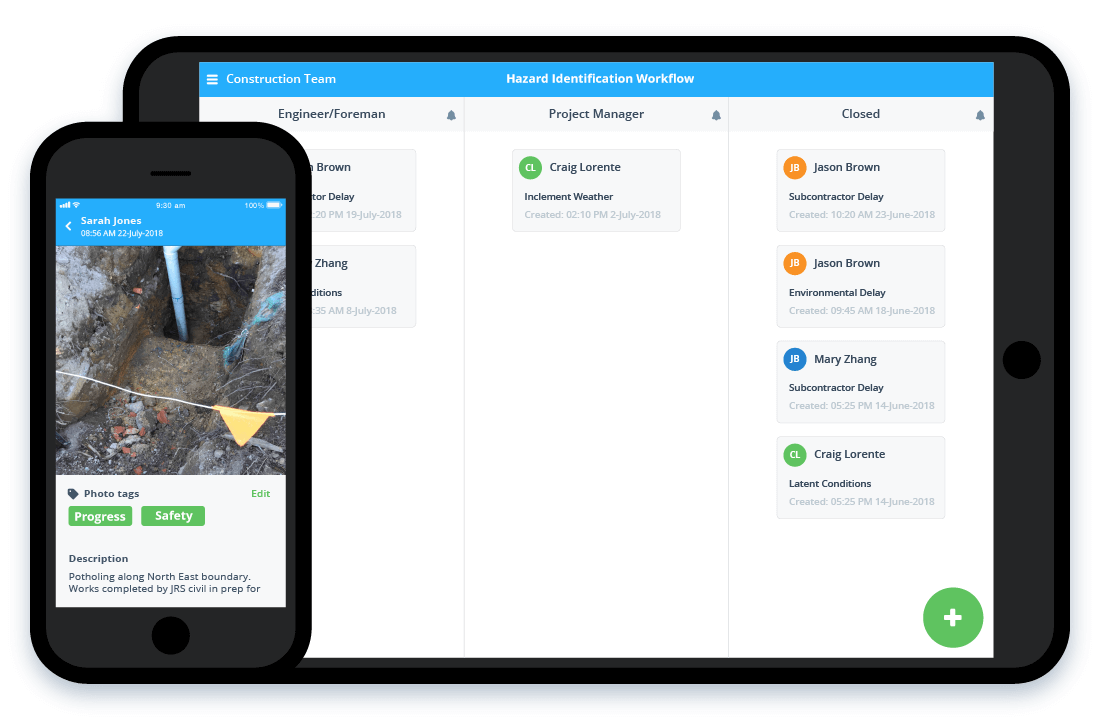
These tools also ensure all of your hazard records stay organised and searchable so you stay compliant and keep all of your procedural and record evidence in one place.
If you are looking for a smarter safety management system, check out some software like this - or get started with a digital template below.
These templates enable you to slowly adopt a more digital and streamlined approach to capturing hazard and safety information, which will enable you to slowly move more processes across and build a more efficient business.
Hazard management isn't easy, but it is a crucial part of project and workforce management for every company.
People in 80+ countries use this software to better manage hazards and other safety processes.
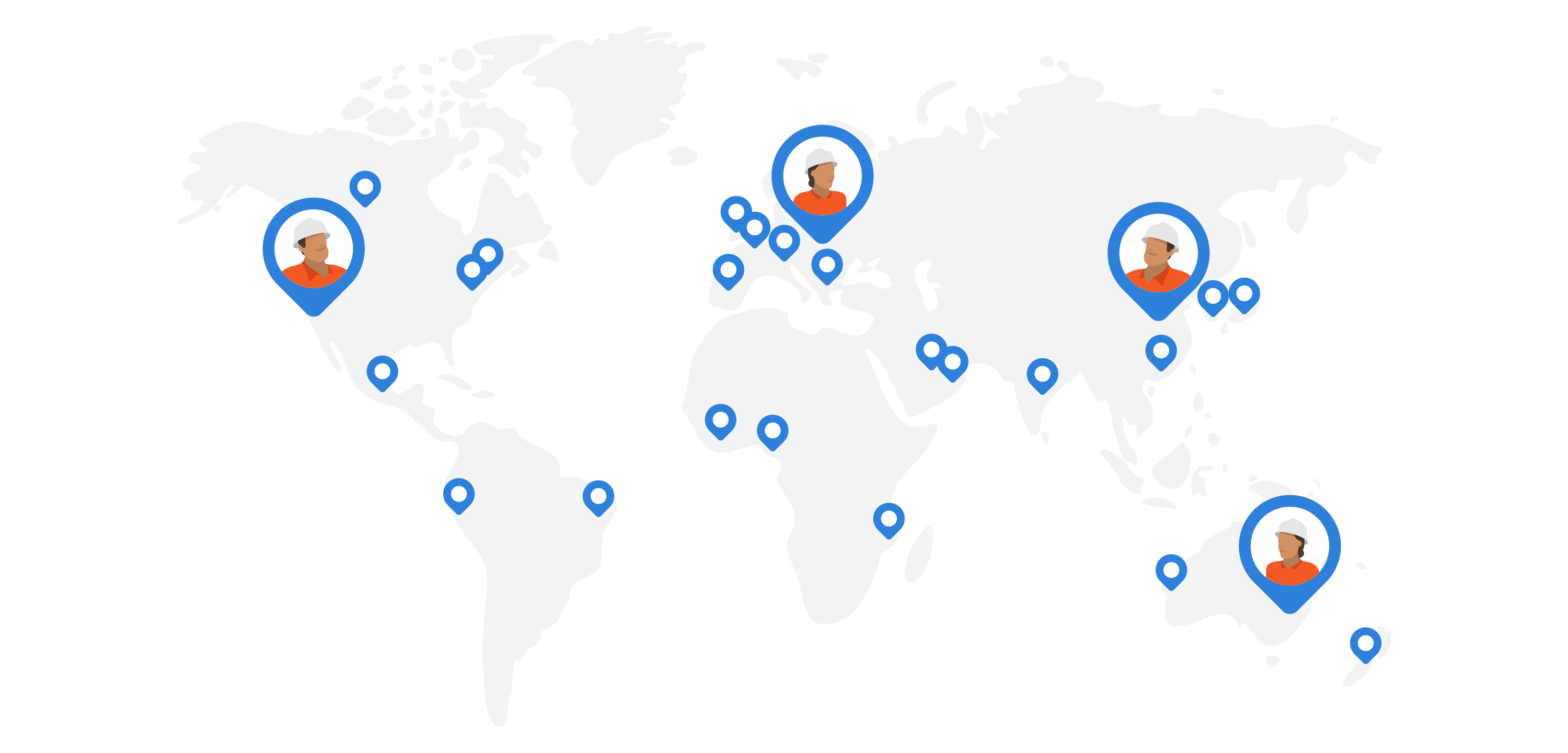