Article Page – Fleet Maintenance Meaning
Fleet Maintenance Meaning
In this article, we’re going to tackle the meaning of fleet maintenance in every way, the process of how to conduct it, the different types and how it differs across industries.
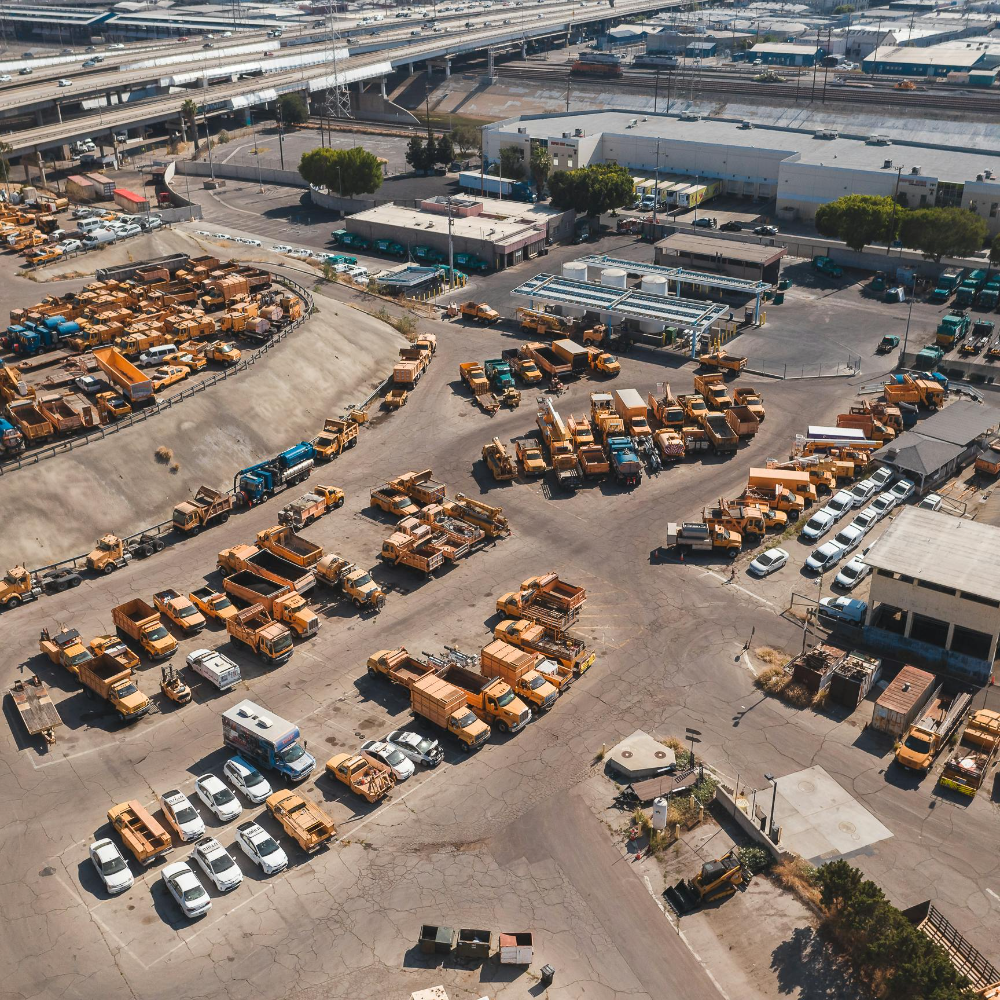
What is fleet maintenance? Meaning and Purpose
If you run a business in construction, delivery and logistics, utilities or even in healthcare or government, transportation is one of the essential resources you need to get things moving–whether to receive supplies or delivering goods or transporting people or animals by air, ship or road. For this reason, fleet maintenance becomes one of the most essential management systems to keep things in order.
Fleet maintenance is the process of preserving the lifespan and quality of a fleet by ensuring safety, reliability and durability of the vehicles. This is achieved through different steps such as:
- Creating a maintenance schedule or maintenance plan
- Developing procedures for conducting maintenance inspections
- Establishing verification methods based on set standards and regulations
- Implementing a system for monitoring these inspections
A fleet is basically a group of vehicles–such as trucks, cars, vans, ships or aircrafts–that are owned and managed by an organization. The way these organizations work in business is that they acquire vehicles whether through purchase or lease, to provide services for clients pertaining to the movement of goods and people or animals.
Since vehicles are subject to intense or frequent use, this naturally causes wear and tear, reduced lifespan and potential breakdowns. Proper fleet maintenance primarily aims to prevent unexpected breakdowns, reduce accidents caused by poor maintenance, and maximize operational efficiency. Being proactive in repair management is crucial for minimizing repair costs, ensuring safety, and maintaining business continuity.
Fleet Management Services Meaning
To gain better understanding of fleet maintenance, it’s important to understand what fleet management is. Fleet maintenance is a key part of fleet management that covers all aspects of monitoring a fleet.
In general, fleet management services include tools designed to track, optimize, and streamline the fleet operations such as inspections, route optimization, location tracking, asset management tracking and telematics. It also involves fuel efficiency management that monitors fuel costs and tracking vehicle’s fuel consumption.
Fleet management services have been evolving over the past years to address common challenges of monitoring the vehicles during transport such as accidents, delays, and asset damage or loss. These challenges pose a threat to the safety of the goods and the drivers.
Therefore, modern fleet and asset management solutions such as fleet maintenance tracking software that incorporate these services are gaining popularity as it combines advance tracking systems, and telematics to improve efficiency and mitigate the risks.
However, let’s delve into the depths of fleet maintenance meaning as it will be the primary focus of this post. In this article, we’re going to tackle everything you need to know about fleet maintenance, the process of how to conduct it, the different types and how it differs across industries.
How to Conduct Fleet Maintenance: Steps & Examples
Maintaining a fleet requires good planning of both the schedule and the procedures, to ensure it is effective and serve its purpose. It also involves getting the right resources to conduct it which includes the competent inspector and the tools necessary for inspection.
Creating a fleet maintenance schedule
The first step of fleet maintenance is developing a maintenance schedule to outline the timing or frequency of maintaining a vehicle. This step goes beyond booking a free slot and making sure the driver, technician and the vehicle are available – but primarily this is scheduling based on necessity.
Factors such as vehicle usage, manufacturer’s recommendation, the usage history or existing condition of the vehicle plays an important role in determining the right maintenance timing. For example, cars with higher mileage requires more frequent maintenance and inspection as components are likely to wear out or reach the end of its lifespan and by putting this in consideration, the vehicle will be scheduled for more frequent inspection.
Fleet maintenance frequency has different types according to its frequency or usage. Let’s enumerate them:
Preventive Maintenance
This is a proactive approach in order to reduce repair costs and ensuring optimum performance and efficiency of vehicles. Fleet preventive maintenance includes regular inspection, parts replacement, cleaning, and lubrication, to make sure the equipment is in good working condition and avoid breakdown during transport. This can be done manually, or with a dedicated preventive maintenance app. Typically, preventive maintenance involves routine oil changes as well as tire and brake checks.
Predictive Maintenance
Predictive maintenance is an advanced method of data analysis used to create improved maintenance schedule. The data considered is historical data of failure or breakdown, real-time data of engine diagnostics, including ultrasonic, thermal, oil and vibration condition analysis to predict potential issues of the vehicle. Predictive maintenance in fleet is either manual or advance in its approach.
- Manual predictive maintenance is quite common in medium to large fleets i.e. 20 to 500 vehicles that often relies on the manual data gathering and experience of the inspectors to predict possible issues.
- Advance predictive maintenance uses Internet of Things (IoT) sensors, machine learning and artificial intelligence to gather real-time data and enhanced data analysis to predict condition of fleet and optimize maintenance schedules.
Corrective or Reactive Maintenance
Corrective maintenance also known as reactive or breakdown maintenance, is when maintenance is performed in a vehicle after a failure or breakdown. The aim is to restore the vehicle to its previous working condition by conducting emergency repair of its system.
A common example for cars is fixing a flat tire, replacing a faulty engine or repairing a malfunctioning part. For ships, corrective maintenance may include fixing cracks, corrosion caused by a collision. In the case of aircraft, it could be landing gear malfunction or fixing loss of cabin pressure or fluid leaks.
Routine Maintenance
Fleet routine maintenance is maintenance conducted to vehicles that could either be usage-based or time-based. Considerably this is still preventive maintenance, but the set schedule is according to its operating hours, mileage, engine hours, and energy consumption. Time-based is according to calendar dates or fixed time interval maintenance of the fleet.
Depending on the necessity, fleet maintenance schedule planning will ensure the condition of the vehicles for it to perform in its optimum level during transportation.
Developing Effective Fleet Maintenance Inspection Procedures
As we have already outlined the inspection frequencies based on vehicle usage, history, condition and manufacturer’s recommendation. The next crucial step in conducting fleet maintenance is developing a fleet maintenance procedure.
Knowing how to develop an effective fleet maintenance inspection procedure is critical in fleet maintenance as this will act as a guide to the inspectors that will conduct the inspection. A standardized procedure will ensure consistency and efficiency of the inspection but will also manage the expectation and communication between the drivers, the technician and the fleet managers.
Effective fleet maintenance inspection procedure involves the following essential components:
Identifying fleet units for inspection
Identifying which fleet units require inspection involves reviewing fleet assets and creating a system for prioritization. This step is closely tied to planning maintenance schedules according on necessity. It is important to have a monitoring system in place such as maintenance log or a fleet management software that are designed to help an organization track the maintenance schedule of a vehicle effectively.
Assigning fleet inspectors and responsibilities
A huge part of developing an inspection procedure is determining the personnel that will conduct the inspection. This is one of the key roles of a fleet manager.
A fleet manager is the in charge of managing the vehicles, in areas of maintenance, fuel management, coordination of personnel who will utilize the fleet. The fleet manager is responsible in identifying and assigning the fleet inspectors. These key persons should be competent to perform the inspections or have undergone fleet maintenance training; however, their duties will depend on their roles. For example, drivers may perform pre-trip inspection focused on visual inspection but may not be qualified to perform repairs. Assigning fleet inspector is a necessary step in conducting fleet maintenance.
Preparing an inspection checklist
A fleet maintenance inspection checklist outlines a comprehensive list of items to be inspected in a vehicle and records if the vehicle is compliant or not in each specific item. This tool is essential for helping the inspectors follow a clear and organized plan during inspection, which also promotes accountability, compliance and efficiency.
Preparing an inspection checklist can save time and allows for a focused inspection especially for fleet managers by ensuring that regardless of who is performing the inspection there is a consistent set of expected outcomes.
Fleet Maintenance documentation and records
Below is an example of a fleet maintenance inspection form, which can serve as a helpful reference for fleet managers when preparing a comprehensive and effective checklist.
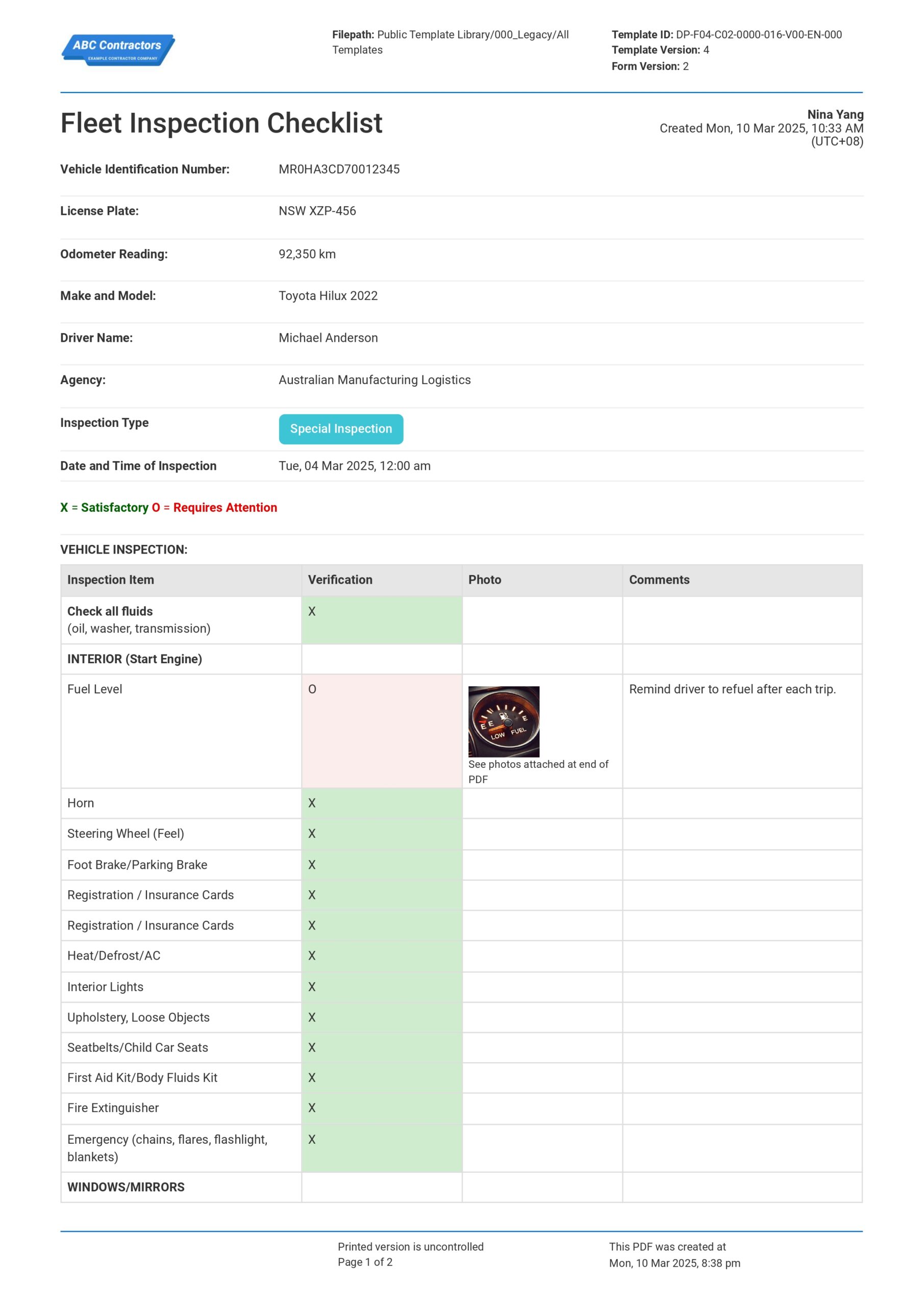
Use this fleet maintenance document framework for your fleet for free.
Establishing verification methods based on set standards and regulations
Once fleet maintenance scheduling and frequency are set along with the inspection checklist prepared, another aspect you need to carefully consider is the verification method.
These verification methods could be:
- Visual Inspection
- Functional Inspection
- Manual Measurements
- Data-Driven testing
Visual and functional verification in vehicle inspection and maintenance involves using your senses to confirm if the component meets the required standard or requires attention. This is usually done through manual methods. For example, when checking the brake fluid level, the inspector must open the hood, locate the brake fluid reservoir, and observe the fluid level against the “Min” and “Max” markings. If during the inspection the fluid level is below “Min” mark, they may need to add brake fluid–or that depends on the scope of the fleet inspector’s responsibilities.
When using a maintenance inspection checklist, you commonly need the inspection item to be answerable by “yes” or “no” to indicate if the check item has complied to the set standards. However, for data-driven analysis such as predictive maintenance, a more advanced verification methodology is required for fleet maintenance inspections. The choice of verification method will depend on the organization’s goal, resources and how much proactive maintenance inspection is valued.
Implementing a system for monitoring these inspections
After establishing a fleet maintenance schedule, developing procedures and identifying how to verify these inspection items, the next crucial step is implementing a system that would monitor the inspections of a fleet. This system should ensure that schedules are being followed, assets such as spare parts are tracked, data is properly recorded and analyzed, and further actions are monitored and followed up.
While a system can be monitored manually and usually sufficient for smaller fleets, for large-scale fleets it would be highly essential if not required to invest in digital tools or fleet management software. These solutions are designed to streamline fleet operations to make it more efficient and accurate especially for data collection purposes.
For data recording, it’s recommended to use a fleet maintenance software especially for large fleets, as it can store and manage sizable documentation. Manual inspection documentation consumes time, can be tedious, and repetitive. Using digital tools to fill out a digital Driver Vehicle Inspection Report (DVIR), for example, would make the process significantly more efficient.
How Fleet Management Differs Across Industries
There are different types of fleets that exist across industries and while fleet maintenance best practices are applicable, each type has its own unique considerations. Now let’s take a brief look at the shipping and airline industry and how it compares to road fleets in terms of maintenance and management.
What is fleet management in shipping?
Shipping is often described as the backbone of global trade, and that backbone wouldn’t function without fleet management. Consumer goods, electronics, medical supplies and raw materials are transported every day via shipping fleets. Managing a single large vessel is already a complex task, and overseeing multiple vessels requires proper planning and coordination. The goal of fleet management in shipping is the same with other fleet industries, it is ensuring operations are more efficient, cost-effective, safe and compliant.
Although both used in transportation road fleets–such as cars or trucks–and maritime fleets differ particularly in fleet maintenance. Fleet sizes are smaller in number in shipping, and the maintenance frequency is more extensive but less frequent compared to road fleets. However, the fundamental logic of how to conduct it similar across both types.
What is fleet management in aircraft?
Fleet management in aviation ensures safety, profitability and cost effectiveness and operational optimization. This is critical in any airline both in commercial and otherwise. It goes beyond simply keeping planes in the sky, it involves meticulous maintenance planning, strict regulatory compliance, and regular or even real-time performance monitoring.
In comparison to road fleets, aviation fleets are smaller in number in terms of fleet size. Their maintenance schedule is highly regulated and strictly scheduled. The complexity is very high covering avionics, engines, pressurization systems and safety protocols. It might seem obvious, but aircraft fleet management is far more elaborate and rigid compared to road vehicles, given that there’s not much room for flexibility once a plane is in the air. The process is both highly regulated and high stakes.
As such, aviation fleet management is governed by stringent international regulations and requires precision at every stage.
Conclusion: Why fleet maintenance matters
In this article we covered all fundamental aspects of fleet maintenance and management. We explored how to conduct fleet maintenance, provided a brief overview of the different types of maintenance, and included general examples to illustrate essential procedures. A fleet maintenance inspection checklist template was included as practical reference. Finally, we looked at the different types of fleet management across various industries.
Fleet maintenance matters—whether it’s for road, maritime, or aviation fleets. Effective maintenance reduces direct costs, promotes safety, and provides peace of mind during operations. It ensures that every asset performs reliably, meets compliance standards and supports business continuity. Most importantly, it helps prevent unexpected downtime—whether on the road, at sea, or in the sky.
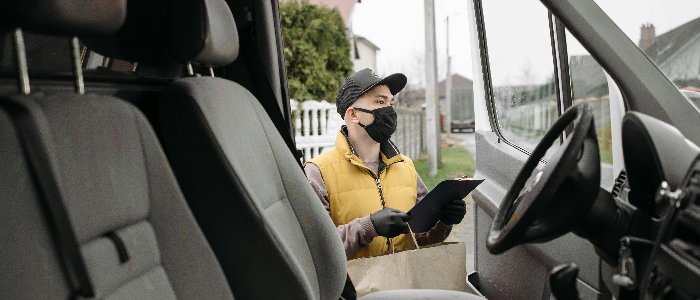
Fleet inspection checklist template
Conduct streamlined and organised vehicle fleet inspections.
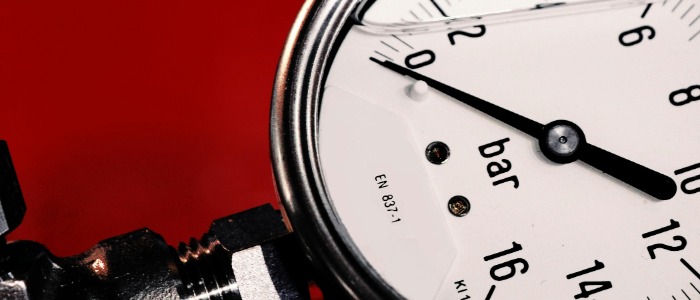
Equipment calibration log
Document, monitor and schedule calibrations using this form and register.
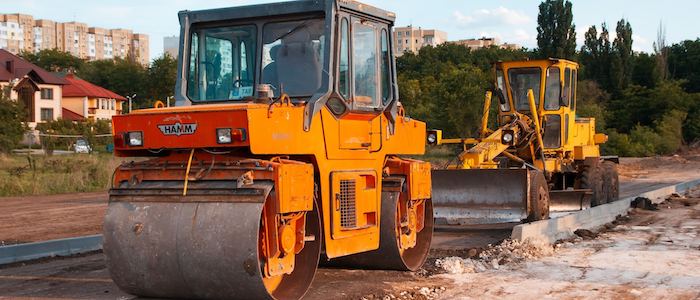
Equipment maintenance log
Improve how you log, track and conduct maintenance on your equipment.