Plant – Lifting equipment inspection frequency
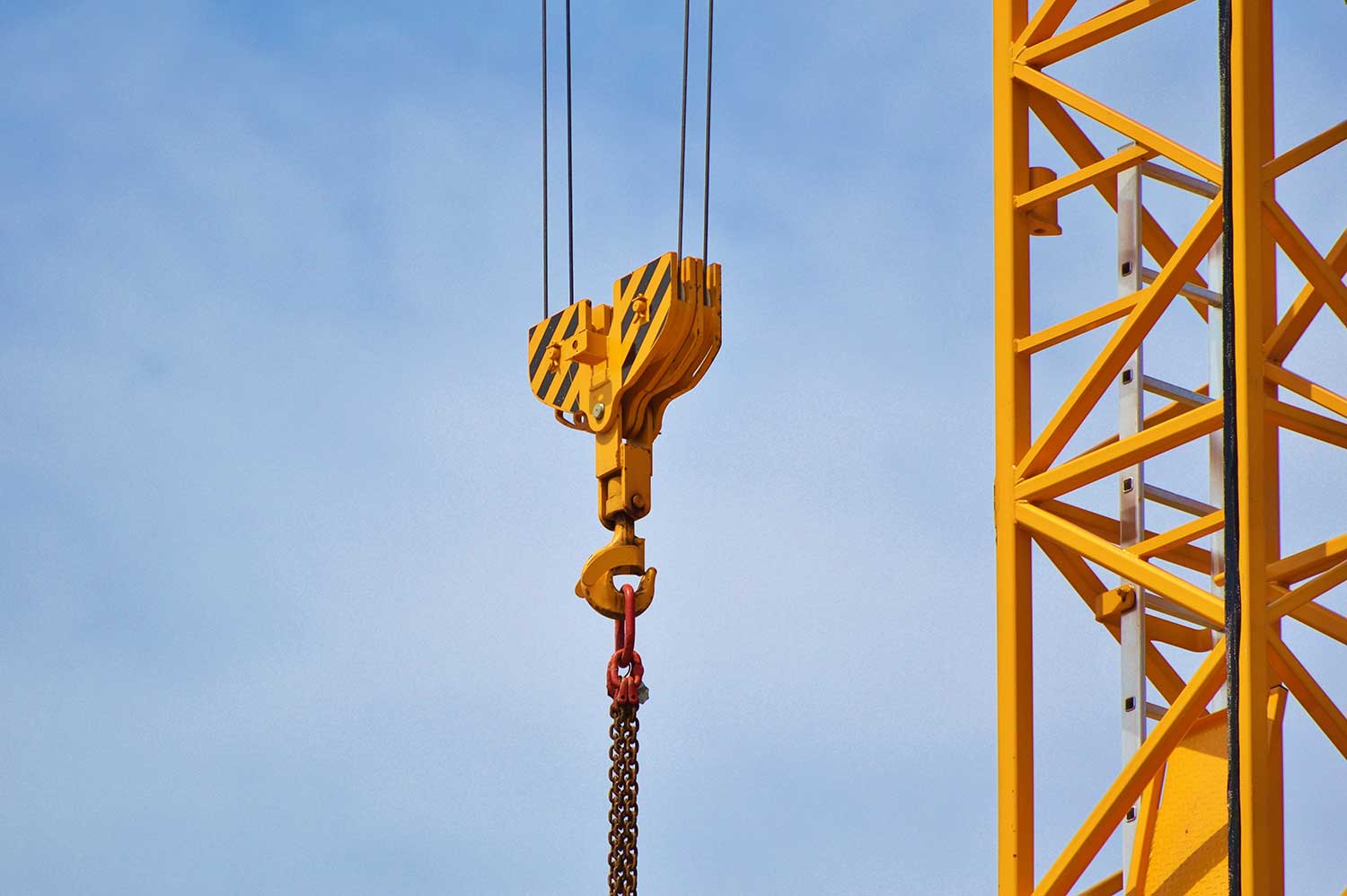
Lifting equipment inspection frequency
The importance of lifting equipment
Different workers and different companies may be referring to slightly different things when they talk about 'lifting equipment'. As a relatively general term, the term usually requires a little more context around the industry and use case to fully understand the exact type of lifting equipment being referred to.
But in most cases, lifting equipment refers to any plant or piece of equipment which is designed to move a 'load' from point A to point B.
So lifting equipment can include hoists, cranes, shovels, forklifts, elevated work platforms, rigging equipment, slings and more.
To anyone who has worked on an industrial site or project, the importance of every type of lifting equipment is obvious.
- Projects and assets are becoming larger, taller and more sophisticated, and sophisticated lifting equipment is required to deliver these projects.
- Workplace and worker safety is more important than ever (and more scrutinised), so ensuring safety for people working at heights and using lifting equipment is a minimum requirement.
- The pressure on contractors and subcontractors to deliver quality work on time and on budget is growing, so 'capital' in the form of lifting equipment and other machinery is vital for speed and quality
In order for companies and projects to minimise the chance of lifting equipment issues, failures and accidents, they engage in lifting equipment inspections. And the procedure and frequency of these inspection is crucial.
The right lifting equipment inspection frequency for you
Getting your lifting equipment inspection frequency is the most important part of lifting equipment management and maintenance, as that dictates whether you are in a position to surface and rectify any of the issues which do arise - before they turn into incidents.
Most countries or local authorities have their own guidelines and rules around lifting equipment inspection frequency, so we are going to focus on the Australian standards today - as Australia is generally a good example of site safety best practice anyway.
Below, we have two examples of lifting equipment frequencies, both of which stems from the general Australian standards.
You may also need to fill in some gaps with other guidelines or materials, and end up with an inspection frequency which will stand up to any audit and stand your company in good stead too.
The below inspection schedule comes from Lifting Victoria (a state in Australia), who have created this inspection frequency from the Australian standards.
The above lifting equipment inspection frequency and schedule can serve as a really reliable framework for you.
Below is some more written detail around inspection frequencies for lifting and rigging equipment pulled directly from the Australian standards:
Inspection guide for alloy chain slings:
1 - 5 lift cycles per week → Inspection required 12 monthly
6 - 25 lift cycles per week → Inspection required 6 monthly
26 - 200 lift cycles per week → Inspection required 3 monthly
200+ lift cycles per week → Inspection required monthly
Inspection guide for height safety equipment
Harnesses, lanyards, associated personal equipment, fall arrest devices, ropes and slings, horizontal and vertical lifelines (fibre rope and webbing) → 6 monthly inspections
Anchorages (drilled-in types or attached to timber frames), anchorages (other types - as recommended by the manufacturer), horizontal and vertical lifeline (steel rope or rail) → 12 monthly inspections
Fall arrest devices → Inspection 12 monthly servicing
Inspection guide for round and flat synthetic slings
All round and flat synthetic slings → 3 monthly inspections
Details about inspections for lifting devices and their capacities can be found here.
So knowing the frequency by which you will inspect your lifting equipment is half of the battle, and the other half comes down to having the right procedure and process in place to effectively document, organise and track all of those lifting equipment inspections.
What do the actual lifting equipment inspections look like?
So what does one or all of these inspections actually involve and look like? This can vary quite a bit from project to project and company to company. Some companies use simple templates which they have downloaded online, while other more specialised companies use comprehensive frameworks and checklists which have been honed and optimised over time.
The other things that increase variation across lifting equipment inspections is that different companies inspect their equipment in different ways.
Some companies may have individual templates and procedures for:
While other companies may roll these different lifting equipment categories into a more general inspection checklist which is applicable to more and often less frequent lifting activities.
You can explore the more specific inspection frameworks above, or browse through and use the comprehensive general lifting equipment inspection checklist you see below.
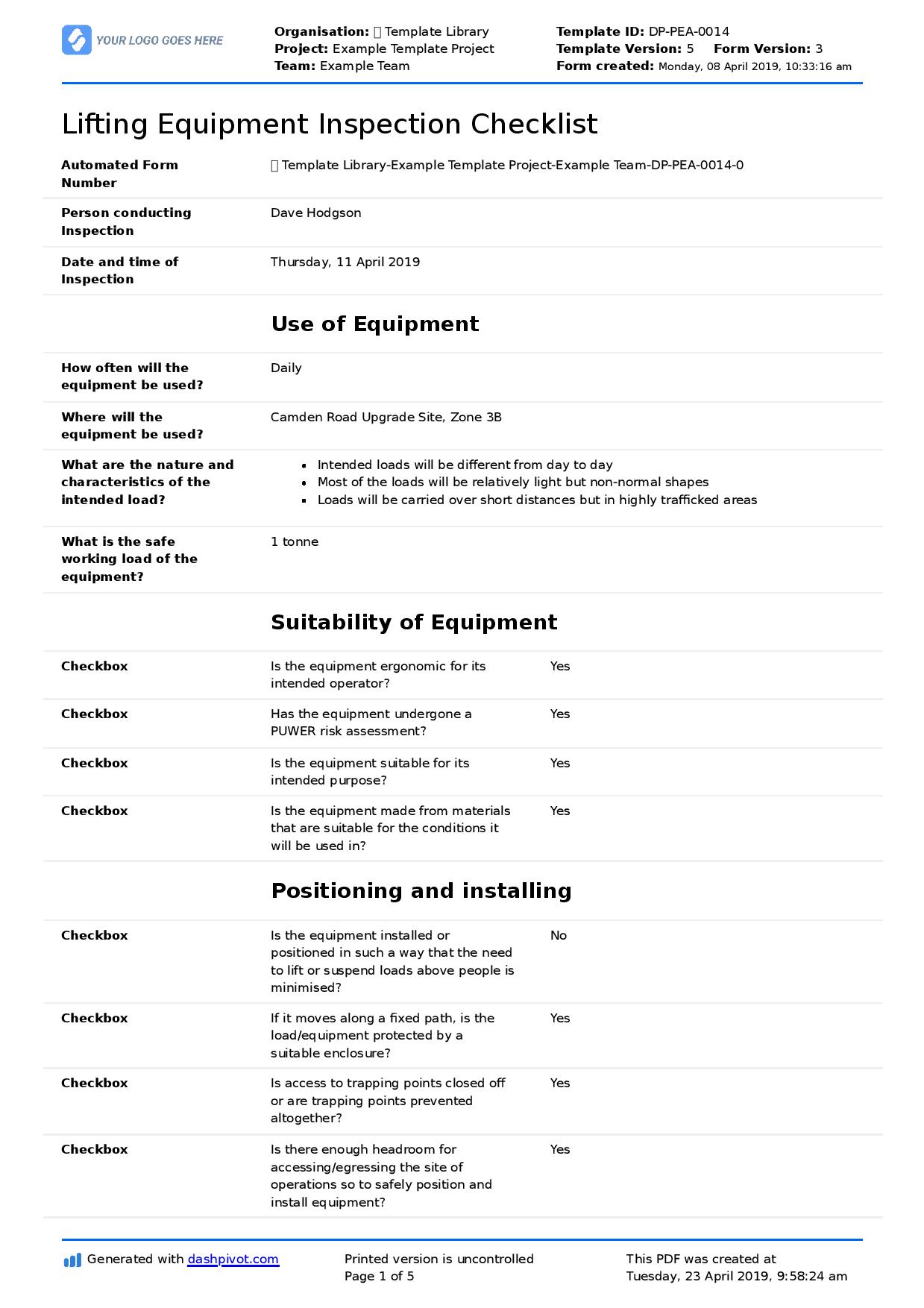
Use this lifting equipment inspection framework for free now.
How to properly conduct your lifting equipment inspections
The equipment inspection problem isn't solved when you have the right frequency and the right template or framework in place.
In fact, many of the issues associated with managing these inspections remain: the admin, the tracking, the accountability and more.
These problems still largely remain because many companies and projects still rely on manual inspection methods and procedures grounded in paper, word docs, spreadsheets and PDFs.
While they have 'worked' in the past, they create a lot of admin and reconciliation headaches, with administrators, workers and safety personnel trying to keep track of when the next inspection should be, who will conduct it, and where it will get stored and actioned.
Luckily, today, there are smarter options for conducting and managing lifting equipment inspections from start to finish through software and apps.
Providing your workers, inspectors and operators with the ability to access and complete their lifting inspection with a mobile device eliminates the need for them to print paper, scan, upload and email reports. Instead, they can instantly open the right and latest version of the inspection template, and the completed inspection is instantly uploaded to the cloud.
From here, the software or system in place can automatically crunch the dates and numbers, and place expiry dates on specific pieces of plant, assets and lifting equipment.
When that life-saving sling is due an inspection, the right person or people will be notified, and they can quickly and properly inspect the equipment, surface any issues, and move on with their work.
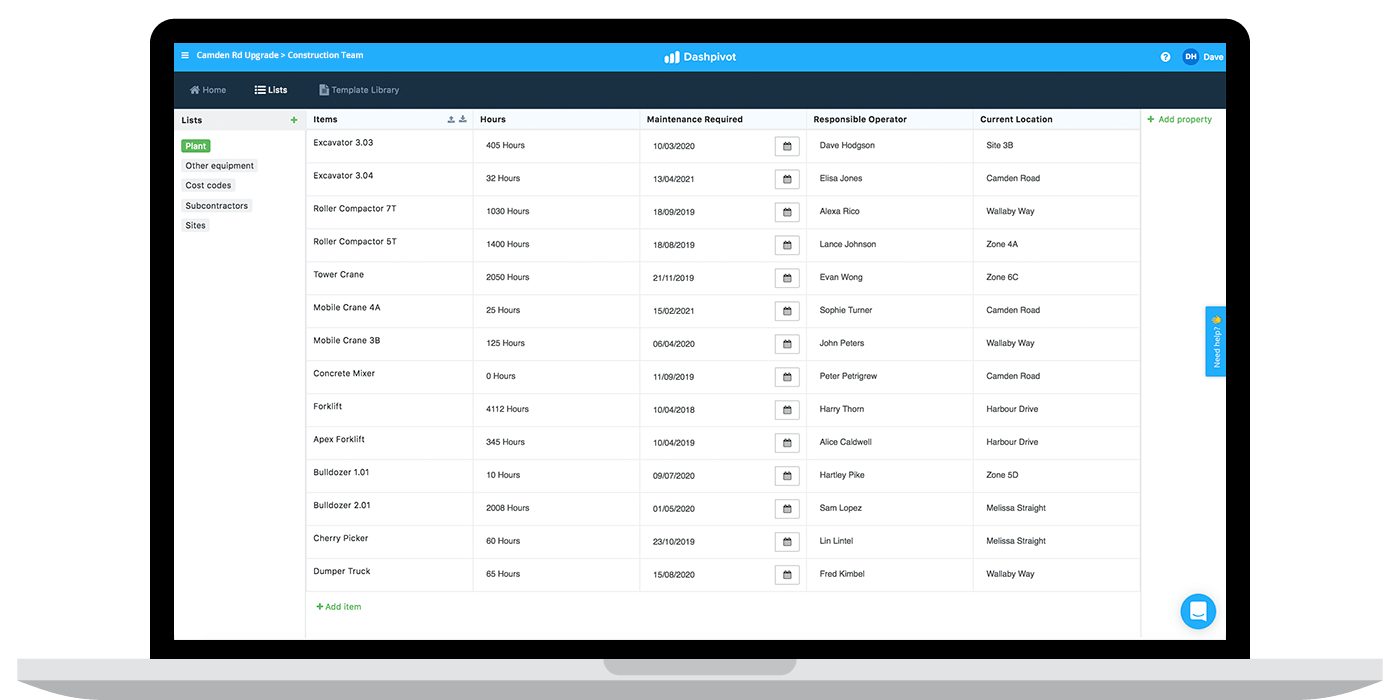
A huge benefit of these softwares, apps and systems is how much time they save, and how much the reduce the logistical and communication issues associated with managing inspections in the most basic way.
But the hidden benefit of these systems is that they don't miss, misplace or forget things.
An inspector or operator may forget to upload the result of an inspection or forget to set a reminder for the next inspection.
While on the surface these issues may appear 'small', we are talking about high risk equipment and extremely high consequence situations, not to mention the legal issues which stem from failing to meet safety and inspection standards during an audit.
A missed sling or harness inspection can be the difference between life and death.
There are easy and affordable ways to better manage your assets and equipment today; to lower the risk of lifting equipment tragedies, improve and guarantee your lifting equipment inspection frequency, and to keep all of your equipment in good and safe working order at all times.
People in 80+ countries use this asset management software to manage their equipment and assets more efficiently.
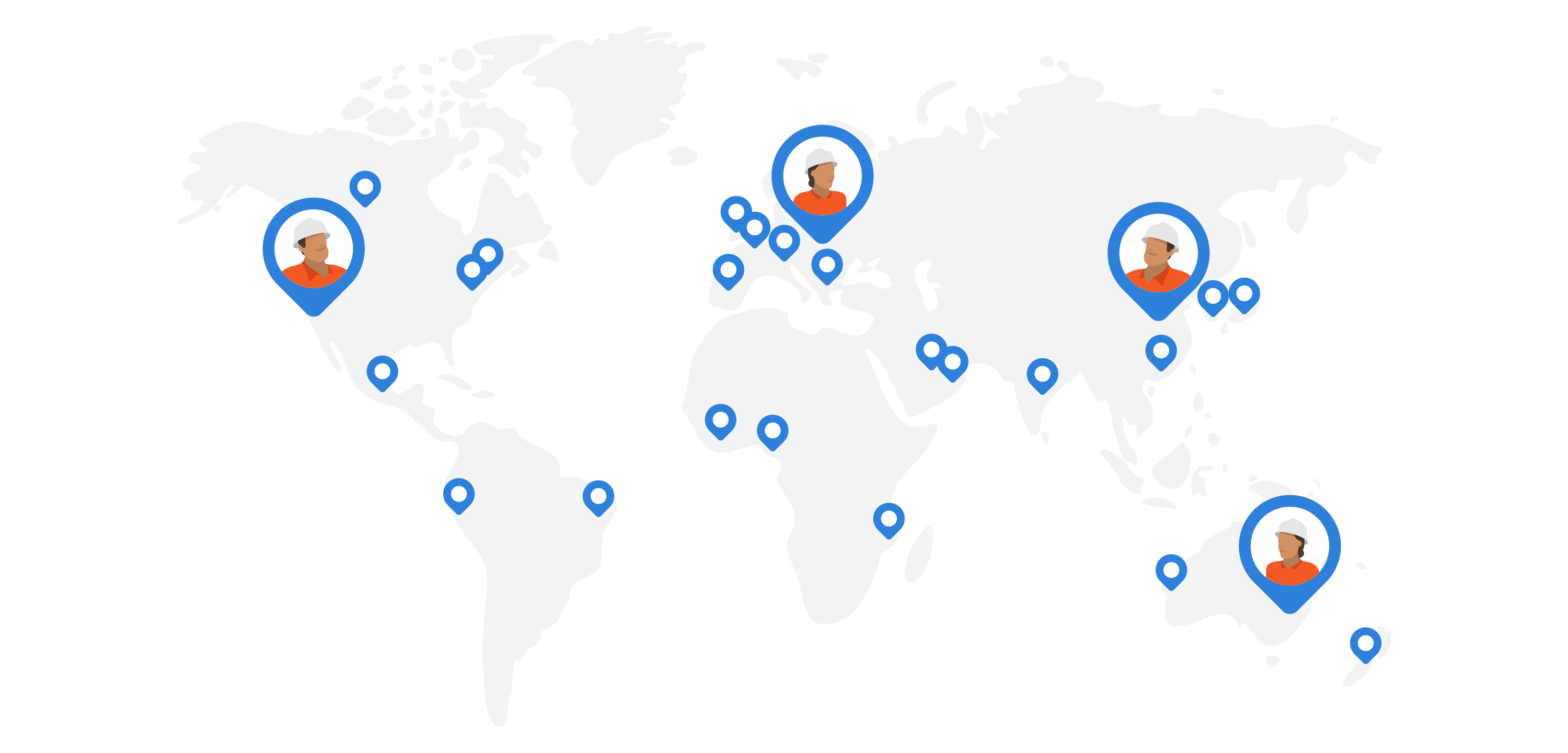