Dashpivot Article – How Long Do You Have to Report an Incident?
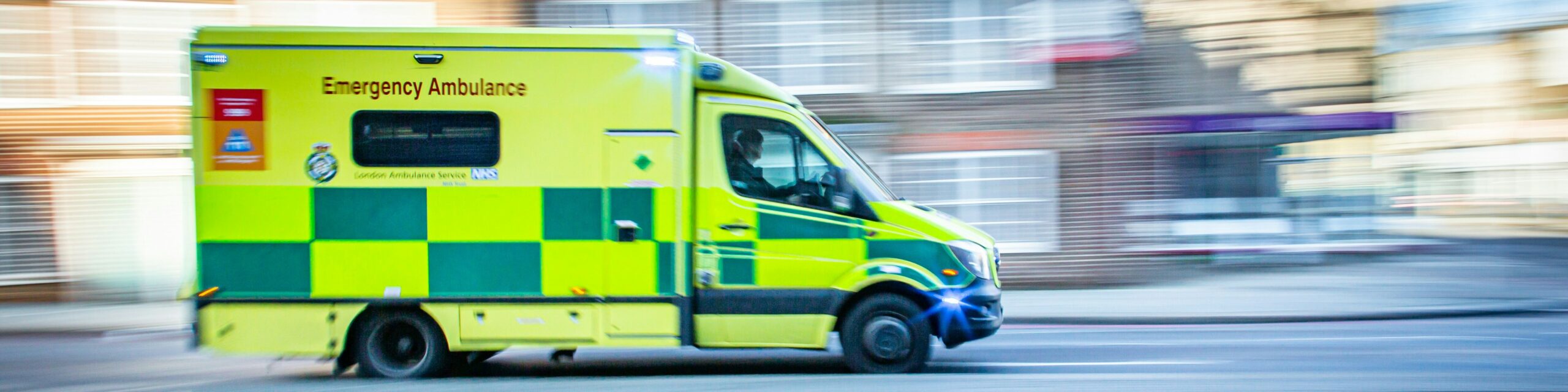
How Long Do You Have to Report an Incident?
Why Incident Reporting Is Crucial for Workplace Safety
Efficient incident reporting is a common struggle by many businesses. In fact, studies show that a huge factor in increasing workplace accidents is because of delayed reports, underreporting and unreported accident occurrences. Human as we are, although it is not our intention to have someone get hurt, it is our tendency to not go through the intimidating documentation of the accident and play the blame game during investigation. Keeping all of this in mind, the question companies (and employees) quickly start asking is how long do you have to report an incident?
Taking a long(er) time to report an incident can cause a number of issues: there could be series of incidents already that could indicate larger problems may be overlooked, important details may be forgotten or lost, and conducting safety audits can become a lengthy and difficult process.
In here, we'll be answering the question: How long do you have to report an incident? But first, we will go through the importance of timely incident reporting in workplace safety, detail the unsafe practices that result to workplace accidents and by the end provide strategies on how to immediately and accurately report an incident to better understand the purpose of speed and accuracy in incident reporting.
Why is timely incident reporting important for workplace safety?
An incident, which is an unsafe event that occurs in the workplace that could potentially i.e a “near miss” or has already lead to a minor or major injury, poor health or fatal accidents. The timeline for reporting incidents are necessary for maintaining a safe work environment and preventing future incidents from happening.
Imagine this: A minor spill occurs on a factory floor. To the workers, it seems insignificant—just a small puddle of oil. No one reports it, thinking it's too trivial to mention and they were about to clock out. A couple of hours later, an employee working for the next shift slips on the disregarded spill. However, it did not result to an injury, the employee took a mop and cleaned it. A week later, a manager walks around the factory for an internal audit and slips to the same area of the puddle of oil, resulted to a sprain and a minor head injury.
The safety task force comes in to investigate and found out that the oil spill was caused by oil leak from one of the machines because the o-ring is worn out. The incident report notes that the problem has been resolved because the o-ring was replaced. In this scenario, the safety issue was only discovered when a serious accident already happened. Of course incident will not occur if there was no oil leak but since it did, it could have been avoided if the first incident of a slip regardless if it did not result to an injury was reported on the onset and the problem was discovered and resolved earlier.
Unsafe practices that result to workplace accidents
Since the act of reporting an incident falls to the responsibility of the all workers in the company, we will put emphasis here the practices caused by human error. Every industry has its own safety protocols that fits to the hazards found in the workplace. When all the controls are in place, and the personal protective equipment are provided, it will fall on the individual on how to take advantage of these safety measures and utilise it to make it effective. The following are the common unsafe practices:
Failure to Attend and Complete a Safety Training
Safety trainings are created to ensure that every employee understands the health and safety risks in the workplace and understand why there are restrictions and rules that is needed to follow as soon as you enter the company gates. Small and large industries invest time and finances to conduct detailed hazard assessments and create controls not only to safeguard the business but because manpower safety is an asset. Despite that, some would still skip out of this training and unfortunately experience or witness occupational accidents first before they sit down and listen. This unsafe practice is not only because of the inability to attend but at times because the lectures are so theoretical and unimaginable that it is hard to believe it could happen, personal schedules would interfere or that it is not mandated and easy to miss.
Complacency to personal safety
Being complacent to personal safety falls under unsafe behaviour of an employee that can result to accidents. When an employee is always in a hurry, that causes misjudgment and bad decisions. Entering the workplace despite being unwell or even intoxicated means the employee is distracted and physically exhausted and not able to make a sound decision that could put them and others at risk. There is also just general complacency – an example is if a worker on a break was in a hard hat area and because for the past 15 years, he had not experienced a falling debris hit him in the head he quickly bypasses the safety and walked around and a piece of wood struck him causing a major head injury. This is an example of complacency because of overconfidence that was built through time.
Ignoring safety protocols inside the workplace
These safety protocols include - safety signs, wearing of personal protective equipment, and failure to report incidents. Safety signs are administrative controls placed in the work area to remind and warn the workers of the hazards identified - whether worker is in the line of fire i.e exposed to hazardous chemical and electrical shocks, prone to get hit by a moving equipment or prone to slip, trip and fall. The last line of defence which are the PPEs are provided to the workers as an added protection and should always be worn whenever necessary. Lastly, reporting incidents like the scenario shared in the first part of the article will help hazards be discovered before worst things happen.
Failure to perform preventive maintenance of the equipments
Machinery saves time, space, and effort in any industry. Almost all are reliant on this small and large machines to produce products and the built world runs smoothly. When machines are in downtime because they break down, it’s a big hit in the efficiency of the organisation. However, performing preventive maintenance does not only ensure the machine is working well but ensuring that it will not create unsafe accidents in the workplace. Routine inspections when done correctly may uncover hazards that can me mitigated early to avoid incidents.
So, how long do you have to report an incident?
Well, immediately. The sooner you can report the faster it urges those involved for a call-to-action to find the cause and resolve it. Workers should never have to think twice whether their situation needs an incident report.
Of course this means they should already know what calls for reporting. Immediate reporting also guarantees that witnesses can accurately remember and evidences are easy to locate.
If there are delays or if there is anything which needs further investigation after the incident occurs, then an incident investigation report is likely.
Strategies on how to immediately and accurately report an incident
Know your workplace guidelines and how long you have to report an incident in the context of your workplace
When the incident occurs, you should know what to do or who to call like the incident response team or safety task force. Responsible companies with solid safety management program usually has a safety task force that is especially assigned to provide a standardised incident report form template that is readily accessible to all employees, investigate the cause, resolve the issue and if possible eliminate the hazard. If an accident happened that cause the employee to be injured, it should be made sure that immediate response has been provided. A workplace that cares about the safety of their employees will have safety signs all over the area to remind everyone what to do in case of danger. Follow your organisation's specific protocols for incident reporting. Pay close attention to timelines, required forms, and designated report contributors.
There is a Free Incident Report form available in Dashpivot that is completely customisable, and makes the job of reporting, recording and mitigating the incident easy, timely and reliable. This is the best way to systematically record the issue, the cause, and even add photos easily or sketch the location of the incident. This form has multiple choice or drop down list fields that details the incident classification that you can customise according to your workplace’s standards. You can simply click a button to provide the direct cause of the incident instead of typing or writing it down manually.
Hold regular toolbox talks to teach people how long they have to report an incident
Toolbox Talks are informal and brief group discussions, usually lasting 5-15 minutes or so, which are held before a work shifts start. These discussions are used to discuss safety issues related to work that can potentially happen or is ‘on the radar’, or work or issues that have already happened. Usually, toolboxes outline reminders, discussion topics, how-tos, and specified safe working procedure regarding presented by a supervisor, safety manager or similar. For example, holding a toolbox talk about incident reporting like this form below.
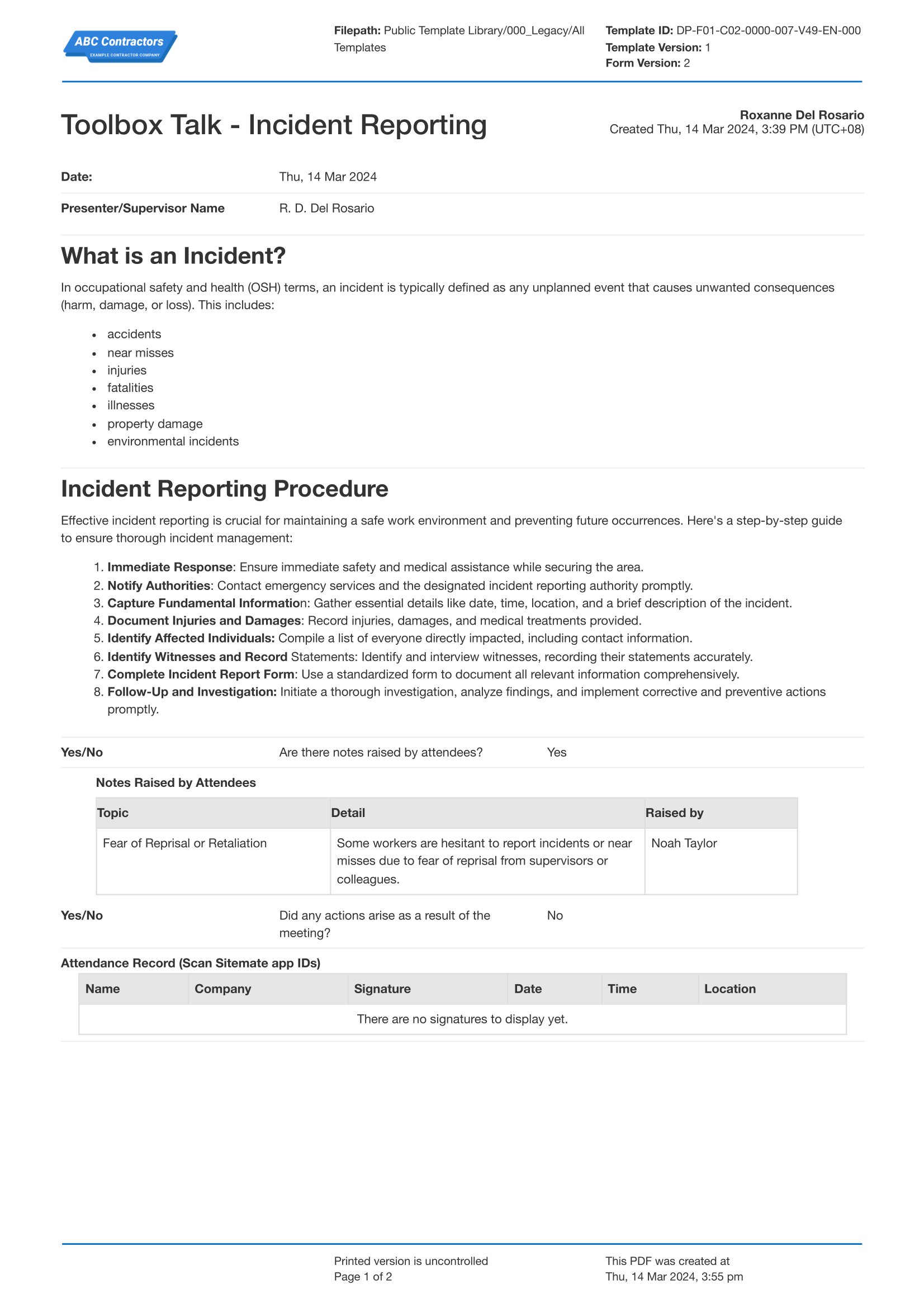
Use this incident report training session form for free
If the talk is about incidents and how long you have to report an incident, the supervisor would set the stage by providing a general summary of incidents on construction sites or other workplaces, re-explain the proper incident reporting procedure, and then explain how long you have to report an incident. After covering the core topics, it would then be opened up for discussion amongst the attendees. This would really drive the home the point around how long a person has to report an incident, keeping it front-of-mind for the team and ensuring everyone is accountable to reaching this safety standard.
This sample digitise toolbox talk form can help the planning and scheduling of action easy to record. You can even set up a QR code poster on site so that the workers can simply scan and access toolbox talks instantly! Getting workers to engage in toolbox talks like this also prepares them for reporting incidents on time. If you have proper electronic incident reporting procedures, then workers could also submit incident reports via QR codes and other digital methods, meaning they are more likely to submit them on time.
Focus on Streamlining Your Incident Reporting Process
In this article, we have covered the importance of timely incident reporting in workplace safety and how long you have to report an incident. We provided a scenario of how an incident could have been avoided if the incident report was not delayed; we enumerated the common unsafe practices that result in workplace accidents and again answered the question: how long do you have to report an incident?
The answer to this question is usually simple: immediately! as this provides an accurate report that will mitigate unsafe incidents in the workplace and ensure that the necessary steps are taken to try to prevent a similar incident from happening again.
Lastly, we provided strategies on how to immediately and accurately report an incident in the workplace by knowing the workplace guidelines and holding digitalised toolbox talks using electronic methods like Dashpivot, which can also be used for incident reporting specifically as well.
Many companies focus on worrying about and tracking how long it takes their teams to report incidents without investing in streamlining the process behind incident reporting through proper incident report software and other tools.
If you want to speed up your incident reporting process, it’s often systems and processes which are the problem, rather than people. So clean up your systems and processes first, and you may just find that people find it easier to align with your processes, like reporting incidents on time.
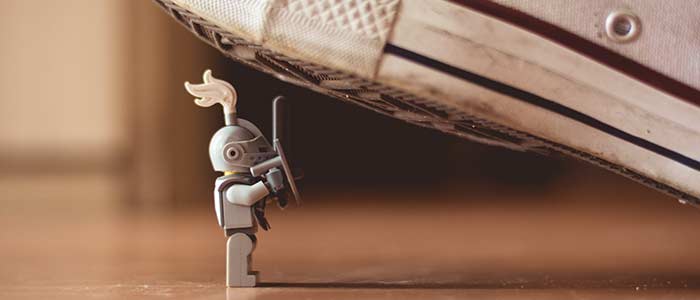
Incident Notification Form template
Document incidents and near misses properly, and more easily.
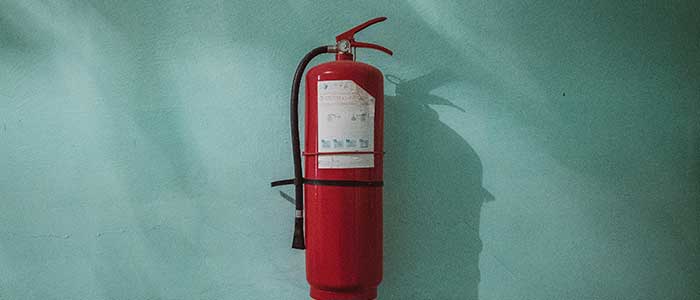
Incident Investigation Report template
When any incident requires further investigation - use this template.
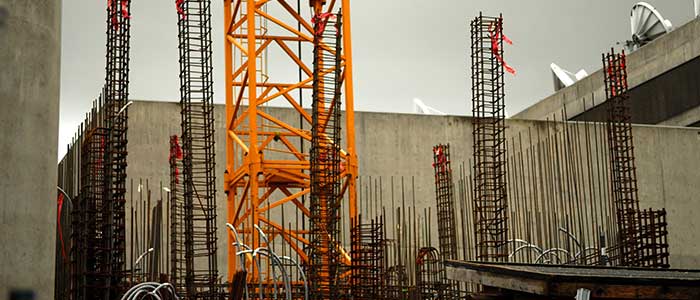
Construction Incident Report template
Streamline how your construction incident reports are accessed and managed to improve safety outcomes and compliance.