Dashpivot Article – Gemba Walk Examples
Gemba Walk Examples
In this article, we cover a number of real-life Gemba Walk examples so you can better understand the critical details of this tried and trusted safety method.
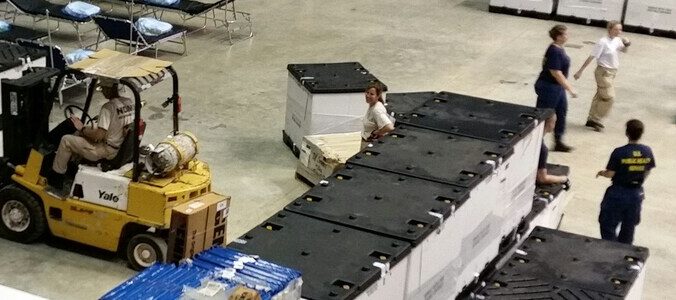
Gemba Walk Examples Intro
Do you know that managers spend 65% of their time in meetings and behind desks and only 10% observing first-hand? And more shockingly, 80% of process improvements come from direct floor-level observations rather than boardroom discussions. The productivity loss is estimated to be about $37 billion a year from the gap between leadership and frontline operations of business. In this article, we'll highlight a number of key Gemba Walk examples and best practices that should change you and your company's thinking around this status quo.
In operational management, the answer to this gap has been the concept of Gemba Walk. From the Japanese term "Gemba," or "the real place," it’s a form of hands-on leadership that has helped companies like Toyota reduce defects by 45% and employee engagement by 32%. Just doing Gemba Walks regularly, even in the construction itself, has allowed an organisation to drop incidents of safety by 28% and complete a project 23% faster.
What is a Gemba Walk?
At its core, a Gemba Walk is more than just a physical walk through the workplace - it’s a structured management practice that changes how leaders interact with their operations. The main purpose of a Gemba Walk is that Instead of staying in their offices, managers or team leaders get out of their chairs and into the actual work environment, engage with frontline employees, document their observations, identify opportunities for improvement, and build stronger relationships with their teams.
Gemba Walk Principles and How to Do It
Now that you know what a Gemba Walk is, it’s time to know the principles and how to do it properly. Here are some things to consider when doing Gemba walks and some tips on how to do it for your team:
1. Observation-First
A successful Gemba Walk is more about observation, and the leaders have to hold themselves back from being problem solvers at first but focus more on the workflow patterns, process sequences, and movement patterns at the workplace to bring out the inherent bottlenecks and inefficiencies that would not have been spotted otherwise.
2. Employee Engagement
The heart of a good Gemba Walk is talking to employees, and having open conversations and asking good questions about processes allows leaders to get valuable insights from those who know the work best. This shows respect for employee expertise and creates collaboration opportunities.
3. Open Mindset
A good Gemba Walk requires leaders to put away their critical eye and adopt a learning mindset, and the goal is not to evaluate or criticise but to understand and learn. This gives employees the safety of mind psychologically to give candid feedback and true concerns over their processes.
Why We Do Gemba Walks: The Objectives and Goals Behind Them
After Japanese companies have been doing Gemba Walks for years, there are multiple reasons why they do it in the first place. While different industries have different results, the same objectives and goals can be benchmarked. Here are some of the objectives and goals to consider to achieve a good Gemba Walk:
Short Term
Gemba walks leave short-term impressions in several aspects, and leaders achieve real-time operations visibility, observing waste and inefficiencies and garnering data from processes. Leaders see safety issues firsthand and identify how resources are being used within different areas.
Long-Term
Over time, Gemba Walks can change the organisational culture, and decision-making improves through observation, communication channels between management and employees get stronger, and a culture of continuous improvement takes hold. In return, teams build stronger relationships, and problem-solving becomes more effective and collaborative.
Gemba Walk Myths
Most people misunderstand the purpose of Gemba walks, which is very important because these walks are not audits, inspections, or performance reviews. These are not opportunities for criticism or casual walkthroughs but a structured approach towards understanding and improving the whole process.
Gemba Walk Examples and Best Practices
Different industries adapt to the needs of Gemba Walks: a manufacturing facility pays attention to productivity and equipment conditions; a construction site ensures safety compliance and work sequencing; in healthcare, for patient care flows and staff coordination; and the service industry looks at customer service delivery and the efficiency of their processes.
Leadership commitment is required for a Gemba Walk, as leaders should take actual interest in the walk and have regular schedules, checking on the insights gathered. Transparency may be achieved through documentation using appropriate forms that are standardised, process timing, and improvement metrics to check progress and validate the impact of the walk on the operations.
Some examples to benchmark with your team while doing a Gemba Walk are the following:
Gemba Walk Example 1: Residential Construction Site
The site supervisors and a variety of trade workers on the residential construction site do weekly Gemba walks with a project manager. In such walks, it might focus on the current construction phase, like framing or plumbing. The manager observes the work, talks to the workers regarding the challenges, and gathers feedback regarding obstacles such as material deliveries delayed by days or inefficient equipment.
For instance, during one of the Gemba Walks, it was observed that workers were spending too much time getting tools and materials from a central storage area located at one end of the big site. After talking to the workers and seeing the issue firsthand, the manager decided to introduce additional mobile storage units and position them across the site. This led to a significant saving in time and energy and a rise in productivity and worker morale.
Gemba Walk Example 2: Commercial Building Retrofitting
For instance, another example of a Gemba Walk is when there is commercial building retrofitting, and in such a case, the focus might be on integrating new technologies or systems into pre-existing buildings. A facilities manager would conduct Gemba walks when installing energy-efficient heating, ventilation, and air conditioning systems in an old building. As one observes the installation process, one could realise miscommunication between the design team and the installation contractors or inefficiencies in how materials are delivered and handled on-site.
For one instance, a Gemba Walk revealed that the HVAC installation team was being sidetracked all too often to adjust other building components that were not caught up well in the original designs. To rectify this issue, the facilities manager helped organise a series of planning sessions with the building engineers and installation contractors to rework and fine-tune the workflow. The preemptive measure thus prevented additional disturbances and produced a relatively fluid retrofit.
Gemba Walk Example 3: Infrastructure Maintenance
Infrastructure maintenance, especially in utilities like water and sewage, can also benefit from Gemba Walks. By visiting sites where maintenance crews are working on pipe repairs or installations, managers can see and understand better the complexity of the task. This direct observation can lead to improvements in safety protocols and the introduction of more efficient tools and technologies.
Such as during a Gemba Walk on a water utility maintenance project where the manager of the crew recognised that they utilised archaic manual locating methods for the underground pipes to be located—time-consuming and often yielding inaccurate results. The company bought modern digital equipment for pipe locations, which also speeds up this process but makes it less hazardous and less error-prone due to damage from the digging area. Gemba walks give managers in the construction and built world industries an opportunity to see and understand their operations better.
These examples show how these walks can lead to operational improvements from residential construction sites to retrofitting projects to safety and efficiency in infrastructure maintenance. As industries change, the Gemba Walk remains a timeless tool for continuous improvement and operational excellence.
See the Gemba Walk checklist template below for how you might document to standardise your process to better perform how you do things:
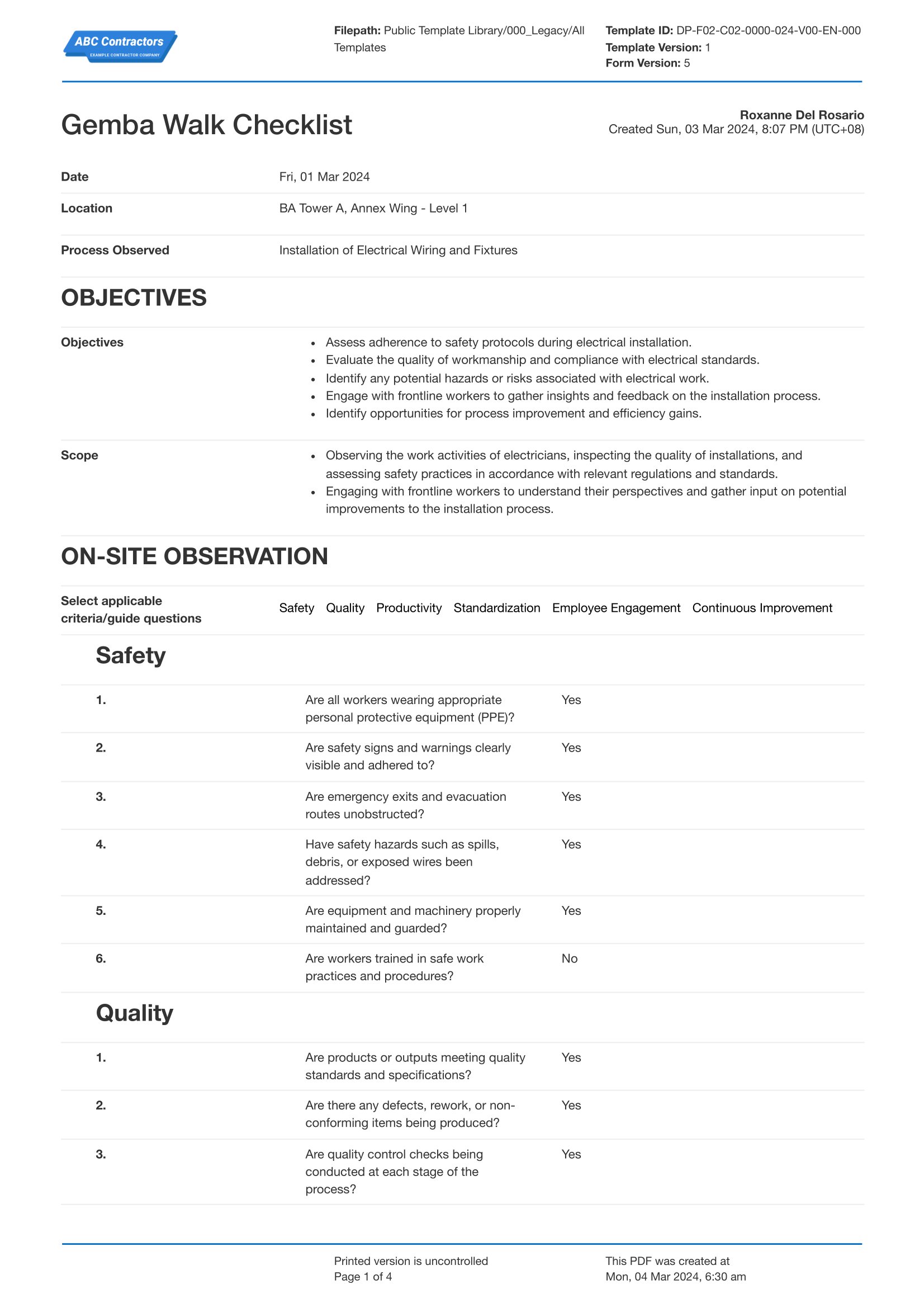
Use this Gemba Walk Example for free
Save time and build better processes with a Gemba Walk solution
While historically, many companies have used paper forms and checklists to run their Gemba Walks, it’s now more common for these walks to be run via a Gemba Walk app or proper system.
The main reason that these Gemba Walks are now conducted via a proper solution is that it will help you and your team manage the processes so they run smoother and you can get more insights; you can also document the walks on-site via mobile or tablet and then sync the data back to the office once submitted.
While on the go, you can take photos from the app, attach them to your Gemba Walk template, and use photo markup to highlight important information such as hazards or something you've seen that can be improved.
You can also incorporate other aspects of your safety paperwork into an app like Dashpivot, which enables built-world companies to streamline these critical processes
The Bottom Line
The culture of the workplace in the digital age is changing because of Gemba Walks, and this breaks the barriers between the management and frontline operations while ensuring continuous improvement and stronger organisations. Regular Gemba Walks have resulted in as much as 40% faster problem resolution and 25% improved employee satisfaction. Current technologies and mobile apps have emerged as innovative adaptations to support Gemba Walks, and to reach excellence, leaders must get in touch with their teams and processes on a personal level.
Kick-start your Gemba walk journey today with the Gemba app and unlock all the secrets.
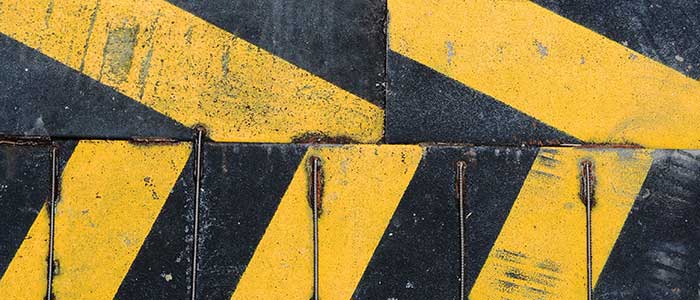
Snag list template
Don't let snags get in the way of project completion.
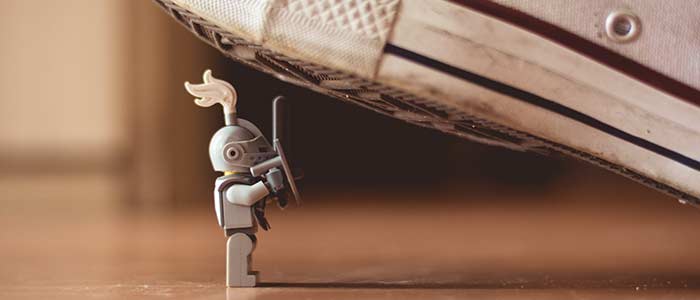
Non-conformance report (NCR) template
Document those painful non conformances with this powerful template.
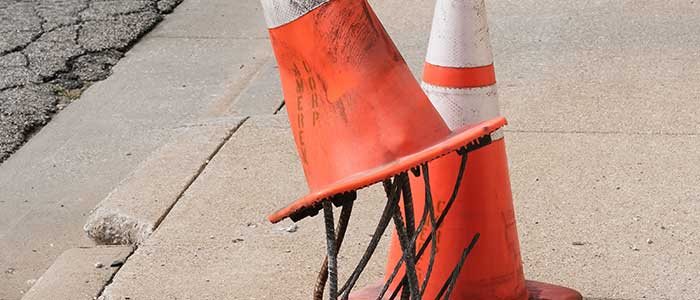
Defect Report template
Manage and rectify those inevitable defects with ease.