Quality – Non conformance procedure and flowchart
Non conformance procedure and flowchart
In this article, we will focus on the critical aspects of nonconformance procedure and flowchart to effectively manage and resolve nonconformance issues to maintain quality and ensure compliance.
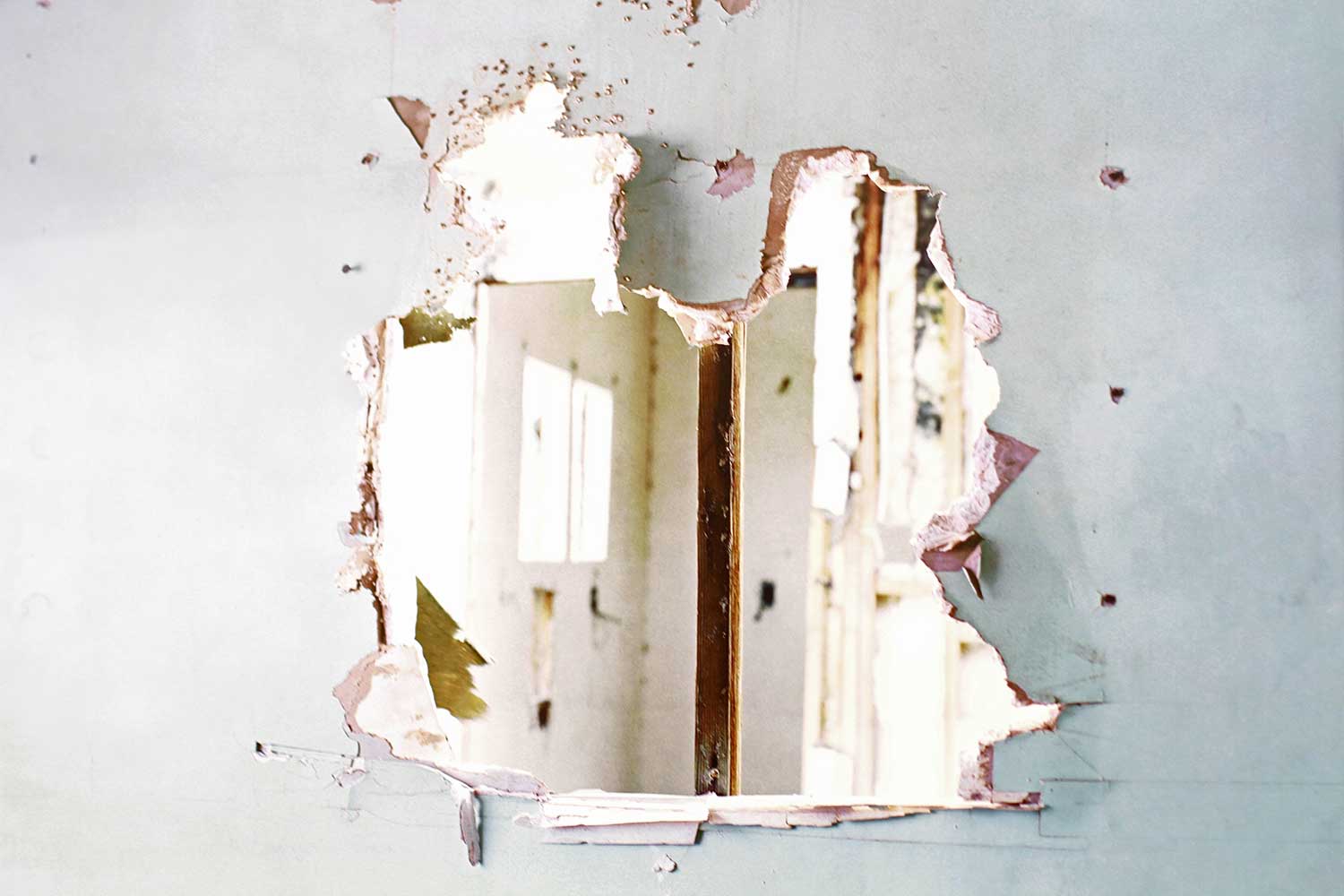
What is a non conformance?
A non conformance 'occurs' when something (a product, process, output, piece of work) does not meet specifications or requirements which were previously defined by a customer, regulatory body, internal procedure or agreement between one or more parties.
In simple terms, a non conformance is a result of something going wrong, either in the output of work or in the process itself.
Non conformances can be extremely costly for a number of stakeholders.
- They can be costly to producers or suppliers who invest at a lot of time and money upfront in inventory and supplies
- They can be costly to contractors and subcontractors who rely on other company's goods and services to get the job done to spec
- They can be costly for consumers and end users who may suffer injuries, issues or fatalities resulting from high consequence non conformances
Because of the high cost of non conformances, companies work extremely hard to create procedures and processes which 'catch' non conformances and action them as early as possible - in the form of corrective actions.
Non-conformances can be reactively identified by customer complaints, inspections or internal/external audits - or they can be proactively identified and rectified through normal testing procedures and good internal processes.
What does a good non conformance procedure look like?
As was foreshadowed above, there are multiple elements and dimensions to a good non conformance procedure, much of which has to do with creating processes which prevent non conformances from taking place.
But because we are looking at the non conformance procedure and flowchart, we will focus on the procedure which takes place after a non conformance has been identified.
The purpose of a non conformance procedure is to document non conformances, action non conformances and to ideally stop similar non conformances from occurring in the future by identifying the root cause.
The non conformance report you see below (NCR) is a framework for following a good non conformance procedure. In practice, it's also how many companies (especially construction and other industrial companies) properly document, action and then track non conformances.
You'll notice that there are a few key elements to this non conformance procedure:
- Identifying and documenting the non conformance (With evidence/proof in the form of photos)
- Identifying who was at fault for the non conformance (was it a supplier, contractor)
- Recommended corrective actions
- Root cause analysis
- Preventative actions which will stop the non conformance from occurring again
- Close out signatures once both or all parties haveΒ rectified and closed the non conformance
When documented in this way, it becomes far easier to see what a good non conformance procedure looks like - and becomes easy to implement a strong framework for non conformances which everyone can use and rely on.
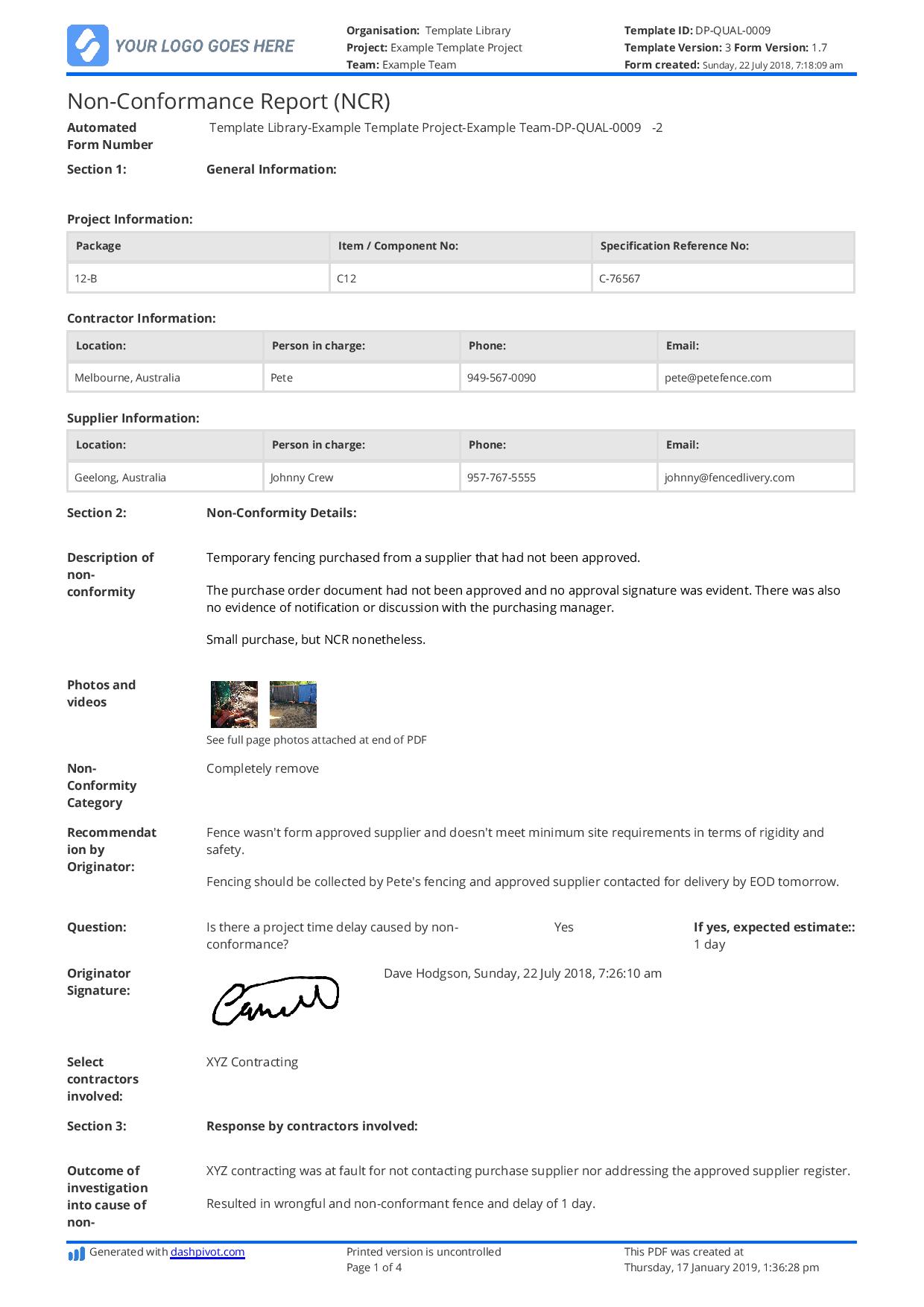
Use and customise this non conformance procedure framework for free.
A non conformance procedure example flowchart
What happens when the person who identifies the non conformance documents it?
Does he or she send it to someone internally or externally?
These questions can be answered by a con conformance procedure flowchart. These flowcharts, which are sometimes 'real' and stuck on a wall or established on a document and other times more informal and understood, enable companies to follow a reliable process for quickly moving and rectifying non conformances.
A good non conformance flowchart or 'workflow' is the workflow which gets non conformances from identification to corrective action as quickly as possible - while touching and informing all the necessary stakeholders.
While companies can have slight variations and nuance in how they setup their non conformances (often guided by how many employees they have), at most companies, this workflow or flowchart looks like this:
- An inspector, auditor or normal employee detects, or identifies and then reports the non conformance
- A manager (sometimes project manager, quality manager) then evaluates the non conformance, confirms who was responsible, and then creates or approves the corrective action plan
- The at-fault party (internal, supplier, subcontractor) then agrees to and performs the corrective action - while working on and collaborating with the initial 2-step parties to establish preventative actions
- Once the corrective action is complete, the teams together (from steps 1,2,3) or a quality management team or manager validate the report and actions, see whether it was effective, and then communicate potential improvements or actions
- Finally, the non conformance is closed and work can begin as normal
Streamlining how you manage and move non conformances through your flowchart
You can probably see already that repeating this non conformance procedure regularly can turn into a logistical headache.
Every new non conformance has a different responsible party, and every non conformance must be dealt with properly.
However, you'll also note from the above non conformance flowchart that the flow of non conformances will remain largely the same for every non conformance on a project or at a specific company.
Because of the repeat and consistent nature of non conformances, much of the work and procedure can be automated through corrective and preventative action software, and smart project management tools.
Workflow management softwares enable you to setup simple automated workflows which streamline how non conformances are managed from start to finish.
Instead of relying on PDF documents, emails and phone calls to figure things out, the entire non conformances flowchart can be automated.
And it works like this.
- When a non conformance is created by the inspector, auditor or worker, it enters the workflow
- When this identifier signs off on the non conformance declaring that all of its details have been captured and documented, the non conformance report then moves to the approvers column, who gets an instant notification that the non conformance is ready for their judgement and approval
- The manager then opens the report, agrees to the responsible party based on the evidence, confirms the corrective and/or preventative actions and then signs off the report
- If the non conformance is external (subcontractor, supplier) then it will then be sent to that party to be actioned and signed; if it's internal, then it will be sent or move internally to be actioned.
- Once the corrective action is complete and signed off, the non conformance will move into the 'closed' column, where it stays for record keeping purposes
With software, all of the collaboration between steps is automated and triggered through approval signatures, with no need to jumping back and forth between documents, systems and conversations.
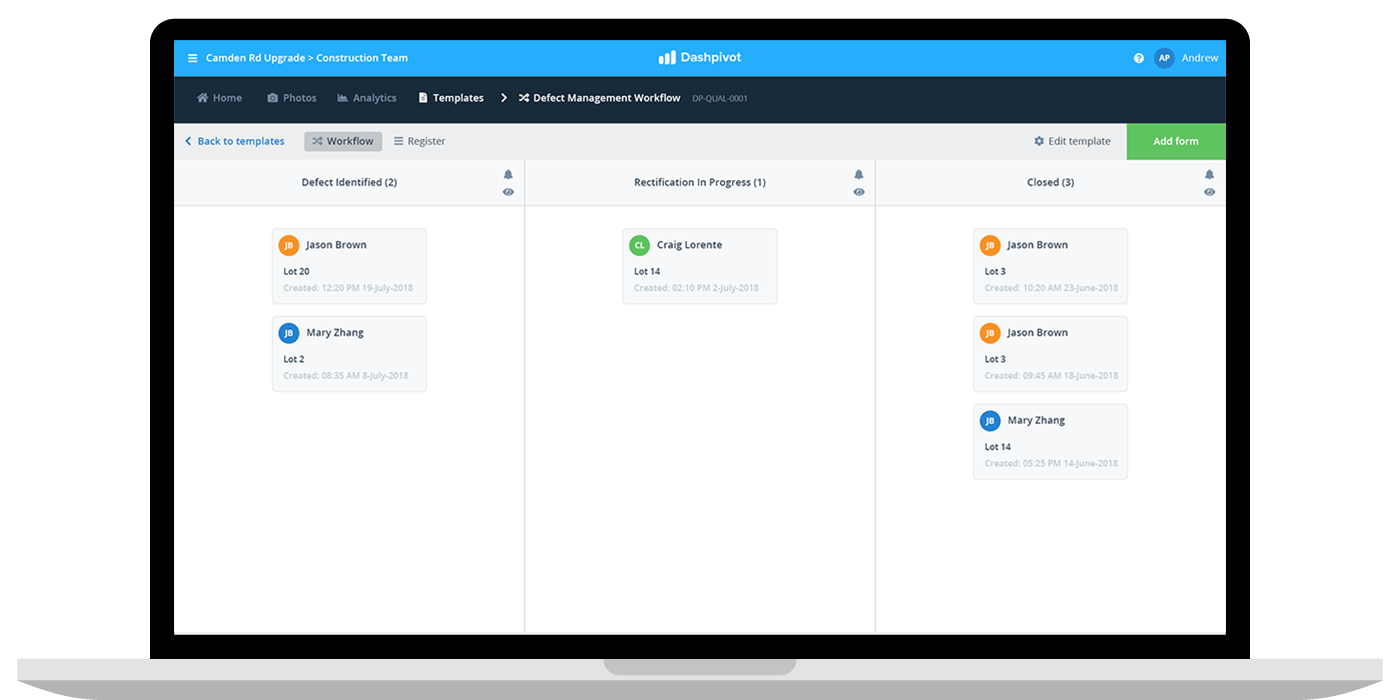
Start improving your non conformance procedure
Quality is of the utmost importance to all companies, and is especially important to companies who's projects have extremely high impacts and consequences such as the building of bridges, manufacturing of important equipment and many others.
Part of ensuring good quality comes down to the right workers and the right company doing the right jobs, but much of it comes down to companies and workers establishing procedures and practices which provide checks and balances on the activities being performed - in a consistent and standardised manner which enables continuous improvement.
Mistakes and non conformances are bound to happen in every industry, but with the right non conformance procedures and processes in place, you are far more likely to catch them and prevent them from turning into disasters.
And with the right non conformance flowchart and workflows in place, you'll have less quality delays and keep your work and projects moving forward quickly and properly.
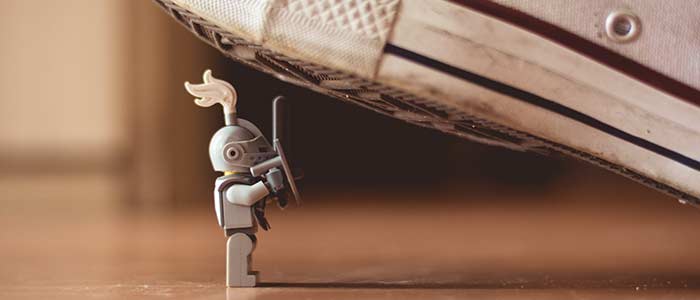
Non-conformance report (NCR) template
Document those painful non conformances with this powerful template.
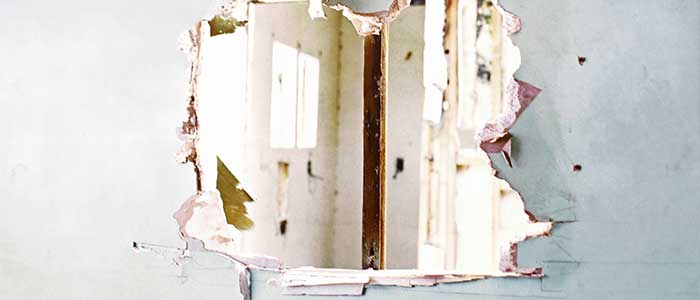
Construction Punch List template
Punch your way through those punch lists with this powerful template.
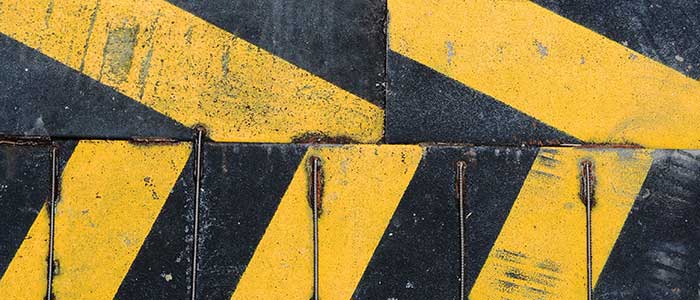
Snag list template
This complete construction snag list template comes pre-built with all the fields you need