Article Page – Equipment Commissioning and Qualification
Equipment Commissioning and Qualification
In this article, we discuss what Equipment Commissioning and Qualification (C&Q) is and how it plays a vital role in quality assurance in supporting key industries like healthcare, pharmaceuticals, and semiconductors.
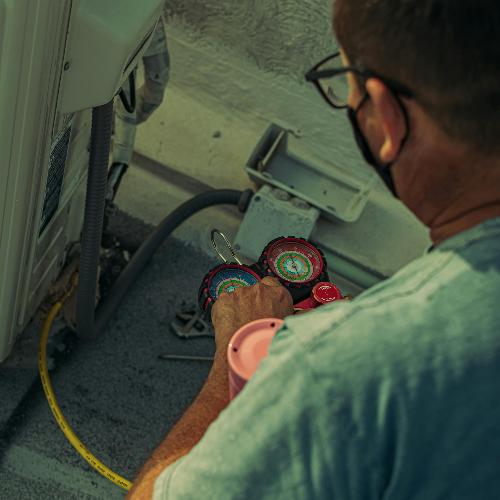
Table of Contents
Article Summary
- In this article, we will discuss the meaning and importance of Equipment Commissioning and Qualification.
- Commissioning means verification that a new equipment is installed correctly and performs as intended.
- Qualification means gathering documentary evidence that a new equipment consistently meets regulatory requirements.
Why is Commissioning & Qualification Important Processes in the Built World?
Commissioning & Qualification (C&Q) are both very important processes because they both ensure the safety and quality of new equipment, facilities and systems in strict-regulation industries. Though terminology may differ across lines of work, the methodology of both processes are similarly engineered towards quality control and assurance.
In highly technical and regulated industries like biotechnology and pharmaceuticals, qualification is a strict process and a regulatory requirement (under FDA 21 CFR Part 211, EU GMP Annex 15, and ICH Q7/Q9/Q10) to ensure consistently safe and quality products.
These processes are highly relevant in industries where public safety is a concern, such as the healthcare industry, or other critical, highly-technical industries like the semiconductor industry. If you’re work is involved in the construction or installation of infrastructure to support these industries, you will need to be well-versed with industry best practices to perform proper qualification and commissioning.
How Do You Format an Effective Commissioning and Qualification Program?
Commissioning and Qualification are both meticulous processes that require comprehensive documentation from start to finish. Depending on the specific equipment commissioning procedure and the governing/regulatory body in your region, you may have to adjust your workflow to comply with manufacturer or government regulations.
But before you even begin, you will need to ensure that your project area is safe and all relevant protocols have been noted and followed. Many companies have opted to use pre-start checklists in order to track all these protocols and to ensure that they have been complied with. These checklists also act as mediums for transparency, as it allows for future review of the procedures that are in place. The example shown below should give you a better picture on what a good pre-startup safety checklist should look like.
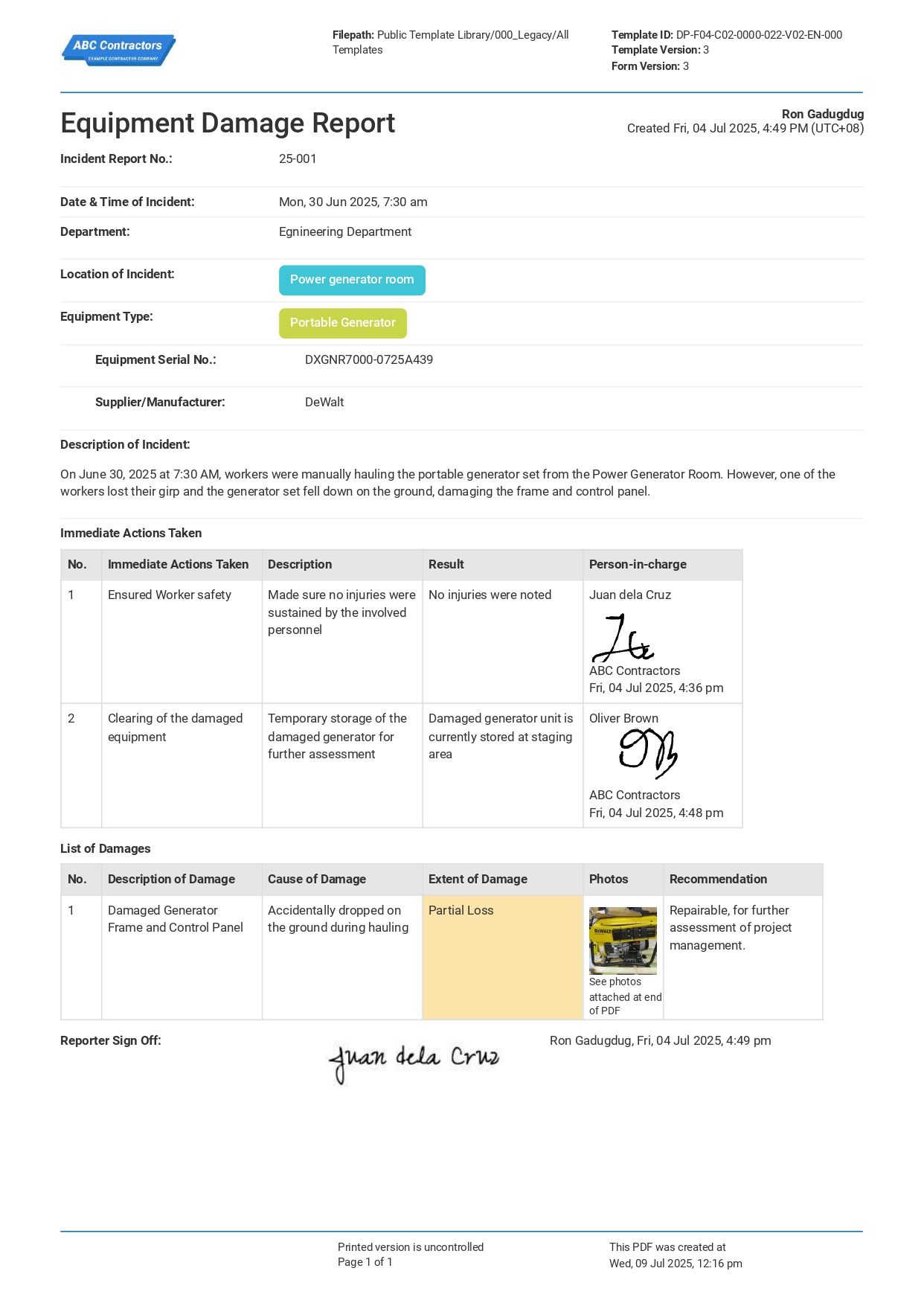
Use this Pre-Startup Safety Review Checklist for free
Why is Commissioning Electrical Equipment and Machines Important?
Commissioning Electrical Equipment and Machines are important because it assures us that the said equipment have been installed correctly, perform as intended, and have been properly integrated into its specific operational system before it is put into normal use. Mechanical & Electrical Equipment used for a building’s operational systems, such as HVAC, FDAS, Power & Electrical Systems, etc., are often, if not always, composed of many electronic parts. These parts are often sensitive and fragile, and will need expert care and handling during the production, transportation, and installation of your equipment.
To prevent scenarios where these equipment don’t quite live up to expectation and design, suppliers and contractors alike have set protocols to safeguard the Owner (who owns the building) from unforeseen losses that may arise. Warranties, lock-in servicing periods, and consultations are usually provided as an after-sales service by the supplier. While these things are nice to have for assurance, you wouldn’t want any unforeseen losses to happen in the first place. As the saying goes, prevention is always better than the cure.
This is where commissioning your equipment becomes critical. Proper testing & calibration of the equipment and integration into your system before it is put in to regular use is an important step to make sure your equipment is capable of withstanding the designed load. Ultimately, it is a vital step in the turn-over process that you will have to accomplish in order for your work to be accepted by the Owner.
What is Equipment Commissioning and Qualification?
As we have previously established, equipment commissioning is the systematic process of testing and calibrating a piece of equipment to ensure that it performs as per design specifications before it is put into regular use. This is most usually performed after your equipment is physically installed and before normal operations begin.
On the other hand, equipment qualification can be understood as a validation process and is generally accepted to be part of the overall Commissioning process. It refers to the task of gathering and vetting documented evidence that a certain equipment is capable of producing the intended output consistently, ensuring safety and quality over a certain amount of time. Qualification is commonly seen as a requirement for new equipment intended for the pharmaceutical, biotech, & healthcare industries, as there are increased risks of greater losses in these industries.
A simple analogy: Commissioning is like testing an entire car and all of its components (lights, radio, brakes) to ensure everything works as intended. Qualification is like testing and documenting evidence that the seatbelts lock and airbags deploy consistently as designed, because lives depend on it.
There are three core qualification activities that you must consider when performing proper C&Q: Installation Qualification (IQ), Operational Qualification (OQ), and Performance Qualification (PQ).
Installation Qualification (IQ) refers to tasks that verify & document the correct installation of new equipment or systems. These tasks include:
- Verifying & Documenting equipment specifications and serial numbers
- Cross-checking installation versus plan design
- Verification and safe-keeping of equipment manuals, warranties, and certificates
Operational Qualification (OQ) refers to tasks that verify that the equipment and all its parts operate as advertised. These tasks include:
- Testing of any alarms, sensors, breakers, and other emergency measures
- Verifying operational ranges and conducting challenge tests (ie. temperature, pressure, speed tests)
- Checking for proper integration with any software, or into other systems, as needed
- Producing test results with pass/fail criteria
Performance Qualification (PQ) refers to tasks that ensure the new equipment performs and produces the intended output consistently over a certain period of time under regular load or working conditions. These tasks include:
- Producing actual products/material, or running the system to verify output
- Verifying repeatability or consistency of output
- Ensuring output meets pre-determined standards or industry regulations
What is the Commission Equipment Definition in GMP?
In the context of Good Manufacturing Practices (GMP), Commissioning Equipment does not deviate far from standard equipment commissioning procedures and definitions. However, given the higher risk of greater potential losses, there is greater sense of urgency in the installation, testing, inspection, and qualification of these new equipment. This is highly relevant to equipment that are to be used in industries like pharmaceuticals, healthcare, biotechnology, food, cosmetics, and other highly critical fields.
GMP is a set of agreed-upon guidelines and practices that ensure products are safe, of quality, and effective. These regulations are enforced by several national and international regulatory bodies like the US FDA, the European Medicines Agency, and the Therapeutic Goods Administration in Australia.
Improving your Equipment Commissioning and Qualification Processes
With all the inspections and tests that you will have to conduct during the Commissioning & Qualification process, it won’t be easy to document, keep track, and archive all the necessary documents. Tracing these documents will get messy if your team isn’t ready.
Fortunately, you can use the Inspection and Test Record App to help improve your team’s workflow. Alleviate the labor intensive, paper-centric workload by using this app to document inspections, record test results, and sign-off on reports.
Summary of Article
The definition and application of Equipment Commissioning and Qualification can overlap in some instances, especially in the context of critical, GMP-related industries. However, one can understand the distinction as a difference in regulatory urgency.
Commissioning Equipment refers to practices that ensure a certain equipment is installed correctly and performs as intended before it is put into use, and is usually implemented across the board. While Qualification refers to practices that gather evidence that equipment produce quality output consistently, and are usually performed for new equipment in fields where there is greater likelihood of substantial, compounding loss or where products directly affect the safety of the general public.
Frequently Asked Questions
Is Commissioning & Qualification required by any regulatory body?
Yes, Commissioning and Qualification of new equipment is strictly required and regulated by Good Manufacturing Practices in industries like the pharmaceutical, healthcare, and semiconductor industries.
How does technology improve current Equipment Commissioning and Qualification practices?
Technology plays a significant role in ensuring the Commissioning & Qualification process is executed correctly and consistently. New devices and methodologies allow for more comprehensive testing, and digital tools like allows for seamless coordination and archiving of relevant files.
Does Sitemate offer templates I can use for Commissioning & Qualification?
Yes, Sitemate offers different templates you can use to improve your Commissioning & Qualification procedures. Several companies use our templates to improve their workflow and streamline processes.
Related resources
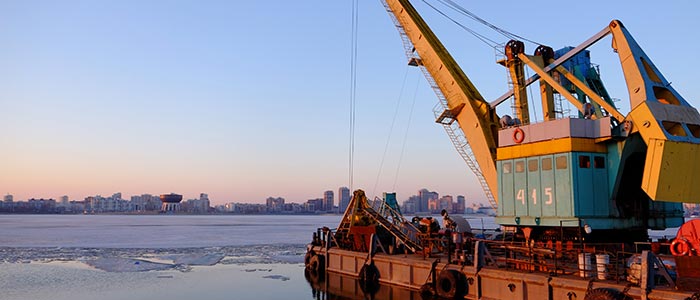
Site diary template
Complete and organise your daily diaries more efficiently.
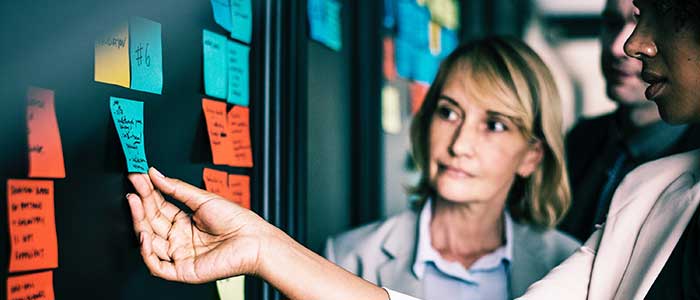
Meeting Minutes template
Capture, record and organise those meeting minutes.
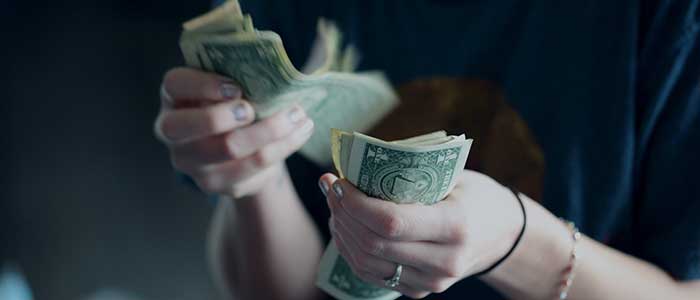
Progress Claim template
Streamline and automate the progress claim process to get paid faster and look more professional.