Quality – Quality control procedures in construction
Quality control procedures in construction
In this post, we break down quality control procedures in construction in a simple, relatable way, explaining why they matter and how to put them into practice using proven frameworks which we also provide in the post.
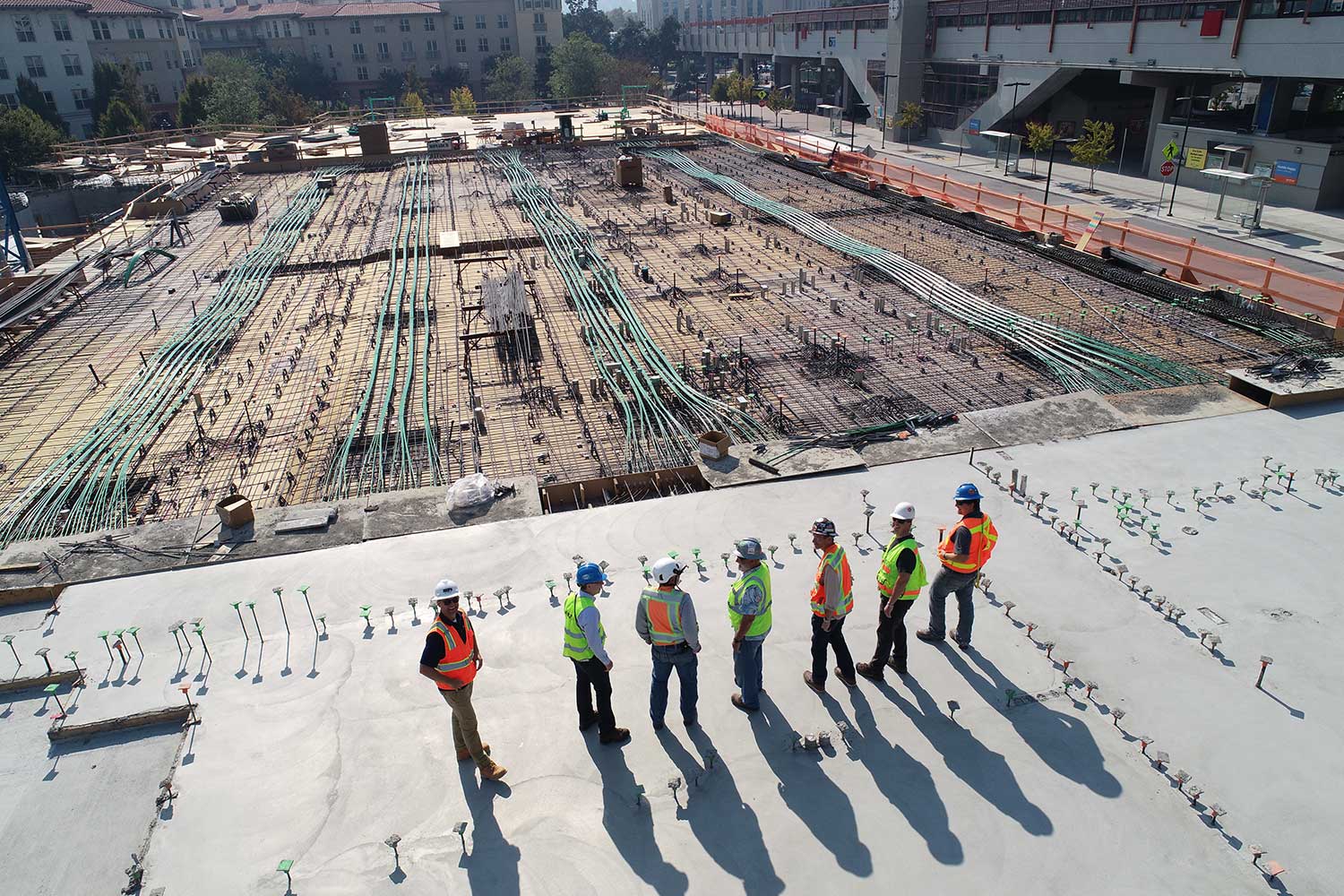
What are construction quality control procedures?
Construction quality control is at the heart of the construction industry. Construction projects create and deliver the assets and infrastructure which people rely on to move around and conduct life safely. Because of this - every supply, every piece of equipment and every activity conducted on construction projects must be conducted in such a manner that quality can be almost guaranteed. And where it can't, there must be adequate testing in place to catch these mishaps and rectify them before the end of the project or end of that phase of works.
Quality control procedures are a code of guidelines (usually written down and kept in quality documentation) which set and establish the quality standards and norms which ensure consistent quality across the company and across projects.
Many of these quality control procedures don't originate in thin air and aren't down to interpretation. They are often minimum standards derived from standards set by authorities, governing bodies and governments. In fact, your quality control procedures are often simply aligning your project and company activities with these ISO and other standards - and then bolstering the edges and inputs where required.
What is the objective of quality control procedures?
It can be easy for companies to get caught up in documenting and creating quality control procedures for the sake of it and making it up as they go along. It's important to ground these documents, both when creating and maintaining them in the overarching objective ofΒ delivering better work, every day.
And the way in which companies do this is by creating systematic and uniform approaches to getting work done.
Without these processes, there is too much room for interpretation amongst teams and the standards of the organisation aren't clear.
While there is always an established minimum standard for work, construction companies - and particularly successful ones - raise the bar for quality on a consistent basis.
So the objective of quality control procedures is to establish the quality requirements of your company and workers whilst seeking to continuously improve the quality of work over time.
The goal of writing these procedures down and putting them onto paper is to ensure internal and external consistency. Often times, these procedures - especially on the construction industry - are incredibly complex and multi-faceted. They need to be written down to be properly understood and applied.
Implementing quality control procedures on your construction projects
So the mechanisms for creating and 'keeping' these quality control procedures are quality policy and procedure documents. These documents can long and short, and contained in word docs, PDFs, excel spreadsheets and more.
But these documents in and of themselves do not create quality work. Workers may read them and see them on a daily basis, but it's at the project execution level where the rubber meets the road and where quality either hits or misses.
Your quality control procedure documents should contain information and guidelines as to how total quality management will be maintained including:
- Physical quality guidelines
- Inspections, approvals and certifications
- Inspection and test plans and certificates
- Methods and sequence of tests
- Acceptance and rejection criteria
- Key control points
- Performance specifications
- Visual quality
And then you will implement these procedures through the daily processes of your workers: engineers, foremen and project managers.
These workers are capturing, organising and tracking what's happening on your construction projects, and they are the real extension and implementation arm of your procedures.
They are documenting the inspection test plans; they will create and communicate snag lists; they will initiate hold points and witness points and monitor all aspects of quality management.
You may also have some intermediary quality documents which sit between these execution layer and the procedures - such as the project quality management plan below. These documents establish specific plans and processes for each unique project.
Policies and procedural documents will often be linked to and reference the high level quality control procedures to ensure consistency.
But your quality control procedures will be generally two pronged:
- Quality control procedures sets the quality plan, strategy and guidelines for work
- Quality control processes enable companies to adhere to these procedures and achieve their quality goals by implementing these procedures on a daily basis
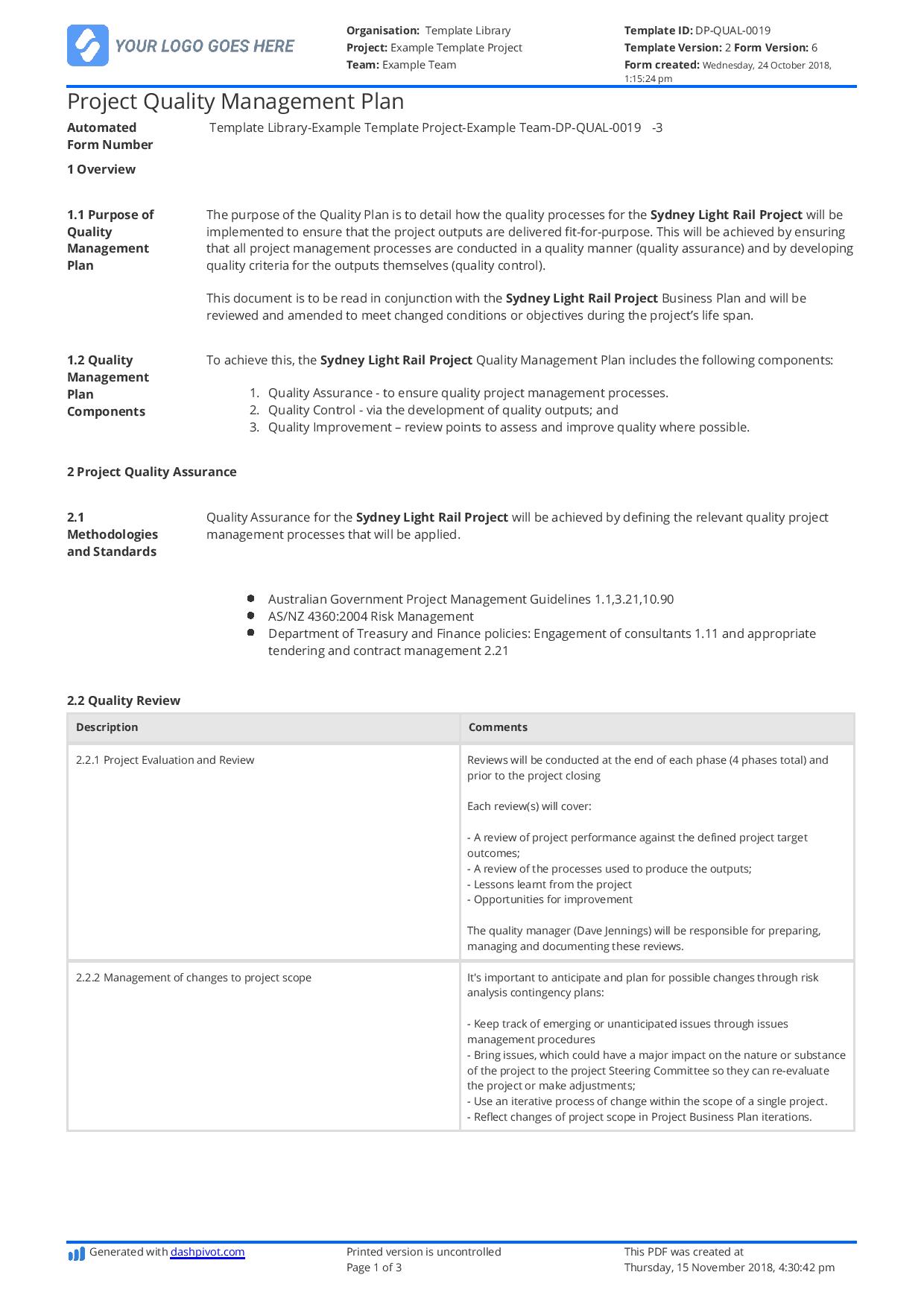
See our free quality control procedure documents and form library.
The road to total quality management
Your quality control procedures and processes form an integral and central part of your overall quality management plan and quality management system. In some part, this quality management system or your quality control procedures will also incorporate the people involved in maintaining quality at your organisation (everyone is involved at some level) and a description of the key activities which you conduct.
How many quality procedures and processes you document will largely be based on the clients and contractors you work with - as well as the nature of work you conduct.
But beyond what is necessary to simply win and conduct work, the practice of creating, maintaining and discussing your quality control procedures is a good one. It forces management and teams to think about ways in which quality could be improved, from day-to-day materials and inspections all the way through to internal and external auditing.
The more integrated your quality control procedures are with the daily execution of work and quality record keeping, the easier you will be able to track performance, understand what's working and make improvements.
Safety management is a constant work in progress - and your quality control procedures should be too.
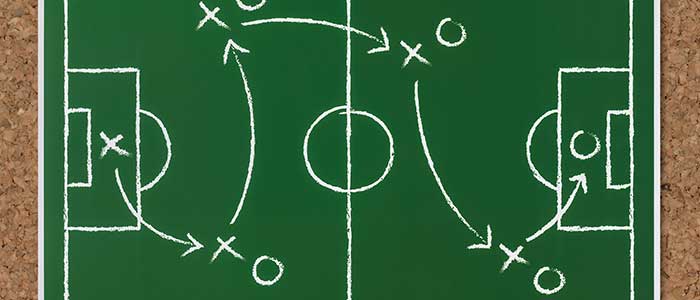
Construction Quality Control Plan template
Complete thorough and professional quality control plans which impress your clients and contractors.
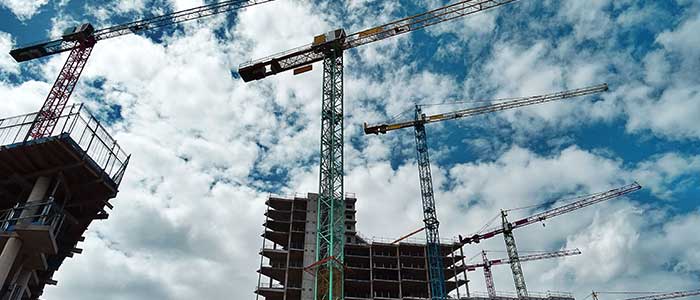
Quality Assurance Plan for Construction
Build and maintain a quality assurance plan like this to build confidence amongst your stakeholders.
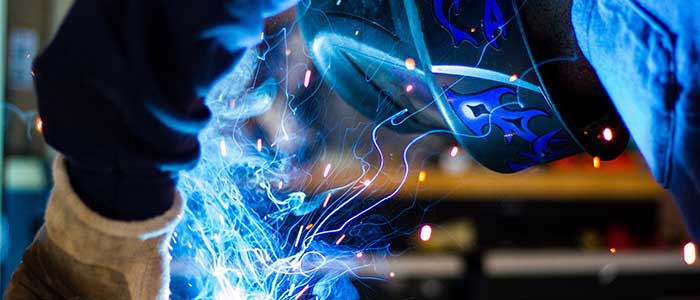
Corrective Action Report (CAR) template
Pre-built with all the fields you need to accurately capture the defect or non-conformance quickly, so that projects can move forward