Quality – Quality control and tracking
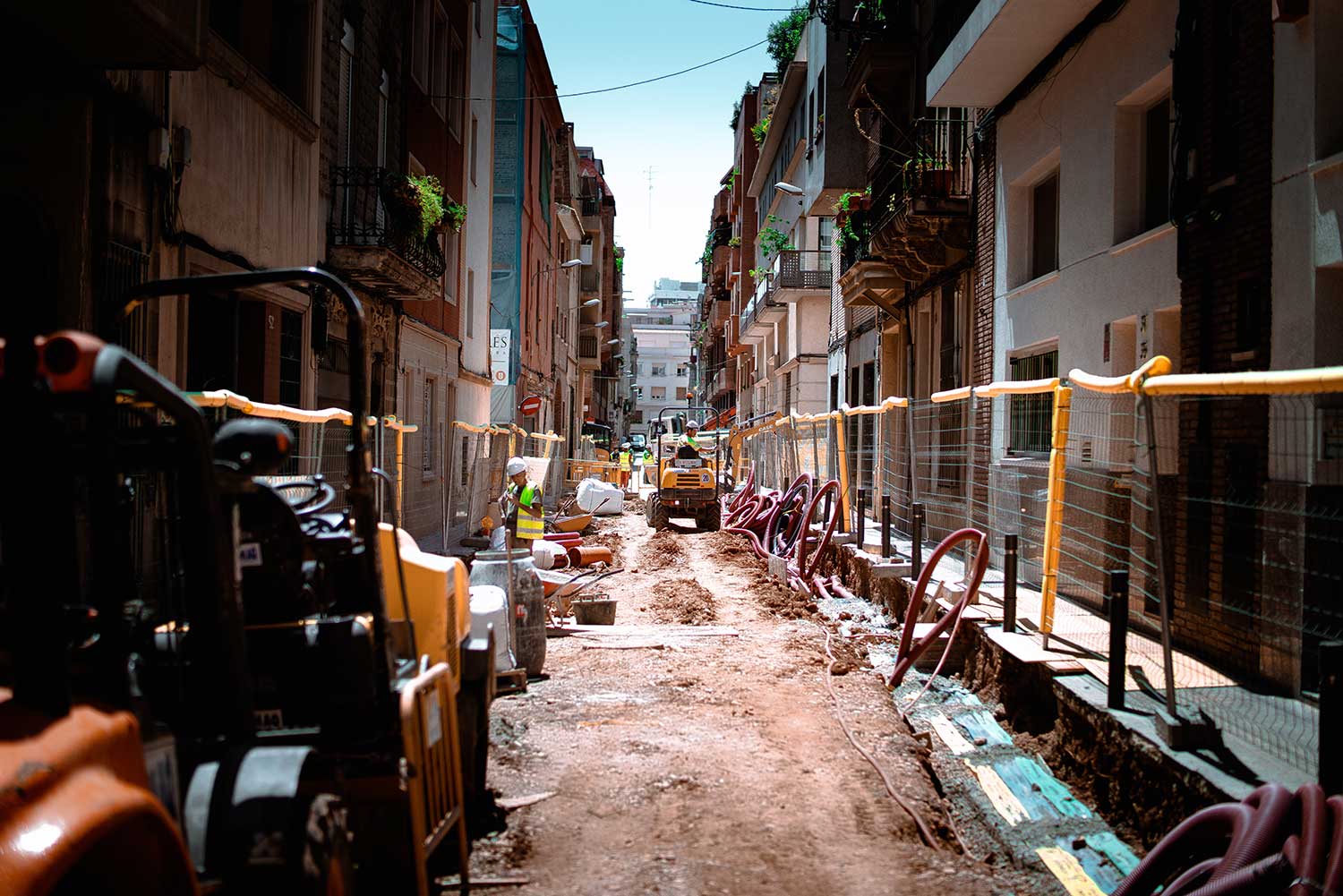
Quality control and tracking - how to get it right
What is quality control?
Construction, mining, oil and gas and other industrial projects are complicated concoctions filled with thousands of moving parts. To bring a project all the way from conception and design to delivery is a monumental achievement which takes many hands and the collaboration and cooperation of many parties.
The complexity and detail required to deliver an asset means that quality control is essential.
At a high level, quality control (commonly abbreviated to QC) is the part of project and quality management which is charged with ensuring that products, services and processes comply with the requirements set out in the contract and project specifications.
So quality control is the control mechanism of quality management. And you can imagine what would happen without quality control. One product outside of spec or one installation mishap can domino across a project and result in a catastrophic failure.
Contractors, subcontractors and suppliers who maintain strong quality control build positive reputations and positive stakeholder relations - and end up winning more work.
This is good for the company of course, but is also good for projects and people, who get better quality assets which improve over time as the quality work continues and those who don't maintain quality are squeezed out to the margins.
Quality control can take the form of a number of activities, checks and balances. One common way of controlling quality is through inspections or the verification of finished products. These methods can be proactive in nature (which is ideal), and help to filter out faulty products before they reach the project site or delivery stage.
While other inspections are more reactionary, and can cause delays and financial headaches throughout the life of the project.
What is quality tracking?
While quality control is based on ensuring the quality of projects and work remain high, it's also important to track quality or implement quality tracking to understand what is happening on your projects over time so that you can make informed decisions about how to improve.
Quality tracking is the act and process of tracking quality over time. That time frame could be a single phase of work, entire project, or over the life of a company. The goal of quality tracking is to measure the standard of your work in order to create more proactive measures and process for quality control.
As an asset owner or client, you want to track the quality of your asset to ensure it will last its intended lifecycle and be 'complete'
As a contractor, you want to ensure you have tight quality tracking so that your workers and subcontractors are maintaining high quality standards - which are a reflection of you to the client.
As a subcontractor, quality tracking ensures that you are delivering good work and finding ways to improve so that you can keep winning work and maintain your reputation as a reliable source of good work.
How to get quality control and tracking right..
Getting quality control right is a constant endeavour. It's one of those things which can never be perfected, because there is always a way to improve quality.
But getting quality tracking right is easier. It's something that can be drastically improved with a few small tweaks to the tools and processes you use to get work done.
Good quality tracking starts with the information and frequency of information being captured on site. While it doesn't help to cripple your teams with hundreds of quality documents and forms, in order to properly track quality, you will need to be capturing what's happening in the field.
There are many quality forms and documents deployed across projects for quality tracking - from simple checklists to more detailed inspection forms.
The type of quality tracking forms you use and the frequency with which those processes are conducted should be setup in your project quality management plan or something similar. Outside of this, your quality team and engineers may do some ad hoc inspecting and reporting.
The example defect report form is a great example of how your team will be tracking defects on a project. Every time a defect is found or noticed, a defect report will be documented which contains information regarding what happened and ideally why it happened. This record then sits in your management system or quality management system and forms part of your big picture quality tracking.
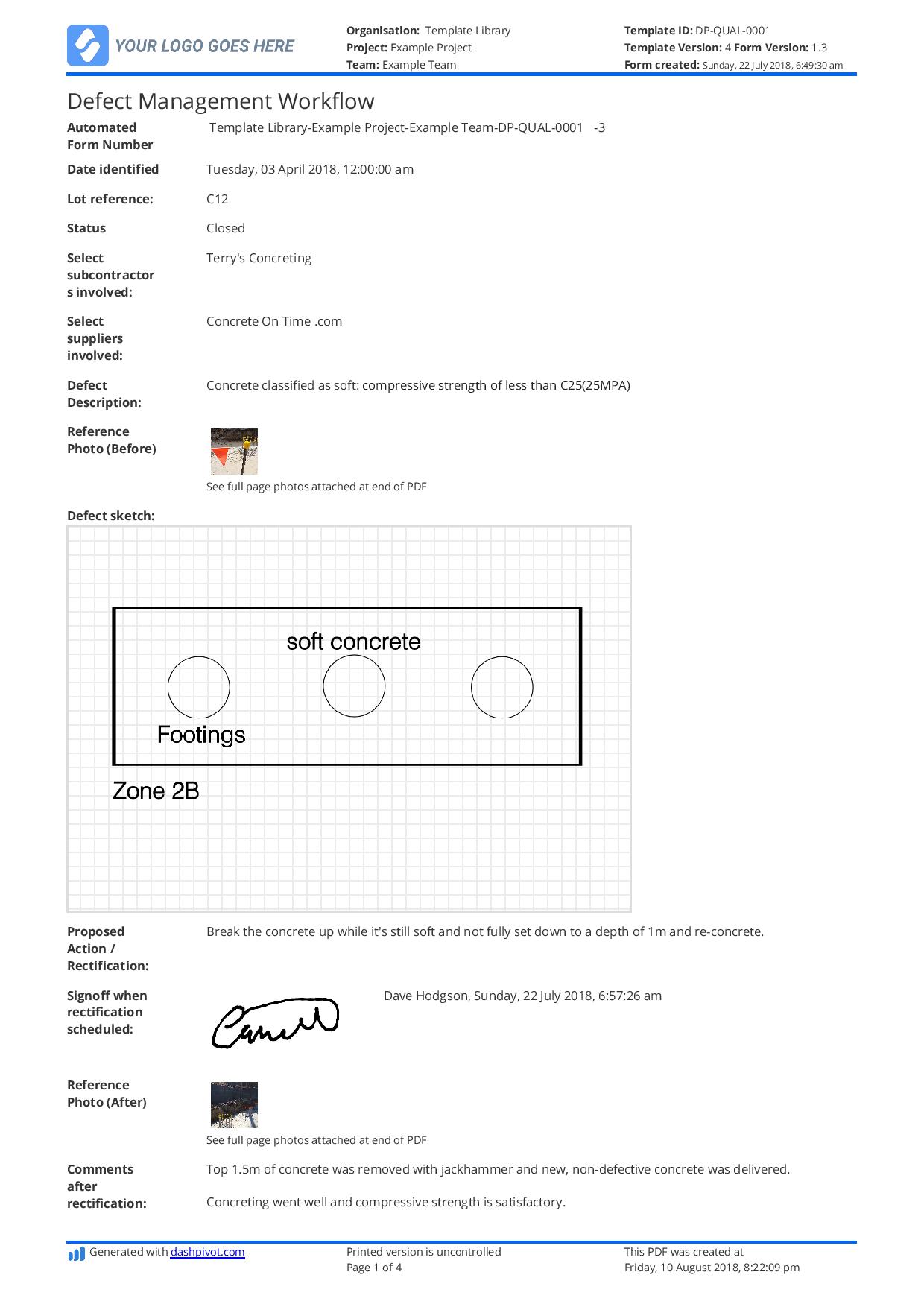
Use this defect report as a part of your quality tracking processes for free.
What do you do with all of the information and data being tracked on site?
Capturing information on site is arguably the most important step in the quality tracking process. But it's the next step which most companies fail to do well - the organising and analysis of this data and information.
Most of the issues around quality tracking stem from how quality is being captured on site. If you are using word docs, PDFs and excel spreadsheets to track and control quality, then your data will be manual, fragmented and difficult to aggregate and understand.
You can eliminate most of this problem by creating standardised templates which then lead to standardised data, which can be combined to form insights. At a minimum, you will want the data you are collecting on site to be digital, so that it can be tracked without spending hours and hours updating spreadsheets and attempting to sort this data.
Alternatively, you can employ the services of a more sophisticated safety management system like Dashpivot.
A good safety management system will automatically aggregate all of the data being captured on site and pipe it through the system to automate quality tracking through real-time analytics.
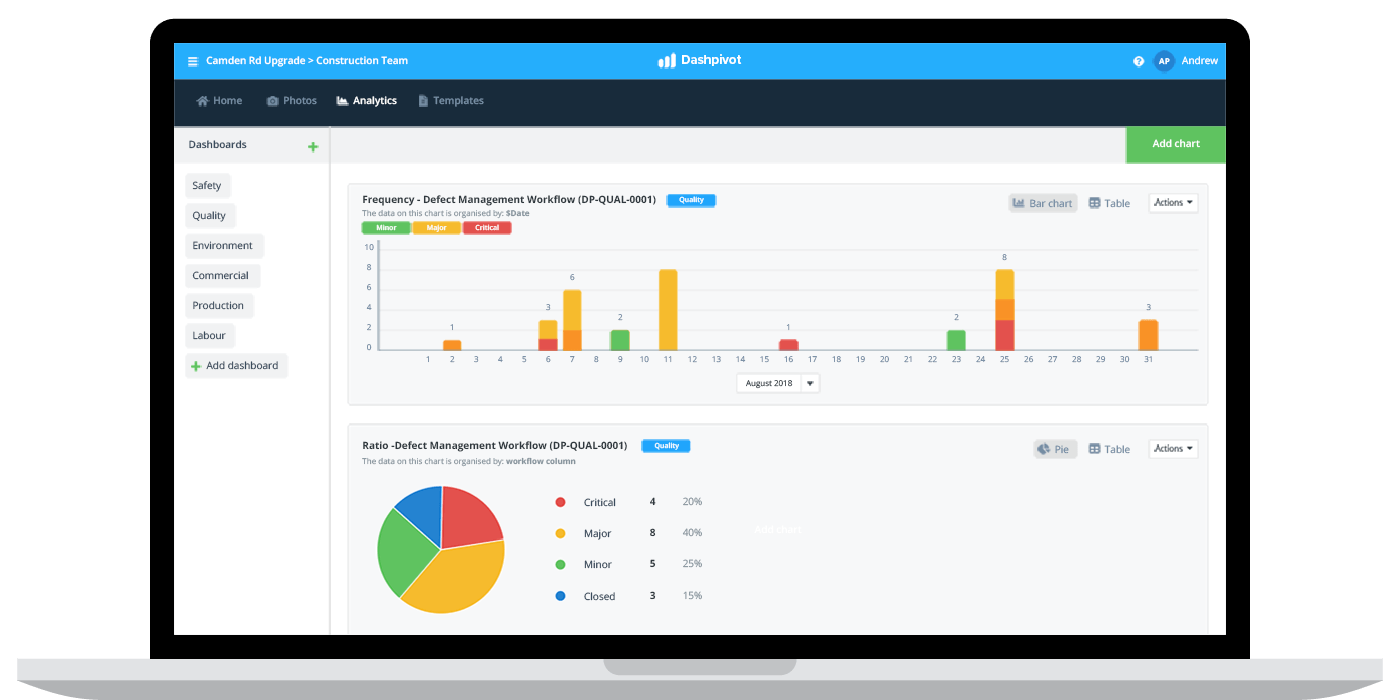
If you do quality tracking this, not only can you automate the tracking and reporting process - but you can get new insights from your data. These systems aggregate all the data collected from defect reports, checklists and other quality forms and organise them into coherent data sets which you can display in timelines, registers and analytics dashboards.
Instead of spending hours and hours sifting through information and attempting to build pivot tables and charts in excel, you can simply toggle with and manipulate your Dashpivot dashboards.
How sophisticated you want your quality tracking to be will dictate what level of tracking you employ.
Good quality tracking starts with:
- Planning out how you will manage and measure quality on your projects.
- The next phase of quality tracking involves how you actually collect data on site through forms, documents and registers.
- And the last phase (and often most ignored phase) is the organisation and analysis of this information.
At Sitemate, we have a bunch of resources and levels of support we can provide you and your quality jobs. You can try the full software suite, or get started with one of our digital quality tracking forms.
We have been able to digitise our HSEQ and commercial processes and engage with our clients and partners on the platform. It has improved the efficiency of our project delivery and allows our engineers to get back to doing what they should be doing.
Brian M.
Chief Operations Officer
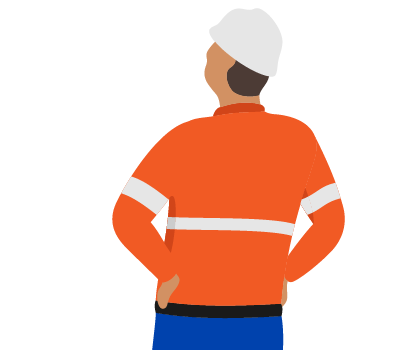