Quality – Quality assurance system example
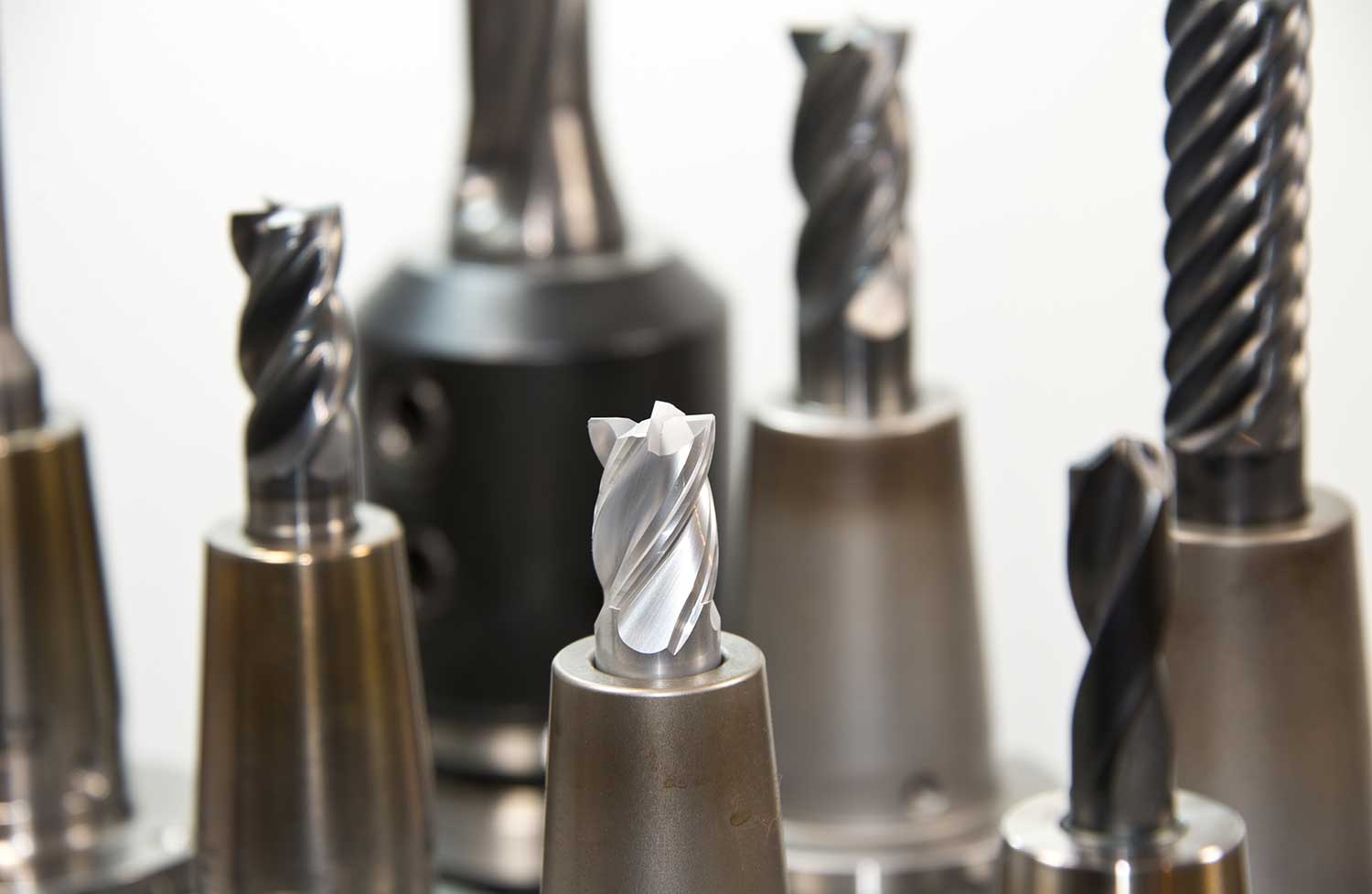
Quality assurance system example: A more useful QA system example
What is a quality assurance system?
Quality assurance systems delve a few meanings deep, starting with quality.
What is quality?
Quality can be simply defined as fit for purpose. As in, what was delivered, whether that was a product, service or something else, does the job it was set out to do.
What is quality assurance?
Quality assurance sits on top of quality in that it is a declaration of quality, made by a specific company or organisation. In other words, they are declaring or 'assuring' end-users or beneficiaries that the deliverable will be fit for purpose.
What is a quality assurance system?
And finally, a quality assurance system is the systematic processes and tools which combine to create a 'system' which can reliably assure quality.
Many companies, especially in industrial verticals, lean on the quality assurance standard ISO 9001 as their quality assurance system. The ISO 9001 being the global business standard which shows commitment to delivering quality products and services to customers.
But while meeting the requirements of ISO 9001 shows your commitment to delivering quality products and services to your customer, it's not actually a quality assurance system which creates processes which result in quality.
Some companies lean on superhero quality assurance teams which save the day when an issue occurs, while others put more effort into creating automated processes which don't require dedicated teams.
Today, we are going to look at what is in my opinion a more useful quality assurance system example; one which companies use to implement their quality control and assurance ideas and plans and one in which they use to deliver higher quality assets more often.
The more important component of your quality assurance system
Quality plans, policies and procedures are incredibly important, as are quality standards like the ISO 9001, because they set the general frameworks and guidelines which companies use to set high level quality controls specific to what they want to achieve.
But where most companies inevitably fall short, and where they lose big sums of money and reputation is in being able to deliver on quality, and delivering on quality comes down to the actual systems and process in place which are able to capture, monitor and track quality so that it can be effectively improved over time.
It's important to plan, and create policies and procedures, but it's more important to be able to implement those plans and policies into tangible processes which are possible to follow on every project or every task.
The better quality assurance system example
With this mantra of implementation in mind, we are going to look at a tangible quality assurance system example in the form of total quality management software.
This quality assurance system example is going to be mostly explained through the eyes of site and project based companies (construction etc.), but it's also heavily applicable - especially towards the end through quality tracking and reporting - for manufacturing and other heavily quality dependent industries.
So we start at the very beginning with the quality assurance system, in the form of those plans and procedures. One component of this is simply completing, collaborating on and then storing your quality documents, and then the next is linking these policies and procedures to the every day forms which govern how work is actually delivered.
A good quality assurance system enables this. You can evolve your policies and procedures into standardised templates which ensure the way people do work, and QC/QA their own tasks is up to scratch.
With a digital quality assurance system, this often takes the form of digital templates, which unlike word and excel and traditional documents, can be accessed directly from the field.
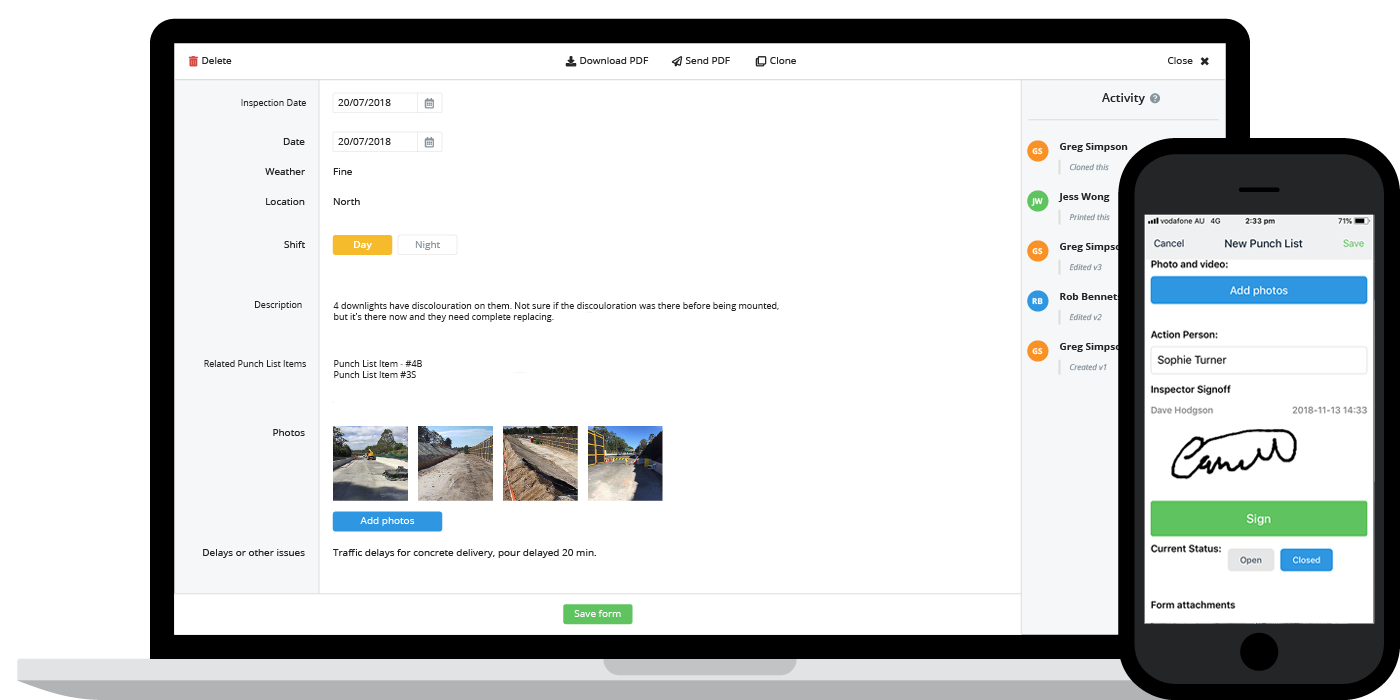
The always accessible quality assurance system
This makes all of your trusted and reliable process templates which you spend time creating and debating accessible to everyone. Workers on site or on the factory floor can open their mobile or tablet and be guided through the processes which dramatically limit the chance of quality mistakes being made or overlooked.
These digital templates and forms solve the capturing quality problem which many companies have a lot of trouble with.
When managing fast moving projects or a number of projects at the same time, it can be almost impossible to get all of that information from the field and reconciled in one place when using word, PDFs and other manual documents.
It's far easier to assure clients and partners of your ability to deliver and showcase quality when you know exactly how it will be captured and illustrated to them.
Quality assurance records
So what happens once work and activity is properly captured?
When you are using a quality assurance system like this example, all of that information is instantly synced to the cloud.
Every quality from, photo or video captured is instantly available and tagged with all of its key information - and it doesn't require 3 or 4 administrators just to manage it.
This serves a number of quality assurance purposes.
Firstly, it ensures that your contractors, customers, subcontractors, suppliers etc. can't wrongly accuse you or your work of being something it's not. When you have all of your proof in a digital format and it's easily findable, people start to quickly have confidence in what you say and deliver in your records.
Secondly, quality record keeping is incredibly important for external audits as well as potential disputes. Having undeniable proof of your work can save you hundreds of thousands of dollars in a single claim.
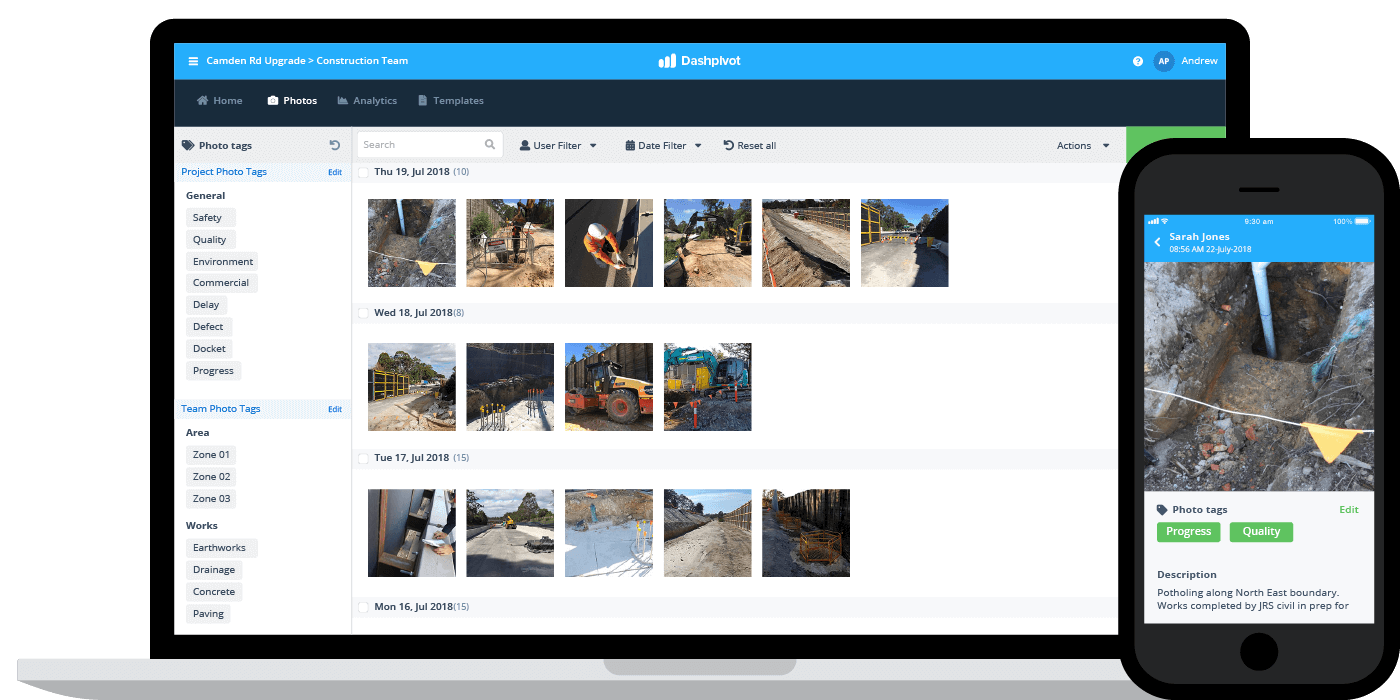
Reporting for quality assurance
Once you have comprehensive records, you need to be able to action those records.
Using this quality assurance system example, you have a few powerful options for getting your quality issues or concerns actioned quickly.
You can export any of your records or information as a quality report, which you can see comes with all of the detail as well as the proof required for other people to quickly action.
This type of comprehensive and detailed reporting improves the quality assurance power of your information as well as your logo. Your reports become the marker and professional stamp of quality.
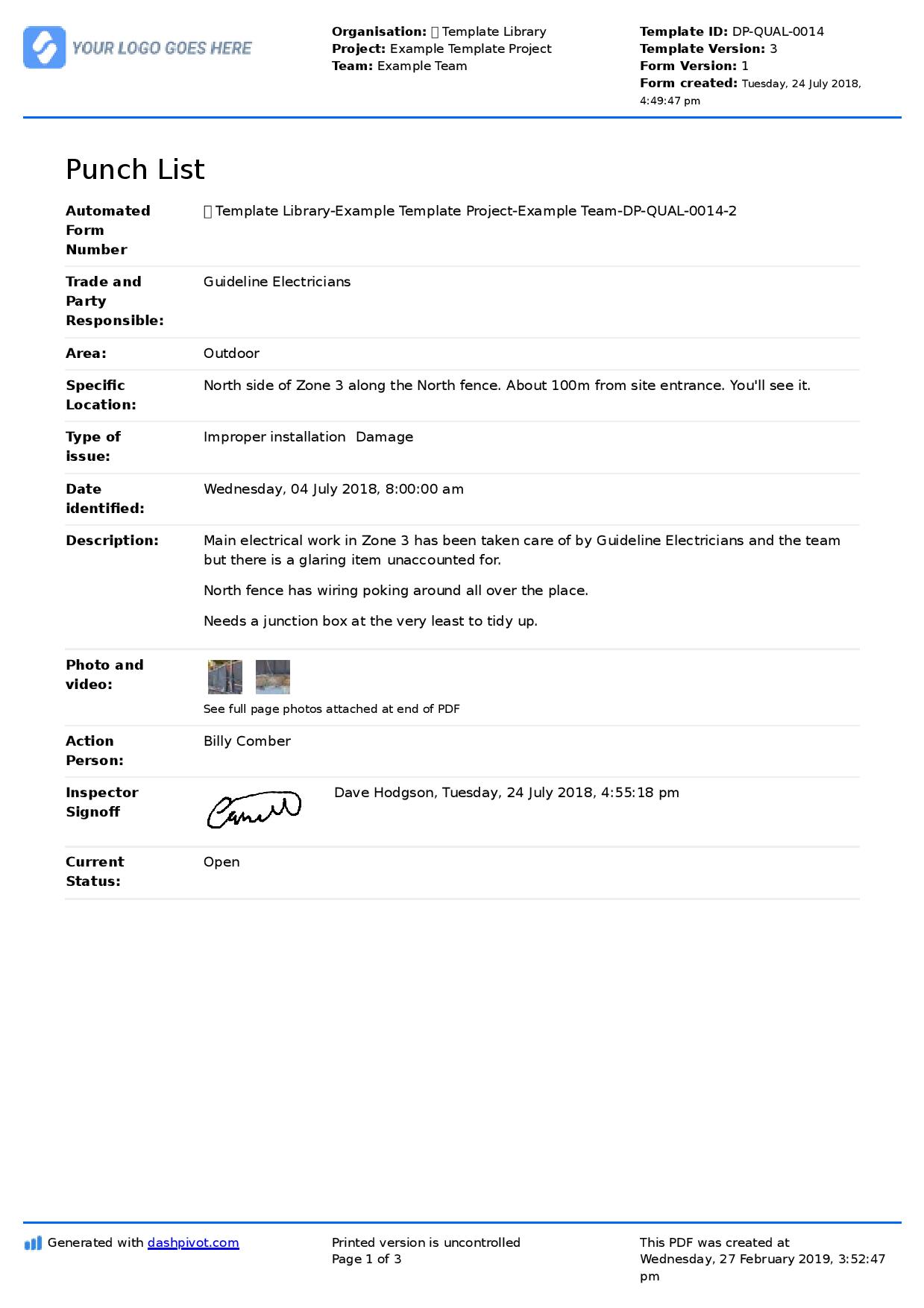
Use this digital punch list for yourself
Workflows
The other thing you can do is to setup automated workflows in a quality assurance system. This is one of the more powerful tools in the system, because quality issues such as defects and non-conformances can move slowly, delay fixes and result in ongoing quality issues.
With automated system workflows the chance of this happening is drastically reduced. When someone created a witness point, hold point or other permit or approval based quality control process, the workflow is initiated.
Responsible parties are instantly notified, workflows can flow between internal and external parties, and quality happens organically by ensuring work touches the right hands and gets the right eyes.
A quality assurance system example workflow for defects is below. When a defect is identified, a person creates the defect report. Once that report is created and signed off, it moves to the rectification in progress column where the actioner is notified that they need to rectify that defect. They can get to it faster, and the defect is closed quicker.
While standalone policies and procedures can illustrate non conformance workflows, think how 'assuring' it is for asset owners and your partners to communicate and collaborate through automated workflows and flowcharts. This is what unbreakable QA/QC looks like.
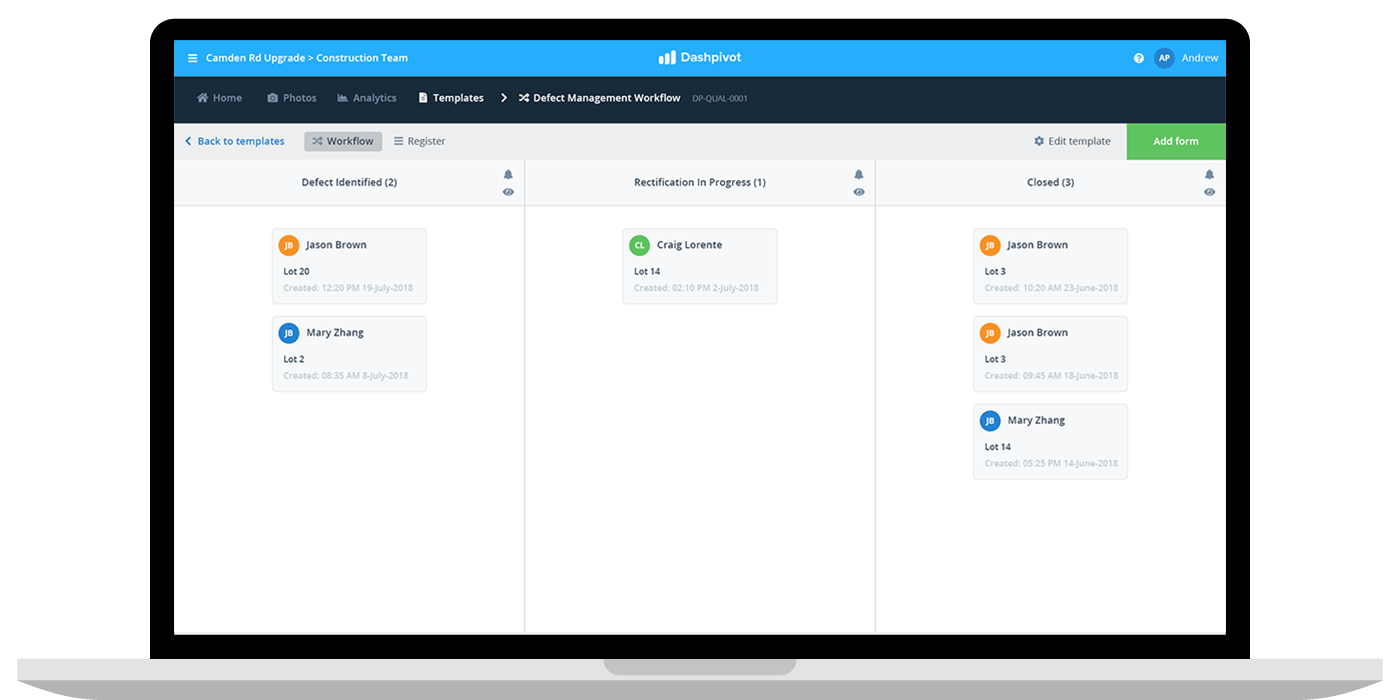
Quality assurance system tracking
And the final major piece of any quality assurance system is that people can understand and analyse quality performance today - so that it can be improved.
Your quality assurance system should be able to display and filter through the data which has been collected in the field to show you insights about things like defects, non-conformances and hold points.
This quality assurance system example can actually aggregate and display all of this information in real-time. So when people are submitting punch lists and defect reports and hold points, the system can display all of this in dashboards and charts which show management what's going on and enable them to see the weakness and strengths in their quality performance.
Being able to see which projects have the most NCR's, or which subcontractors have the most punch list items can be an invaluable asset in being able to improve your own quality control and quality assurance.
Quality assurance in many industries is not a solo affair; it can involve many parties working together, and so project, teams and party performance is a need-to-know in order to remove the drags on quality and resource the high performing areas.
Analytics and tracking brings your quality system full circle, and creates a constant feedback loop whereby you can constantly tinker with inputs and make data based decisions which enable you to deliver more quality more frequently.
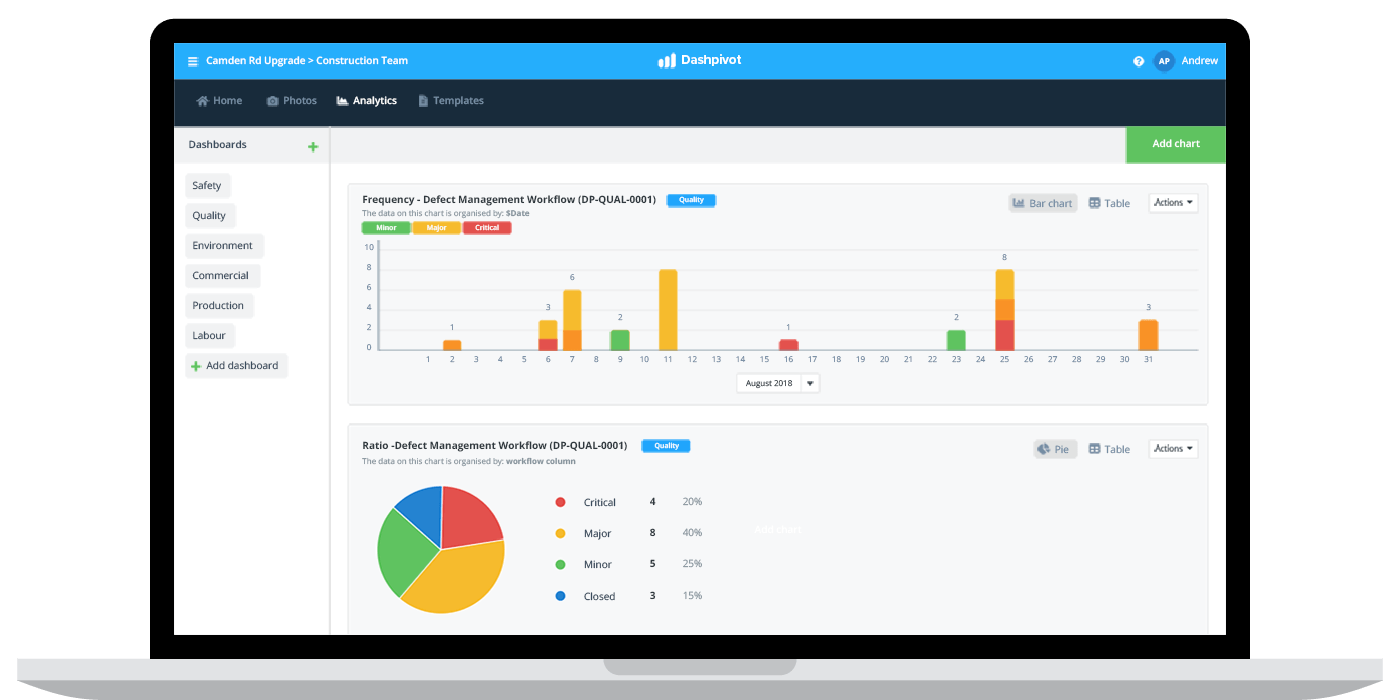
Getting started with a smarter quality assurance system
Getting started with a quality assurance system can seem daunting, but it's actually pretty easy.
If you have your standard quality operating procedures sorted, and your policies and procedures relatively clear, then converting these processes into a digital system is quite easy and quickly reaps benefits.
If you are interested in learning more about this quality assurance system example, you can do that here, or you can look at individual elements of the system below, which enable you to get started with a digital quality assurance and quality control system which does a lot of the hard work for you.
Quality assurance is a hard thing in general, because assuring anyone of quality is difficult when you are managing thousands of moving parts and complex projects or products, which is why you need to lean on quality teams and the quality of your workers - and put the right tools and quality assurance system in their hands.