Plant – How to create a preventative maintenance plan
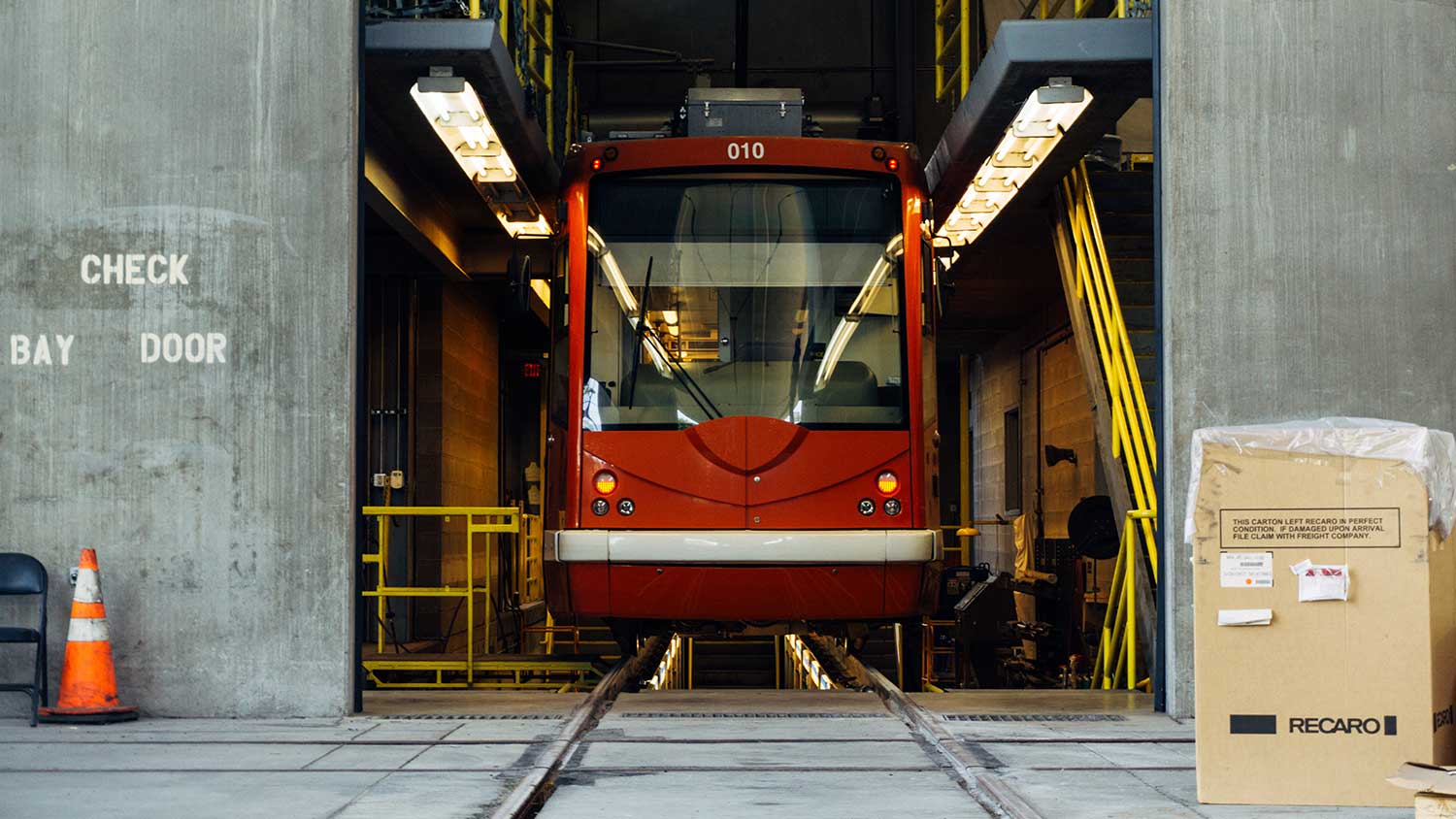
How to create a preventative maintenance plan
Why create a preventative maintenance plan?
Preventative maintenance is defined as the maintenance performed on a piece of plant, equipment or asset (buildings etc.) to lessen the likelihood of it failing.
Unlike regular maintenance, preventative maintenance is the proactive maintenance which companies and workers engage in while the equipment or asset is working - to prevent the need to fix bigger and more expensive issues further down the road.
Today, preventative maintenance is seen as an essential part of normal operations for most companies (as well as individuals).
The 'issue' with preventative maintenance is that it requires an investment of time and resources. The best way to mitigate and minimise this issue is to create a smart and efficient preventative maintenance plan.
Without an actual preventative maintenance plan, 'preventative' maintenance quickly devolves into actual maintenance. Staying ahead of the maintenance curve requires a formal and thought out preventative maintenance plan.
The purpose of this plan is to outline the who, what and when of preventative maintenance so that everyone understands how preventative maintenance will be conducted at the company, on site etc.
How to create a preventative maintenance plan
Creating a preventative maintenance plan involves a number of relatively basic steps. The time spent on each of these steps will vary depending on the size of your projects or company - but the sequence of the steps should remain pretty similar.
The most important part of creating your preventative maintenance plan is keeping it grounded in what will actually be implemented.
There is no point in crafting a detailed and comprehensive maintenance plan which you can not physically resource or adhere to.
Your plan should align with the resources you have at your disposal, and the ROI which is made possible by improved preventative maintenance.
The tools you use to manage your processes (like this equipment management software) can also enable you to streamline your preventative maintenance processes so that they are more efficient and easier to conduct. So the tools at your disposal and the tools you will use to conduct the actual activities should also shape your initial plan.
So with these things in mind, let's dive into how to create a preventative maintenance plan.
1. Establish a plan
The time spent establishing a plan will depend on the number of people who need to be involved in the process - which is usually directly tied to the size of the business.
The first step of creating your plan is to create a plan for the plan, which will include detail around:
Who will be involved in the planning - Creating a plan in a vacuum usually doesn't work out very well. Early in the planning stages, you will want to include as many key stakeholders as possible in the actual planning phases - as well as identify key spearheads for implementation.
The more people you can get onboard early in the planning process, the better your plan will be and the more 'bought in' teams and workers will be too.
How to implement the plan - Early in the planning process, you'll want to know what resources and tools you will have at your disposal for implementation.
Will supervisors oversee the preventative maintenance, how will maintenance will be documented etc. etc.
What are the goals and KPIs of this plan - The purpose of a plan is to improve the outcome of the planned activities. The only way you can know whether or not your plan was successful (and how it could be more successful) is to identify what will be measured during the course of the plan and the overall goals of the plan.
That way when you create your next plan or iterate on the current one, you will be able to incrementally improve again.
2. Reference or build a database of your current plant, assets and equipment
One of the most important and sometimes overlooked aspects of creating a good preventative maintenance plan is to take stock of your current plant, equipment and assets - or to check your 'inventory'.
You will need to create, identify or update a database of all of the equipment which needs to be inspected and maintained as part of your preventative maintenance plan.
Some key data points to collect or ensure you have are:
- The equipment name, model and reference number
- The current hours, KM's or work done
- The current location of the plant, equipment or asset
- The last inspection or maintenance check
- The next scheduled maintenance check
- The responsible operator (where applicable
Obviously you can also include more detail where required, and the more detail you have, the easier it is to quickly identify and action the equipment.
Setting up or collating this database is a key step in the planning process, but this database obviously needs to stay up-to-date throughout the course of the plan - and ideally forever.
Some companies use excel spreadsheets for this database, while others take advantage of a smart database like you see below.
Either way, this database will be the reference point for any required maintenance down the track - and will be updated with the most recent maintenance inspections and other equipment information.
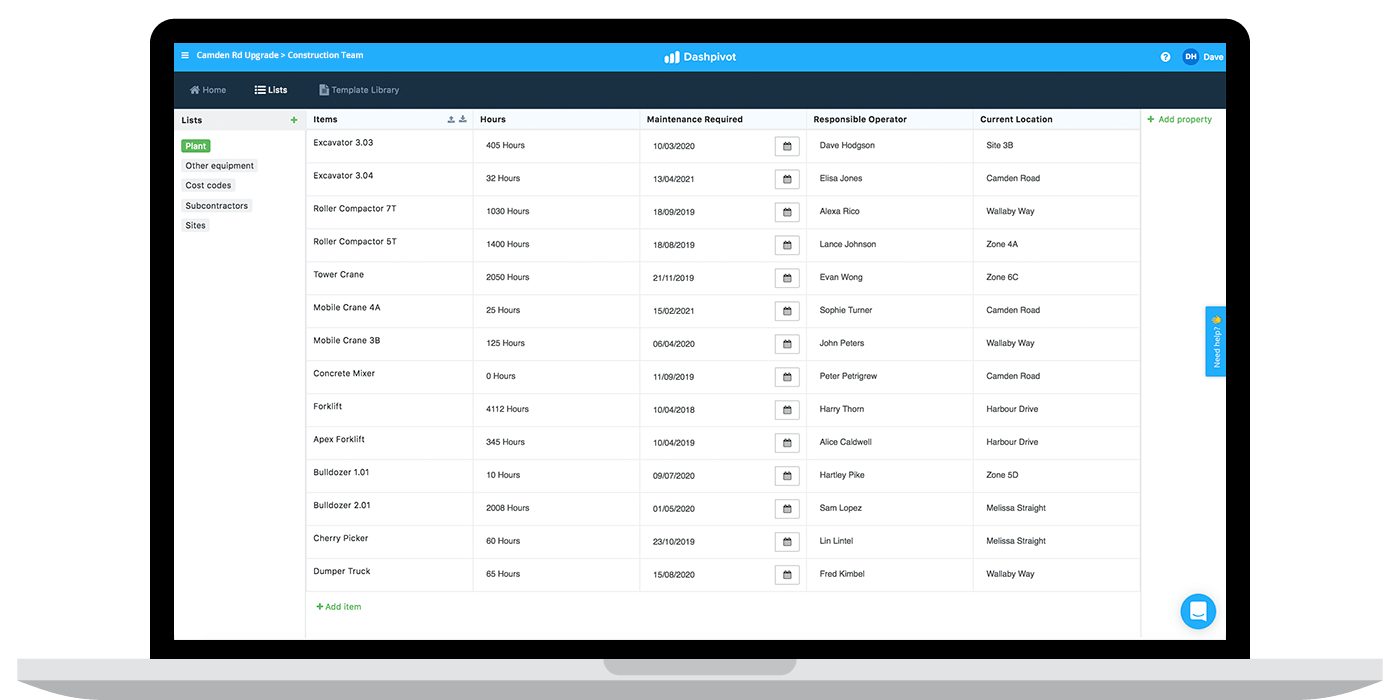
3. Create a cadence for your preventative maintenance tasks and activities
The real key to good preventative maintenance is to conduct it at regular established intervals.
Creating this cadence usually involves a few simple steps.
1. Look at the manufacturers manuals to factor in their suggested inspection and maintenance frequencies
2. Look at historical data and get the opinions of operators and subject experts to understand what has worked well in the past
3. Take a look and update your previous preventative maintenance schedule (where applicable).
Combining what you know and have learned with your new plan and new best practices is the best way to create a good plan.
4. Outline and implement the actual procedures, processes and documentation behind the preventative maintenance
Once you have (1) an agreed to schedule around how often equipment will be inspected and maintained, and you have a (2) database which you can use to reference and notify people when an inspection is required, you can start to create the processes and procedures around what the preventative maintenance practices will look like.
For most companies, this involves creating a series of preventative maintenance checklists and templates which workers can easily access and complete.
These checklists and documents ensure that workers follow the right steps when performing the actual inspections and maintenance which was identified in the plan.
When everyone has access to standardised and reliable templates, all of the procedures and information being collected on site is correct - so it's easy to update the database properly - and to build bulletproof records like the example you see below.
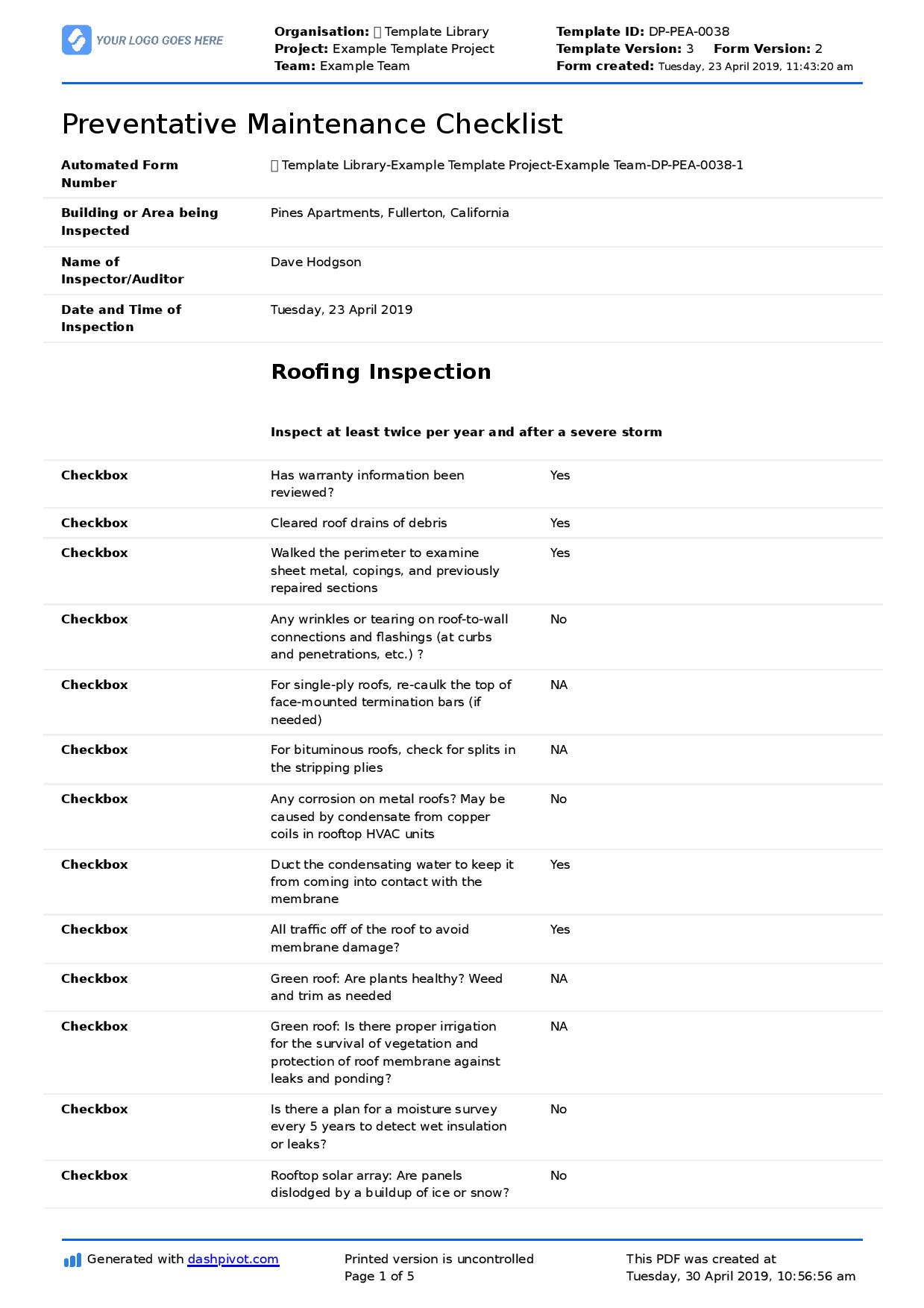
Use and edit this preventative maintenance framework for free.
5. Ensure maintenance technicians and workers understand their roles and are trained in what to do
One of the biggest problems companies have when they spend their time creating a preventative maintenance plan is that the workers on site don't 'do their job' properly.
The 'blame' for this sometimes does fall with the workers, but it can also be traced to the early planning and expectations set by the company as well.
There are two main elements of setting expectations and giving workers the powers they need to fulfil their part of the bargain:
1. Involving workers in the planning process, asking them questions about the current process, and making it clear in the form of verbal and written communications what is expected from them. Poor communication here can leave workers thinking they are doing the right thing - but doing the wrong thing.
2. Training workers in how to conduct the preventative maintenance inspections and maintenance, including the process and tools behind capturing the information - whether that is an app like below or a simple PDF sheet.
Outside of this, workers also need to know what to do when a maintenance inspection surfaces an issue. Do they contact their supervisor to issue a maintenance request or get someone in to perform a field service report - or do they simple submit their form and let other members of the team deal with it. These are the nitty gritty parts of the process which need to be ironed out and understood.
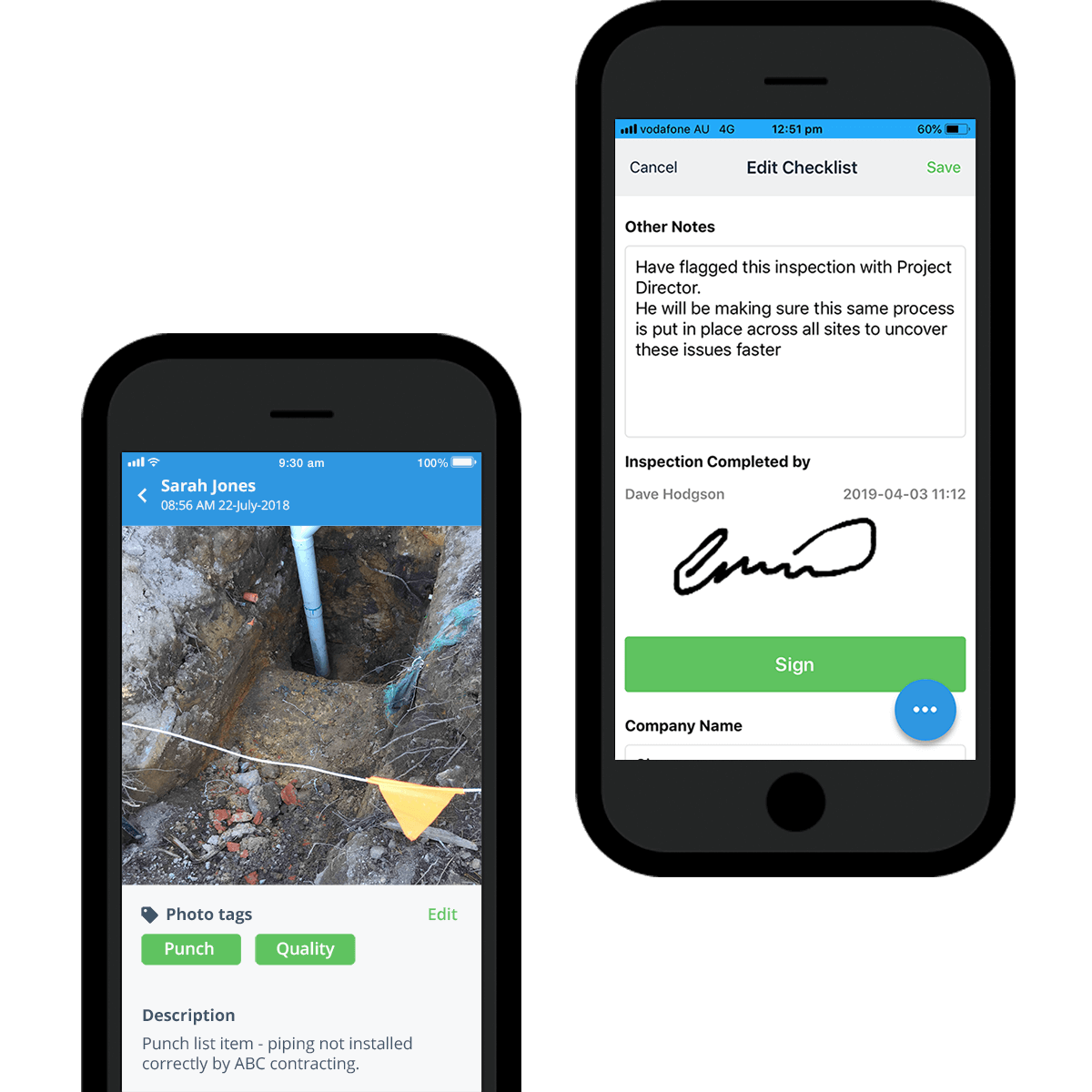
6. Start tracking and measuring the quality and outcomes of your preventative maintenance plan
When you create a preventative maintenance plan, you set your goals and performance metrics, as we described earlier.
During the planning stages, you need to identify how you will track and measure these outcomes, with a couple of the most common options being:
Spreadsheets - Manually updating a spreadsheet with the information captured in the field to derive your own insights.
Dedicated softwares and dashboards - If you use technology to capture information in the field, then this data can be fed straight into automated dashboards like you see below, which can give you real-time insights around the number of maintenance inspections performed, the outcome of those inspections, the ratio of specific outcomes and more.
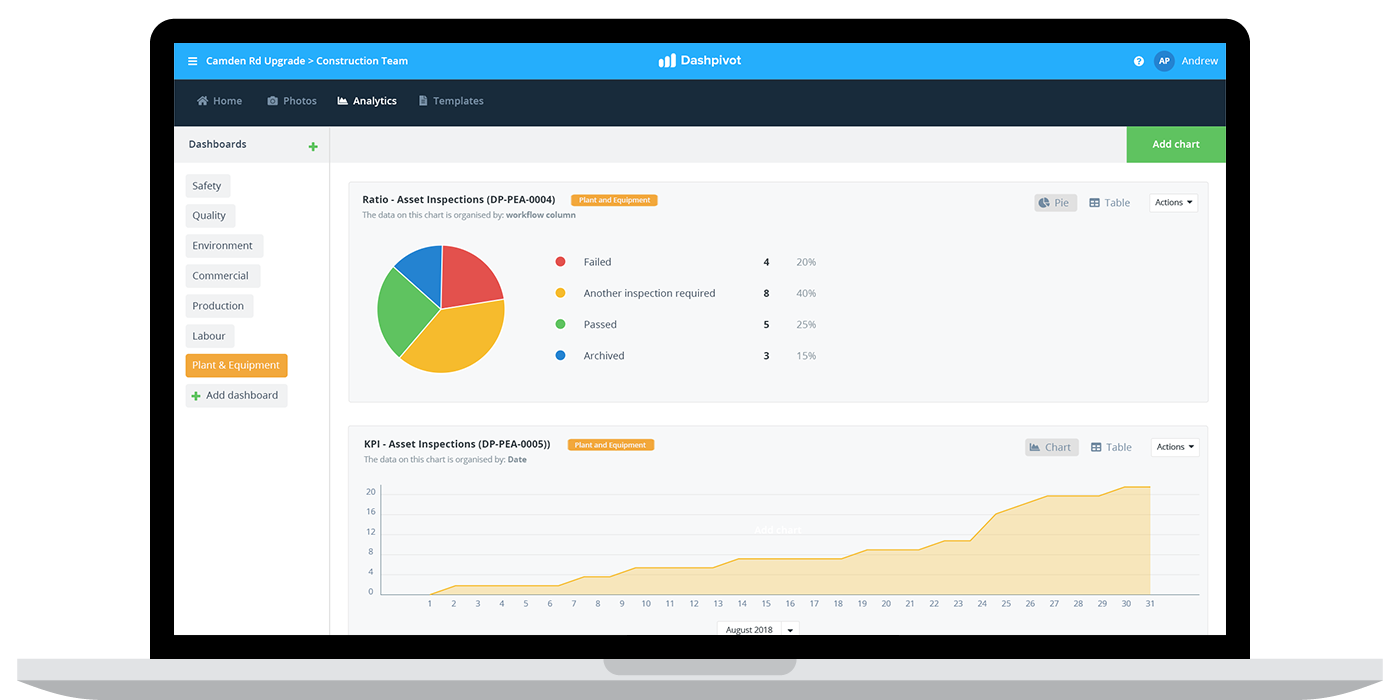
Creating a preventative maintenance plan doesn't need to be that hard...
Obviously there are many benefits to using a dedicated project dashboard and even more benefits when you bundle this dashboard with the inspection app and smart database you saw above.
This then becomes your single source of preventative maintenance truth, and does most of the heavy lifting and admin for you.
Creating a preventative maintenance plan is always 'hard', because it involves some careful thought, pulling multiple stakeholders together, pulling critical data together, and taking stock of your current performance.
But today, creating a preventative maintenance plan is much easier than it was before.
Companies can lean and rely on smarter databases, and hand over much of the implementation to softwares and tools which create processes and procedures which require very little oversight and automate many of the issues companies experienced in the past.
There are multiple ways to create a preventative maintenance plan, and it's critical that you get it right.
Good preventative maintenance can save you large sums of money and help you avoid catastrophic failures and mistakes.
People in 80+ countries use this software to improve their preventative maintenance plans and processes.
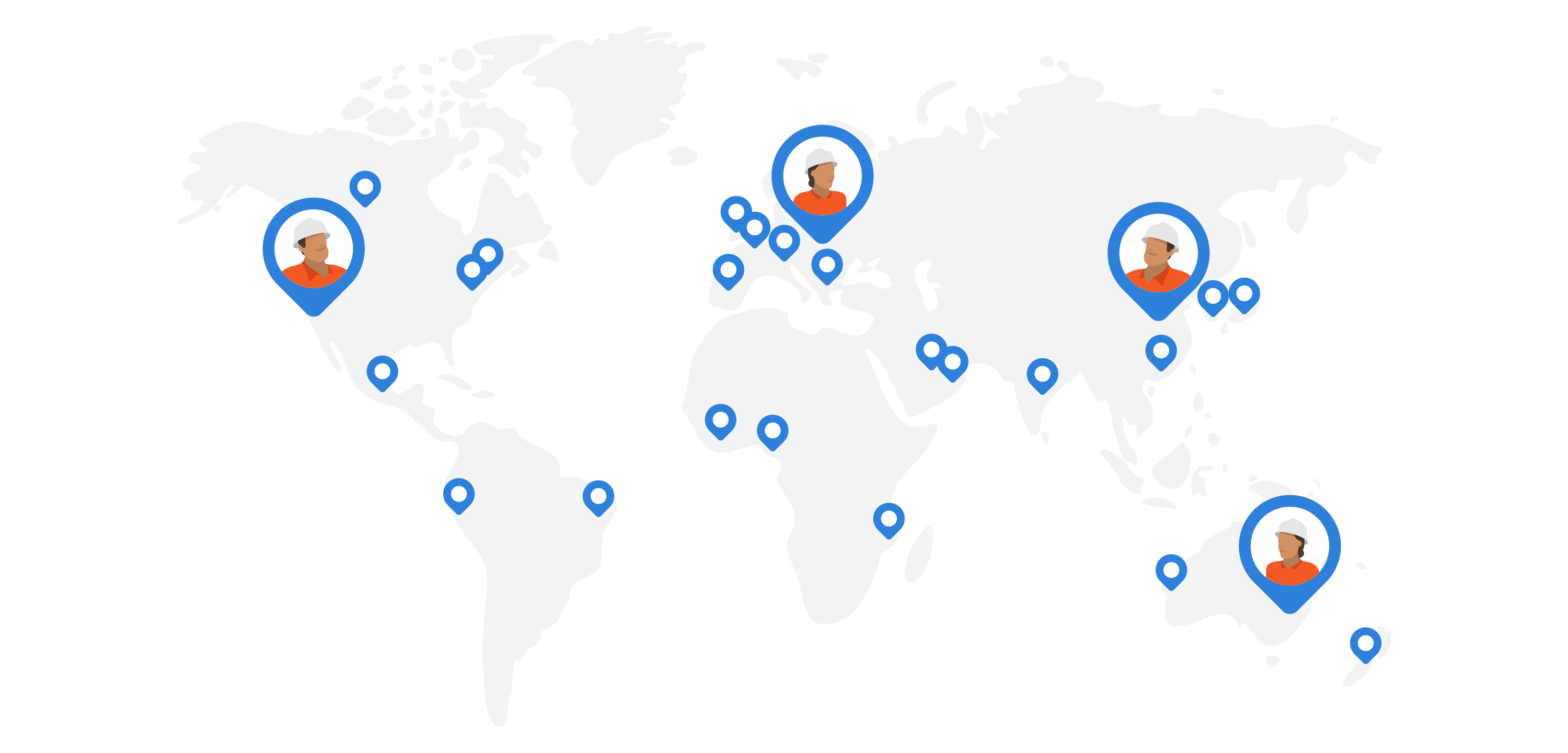