Article Page – What is Commissioning of Equipment?
What is Commissioning of Equipment?
The proper commissioning of equipment is a critical part of ensuring the performance of a building’s operational systems. Here we tackle what this term means and how free digital tools and resources can help you can apply the industry’s best practices.
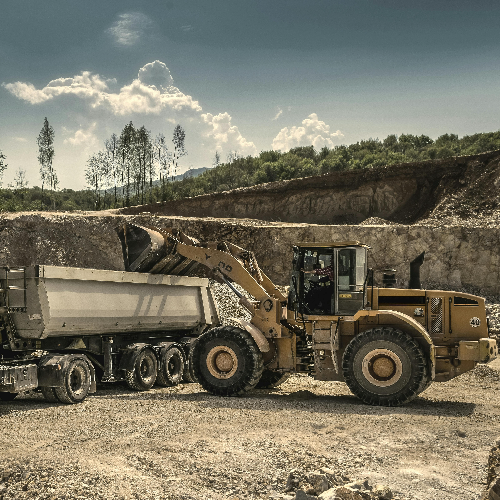
Table of Contents
Article Summary
- This article discusses the meaning and purpose of Equipment Commissioning, in the context of installation and testing of a building’s operational systems.
- Commissioning of Equipment refers to the process of testing mechanical and electrical related equipment to assure performance before it is put into use.
- Proper Commissioning practices help identify equipment issues early, ensure quality performance and compliance, & facilitate good turn-over of equipment.
Why Should Your Equipment be Commissioned?
Your equipment should be commissioned as soon as soon as possible after installation to ensure that it has been properly installed and performs as intended. This is an important step in the turn-over of the equipment from your supplier to you, as it also acts as a safeguard from any unseen factory defects or deficiencies that may affect relevant warranties and future operations.
Several local and national building codes, such as the International Energy Conservation Code (IECC) in the United States, require formal commissioning for equipment intended for energy systems in commercial buildings.
This step isn’t as simple as flipping a switch to see if your equipment runs or not - in fact, meticulous attention to detail is required to ensure adherence to your local building codes and standards. Skipping or rushing commissioning may lead to operational delays and safety concerns that will expose you to unnecessary risk, especially when you are dealing with critical equipment and essential systems.
Further, proper equipment commissioning during the construction phase of a building’s life also benefits future Operations & Maintenance (O&M) works during future regular occupancy. Since commissioning is usually done with your equipment supplier’s representatives and technicians present, this can be an important opportunity for your maintenance team to learn about the equipment they will be handling.
What Format Should Equipment Commissioning Follow?
Proper testing and commissioning of all equipment should also be properly documented for easy tracking and transparency. In order to do this, you must list all necessary information regarding the equipment unit and the commissioning process itself.
The commissioning process differs depending on various factors, such as the equipment itself, the system it will be installed in, the load or capacity it is expected to carry on the regular, any equipment-specific calibration methodology, and other external factors that you will have to consider. You can review the example below to give you a better idea on what a comprehensive commissioning document format.
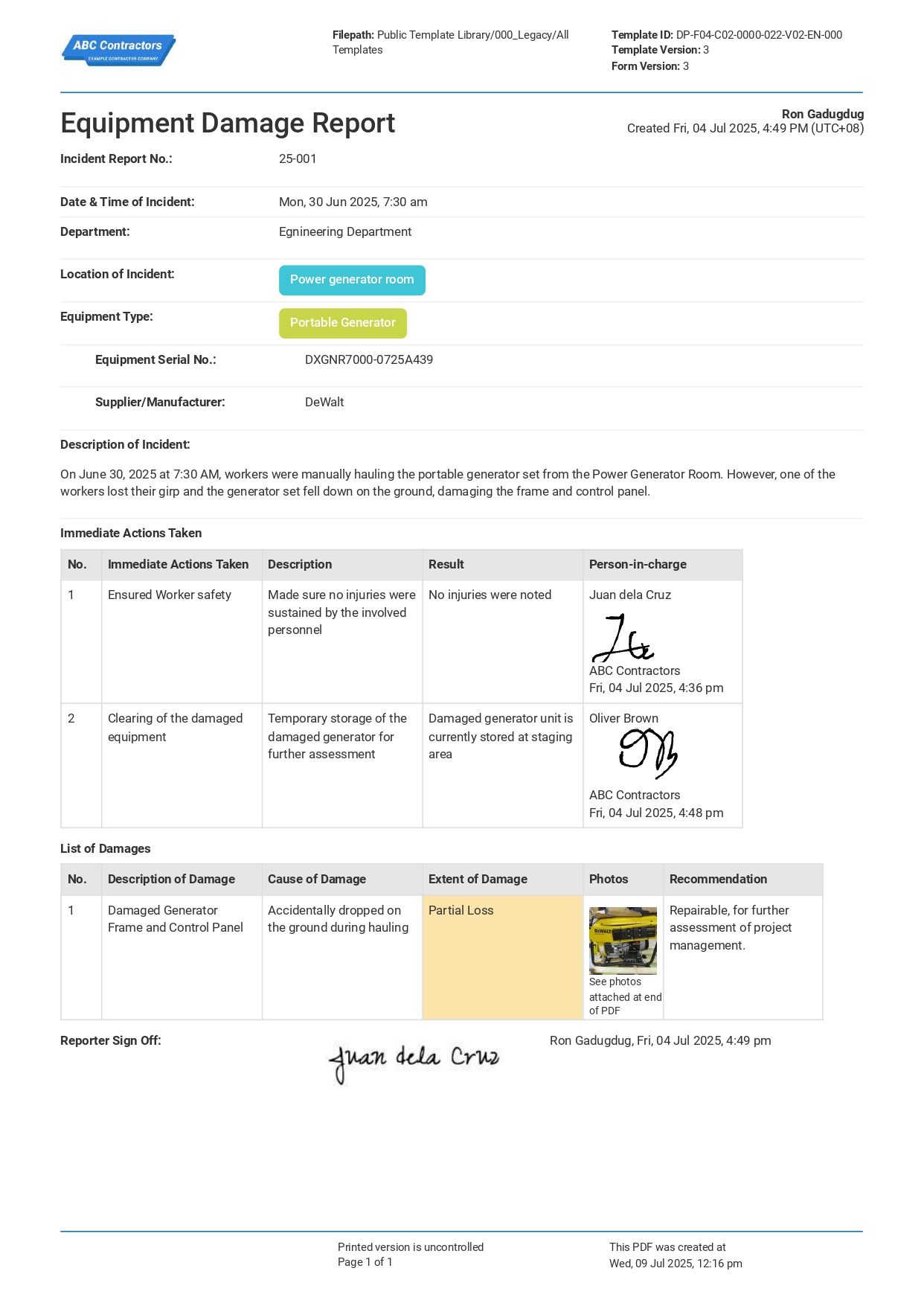
Use this Equipment Damage Report for free
What is Equipment Commissioning: Meaning Explained
The Commissioning of Equipment is a systematic process of testing and calibrating a piece of equipment to ensure that it performs as per design specifications before it is put into regular use. This is most usually performed after your equipment is physically installed and before normal operations begin.
The term “commissioning” is used in this context since the process covers installation & integration of your equipment to your system, inspections, and performance checks and validation. Once all system checks have been done and your equipment has shown to be capable of carrying the designed workload, it will be deemed “commissioned” and final turn-over of the equipment can begin.
OSHA does not explicity require a standardized commissioning process or format. However, several of their regulations imply and adhere to the best commissioning practices.
Historically, in the context of construction and engineering, the term “commissioning” meant the testing and balancing of a building’s Heating, Ventilation, & Air Conditioning (HVAC) systems in accordance to the pre-determined design and specifications. Over time, this term’s scope extended to cover the testing of other building systems that are compromised of various mechanical and electrical equipment, including Power & Electricty, Fire Detection and Alarm Systems (FDAS), Telecommunication Systems, Water Treatment Systems, Gas Supply Systems, Elevator & Escalator Systems, etc.
Notably, commissioning can also be performed after completion of the building & its systems or during normal operations. Some companies perform “retro-commissioning” to existing buildings, which often solves system issues that appear during the building’s life.
Purpose of Commissioning: Going into Detail
Proper Equipment Commissioning practices can only be implemented if the purpose of such practices is understood. Below, discuss the details and explain why commissioning of equipment is critical:
Early Detection of Possible Equipment Issues
Testing and Commissioning your equipment as soon as possible after installation is very important as it allows your team to catch any issues such as defects or damages that may negatively affect your system and operations. Regardless if the issue is due to inherent factory defects on the equipment or possible damages due to the transport and installation of your equipment, you will be able to resolve these issues before going into normal operations.
Verification of Performance vs. Design Specs
One of the most important processes in Commissioning your equipment is the actual testing of said equipment to verify whether they perform as per plan. Depending on the type of equipment, this may include tests such as no-load tests and full-load tests. It is during these tests that your team, ideally together with your supplier’s technicians, can adjust and calibrate your equipment for proper integration into your system.
Compliance of Standards & Regulations
Depending on the type of system you are running, there may be local and/or national building codes that you will have to comply with when installing your equipment. For example, in the United States, there are NFPA regulations that one must comply with when installing new electrical and power systems (NFPA 70E, Electrical Safety in the Workplace). Being aware and complying with these regulations will be critical to ensure workplace and equipment safety, and will keep you on the good side of warranty and insurance issues if they arise.
Facilitate Maintenance Personnel Training & Turn-over
Regular preventive equipment maintenance during normal operations is one of the most critical aspects of property management. The testing and commissioning of your equipment is the ideal time for your Operations & Maintenance (O&M) team to “get to know” the machinery they will be handling, as they will be guided by experts from your supplier.
“Digital” Commissioning of Equipment
With the continous advancement of technology, new Equipment Commissioning processes have begun to arise. One example of this is the use of sensors and IoT devices to allow access to live data during the commissioning process. This gives engineers and technicians the option to perform real-time diagnostics, calibration and testing of these equipment even when they are not on site.
Simplifying the Equipment Commissioning Process
You can expect that the commissioning of critical equipment will entail long, arduous sessions with your team and other relevant parties. Manually tracking these sessions, while important for transparency and record-keeping, will definitely get messy if your team isn’t adequately prepared to deal with the mountains of paper that will eventually form.
Fortunately, with the Inspection and Test Record App, you will be able to create, record and store all the necessary documentation you will need during the Equipment Commissioning phase of your project. Easily coordinate with your team and other third-party representatives to log attendance, take down notes, record results, and sign-off on documents - all in one place.
One other more closely-related digital solution is this Plant & Equipment Inspection App to gain insights and improve operations.
Summary of Commissioning of Equipment
Commissioning of Equipment is an essential process composed of calibrating and testing all mechanical and electronic related equipment to ensure they perform as intended. It allows you to identify and address equipment issues early, test and calibrate the equipment for proper system integration, ensures you comply to the relevant regulations, and acts as equipment training for your O&M team. As this is a formal and highly technical process, you will need to document any and all tests done during this time.
Frequently Asked Questions
Are there any regulations to comply with during the Commissioning of Equipment?
Yes, there are some regional regulatory bodies that enforce certain practices during equipment commissioning, particularly when dealing with potentially hazardous operational systems, such as Power & Electricity systems, or systems that deal with chemicals.
What part does technology play to better existing Equipment Commissioning practices?
Emerging technology now allows engineers & technicians the option to move toward a digital, paper-less system to document and track the commissioning of equipment from start to finish.
Does Sitemate offer templates for Commissioning of Equipment?
Yes - Sitemate offers a wide array of templates that will help you document your commissioning process. From Pre-start Safety Checklists to Equipment Damage Reports, several companies are using our templates to streamline their digital logs.
Related resources
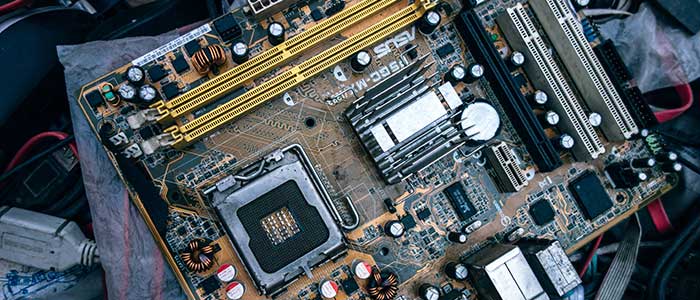
Equipment Inspection Checklist
Conduct and complete equipment inspections directly on site with a convenient digital checklist.

Pre Start Checklist for Machinery
Ensure pre-operations and pre-starts are fully checked for site and industrial equipment.
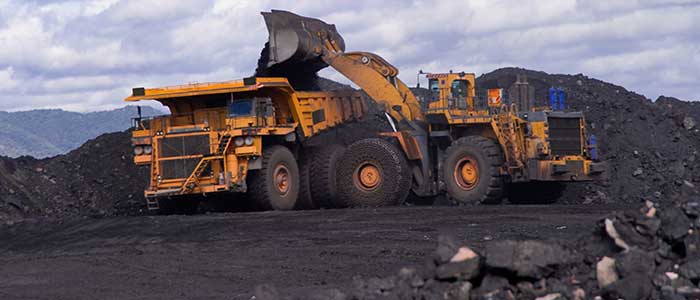
Heavy Equipment Inspection Checklist
Use a convenient checklist for heavy equipment prior and post using in heavy operations.