Dashpivot Article β Conveyor Safety Standards
Conveyor Safety Standards
In this help article, we cover the most important conveyor safety standards inline with safety regulations governed by OSHA etc., as well as how to maintain these standards in your workplace.
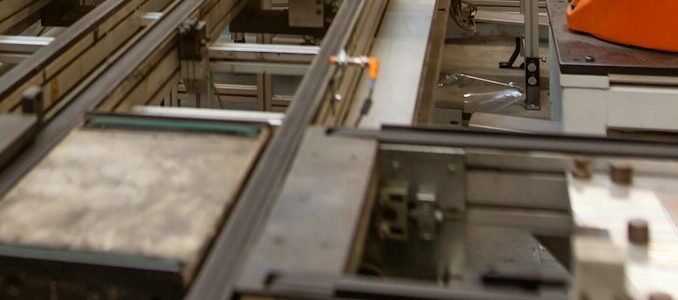
What is the Purpose of Conveyor Safety Standards?
A conveyor system is a mechanical system that is utilised for transporting loads. Typically, conveyor systems consist of a belt stretched between 2 or more pulleys. The belt is built to form a close loop around the pulleys so it can rotate continuously. These remarkable systems were the solution to objects that were too bulky and heavy for humans to carry repeatedly. These systems were key contributors to revolutionising the industry to be more efficient and prompt. However, no matter how helpful these systems may be, they carry many hazards with them, which is why there are detailed conveyor safety standards and regulations which all companies need to adhere to.
According to the US Bureau of Labour Statistics, 9000 Americans get injured and 40 die because of conveyor belt accidents yearly. It is vital that organisations must identify these hazards so that they could provide safety measures to keep employees and company assets free from danger.
Common Conveyor Hazards
Workers must be vigilant around conveyor systems. There are a number of hazards that lie around the machine. These hazards need to be identified so that organisations can place safety controls to have a safer working area. Here are some common hazards that are found in conveyor systems and tips on how to avoid them.
Entanglement
Entanglement by hair, clothing, accessory, or body parts are the most common accidents with conveyor systems. These risks could lead to major physical injuries (i.e. amputation and bone fractures) and fatalities.
Pinch Zones and Nip Points
Pinch zones and nip points are areas on a machine where moving parts meet and has a potential to cause injury. It is crucially vital that operators should know what nip points are and where to find them so that the right safety measures will be carried out.
You can see more examples of pinch points in the workplace here.
Overhead Hazards
Falling objects and overhead hazards are often overlooked. They are commonly present in industries that use roller conveyors. Conveyors may sometimes carry objects that are awkward, which can present a risk of falling. When these hazards are left unaddressed, they can cause serious damage to employees and properties.
Jamming
Jamming can cause sudden belt movements, which can hit nearby employees and injure them. Jammed objects might also get thrown off from the machine, causing potential harm to nearby workers and damage to properties.
Electrical hazards
Conveyor systems are mostly powered by motors, controls and sensors. Damage to these electrical components poses a hazard to the workers surrounding the area. Also, improper isolation during maintenance can pose a risk of electrical hazards in conveyor systems.
Hazard Awareness Inline with Conveyor Safety Standards
The examples mentioned above are only a few common hazards found in conveyor systems. Different Conveyor systems have many different hazards, so It is essential to note that one must always be observant to their surroundings and always remain vigilant when operating or working with conveyor systems. One way of informing workers of the hazards found in conveyor systems is through toolbox talks. These talks promote hazard awareness by providing an area for open communication and knowledge sharing about specific hazards in conveyor systems, therefore preventing accidents.
You can see an example of a toolbox talk on conveyor safety below.
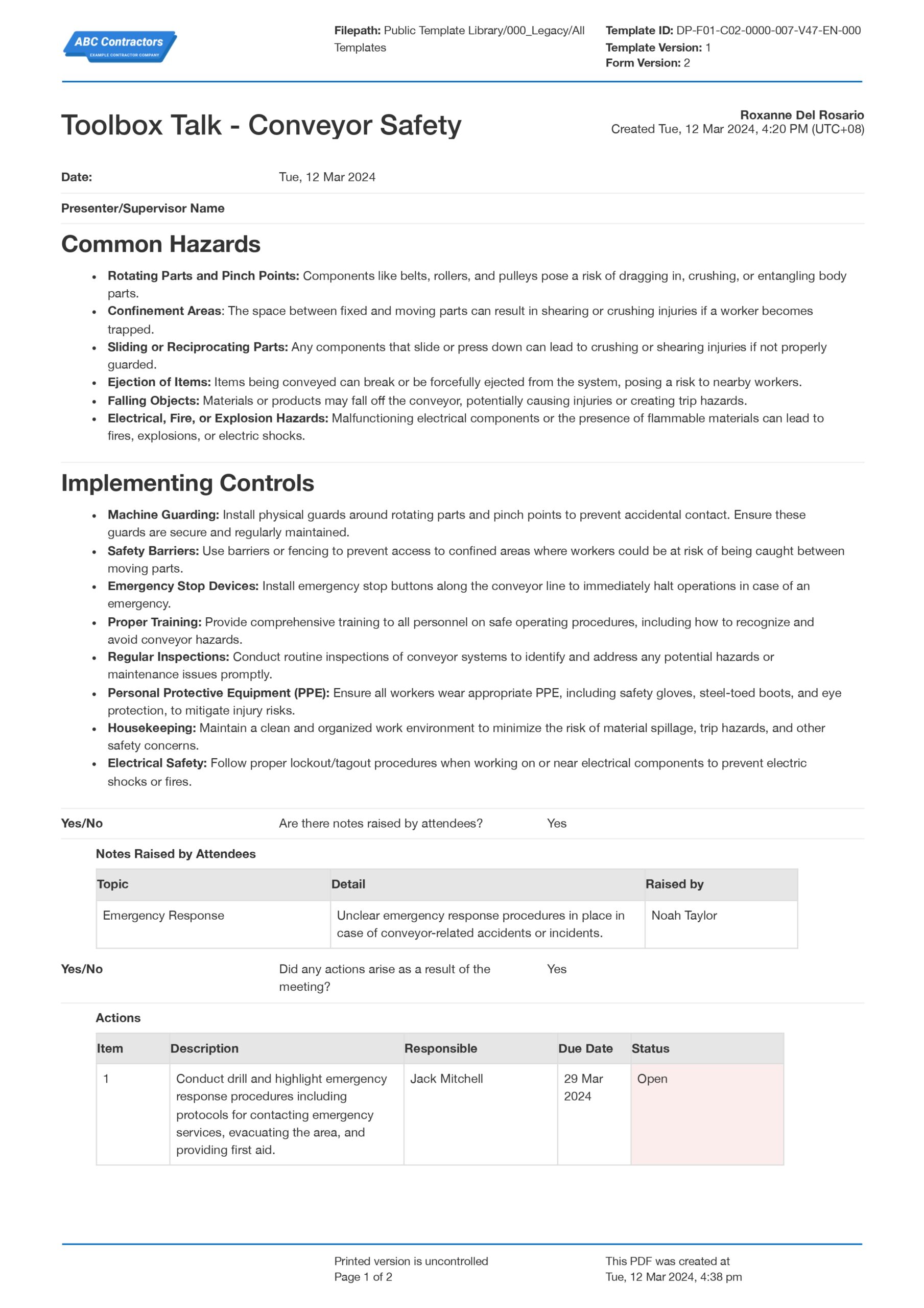
Use and customise this toolbox talk for yourself
Safety Standards
Safety Regulatory Standards as a Requirement
We have laid out that while conveyor systems are a big help in our industry, they pose significant hazards that can injure or kill people and can also severely damage company properties. World leaders recognise these hazards; thus, they have mandated safety regulatory standards requiring organisations to check if their safety controls are satisfactory enough to safeguard their employees and company assets.
Countries with Leading Regulatory Standards
Different countries have different safety regulatory standards, but has one direction in mind, which is keeping the employees and company assets safe. Here are example of countries with leading regulatory standards.
Regional Conveyor Safety Standards
British Safety Standard
The UK establishes its conveyor safety regulations based on PUWER, BSI and UKCA.
PUWER, or specifically known as the 1998 Provision and Use of Work Equipment Regulations, mandates that it is the responsibility of the owners and operators of conveyors to provide safety measures around the equipment. According to PUWER, organisations using conveyors must:
- Use conveyors for their intended purpose
- Inspect conveyors regularly after installation
- Provide training and safety information for everyone using or managing conveyors, and ensure only trained people use them
- Prevent people from accessing dangerous conveyor parts, usually through either fixed or interlocked guarding
- Install and clearly identify systems for starting, controlling, and stopping conveyors, including stopping them in an emergency
- Practise thorough conveyor maintenance to keep conveyors running safely, correctly, and efficiently. This includes keeping maintenance records
The BSI standards (British Standard Institution) provides the following specific regulations when it comes to conveyor safety:
- BS 4531:1986 covers dimensions for portable or mobile belt conveyors that have a containing trough above the belt
- BS EN 618:2002 covers managing hazards in mechanical equipment conveying bulk material
- BS EN 620:2021 covers safety and electromagnetic requirements of belt conveyors that transfer loose bulk goods
The UKCA administers marks for companies selling conveyors in Great Britain. This mark signifies that the design has satisfactorily met and adhere to the safe design regulation standards in the country.
Australian Standard
The safety regulations in Australia are governed by the Work Health Regulations (WHS). This organisation lacks specific regulations about conveyors, but it does point out that companies are required to make a comprehensive risk assessment when working with moving machinery. The risk assessment should pinpoint hazards when working with conveyors, assess the effects of these hazards, and provide the right safety controls. The goal of the risk assessment is to eliminate and mitigate the hazards defined when working with moving machinery.
Safe conveyor design, installation and operation is also defined in AS 1755-2000. This clause covers multiple relevant guidelines on conveyor safety. It shows the importance of why the implementation of a comprehensive risk assessment is vital and how specific safety measures are tailored to certain types of conveyor systems and the environment it is installed in.
American Conveyor Safety Standards
The conveyor safety standard in the United States of America is governed by the Occupational Safety and Health Association (OSHA) and American National Standards Institute (ANSI). These organisations help companies provide the proper safety measures when dealing with conveyor design, installation, operation, and maintenance.
OSHA, the federal agency responsible for ensuring safe and healthy working environments, has laid the foundations of the safety standards to address conveyor-related hazards. These are found in 29 CFR. 1910.22(General requirements) and 29 CFR 1926.555(Construction Industry Standards). These standards point out the key requirements for conveyor safety: guarding, emergency stops, maintenance and inspection, lockout tag-out (LOTO), training, material handling, electrical safety, and noise and vibration.
The American voluntary consensus standardisation system is also directed by ANSI. It is the United States member body to ISO (via USNC) and IEC, synchronising international standards to maintain consistency and compliance in various American industries.
Canadian Conveyor Safety Standards
In Canada, the Canadian Centre for Occupational Health and Safety(CCOHS) is the primary national agency that governs the advancement of safe and healthy workplace and preventing work-related injuries, illness, and death. The CCOHS has guidelines related to conveyor ergonomics, conveyor safety, and conveyors guarding by location. These have general guidelines on safe conveyor operation and maintenance. This is used as a basis for placing the proper safety controls provided in conveyor systems. Canada also adapts the ASME B.20 1-2024 which applies to the design, construction, installation, maintenance, inspection, and operation of conveyors and conveying systems in relation to hazards.
Are you up to Standards?
Now that we know that organisations are required to comply to safety regulatory standards when dealing with conveyor systems. The question is: How are we going to know that we are up to standard? The answer is pretty simple if you ask me. An organisation needs to make a checklist that has all the safety regulatory requirements of the territory, state, nation, or whatever applies. What makes it a hassle is the paperwork. Organisations have to repeat the printing, documenting, manual data entry and compiling process. This routine is time-consuming, prone to mistakes, and consumes resources like paper and ink. Fortunately, Dashpivot by Sitemate has provided a solution for this hassle of a routine. Dashpivot converts these paper checklists by creating and customising a digital form with the simple drag-and-drop form builder.
Dashpivot also safe keeps all filled forms. You can always find your safety regulations inspection without doing any manual data entry in the computer. You can view the data in all filled forms in chronological order using the timeline view in Dashpivot.
Dashpivot streamlines how your safety regulatory inspections are made, organised and tracked to save time and improve safety regulatory audit outcomes.
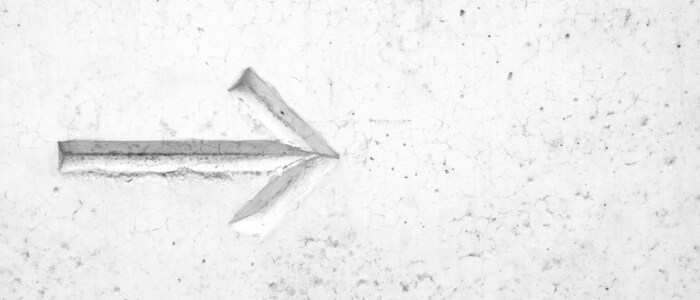
Toolbox Talk Pinch Points Template
Minimise the impact of pinch point incidents by following this toolbox talk.
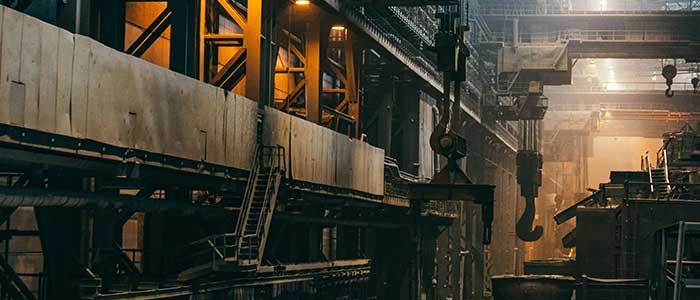
Machine Guarding Checklist template
Easily complete, manage and action your machine guarding checklists using this proven framework.
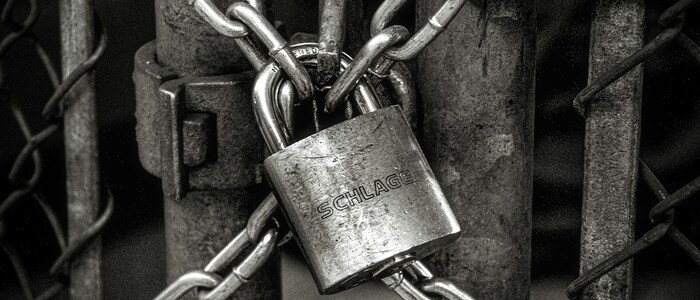
Lockout Tagout Toolbox Talk Template
Make sure your team is following your Lockout Tagout procedures by using this Toolbox Talk.