Article Page – Proactive vs Reactive Maintenance
Proactive vs Reactive Maintenance
In this article, we will define the distinctions between proactive and reactive maintenance and take a closer look at what proactive maintenance entails and why it remains the preferred choice for most companies.
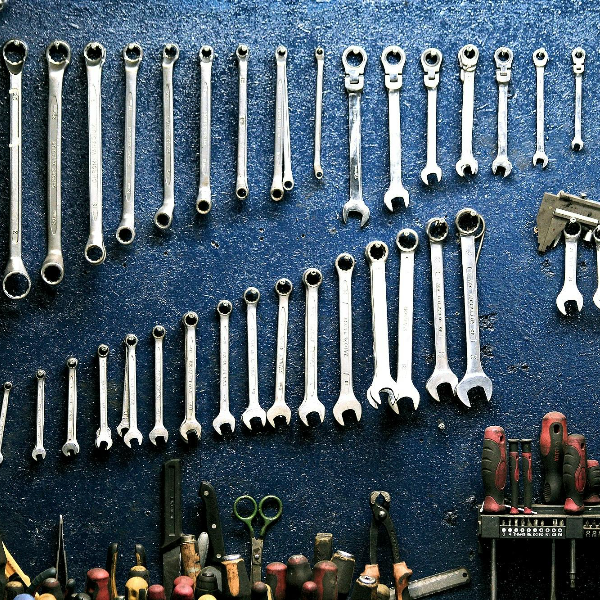
Choosing Between Proactive vs. Reactive Maintenance
What’s your business’s attitude towards maintenance? Are you more of an “If it ain’t broke, don’t fix it” type, or the type to “fix it before it breaks”? The former reflects a reactive maintenance approach—often called breakdown or corrective maintenance—because you start fixing the problem only when it happens or is discovered. This is not necessarily because of poor planning, but at times a preference for some companies because it’s arguably time-efficient. The latter holds the mindset of fixing things before they fail, which requires careful planning, analysis and a good strategy to ensure the work is uninterrupted.
In fleet maintenance, companies prefer proactive approaches because it has less damage, it makes the operations more efficient and it prevents downtime while the vehicle is in the middle of transport. However, many fail to place enough emphasis on reactive maintenance when it is needed–a topic we further broken down in our article “Reactive Maintenance Meaning” covering its importance, types and how much it holds value to the fleet management.
Anyhow, there is an ongoing discussion around these two slightly opposing maintenance approaches, and choosing between proactive and reactive maintenance becomes a critical business decision for fleet-heavy industries such as delivery and logistics, construction (including heavy equipment and service vehicles), or goods distribution—all of which rely on well-maintained vehicles as part of the operation’s backbone.
The choice would primarily fall on how the company sees the best fit to make sure the operation is efficient, while maintaining safety, asset reliability, decreasing maintenance costs and minimizing downtime.
In this article, we will delve into the distinctions between proactive and reactive maintenance and which one should you choose while striking the right balance to make it an effective fleet maintenance strategy. We’ll also take a closer look at what proactive maintenance entails and why it remains the preferred choice for most companies.
What is proactive maintenance?
Proactive maintenance in a fleet is the forward-thinking approach of repair and inspection of vehicles. Beyond the routine maintenance it attempts to fix issues before it happens by predicting it through data analysis, failure analysis, and breakdown assessment.
The goal of proactive maintenance is to avoid breakdowns, reduce downtime and repair costs along with minimizing the negative impacts of unexpected breakdown.
Every fleet-dependent business has experienced major breakdowns that caused service disruption, thereby losing customer trust and eventually losing customers. Dropping clients impacts the business, making them lose their employees and the livelihood of a family. Apart from this, vehicle issues can also endanger the drivers and the passengers, worsening the situation. Because of all of these major issues, fleet management has grown more focused on proactive methods and innovative approaches to avoid failure, so that once the vehicle and its performance begin to degrade, effective strategies are present to mitigate it before it even happens.
What’s the advantage of proactive maintenance?
At its core, proactive maintenance’s aim is to ensure the fleet runs uninterrupted. This means continuously monitoring and restoring the working condition of the vehicles, whether real-time or deferred to make sure it avoids breakdown. That being said, it would result to proactive maintenance having numerous advantages:
1. Lower unplanned downtime – The idea of proactive maintenance is that it prepares to fix before it’s urgently needed pausing the business. For example, a fleet of delivery trucks that regularly monitors the engine performance and conduct routine oil changes will likely prevent unexpected engine failures.
2. Enhanced Safety and reduce risks – Proactive maintenance helps addresses potential safety hazards before it causes accidents by helping to address potential safety hazards before it causes accidents such as by replacing worn brake pads and ensuring proper brake fluid levels, the risk of brake failure during operation is minimized.
3. Lower repair costs – There are a lot maintenance costs involving proactive maintenance especially considering initial investments however because it aims and is successful in lowering unplanned downtime it inevitably lowers repair cost.
4. Extend asset lifespan – Consistent proactive maintenance activities extend the usable life of heavy vehicles and equipment, reducing the need for expensive replacements or overhauls.
These four advantages are the most common benefits of proactive maintenance, which make it the better approach in fleet maintenance in these accounts. To explore this further, let’s go through the types and examples of proactive maintenance.
Proactive maintenance: Types and Examples
Preventive Maintenance
This involves functional, safety and performance test done regularly to the vehicles in order to avoid unexpected malfunctions and to reduce breakdowns as it extends vehicle life. This approach is conducted routinely (e.g. weekly, monthly) and or per mileage (e.g., oil change every 5,000miles)-it will be based on the understanding of the overall condition of the vehicle including its components.
Examples of these are oil changes, tire rotations, air filter replacements, battery maintenance and air filter replacements. These are the most common but it could be any inspection item that is part of fleet basic care. Some of these items can also be found in the vehicle’s manufacturing manual.
Predictive Maintenance
This involves real-time data analytics and technologies in order to predict when the vehicle and its components is anticipated to fail. It relies on data-driven collection method from sensors and machine learning to analyze data and predict or provide warning for potential failures. It is based on the premise that no reactive maintenance is needed until the data indicates that failure is about to happen.
Telematics which are a combination of GPS, onboard vehicle, wireless telematics devices and blackbox is a common tool or example of predictive maintenance for vehicles. It tracks the vehicle and transmits data in order to have a data-driven analysis to predict failures.
Reliability-Centered Maintenance
This is a strategic mix of all maintenance types meaning that it can be proactive and reactive, it’s a systematic approach by analyzing potential failure modes and conducting tailored maintenance according to the type of failure or criticality.
A typical example of RCM being applied is when it is “run-to-failure” or literally it’s being used until it fails. This is common for non-operational vehicles that are there as back-up, and non-transportation fleets such as construction equipment such as bulldozers and cranes and agricultural equipment such as tractors-they follow RCM because it’s a good avenue to prioritize reliability and cost-effectiveness since it does not need to travel long distance.
Condition-Based Maintenance (CBM)
This is only performed when signs of deterioration are detected, which are continuously monitored through vibration, temperature, and oil quality. Basically, it is done only when maintenance is impending and before a failure happens. There are claims that it is the most successful form of maintenance because it is based on the actual condition of the machine; however, it could be costly because of rigorous monitoring.
Examples of condition-based maintenance is monitoring the current condition of equipment or systems using sensors, measurements, and data collection techniques such as monitoring engine temperature and oil pressure alerting when maintenance is needed before a breakdown.
Proactive Maintenance Approach
You can see a good example of a proactive maintenance report below.
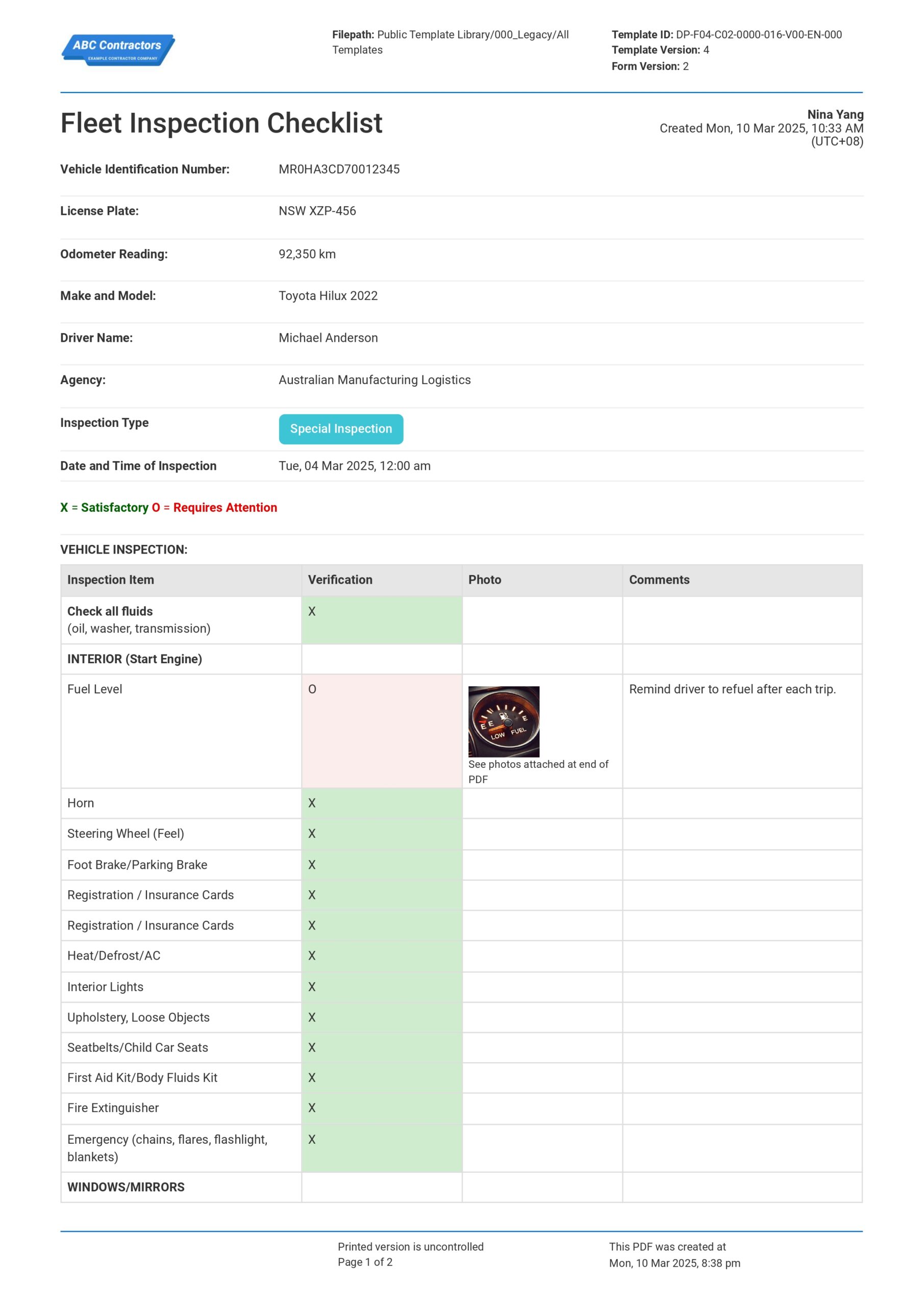
Use this free Proactive Maintenance Report for free
Proactive vs Reactive Maintenance: Which strategy works best?
Reactive maintenance, when done right and given more attention, can provide the quick fix needed during urgent breakdown operations. It’s about how you react (i.e., the process in place) when the situation occurs, and this should be balanced with proper post-inspection and proactive maintenance intentions. Missing an important preventive maintenance inspection can cost issues that only a skillfully developed reactive maintenance can mitigate in the event of a breakdown. Thus, it is the balance between both strategies that provides the fleet with a more structured approach to its maintenance efforts.
That’s not to say that if you’re truly invested in the overall improvement of the condition of your fleet, focusing on improving proactive maintenance efforts means carefully looking into the root cause of the breakdown, which is a part of proactive maintenance, since there isn’t much time to do this with reactive maintenance. However, let’s put it side by side and compare the two in important categories to identify which would work best?
Proactive vs Reactive Maintenance - which strategy is time-efficient?
Time efficiency in a fleet matters especially if you are targeting reducing downtime as a key performance indicator (KPI) in your fleet maintenance. If you are a fleet manager you would direct the resources of your company to a strategy that has a lower maintenance time, response time and repair time.
• Maintenance Time - Even when the breakdown and the maintenance schedule is unexpected, reactive maintenance can spend less time compared to proactive maintenance as proactive maintenance deals with thorough maintenance inspection to address bigger issues to avoid a breakdown. On the other hand, when you keep conducting reactive maintenance, without fixing the root cause of the issue, you would be spending more time in the long run.
• Response Time – When a problem has been reported or detected, proactive maintenance spends less time responding to it because of the prior predictive data and analysis. Response time often involves diagnosing the problem and finding the right spare parts. In reactive maintenance, since it’s unexpected, it entails a higher response time because it is unprepared.
• Repair Time – This is when an emergency or breakdown happens and requires immediate repair. If the issue is related to a previous observation, proactive maintenance can be quicker but if there’s no luxury of time, the process of reactive maintenance can be more efficient initially.
This means given the three categories: maintenance, response and repair time. Proactive maintenance strategy is evidently more time efficient than reactive maintenance.
Which strategy is cost-saving?
For cost-effectiveness, reactive maintenance has a better edge in terms of initial investment on a relatively new fleet, if a business didn’t start with proactively arranging schedules for preventive maintenance measures and decide to risk it until first few signs of failure or the “run-to-failure” strategy and then conduct reactive maintenance to repair a problem, then it would seem reactive maintenance is cost-saving because there is no initial cost necessary. Proactive maintenance would entail a higher investment depending on the type of system you would choose.
For more advance methods, this would mean installing black boxes and network of sensors to monitor vehicle condition and for manual ways just arranging series of routine inspections in the first year would entail maintenance along with labor costs. However, in the event of a breakdown if there were no proactive checks involve for instance in a brake pads replacement and there were no prior inspections of its conditions, given the urgency and the repair cost overall it would still mean a higher expense for reactive maintenance alone.
Which strategy extends vehicle health?
The condition of the vehicle depends on two main factors: usage and maintenance. Usage refers to how the driver handles the car or driver behavior, how frequently it is used, and the type of driving. There are transportation-heavy fleets, such as trucks and other heavy-duty vehicles in the logistics industry, that require closer attention and monitoring, which can lead to accelerated degradation of vehicle health. Maintenance refers to the care the vehicle receives, including regular inspections and other maintenance efforts. Regularly reviewing vehicle condition, such as tire pressure, oil changes, and brake system evaluations, greatly contributes to vehicle health.
That being said, employing proactive maintenance is more recommended for extending vehicle health because it addresses issues early on. On the other hand, a continuous reactive maintenance approach leads to repetitive repairs without fixing the root cause, compromising the vehicle’s longevity.
So, which one should a good company choose? In this case, it doesn’t necessarily mean favoring one strategy over the other; it's about finding the perfect balance between using both strategies in a way that complements each other to optimize performance and reduce breakdowns.
Common Challenges in Proactive Maintenance and Strategies to Mitigate Them
While proactive maintenance remains to be the preferred choice in fleet maintenance, there are still challenges in proactive maintenance that can be improved in order to maximize its effectivity, and below are the most common:
1. Managing driver behavior – Vehicle conditions due to wear and tear or design considerations are manageable after thorough review of data and failure analysis however if it leaves to issues with the vehicle usage due to the driver’s poor driving habits–it becomes a challenge in the effectivity of the maintenance. Not only this, maintenance can only do so much on vehicle condition that affects the safety but reckless driving can cancel all that. To mitigate this is doubling down on hiring more qualified drivers in terms of training and attitude.
2. High initial investment - As compared earlier in this article, because of the pre-failure analysis, real-time data collection and routine maintenance prior to failure, this means it entails high initial investment to set-up. However, while this is a challenge, given all of its advantages this is something that should be a challenge to get through but cannot be avoided.
3. Asset management – A systematic asset management can significantly affect the success of proactive maintenance as it provides a comprehensive overview of the lifecycle status of the vehicles, the maintenance history, and their current condition, but this also poses a challenge because of the tendency of data overload, scalability especially in managing a larger or expanding fleet. With this, it's only reasonable for a company to invest on technological advancement to help track data, manage assets and improve operational efficiency. It means investing on technology to enable real-time condition tracking, software for documenting maintenance forms and work order and software to view and manage asset records.
Final Thoughts on Proactive vs. Reactive Maintenance
When considering proactive maintenance versus reactive maintenance, it’s important to understand that both strategies have their own challenges and merits.
While proactive maintenance is the preferred choice because its advantages align with the goal of a well-managed fleet, reactive maintenance also has its place in responding to unexpected failures.
All things considered, successful fleet management is about maximizing asset lifespan, reducing downtime, and ensuring safety, while also being cost-effective and time-efficient.
Focusing on balancing the appropriate response before or after failure not only supports a company’s operational goals but also drives customer trust and business growth.
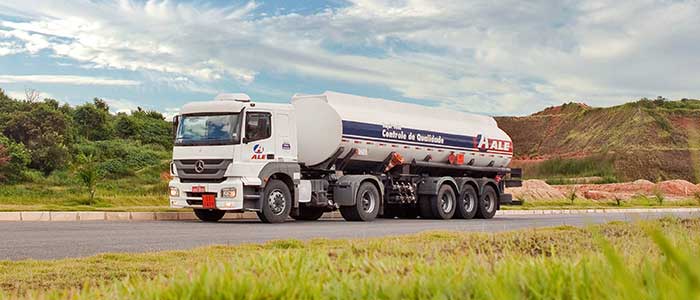
Preventative Maintenance Checklist for Trucks
This truck maintenance checklist makes truck inspections and maintenance easier and more reliable for diesel, semi trucks and more.
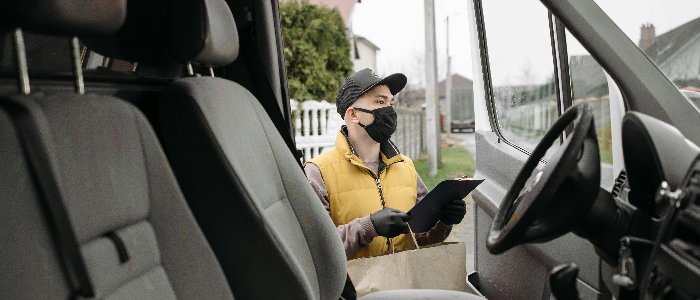
Fleet Inspection Checklist
Conduct streamlined and organised vehicle fleet inspections.
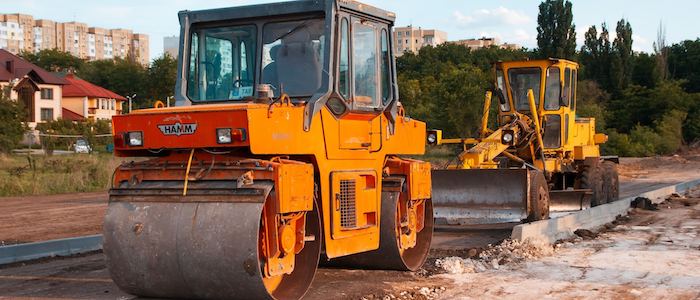
Equipment Maintenance Log
Improve how you log, track and conduct maintenance on your equipment.