Dashpivot Article β OSHA Fall Protection
OSHA Fall Protection
This article will cover OSHAs regulatory requirements for fall protection, so that you can ensure compliance.
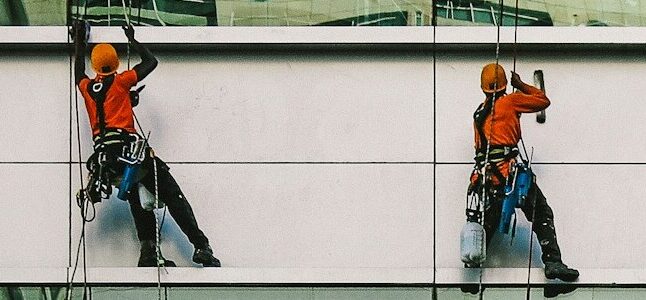
What is Fall Protection?
In the context of workplace safety efforts, fall protection refers to a wide range of programs that are aimed at avoiding accidents that may occur when working at heights. Not only does it cover strategies for lowering the likelihood of a fall occurring, but it also provides precautions to take in the event that a fall does take place.
Employers are required to arrange the workspace such that workers cannot fall from elevatedΒ workstations, overhead platforms, or into gaps in the walls and floor. Fall protection must be installed at altitudes of four feet in general industrial workplaces, five feet in shipyards, six feet in construction, and eight feet in longshoring industries, according to OSHA regulations. Furthermore, OSHA mandates that fall protection be provided regardless of the fall distance while working above machinery and other hazardous equipment.
OSHA Fall Protection in Construction
As per the Occupational Safety and Health Administration (OSHA) the standard for fall protection deals with both the human and equipment-related issues in protecting workers from fall hazards. OSHA laid out all the regulations on fall protection in construction in Subpart M. It is applicable when employees are working six feet or more above the ground. Regardless of height, it also involves protection from falling items, falls from tripping or falling through holes, and safety while working and strolling near hazardous equipment. However, workers who examine, research, or evaluate working conditions before work actually begins or after all construction is finished are exempt from Subpart M requirements.
OSHA Fall Protection Requirements for Construction Activities
Leading Edges β 29 CFR 1926.501(b)(2)
Guardrails, safety nets, or personal fall arrest devices must be used to safeguard any worker building a leading edge six feet or more over a lower level. Exceptions can only be made if the employer can prove that it is infeasible and can potentially increase the hazard in a given situation. Additionally, even if they are not engaged in leading-edge work, workers are required to be protected by guardrail systems, safety net systems, or personal fall arrest systems if they are on a walking or working surface that is six feet or more above a level where leading edges are being constructed. This is the case even if they are not working on leading-edge positions.
Roofing Work on Low-Slope Roofs β 29 CFR 1926.501(b)(10)
A low-slope roof is one that has a slope that is equal to or less than four in twelve (from vertical to horizontal). Workers who are engaged in roofing work on a low-slope roof that has one or more exposed sides or edges and is at least six feet above lower levels are required to safeguard themselves from falling by the following means:
- Guardrail systems
- Safety net systems
- Personal fall arrest systems
- A combination of conventional fall protection systems and warning line systems
- A warning line system and a safety monitoring system.
It is permissible to employ a safety monitoring system without a warning line system when one is engaged in roofing work on low-slope roofs that are fifty feet or less in width.
Overhand Bricklaying and Related Work β 29 CFR 1926.501(b)(9)
When employees are doing overhand bricklaying and other similar activities at a height of six feet or more above a lower level:
- They must be protected by guardrail systems, safety net systems, or personal fall arrest systems
- They must work in a controlled access zone (CAZ)
A guardrail system, safety net system, or personal fall arrest system is required to be installed in order to provide protection for any worker who is operating at a height that is more than ten inches below the level of the walking or working surface on which they are working.
Residential Construction β 29 CFR 1926.501(b)(13)
Conventional fall protection, such as guardrail systems, safety net systems, or personal fall arrest systems, must be used to protect workers who are engaged in residential construction that is six feet or more above lower levels. This obligation is mandatory unless another provision in 29 CFR 1926.501(b) provides for an alternative fall protection measure. The term "residential construction" is defined as encompassing construction work that satisfies the following two requirements to determine the applicability of section 1926.501(b)(13): (1) The structure being built must be intended for use as a home or a dwelling, and (2) the structure must be built using materials and techniques for conventional wood frame construction.
Other Walking or Working Surfaces β 29 CFR 1926.501(b)(15)
Generally speaking, a guardrail system, safety net system, or personal fall arrest system must be in place to prevent any worker from falling from a walking or working surface that is six feet or higher than a lower level. Refer to 29 CFR 1926.500 and 29 CFR 1926.500(b)(1) through (b)(14) for exceptions to this regulation that outline distinct requirements.
How to Use Fall Protection Systems the Right Way
Fall protection systems only work if used correctly by the workforce. While workers are required to be trained and certified to work at height, a multidisciplinary team will likely have varying levels of knowledge on fall protection systems. Thus, itβs essential to have measures to ensure everyone is correctly educated on the following fall protection systems in your workplace. Here are some useful tips establishments must benchmark to better protect their workers from falls:
Implement a Full Safety Plan
All workplaces that require fall protection systems need a full fall protection safety plan that includes fall protection protocols, and this plan should outline the types of fall protection systems suitable for different tasks, when and where to use them, and emergency response procedures. The plan must also be easily accessible and understood by all employees to promote a safety culture and compliance.
Conduct Daily or weekly Toolbox Talks
While a comprehensive safety plan is required, it is easier to train workers on fall protection systems through daily or weekly toolbox talks. To successfully hold toolbox talks on fall protection systems, leaders should assemble their team at the beginning of the shift or before height-related tasks to discuss essential topics such as load capacity calculations for fall arrest forces, proper harness fitting techniques with an emphasis on strap adjustments, and detailed anchor point evaluation procedures focusing on structural integrity and system compatibility.
Real-life examples and recent incidents should be used in the talks, keeping confidentiality while trying to enhance common mistakes and best practices.
Questions should be encouraged in the toolbox talks with experience sharing so that open learning and collaboration are fostered, and sessions become brief and workable towards reinforcing safety culture and empowering workers to give safety their priority on both individual and collective levels in their daily operations.
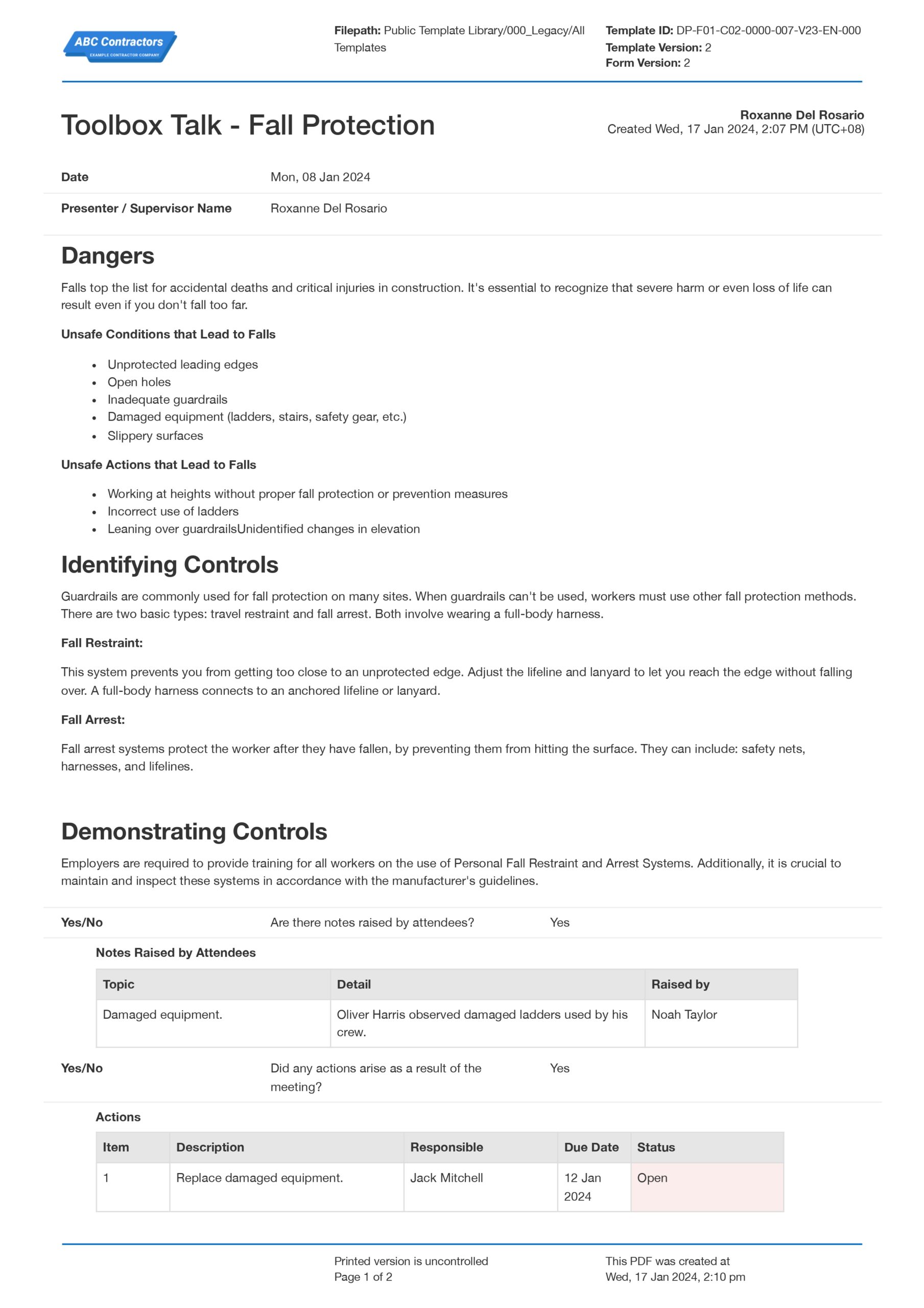
Use and customise toolbox talk fall protection forms for free
Implement Guidelines on Fall Equipment Selection
Companies must provide their workers with the technical criteria for selecting the right fall protection equipment for any job. The guidelines should include the types of harnesses for each task, such as for construction or electrical work, and the lanyard length or material (be it rope, wire, or webbing) appropriate to the fall distance and work environment. Structural integrity and load capacity must also be considered when implementing these guidelines on equipment selection.
Conduct Fall Equipment Inspection Checklists
Companies must also ensure that there are detailed inspection checklists for pre-use inspections of all fall-protection equipment, and these should include proper inspection of harness stitching for frays and lanyard integrity for cuts and abrasions. The safety mechanisms must also be tested to ensure anchor points are not compromised by any rust, some type of corrosion, or even damage. As with any safety inspections, workers must document these, noting the date, inspector name, designation, and any issues or findings found.
Using a Digital Platform for Toolbox Talks
A toolbox talk form contains the safety topics for a toolbox talk and a field to record raised safety issues and concerns. When making a toolbox form using the pen-and-paper method, the long and repetitive process can be time-consuming and compromise other important matters that can be done. Additionally, filling out toolbox talk forms out in the field subjects the paper to the environment, which can possibly soil the form and damage it, resulting in the loss of essential data needed to improve your processes. In conclusion, this traditional method is both tedious and inefficient.
In this modern era, technology has provided us with the perfect solution to this problem. With the Dashpivot Toolbox Talk app, you can now streamline your whole toolbox talk process from the creation of the forms to compiling them. Use a robust form builder to construct a toolbox talk form, or start with the free template in the template library. Launch the toolbox chat app anywhere. Add information and debate topics as you go, then have everyone quickly sign to track attendance. The toolbox talk app also automatically 'counts' and collects your data to provide insights and information on your toolbox talks.
All of these features and more in this powerful app. To learn more, take a look here: Dashpivot Toolbox Talk App
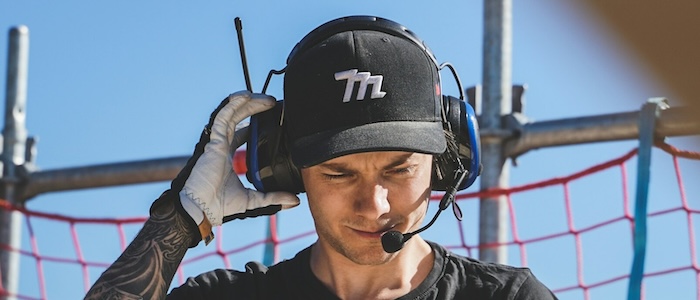
Toolbox Talk Hearing Protection Template
Keep your team's ears safe using this Toolbox Talk Hearing Protection Template.
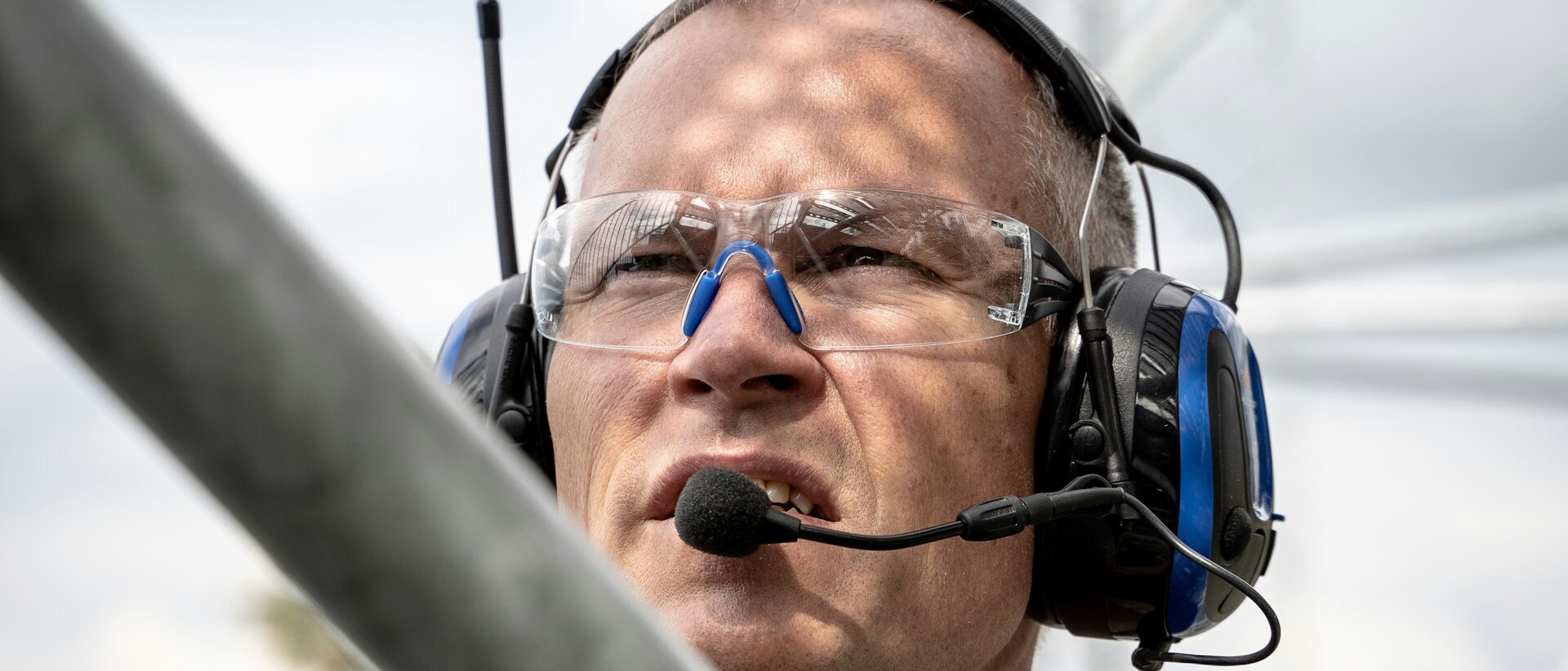
Eye Protection Toolbox template
Manage eye protection PPE and eye hazards with this digital Eye Protection Toolbox Talk template.
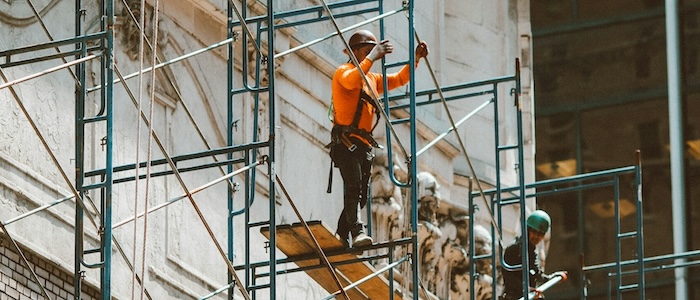
Safe Work Method Statement for Working at Heights template
Reduce the likelihood and consequences associated with terrible working at heights incidents by better managing and communicating your SWMS.