Dashpivot Article – Safety Pinch Points
Safety Pinch Points
Safety pinch points is a more important topic than it may seem, with pinch point injuries being common and dangerous in countless industries. Read on to start solving pinch point safety in a better way.
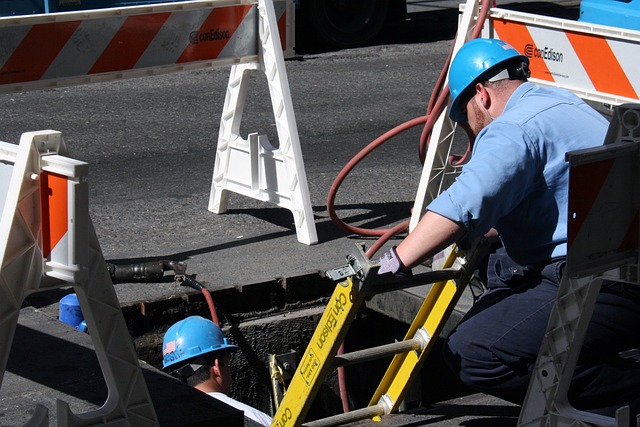
Pinch Point Meaning
When a body part gets caught between moving parts of machinery or stationary objects this is referred as a “pinch point”. It’s the point within the area in an operation where a worker can be injured when they reach in between moving parts of a machine or auxiliary equipment, or between moving and stationary parts of the machine. The term “Pinch Point” is widely used in different industries where these pinch point hazards are commonly found; industries where gears, rollers, conveyor belts, press brakes are used. Safety pinch points and safety around pinch points is more common and important than most people would think, as pinch points can cause serious injury and even death.
Pinch point injuries can include minor injuries like cuts, bruises, blisters, serious injuries like amputations, lacerations, crushing of tissues and bones, and broken bones and fatalities that’s why this should be a major safety concern in any company and efforts to avoid it should be a daily scenario.
Sources of Safety Pinch Point Hazards
Below are some of the common sources of pinch points hazards in the industry and we’ll organise it according to the unsafe opportunities with specific examples that would cause the workers to get into the pinch point:
Pinch Point Hazards in Production Lines
Pinch point hazards are rather common in production lines as these involve rotating machines, rollers, conveyer belt, feeding rollers and an operator’s body part usually their hands/fingers or parts of their clothing can be trapped in between two moving machine parts coming together or stationary surface.
Specific example of machines that are high risk pinch point hazard is a pressing machine – a machine tool that has a moving part that moves up and down to press and apply pressure to an object on a stationary plane to bend a sheet metal, to form holes and other applications. At times, high risk pinch point hazards such as pressing machine has a machine guard or cover so workers would not accidentally insert their hand when it’s in motion, or emergency stop buttons in cases wherein a body parts get caught.
Another example also would be when operating a forklift. Forklifts are not only used in manufacturing but also in construction and it poses risks in pinch point hazards e.g. when the operator gets caught in between the pinch point area of the forklift forks and the pallet being lifted, where the hands could be caught while guiding the load as well as the space between the forklift mast and payload as the arms or hands of an operator can be pinned while guiding a load into place.
Pinch Point Hazards in Construction
In construction, pinch point hazards are common because it usually involves gears, chain drives, rotating parts which are typical especially when operating construction machinery. A person could get caught in between a moving machine or when lifting a heavy material and get crushed.
Specific examples are (1) when operating a concrete mixer because of its rotating parts - the mixer could tip over crushing a person, (2) when operating a crane as the movements of a crane when moving or rotating to transport the load can create a pinch point or crush point. (3) generally, when lifting heavy materials that are not properly secured a person can be crushed or trapped in between.
Safety Pinch Point Hazards in the Office
Did you know there are several pinch point hazards in the office as well? Although, it’s not as widespread as in construction and manufacturing, still, in an office environment pinch point hazards exist. This include: closing heavy drawers or cabinet doors forcefully where fingers could get caught between the door and frame, desk drawers with sharp edges that are poorly design, paper shredders, situations where someone might get caught between a moving office chair, desk or wall, and even when a person’s body part gets hit by a moving door; basically, any situation where two objects come together with a potential to trap fingers or limb. Although these pinch point hazards may not result to severe injuries like amputations, it’s important still to make the workers be made aware of these situations.
Effective solutions to avoid safety pinch point hazards in the workplace
After identifying these hazards, let’s dive into preventing these pinch point injuries or accidents by exploring the following effective solutions:
Perform Risk Assessments in the Workplace
Assess your processes in the workplace and conduct detailed risk assessments focusing on pinch point prone processes. Identifying the pinch point hazard is already the first step in a risk assessment since it will provide the team which area to focus on, to analyze what could happen if a pinch point accident would occur and if there are enough precautionary measures in place then create plans to eliminate the hazards or at least minimise it. Conducting risk assessment means asking, “what controls do we have in place?”, “Do we need to improve our systems?”, “Did we advise the correct PPE?” it’s an important system check that will help you understand if you’re prepared enough as a company to mitigate safety issues and not only complying to regulations.
Improve your machines by adding engineering controls
Improve your machines - as pointed out; after conducting risk assessment, you will be able to identify what controls are necessary including engineering controls and machine guarding. Since pinch point hazards are common on moving equipment, engineering controls should be added to protect the worker from being caught in between the moving machines.
Many machineries of today have improved design to improve visibility and reduce accidents but it’s also at a cost. There are probably some machines in your workplace that doesn’t have built-in machine guarding but you must add in order to protect your worker. It’s important that we don’t regret after an incident and think “this could have been avoided if we improved and add upgraded our machines”
More and more industries have been investing on adding sensors in the machine to auto stop a machine in motion when it detects an operator inserting their hands. Machine guards have been added like enclosure on moving machines so as not to catch a clothing or a body part while machine is operating.
Ensure maintenance and inspections are followed
Maintenance and inspections on machines are necessary to ensure performance and efficiency. However, to make it an effective solution to prevent pinch point, a worker must not operate on a machine that is not well maintained or inspected.
Perform pre-start machine inspection to ensure machine and safety guards are operating safely. This could be visual inspection if the parts have no sign of wear and tear, if there are visible signs of damage see if it can be replaced and using this machine should be avoided. Check labels and warning signs if it’s visible and check if work area is clear – these are some of the basic inspections in the machine done during pre-start. If unsure, try to check out this free standard digital pre-start machine checklist and explore its check items. It’s also free to customise and add relevant check points depending on your need.
Training and Awareness Programs Around Safety Pinch Points and Safety more Broadly
Training and awareness programs should focus on teaching employees to know and be able to individually identify pinch points on machines. This will also encourage them to religiously wear their personal protective equipment (PPE) and follow safe work practices to be more conscious of their actions to protect themselves and others.
Training regarding machine safety would greatly help in preventing pinch point hazards, this would hold workers accountable because they’ve been made aware of the cause and effect and emphasis on maintenance and inspection to the exisiting machine guards ensuring not to operate when condition is unsafe.
Holding Toolbox Talk on Pinch Point
Why hold a toolbox talk? Isn’t it redundant to the training programs? Does it have to be done everyday? On some minor level, you may be right on redundancy after all the talk points are usually the same on the safety trainigs, but toolbox talk is more on the emphasis, a friendly reminder and more than that it’s an opportunity to talk about the exisiting safety protocols – it doesn’t have to be formal too. A toolbox talk on pinch point is a sure fire way to ensure everybody understands and believes in the controls to prevent the pinch points are necessary and that everyone understand the purpose why it’s there. And yes, while these are covered in trainings and awareness programs, the approach of toolbox talks is encouraging open conversations. After the supervisor would reiterate the pinch point risks and current protocols in place, the team can talk about it and it would be beneficial as well especially when there’s a new machine installed, a new process added, or new workers have joined.
Here is an example of a Toolbox Talk on Pinch Points:
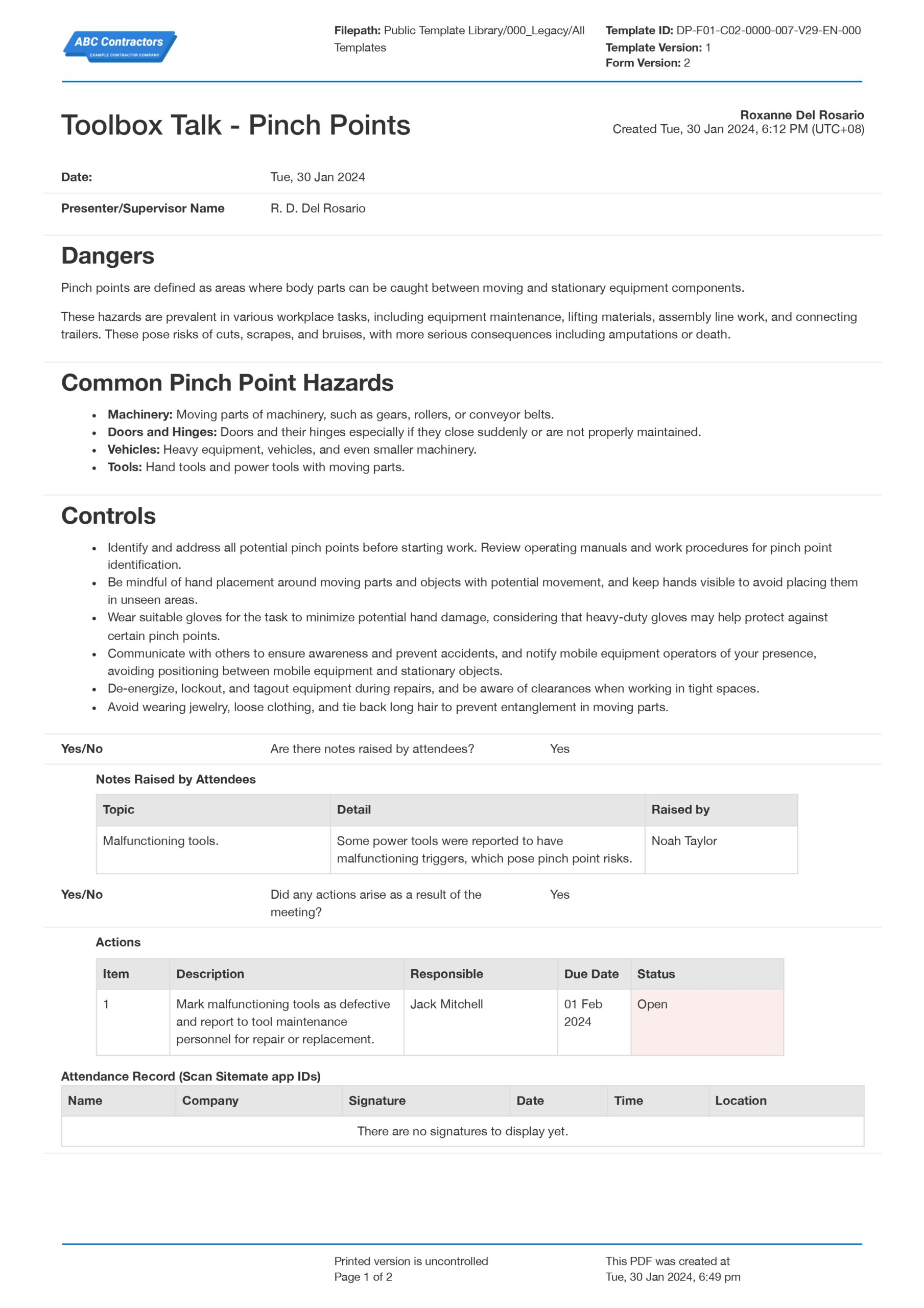
Use and customise this framework for your next safety pinch points talk
The Toolbox Talk on Pinchpoints above is pre-built with all the necessary sections but since it’s made using an app, it’s convenient because you can view and update using a tablet, phone or laptop making your toolbox talk session efficient – this saves you time to have that open discussion for questions, concerns and suggestions from your team and it’s also completely customisable, which will allow you to update the talking points if you wish and open it to the latest version.
Lastly, as this article discussed safety pinch points in the workplace, it is also worthy to note that much like what we walk through on investing on technological solutions like safeguarding the machines using sensors, it’s also high time we improve our documentation and organisational system by centralising it on one app – not only to prevent pinch point related injuries but also for the improvement of your safety management system in the workplace.
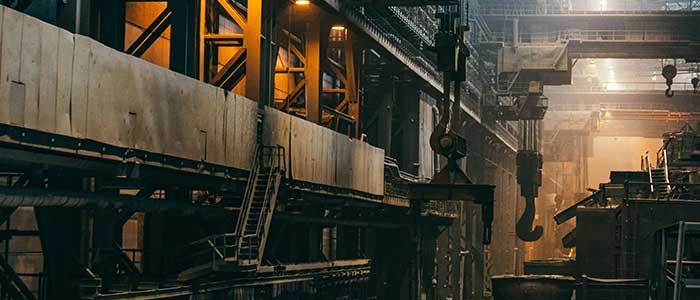
Machine Guarding Checklist template
Easily complete, manage and action your machine guarding checklists using this proven framework.
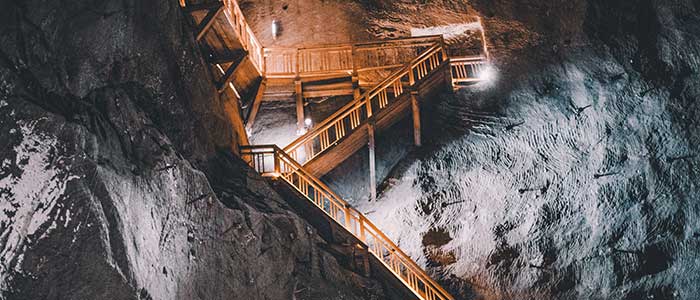
Safety Audit Checklist template
Conduct and manage your safety audits like a pro using a smart digital audit template.
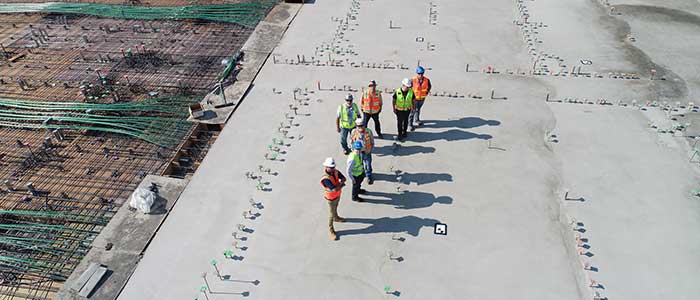
Safety Toolbox Talk template
This toolbox talk template is quick and easy to complete and signoff on site, and keeps all of your toolbox talks neatly organised and professional.