Quality – Corrective and preventive action example
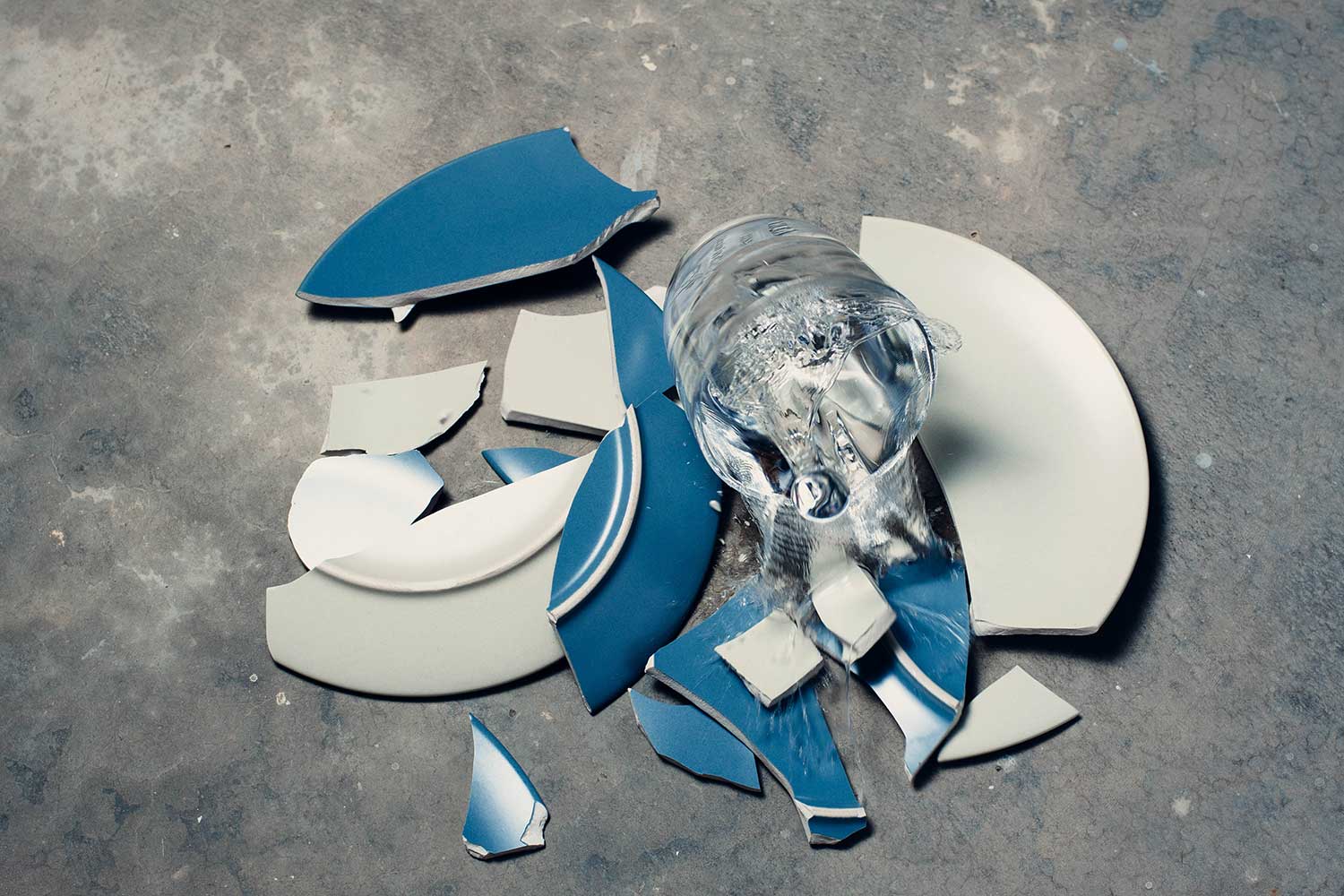
Corrective and preventive action example: Usable examples
What are corrective and preventive actions?
Corrective and preventive actions are used every day, in every day situations. People see something which went wrong or see how something could be improved, and create a 'corrective' or 'preventive' action in order to rectify the issue or improve it in the future.
This type of informal and incremental improvement process is a pretty basic human trait.
But in industries like manufacturing, construction, oil and gas etc., corrective and preventive actions are more formalised, and they are one of the most powerful tools companies in and across these industries can employ to ensure that projects and assets are delivered consistently well.
Corrective and preventive actions are a key component of any businesses quality function. They enable companies to better assure quality in the long run.
While often used interchangeably and inextricably linked, there is a key difference between the corrective and preventive action examples you'll see below:
- A corrective action is issued to simply rectify or correct a problem or defect which has been identified or found i.e an existing non conformity
- A preventive action seeks to prevent a problem or non conformance issue which may not have created a defect (yet), but which has the potential to cause a problem later
You can see how and why they are used interchangeable, as a corrective action often results in a preventive action and vice versa.
The goal of both corrective and preventive actions is to ensure that company or project processes and procedures are working well, and resulting in quality.
Now that we have introduced the idea of corrective and preventive actions, let's look at a corrective and preventive action example.
Corrective and preventive action example
The corrective and preventive action example you see below is 'wrapped' in an actual corrective and preventive report.
It's helpful to look at corrective and preventive action examples in this framework because it's more illustrative of why and how companies manage corrective and preventive actions.
The example below is a simple corrective action example.
In this instance, a subcontractor has installed discoloured downlights. This issue has been identified by a worker or party on the project, and flagged as needing to be corrected.
Once identified, the worker or another party creates and issue a corrective action report, like the example you see below, which provides the responsible party with a description of the issue - and clearly states the corrective action which is required.
The corrective and preventive example is clearly more corrective in nature, as there is a clear problem - solution match, which can be rectified quite easily.
The most important part of this issue is that the electrician corrects the issue. The electrician may look to find a root cause as to why discoloured lights were installed in the first place - especially if this is a pattern for them.
In attempting to find a root cause and create some process or procedural change, the company is veering more towards preventive actions - which will reduce the change or 'prevent' the issue from occurring in the future.
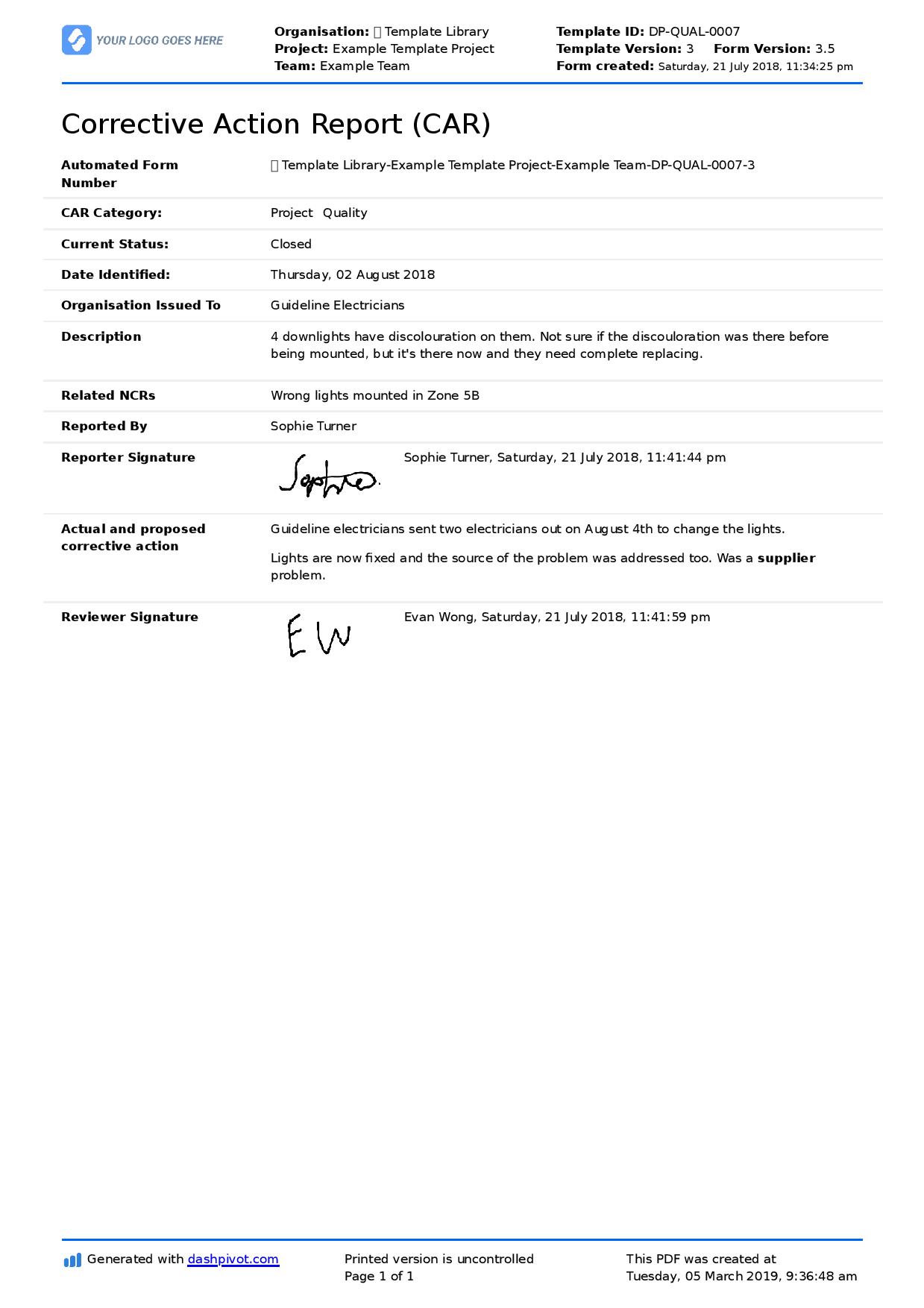
Use and edit this corrective and preventive action example now.
Other corrective and preventive action examples
The exact label which companies put on there quality and CAPA documents will vary. Some companies call their main corrective and preventive action documents a corrective action report, some call it a CAPA report and incorporate both corrective and preventive elements, while others tie preventive actions to non conformances.
The corrective and preventive action example below is a good example of how preventive actions can be neatly tied to any non conformance.
You'll see that the example below featured a non conformance in the form of purchasing non-approved materials.
There are a series of important details covered in the non conformance section of the document, but then the second half of the document focuses on investigating the root cause of the non conformance and creating a process or procedural change through a preventive action.
In this case, issuing copies of the approved supplier registers to everyone on site was the necessary action which would reduce the chance of this happening again.
You'll note the difference between the corrective and preventive action example here again:
- The corrective action example involved simply replacing a defective piece of equipment, which was likely a simple mistake or 'once off'
- The preventive action example shows that not every mistake or issued can be solved. The fence has already been purchased and installed, and the company or workers had to accept that but create a preventive action which reduced the chance of the same thing happening again
While there are plenty of easy corrective and preventive action examples to reel off, as well as non conformances, this list is essentially endless and will depend on the type of work and industry you operate in.
What's more important is to identify how corrective and preventive actions will be identified, and what to do in the face of a simple defect vs. a problematic process issue.
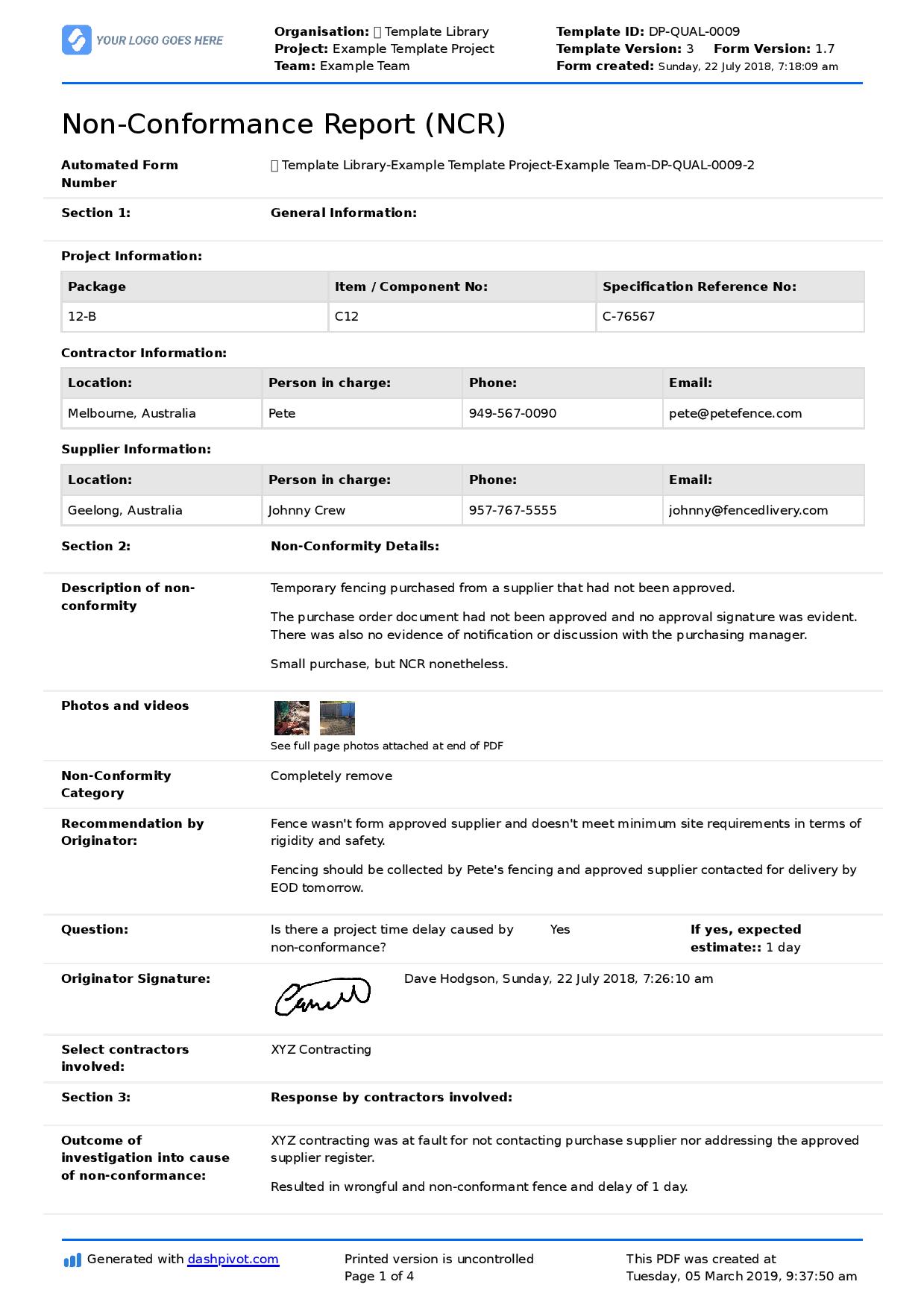
Things you can do to reduce corrective and preventive actions and improve quality
Quality is extremely important in any product or service related business. You won't stay in business for very long if client, customers or partners can trust that you will deliver on your promise of be able to assure or ensure quality.
This is why copying and implementing similar processes to the above corrective and preventive action examples is so crucial to your company and projects.
You need to have reliable processes and documents in place to respond to defects and non conformances quickly and professionally.
In saying all of this, managing quality while delivering on your commercial and financial promises can be difficult. Maintaining quality and improving quality over time requires time and effort, as does simply coordinating non conformances, punch lists like this and rectifications.
To solve the coordination and admin issues associated with many corrective and preventive action examples, a number of companies utilise CAPA software.
Using this software, you can streamline and automate much of the coordination, communication and effort required to manage the rectification and then proceeding preventive actions through digital forms (like the corrective and preventive action example above), automated workflows and real-time tracking.
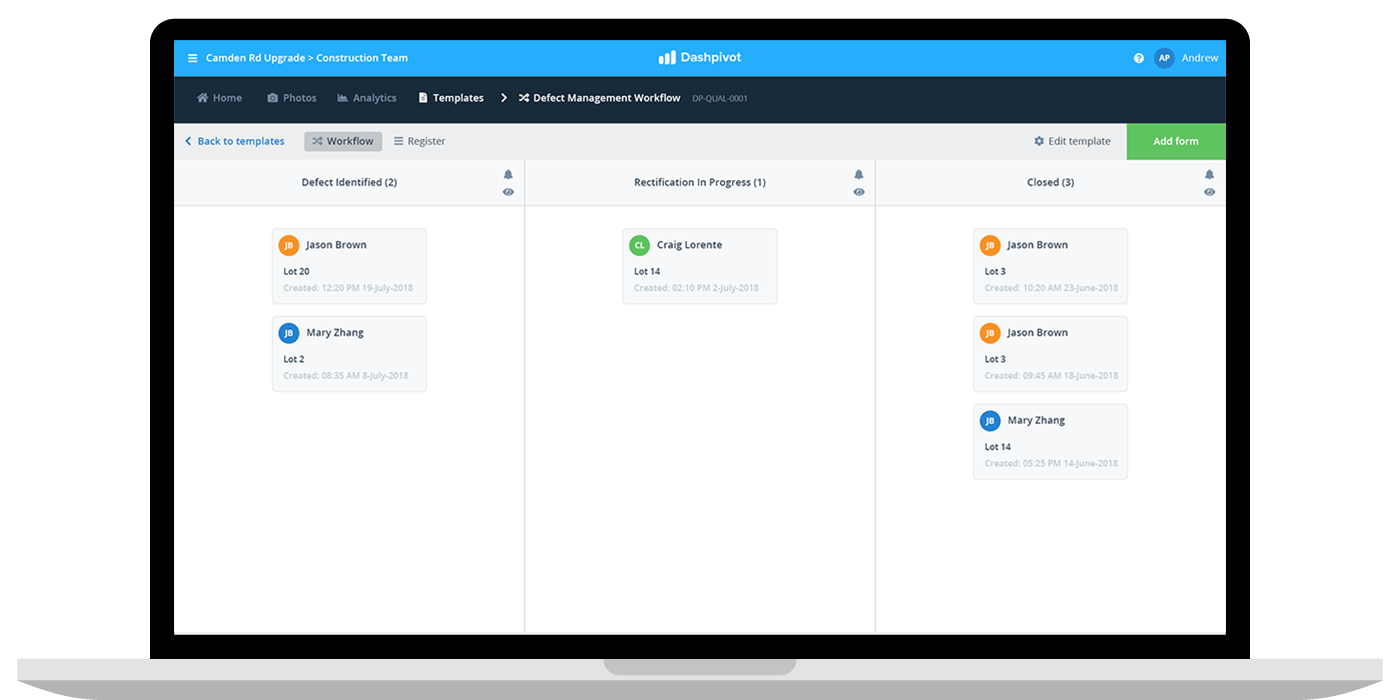
Software obviously can't 'solve' the quality issues which arise from mistakes and negligence, but they can help to speed up corrective actions as well as arm you with better information around quality issues and non conformances which enable you to make better decisions about where and how to improve.
Quality is a project and company long battle, and it will never be perfect.
But focusing on quickly rectifying issues through corrective actions and continuously creating and implementing preventive actions is a sure way to guarantee quality improvements over time.
Hopefully these corrective and preventive action examples have given you a better idea of the difference between the two, what 'normal' corrective and preventive action examples look like - and given you a couple of smart tools to improve how you manage these unfortunate but inevitable part of delivering a product or service.
People in 80+ countries use this quality management system to improve their quality processes and outcomes.
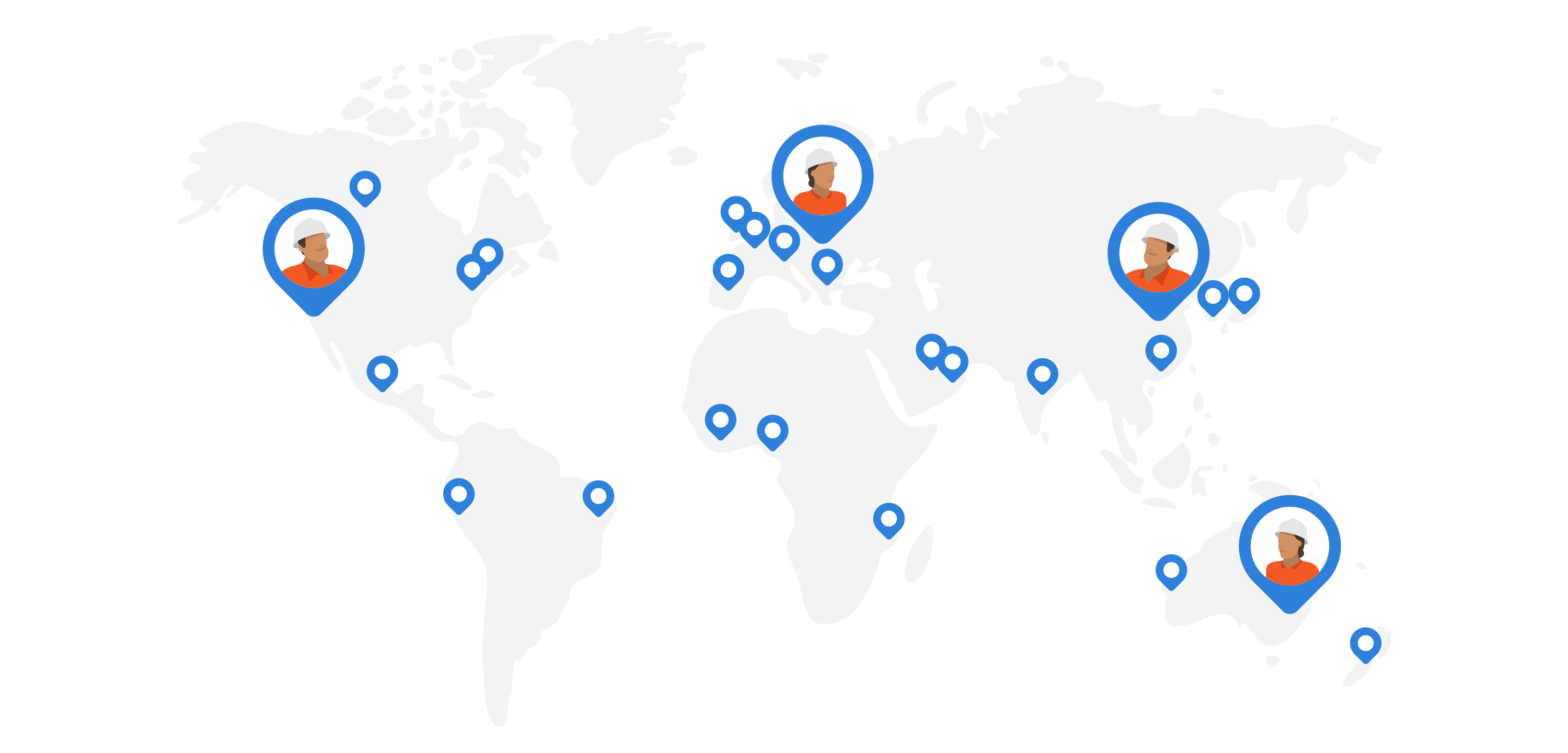