Dashpivot Article β Factory Acceptance Test Procedure
Factory Acceptance Test Procedure: Best practice FAT procedures you need to know
In this article, we break down the most common and critical Factory Acceptance Test procedures, explaining what they are, why they matter, and how to get them right every time.
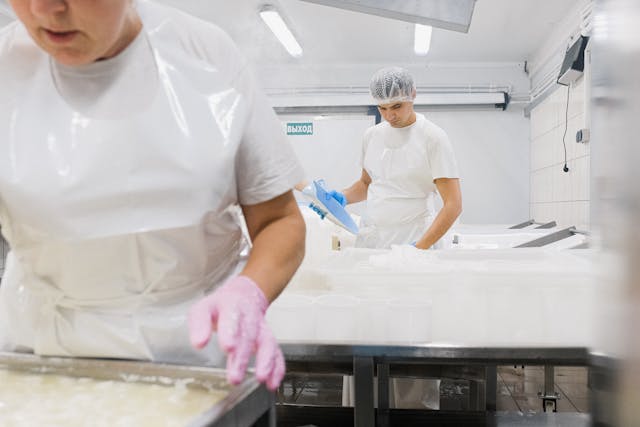
What is a factory acceptance test?
A factory acceptance test, commonly abbreviated to FAT, is a standard procedural step that manufacturing companies perform to evaluate their product at their own facility before delivering that product to a client.
In simple terms, a factory acceptance test is a test performed by the manufacturer to ensure its product meets requirements, from a technical specifications, design and functionality perspective.
Without a standardised factory acceptance test procedure, companies would be sending product with defects, which would then need to be sent back, refunded and tangled up in a logistical nightmare.
It's much easier to perform factory acceptance testing before sending product, so that you can find defects and non conformances early, and tweak the manufacturing process accordingly.
It's these quality management checks which ensure confidence between manufacturer and buyer in a consistent and scalable manner.
It's important to note that there are different types of factory acceptance tests across slightly different industries and equipment types, usually grouped into:
- Mechanical
- Electrical FAT
- Control System FAT
- Software FAT
These different types of factory acceptance tests may have some minor variation, but the overall factory acceptance test procedure mechanics and principles remain the same.
Factory acceptance test procedure best practice
Your factory acceptance test procedure may differ slightly from the below, but it will share many of the same elements, and all could and should be considered as part of looking at and improving your factory acceptance test procedures.
1. Review technical drawings, so we can compare test to drawings
One of the most important aspects of a factory acceptance test procedure is tying it back to the specification of the product at every step of the procedure.
This starts with reviewing the technical drawings. In order to know whether a product meets , we need to compare it to the as built technical drawings. These drawings provide highly detailed technical information about this piece of equipment or 'products' correct design and assembly.
A product could be almost faultless/defectless, but still not meet the requirements of the job, if it is misaligned with the as built technical drawings.
By doing this procedural step, we can confirm that the product matches the drawings, which is true of all engineering disciplines.
Practically speaking, these drawings are then included in the factory acceptance test process, so that they can be referred to at critical steps.
2. Develop a test plan, so we can test against the above
Once we have reviewed the technical drawings, we can create a test plan.
Test plans are very common in engineering disciplines, including inspection test plans in construction.
These test plans are a detailed document which outline testing procedures and the acceptance criteria associated with each test conducted.
These commonly take the form of a structured table, with each line item being a test, with its own acceptance criteria which must be reviewed and signed off before moving to the next part of the test plan.
In essence, this structured test plan ensures that the same tests are performed every time and with the same level of detail, removing human error and the ability to forget to do something from the factory acceptance test procedure.
A normal factory acceptance test plan includes:
- The overall test objectives at the start of the document
- The overall test scope (what it includes and what it doesn't)
- Test methods and procedures
- The acceptance criteria against the above, for each test method
- The test equipment and tools which will be used to again ensure standardisation
- Test timelines and scheduling, so that other variables don't become an issue with the factory acceptance test procedure
3. Conducting standardised tests inline with the test plan
This piece is quite simple, once you have a test plan included in your factory acceptance test procedure, you ca simply deploy that test plan to your teams to begin testing against.
This typically takes the form of a number of practical steps, including setting this factory acceptance testing up in a proper factory acceptance checklist template.
4. Analysing test results, and adjusting accordingly
Once we are running our tests inline with the test plan and against the as built drawings, we need tom monitor for issues/defects/non conformances, and adjust as required.
If a single piece if equipment or product has a defect, then we must analyse the full flow and look for patterns or themes which we can rectify early.
Most manufacturing companies are very good at finding defects and non conformances due to the commercial and reputation risk involved with issues, but this can quickly spiral out of control if results are not analysed well.
Implementing your factory acceptance test procedures
Engineering and manufacturing firms are very strong at building and documenting good procedures, including a seamless factory acceptance test procedure, but the whole procedure can fall over at the most important hurdle if the team on the floor is not empowered to do the actual testing and analysis portion well.
Implementing these procedures can actually be multi-faceted, as you need to build the documentation required to stick to the procedures, as well as train the team on how to execute against these procedures, and escalate any issues through the appropriate channels.
The better your documentation and process is, the less adhoc training your team will require, as the process itself will guide them through the proper testing procedures.
See below for a pretty standard factory acceptance test procedure PDF document, which would be used on the factory floor to guide floor workers against the test plan.
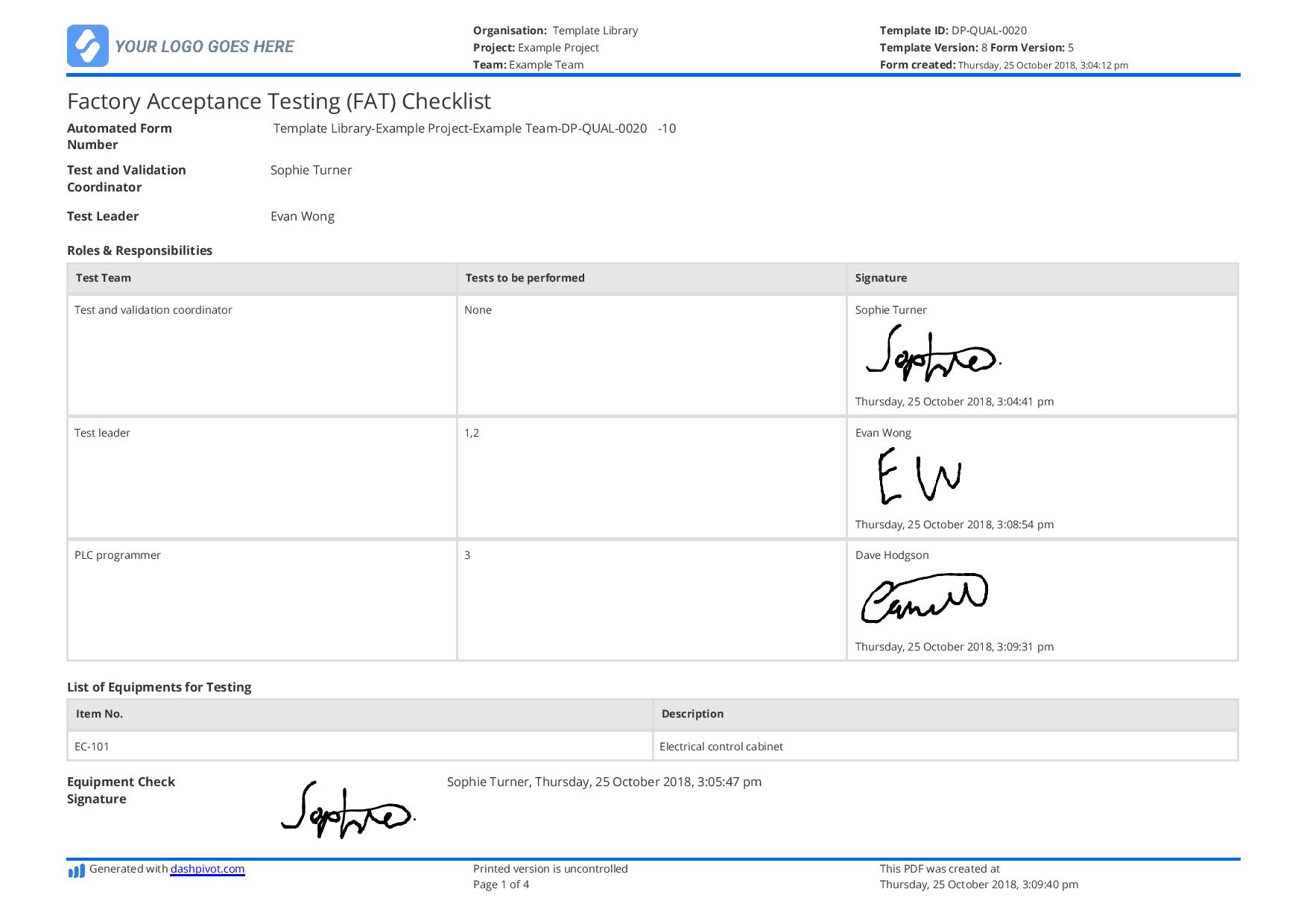
Use and customise this factory acceptance test procedure structure for free
Streamlining your factory acceptance test procedures outside of PDF instructions
Long gone are the days when companies have to rely on PDFs and paper forms to document and manage quality on manufacturing facilities.
The technology involved in manufacturing is incredibly complex, and the technology involved with documenting and tracking quality on those processes has also improved dramatically.
Part of the challenge with factory acceptance test procedures is that it still requires the human element of testing, and manual checks. This then requires data inputs from humans, to document testing outcomes.
To improve how this is managed on the manufacturing floor, you can now use dedicated factory acceptance test softwares and apps to empower testers to more easily capture and share test results.
These results are then stored in a single database, which can be easily reviewed and analysed to spot trends and patterns in the data.
This streamlines the flow of data for everyone, and results in much better quality outcomes across the board.
Build a culture of best practice procedures
The most important element of your factory acceptance test procedures is that they evolve. They evolve with changing manufacturing information and processes, as well as with the testing and product outcomes for your company and process specifically.
Quality management must always be top of mind for manufacturing companies, alongside other critical functions like safety management too, and iterating on your procedures and constantly looking for ways to improve is the only way to ensure ongoing success for your business.
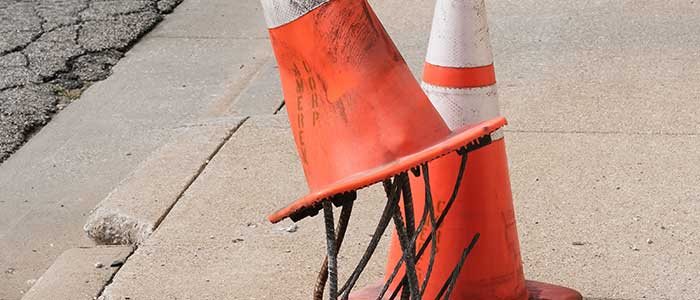
Defect Report
Manage and rectify those inevitable defects with ease.
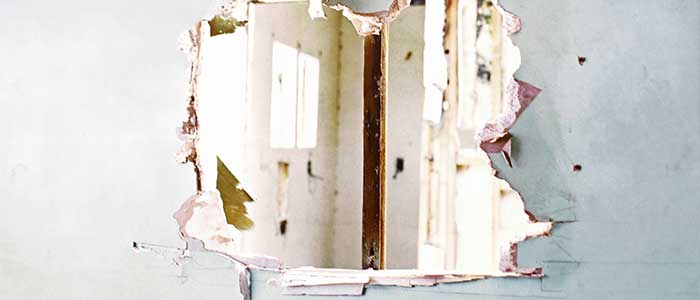
Construction Punch List
Punch your way through those punch lists with this powerful template.
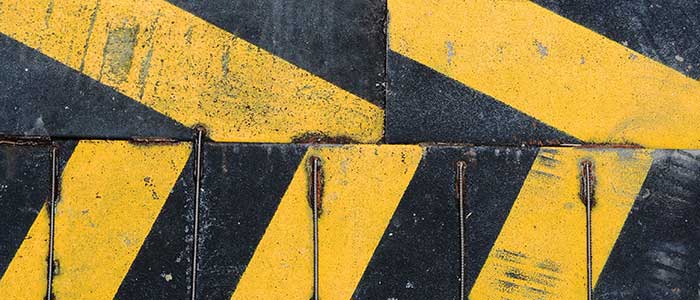
Snag list
Don't let snags get in the way of project completion.