Dashpivot Article – Lifting Operations and Lifting Equipment Regulations
Lifting Operations and Lifting Equipment Regulations
In this article, we will be learning about the LOLER of 1998 in the United Kingdom and best practice lifting operations and equipment regulations no matter where you are.
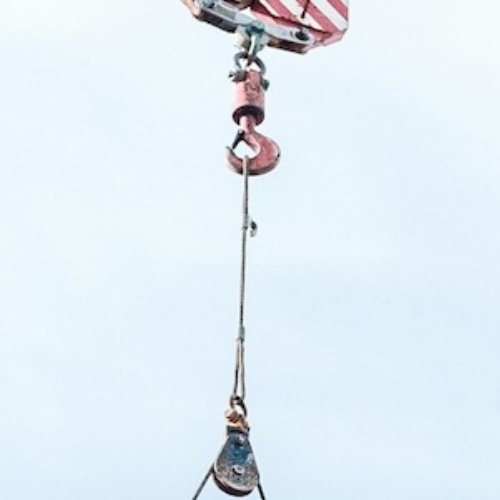
What are Lifting Operations and Lifting Equipment Regulations (LOLER)?
The Lifting Operations and Lifting Equipment Regulations 1998 (also known as LOLER ) are regulations from the United Kingdom that require individuals and businesses that own, operate, or control lifting equipment to fulfill specific duties. This includes all companies and establishments that use lifting equipment, regardless of whether or not the equipment is owned by the company, contractor, or subcontractor.
Since lifting equipment is classified as work equipment, the Provision and Use of Work Equipment Regulations (PUWER), which include inspection and maintenance, will also apply to it. It is imperative that any and all lifting activities, including lifting equipment, be meticulously planned by an experienced individual, suitably supervised, and carried out cautiously.
Requirements of Lifting Operations and Lifting Equipment Regulations
Selecting the right equipment
LOLER requires that lifting equipment must be of adequate strength and stability. They implemented that lifting equipment should be positioned or installed in such a way as to reduce the risk, as far as reasonably practicable, of the equipment or load striking a person or of the load drifting, falling freely, or being unintentionally released.
Therefore, it is crucial for companies to ensure they use the appropriate lifting equipment for the correct load. Operating lifting equipment below the object's load exponentially increases the associated hazards. To solidify safe procedures for operating the lifting equipment, establishments can employ safe work method statements for a more standardized and safe flow of activities.
Marking of lifting equipment
To continue ensuring the proper lifting equipment is used, LOLER strictly requires companies and establishments to clearly mark lifting equipment and their accessories with their safe working loads (SWL). A safe working load is the maximum load that a piece of lifting equipment can carry. Additionally, it is important to display the lifting configuration and its maximum load. This feature helps operators see and know the proper lifting method for each specific configuration.
For machines that lift people, the maximum number of individuals allowed on that lift should clearly be seen (e.g., elevators), in addition to the safe working load. Furthermore, lifts that are not designed for people but have the potential to be used in the wrong way should be placed with marked signs that indicate that they are not meant for them.
Inspection
Any lifting equipment should also undergo necessary inspections and maintenance to guarantee its safety. Because of this, LOLER requires the following:
- Users can have to do routine inspections (like for lift trucks) or basic pre-use inspections (like for lifting chains and slings).
- In some situations, inspections and checks should be performed often, usually once a week, but they may also be performed monthly or quarterly (for example, when a crane operator does checks).
- Employers are responsible for making sure that lifting equipment is inspected carefully, usually once or twice a year, but in some situations this may be more or less regular.
These checks are required by LOLER to ensure the continued safe use of the lifting equipment. To further understand the inspection process needed by LOLER, the HSE's thorough examinations and inspections of lifting equipment explain the whole process.
LOLER training and competence
Since inspections are part of the regulatory requirements of LOLER, the person conducting the inspection should be qualified, have ample experience, and have undergone the necessary training. As per LOLER, the person carrying out a thorough examination has such appropriate practical and theoretical knowledge and experience of the lifting equipment to be thoroughly examined as will enable them to detect defects or weaknesses and to assess their importance in relation to the safety and continued use of the lifting equipment.
On the other hand, this should not be the same individual who engages in normal maintenance of the equipment, since they would then be accountable for evaluating the maintenance work that they themselves have performed.
Risk assessments and safety precautions
Finding and evaluating risk is essential when organizing any lifting operation in order to choose the best tools and techniques for the task. A risk assessment assists in identifying possible dangers, assessing the degree of risk, and choosing the best management strategies to lessen those risks. Employers can see any problems and take the required action to avoid mishaps and injuries by carrying out a thorough risk assessment.
To have an effective risk assessment, LOLER suggests that employers should take into account a number of variables while conducting one, including the load's weight and stability, the state of the lifting apparatus, the skill of the workers performing the lifting operation, and the surrounding environment. Employers are required by the assessment to put in place necessary safety measures.
Record-Keeping
As required by LOLER, it is important to maintain records of all comprehensive inspections and exams, as well as declarations of conformity for all lifting equipment and lifting accessories involved in the lifting process. The appropriate enforcement body is likely to request this information during regulatory audits conducted in your enterprises.
In addition to being a statutory necessity, these records may assist establishments in identifying areas of success and areas for improvement, which they can then employ to either sustain or further develop their operations. Documentation in its entirety has the potential to contribute to the preservation and advancement of workplace safety.
Lifting Operations and Lifting Equipment Regulations Toolbox Talk Example
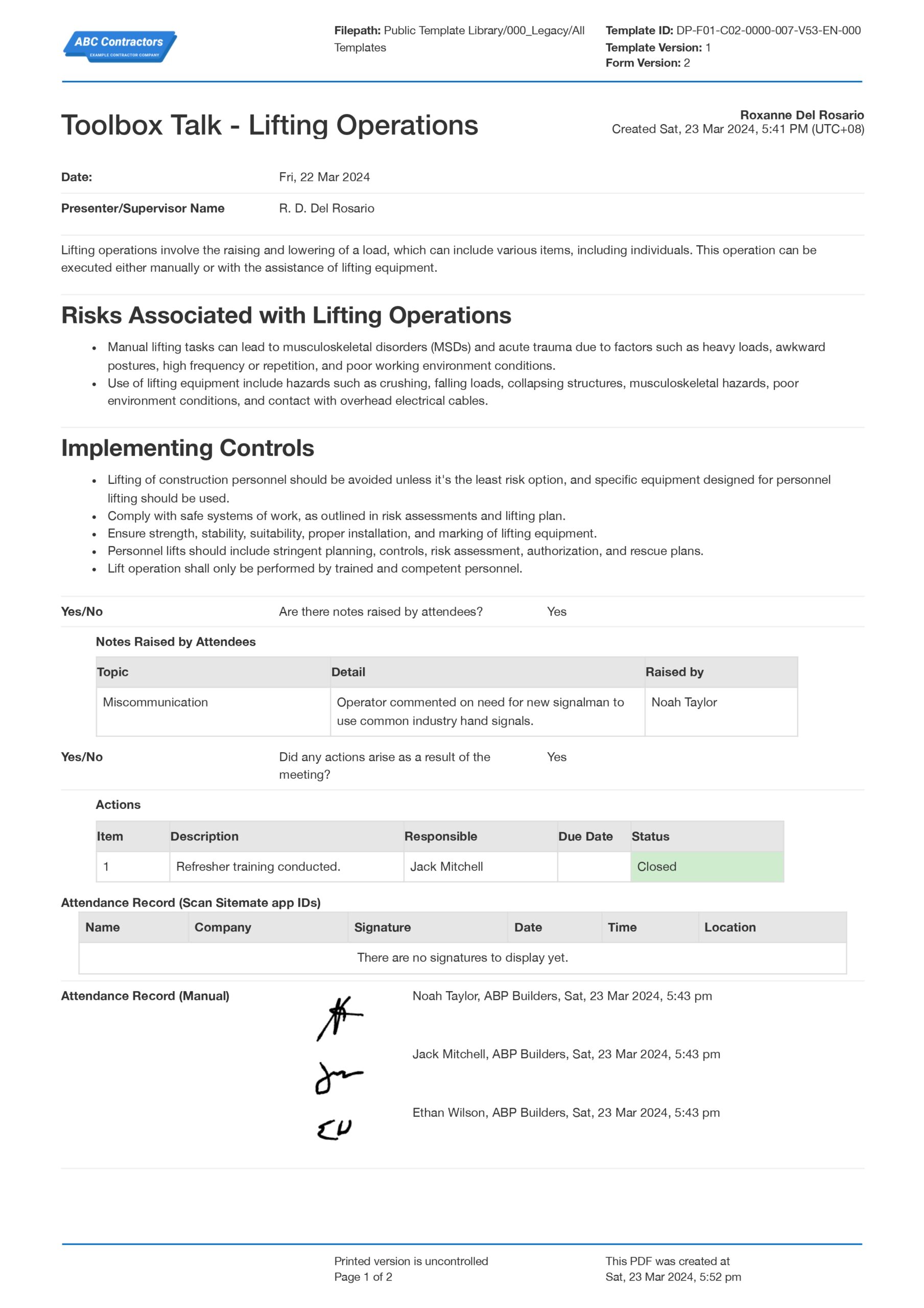
Use this free Lifting Operations and Lifting Equipment Regulations Toolbox Talk for free
Lifting Equipment Covered by LOLER?
The scope of lifting equipment that is covered by LOLER is quite broad, and the regulations may be applied to any and all industries using lifting equipment. LOLER will apply as long as workers or relevant self-employed persons use lifting equipment while on the job. LOLER considers three key factors for lifting equipment coverage. These are the following:
Lifting Equipment
LOLER defines lifting equipment as any work equipment for lifting and lowering loads and includes any accessories used in doing so. To understand the definition better, here are some examples of lifting equipment that is covered by LOLER:
- Cranes (tower cranes, mobile cranes, overhead gantry cranes)
- Forklift Trucks
- Patient Hoists
- Elevators (passenger lifts and goods lifts)
- A building cleaning cradle and its suspension equipment
- Vehicle tail lifts (hydraulic platforms for loading and unloading vehicles)
- Mobile elevating work platforms (MEWP), such as cherry pickers and scissor lifts
- Telehandlers (telescopic handlers)
- Winches, which includes manual and powered winches
- Trolley jacks and hydraulic jacks for lifting vehicles
On the other hand, lifting accessories, which are defined by LOLER as pieces of equipment that are used to attach the load to lifting equipment, providing a link between the two, need to be taken into account in determining the overall weight of the load. Examples of these accessories are
- Magnetic and vacuum devices
- Fibre or rope slings
- Single chains or multiple leg chains
- Spreader beams
- Eyebolts
- Hooks
Lifting Operations
A lifting operation is defined by LOLER as one connected with the raising or lowering of a load. A 'load' in this context refers to the thing or items that are being lifted, which may include any object, person, or individuals. During lifting operations, it is required by LOLER to monitor and control the risks to prevent any injuries or damage from occurring in a company or establishment that engages in lifting activities or is engaged in the provision of lifting equipment for the use of others. Engaging in lifting activities that involve lifting equipment necessitates meeting certain requirements. Their requirements are
- Provide a proper plan
- Deploy competent personnel
- Provide adequate supervision
- Procedures are done in a safe manner
Loads
As per LOLER, in the context of lifting equipment, the term "load" refers to any material, humans, or animals (or any combination of these) that is lifted. In order to facilitate lifting, loads are often equipped with fixed or connected points that are either permanent or semi-permanent. According to the majority of instances, they are deemed to constitute a component of the load. Here are 7 examples that are considered loads:
- Building Materials
- Machinery and Equipment
- Palletized Goods
- Vehicles
- Shipping Containers
- People
- Livestock
A new Digital Approach to Toolbox Talks
Forms for toolbox talks that are created by hand are a real pain to complete. Since there are several processes that need to be completed, they are very prone to errors. Creating and submitting a form takes up a substantial amount of time for a discussion that typically lasts for roughly fifteen minutes.
However, there is now a solution to this laborious procedure that can be easily implemented by using the Dashpivot toolbox talk app. This app has a powerful drag-and-drop form builder that enables you to construct digital forms in a more efficient manner. It is also possible to submit finished forms with only a few clicks, which will save you time since you will not have to open several programs and input all of the information on your paper form.
These are but a few examples of the things that this app may be capable of doing. The Dashpivot construction phase plan app and software is a good resource to consult if you want to learn how you may improve the efficiency of the procedures that revolve around your toolbox talk.
Conclusion
In the UK, the Lifting Operations and Lifting Equipment Regulations (LOLER) were created to help establishments and companies that make use of lifting equipment conduct a safer working operation on said equipment. To help businesses spread awareness of such regulations in the workplace, a toolbox talk can be the perfect avenue to educate workers on this vital information. These informal meetings target safety talks and also acquire insights on what needs to be further improved in the workplace, like on methods involving lifting. With toolbox talks, companies and establishments can ensure that LOLER is properly established and a safe working environment is maintained.
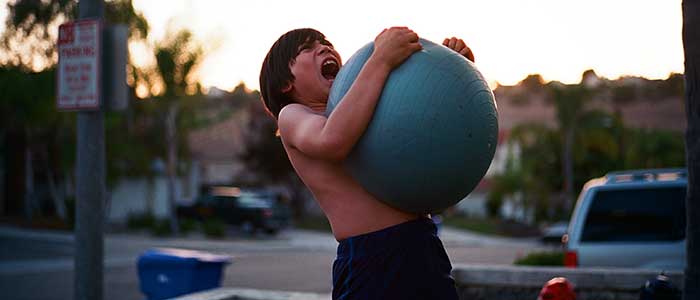
Manual Handling Risk Assessment
Ensure safe manual handling and prevent current and future incidents.
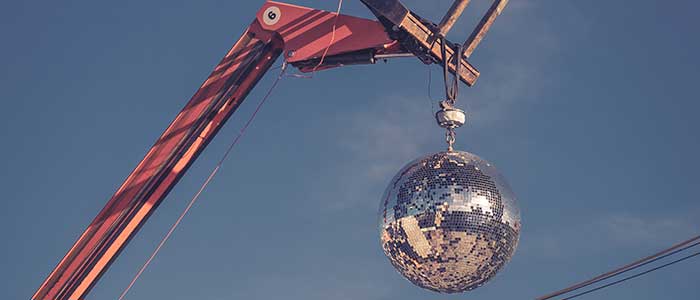
Critical Lift Plan
Approve those potentially hazardous critical lifts quickly & safely.
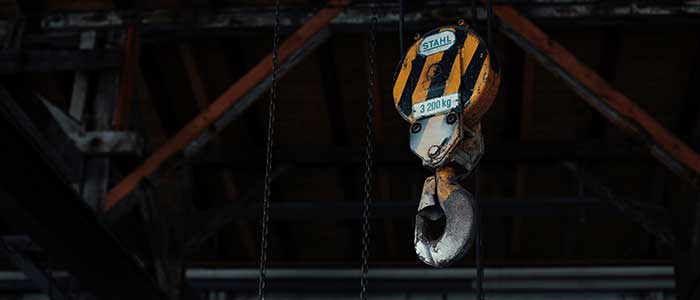
Lift Permit
Manage and approve any type of lift with this flexible permit template.