Dashpivot Article – OSHA Heat Stress Standard
OSHA Heat Stress Standard
In this article, we will discuss what OSHA has provided to address heat stress and hazards in the workplace, how you can prepare, and how you can continuously stay compliant with the standards and best practices.
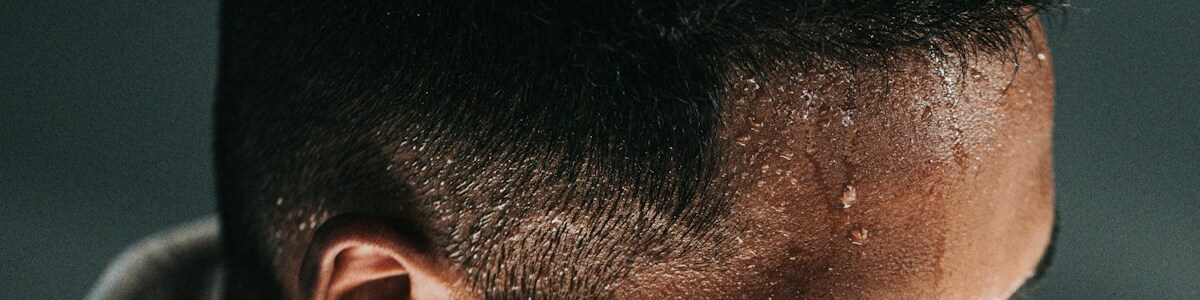
Table of Contents
Article Summary
- The OSHA heat stress standard is the source of best practices in addressing risks, hazards, and health illnesses related to heat stress.
- An informal toolbox talk for OSHA heat stress helps construction teams verify safety and compliance before starting work on site casually.
- In a toolbox talk, supervisors set daily work standards, and workers can raise heat stress and health concerns.
- Digital tools streamline communication and support safety, accountability, and health monitoring across sites.
Why is complying to the heat standards critical?
The Occupational Safety and Health Administration (OSHA) has put together in place an initiative to at least make workplaces exposed to heat risks and hazards workable.
Read more about the responsibilities of employers and the safety standards in OSHA's General Clause, which also applies to heat hazards, here in this article OSHA’S Heat Exposure: Standards.
The safety standards, including heat safety, are critical because it provides employers the best practices in assessing heat risks, making drinking stations accessible to all employees especially in high-risk areas, giving ample breaks, providing shades and cooling areas, and providing heat stress, first aid training and emergency protocols.
How to communicate the heat stress standards using an informal toolbox talk format?
Toolbox Talks are actually one of the smartest and most transparent ways to implement the standards, and build regular and casual communication between employers and employees.
They're quick (around 5-15 minutes) of safety discussions with strict documentation and attendance, which gives workers opportunities to address their concerns about heat stress and ask questions. Supervisors can also use this chance to highlight the contents of the heat stress standards that are applicable for the work of the day and realign the workforce to put health and safety as their priority.
See this digital Toolbox Talk below, perfect for communicating OSHA's heat safety and heat stress standards in the workplace.
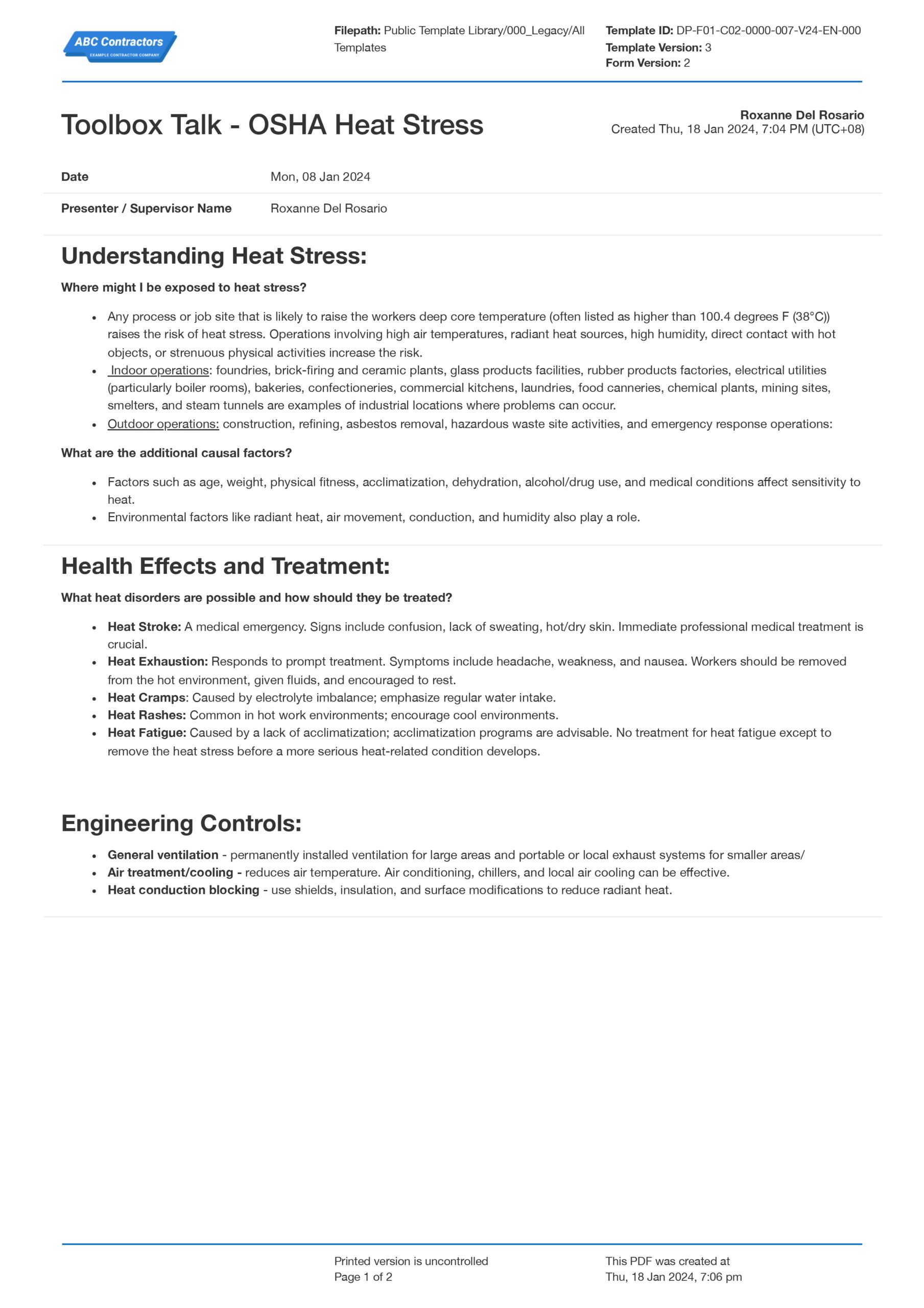
Use this OSHA Heat Stress doc for free
How to know if your workplace must comply with OSHA's heat rules?
The difficulty of complying with the rules and standards set by the agency ultimately depends on the nature of the workplace, what existing safety practices the company has been implementing, and the resources available to the employer. The industries where OSHA has almost full jurisdiction due to their nature are construction, maritime, and agriculture.
The common denominator of these industries is that the workers are exposed to heat for long periods of time, and it’s nearly impossible for them to operate without having to be exposed to some sort of heat. Read more about Occupational Heat Stress and how it is a huge concern across industries.
Most companies that expose workers to extreme heat conditions for work are mandated to comply with the heat rules. We say “most”, because it’s not all workplaces that need to comply with the heat rules. There are a few and limited exceptions like:
Workers are only exposed for a short amount of time
If the employees are only exposed to a heat index of 80 degrees Fahrenheit or higher for 15 minutes or less within any 60-minute period, the employers are actually not obliged to implement measures. However, the company is still required to assess and evaluate whether this short exposure or frequent short exposures can be dangerous for the employees.
Air-condition systems are consistently turned on in the workplace
Workplaces that consistently use air-condition systems may be exempted under the heat standard, for as long as the heat index is below 80 degrees Fahrenheit
The company/group is primarily related to emergency response activities
This is pretty self-explanatory. A very good example would be fire stations or firefighting volunteers/groups.
Remote employees
The employees are working in different locations, which is way beyond the control of the employer.
Updates on the OSHA Heat Stress Standard
OSHA has been actively addressing the growing concern of temperatures rising, which causes the increasing hazards and risks of heat-related illnesses in the workplace.
The OSHA Heat Injury and Illness Prevention Standard is, as of now, in a public input stage, meaning there will be a public and informal hearing soon this coming June 16, 2025, to develop new regulations for preventing heat injuries and illnesses in outdoor and indoor work environments. It mainly involves all stakeholders (like persons, unions, advocacy groups, etc.) in expressing their concerns about heat-related illnesses, for example, in the construction and agriculture industries, and factories and warehouses.
The main goal is to listen to the concerns and perspectives of the actual workers suffering or have witnessed the suffering and effects of heat in open and closed workplaces.
In order for OSHA to update or develop new regulations, they have to know the real-world stories, the recommendations coming from the workers, and even economic data to know what to do with certain measures, which is why a hearing is necessary to “refine” anything before having a verdict.
If you want to participate, join, or provide a testimony, check OSHA’s Heat Injury and Illness Prevention in Outdoor and Indoor Work Settings Rulemaking to stay updated with the latest instructions and status.
Preparing for summer in your industry
Working under the heat of the sun or any sort of exposure to heat is already bad enough, so having to do operations during the summer makes things even worse and hotter. OSHA is already aware of the health risks during the summer and their message is clearer than ever – with their standards and best practices, heat hazards are preventable.
On normal days and all year round, workers suffer from heat exhaustion, heat stroke, and other heat-related or heat-caused health problems. Especially in the summer, instances of these occurring rise. Prepare the summer by highlighting these three things:
Water
Stay hydrated. Encourage your employees to drink water often, and provide enough water drinking stations in all areas or at certain distances. Make stations accessible for everyone every time.
Rest
Provide ample and frequent breaks for employees. Workers are humans and their health and safety must always be the top priority.
Shade
Provide cooling stations and shading areas where workers can rest. Make sure that they provide proper seats and other resting needs.
Read more on what OSHA says about heat stress, the guidelines to follow and know, and the hazards in these articles OSHA’s Heat Stress Guide and OSHA’s Heat Exposure: Hazards.
Planning ahead, OSHA’s advices to employers
One of OSHA’s key strategies is to plan ahead – you have to be ready before the temperatures hit. Instead of “reacting” to when the heat comes, it’s better and safer to be “proactive” by planning ahead, pushing through with the plans, and adjusting accordingly during difficult times. Adjusting won’t even be too difficult if everyone’s prepared for it already.
Read more on Heat Stress Awareness to guide you on the effective strategies for heat stress prevention in various environments and this Heat Stress Hazards and Control Measures for performing risk assessments and knowing which appropriate control measures to use.
Holding trainings is also one of the key ways to let everyone know the signs and symptoms of heat illnesses, how to respond when someone shows those signs, and how to keep themselves hydrated and cool on the job whether they’re formal or informal training. Formal trainings could be ones that are offered by OSHA training centers that issue certificates of completion afterward. Informal trainings involve safety talks, which are commonly referred to as Toolbox Talks.
Smarter heat safety with digital toolbox talks
We mentioned Toolbox Talks briefly earlier, and it’s the OSHA-recommended way. Incorporating digital solutions makes it an even more effective tool for communicating topics like spotting heat exhaustion from your co-workers, or how to stay hydrated as per OSHA guidelines. Here are two digital tools that you can use for your team: Toolbox Talk OSHA Heat Stress and the Toolbox Talk Heat Stress.
Going digital means you can hold toolbox talks anywhere, by just easily bringing a phone or tablet on site – you can record attendances by easily capturing everyone’s e-signatures. Most importantly, when you’re taking down notes of everyone’s comments, concerns, and suggestions, everything can be easily recorded and documented. Compliance tracking is made way easier, and you don’t have to go through heaps of paper to check which ones were present during the informal trainings.
Simplifying heat safety compliance
Digital tools make it easier to record trainings, incidents, and safety checks in real or almost-real time. Workers on site can simply enter data through their phones, and send that over to the employees in the office. Instant documentation improves heat safety compliance, especially when there are inspections and audits.
You’re basically taking out that tedious manual burden and just focus on keeping your team safe from heat hazards and risks. With all data stored in the cloud, you can so easily spot trends and take action immediately. When you act quickly, you’re protecting your workers more effectively.
Summary of OSHA Heat Stress Standard
Overall, OSHA's heat stress standard codifies the ethical responsibility of employers to care for workers put in jobs exposed to extreme heat, assessing single and repetitive jobs whether they're heat risks or not, providing ample resources to stay hydrated, cool, and safe under heat stress, and more. It provides the best practices on how to put safety as a priority, not just between employer-employee relationships, but also between team members – knowing how to spot early signs and symptoms, reporting immediately to safety personnel, and performing emergency protocols when necessary.
Embed these practices into your daily routines and operations and prevent even the simplest and most avoidable incidents.
Frequently Asked Questions
Is the OSHA Heat Stress Standard required in construction, maritime, agricultural, mining, etc. industries?
Yes - heat safety is required and OSHA has enforced heat safety under the General Duty Clause of their Occupational Safety and Health Act. A specific standard addressing heat stress, the Heat Stress Standard, is still ongoing to be regulated, with ongoing public hearing this June 2025. Regardless, protecting workers from heat stress, risks, and hazards is an ethical responsibility.
How is technology improving heat safety compliance in the workplace?
Technology is improving on implementing heat safety and heat stress standards by replacing traditional plans, incident logs, emergency response plans, toolbox talks, incident reports, hazard analysis, and others from paper-based with digital solutions like Dashpivot. Supervisors and safety personnel can now improve compliance, keep track of documents in the cloud, automate their hazard analysis, and easily relay key safety information to teams anytime, anywhere. This leads to safer worksites, more accountable workers, better data for studying trends, and healthy employees.
Does Sitemate offer templates for OSHA heat stress?
Yes - Sitemate offers ready-to-use and editable templates that tailors your company and workflow. Companies of all sizes in construction, maritime, manufacturing, oil & gas, agriculture, mining, and more, are using these templates right now to streamline their toolbox talks, incident reports, hazard analysis, emergecy response plans, and many more.
Related resources
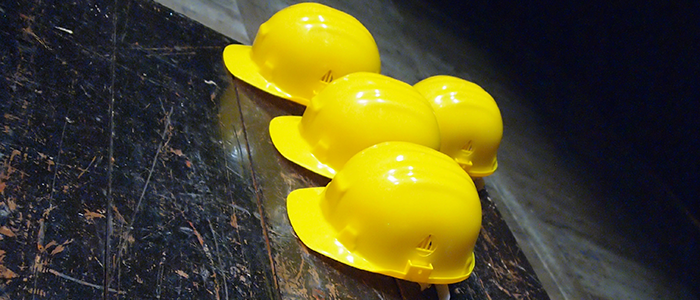
OSHA Job Hazard Analysis
Ensure you're meeting OSHA regulations with the OSHA JHA template.
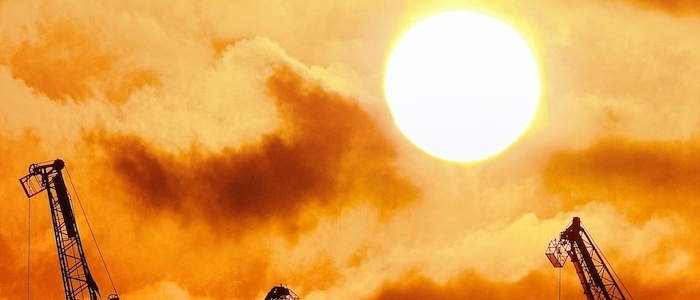
Heat Stress Toolbox Talk
Avoid heat stress incidents with PPE, prevention and identify symptoms using this Toolbox Talk Heat Stress template.
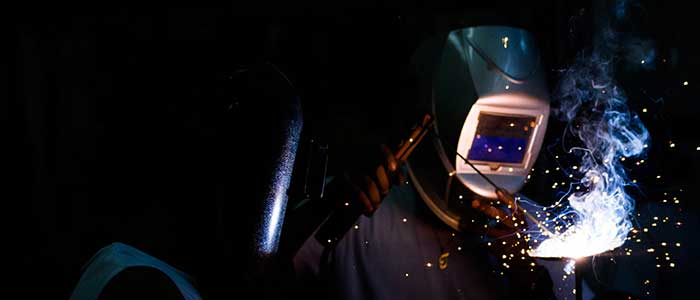
Safe Work Method Statement for Hot Works
Improve how hot works are conducted and managed across your workforce and sites by keeping a standardised and trusted SWMS.