Dashpivot Article – OSHA Requirements for Respiratory Protection
OSHA Requirements for Respiratory Protection
Learn about OSHA's respiratory protection regulations to protect workers from hazards that might endanger their lungs, as well as how to simplify compliance with OSHA's requirements.
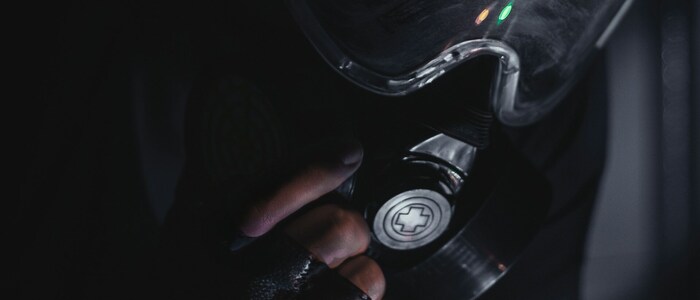
Table of Contents
Article Summary
- Respiratory protection programs reduce respiratory health hazards and ensure legal compliance by providing specific instructions for choosing, using, and maintaining respiratory protective equipment.
- OSHA has provided respiratory protection standards as guidelines to help employers manage respiratory hazards that can endanger the health of their employees.
- OSHA respiratory requirements and standards are based on the following: a respiratory protection program, the selection of respirators, medical evaluations, and fit testing.
What is the Importance of OSHA's Requirements for Respiratory Protection?
In every industry, there are numerous activities that have the potential to harm our respiratory tract. One of the most prominent examples is demolition activities involving asbestos.
Asbestos is a well-known fire-resistant construction material. However, damaging this material releases asbestos fibers, which may be inhaled. Asbestos fibers are harsh to the lungs for they scar lung tissues, which can pose serious health conditions.
OSHA requires companies to provide respiratory protection for workers and ensure that the proper protection is implemented in situations where it is deemed appropriate to be used to prevent any of them from compromising their lungs. Making sure that your employees are free from any danger will continuously keep them healthy and safe, ensuring a productive workplace, which is beneficial to any business. Furthermore, with these regulations properly implemented, companies can avoid any legal problems and maintain a good reputation.
How to format an OSHA-compliant Respiratory Protection Program & Plan?
The Occupational Safety and Health Administration (OSHA) mandated that businesses develop a respiratory protection program in line with 29 CFR 1910.134 to prevent workers from breathing in pollutants that might potentially cause damage to their respiratory tract. Given this information, what defines a good respiratory protection program that is both effective and compliant?
Well, the answer is easy. The document should cover all the criteria outlined in 1910.134(c). It should outline the methods for choosing respirators, conducting medical exams of personnel, performing fit testing, and maintaining respirators. Take a look at the provided example below to gain a clearer understanding of the program's structure.
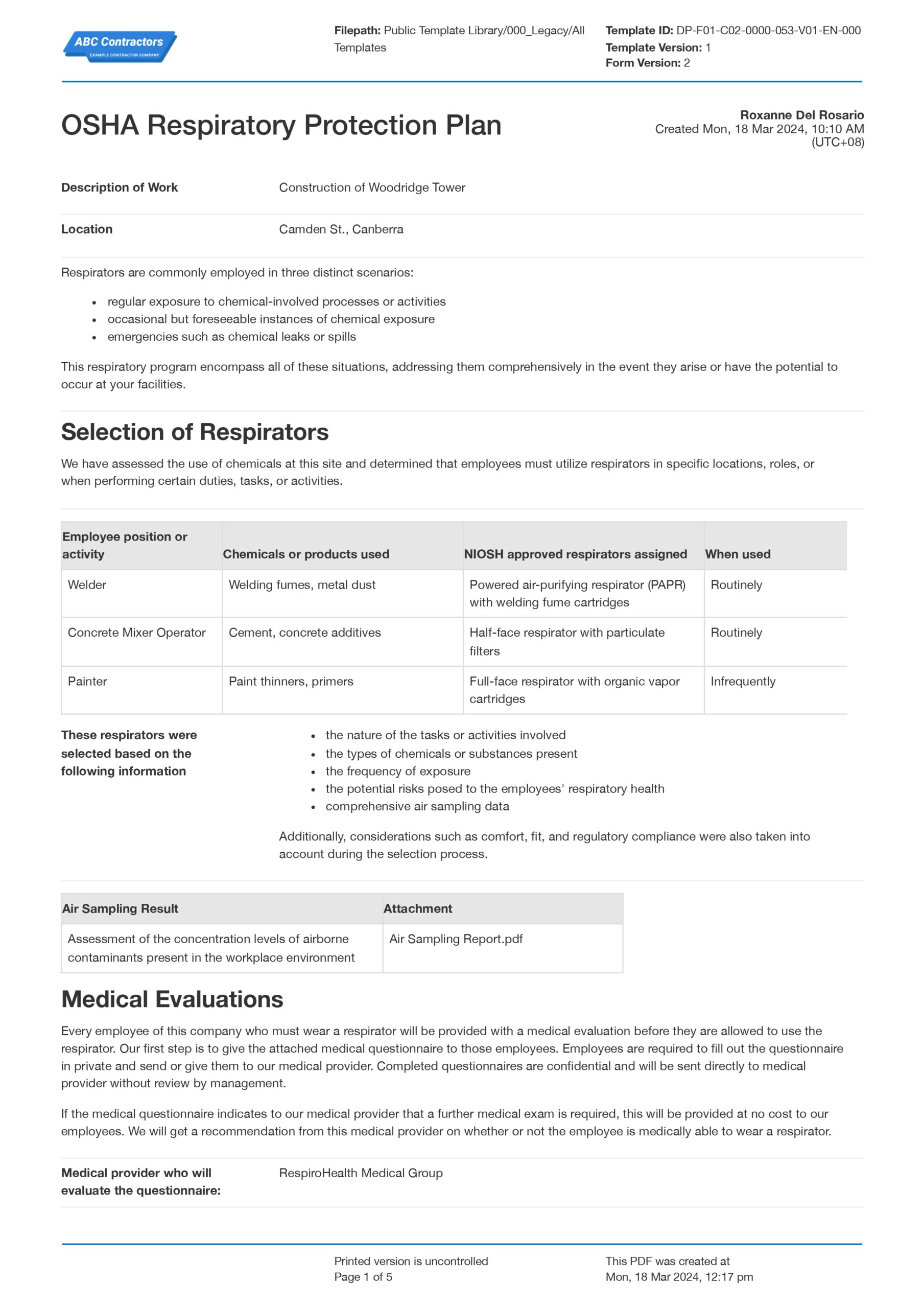
Use this OSHA Respiratory Protection Program for free
What are OSHA's Requirements for Respiratory Protection?
Providing respiratory protection is one effective control measure to protect the respiratory tract health of the workers. Employers must ensure the provision of appropriate protection in specific situations. To help companies secure this, OSHA has provided standards on respiratory protection.
1910.134(c) Respiratory Protection Program
OSHA mandates that the employer create and execute a documented respiratory protection program that includes components for mandatory respirator usage as well as worksite-specific procedures. Employers must create and execute a documented respiratory protection program with worksite-specific procedures in every workplace where respirators are needed to safeguard employees' health or when the employer requests them. The program will be revised as needed to account for changes in working circumstances that impact the usage of respirators. If relevant, the employer must incorporate the following clauses from this section in the program:
- Procedures for selecting respirators
for use in the workplace. - Medical evaluations of employees to use respirators.
- Fit testing procedures for tight-fitting respirators.
- Procedures for proper use of respirators in routine and reasonably foreseeable emergency situations.
- Procedures and schedules for cleaning, disinfecting, storing, inspecting, repairing, discarding, and otherwise maintaining respirators.
- Procedures to ensure adequate air quality, quantity, and flow of breathing air for atmosphere-supplying respirators.
- Training of employees in the respiratory hazards to which they are potentially exposed during routine and emergency situations.
- Procedures for regularly evaluating the effectiveness of the program.
1910.134(d) Selection of Respirators
OSHA established rules requiring employers to choose and provide a suitable respirator according to the respiratory danger or hazards to which the employee is exposed, as well as workplace and user characteristics that impact the dependability and performance of the respirator. Moreover, they require the employer to select a respirator with NIOSH certification and to operate it in compliance with the certification's guidelines. Employers are responsible for identifying and assessing any respiratory hazards in the workplace. This assessment must involve determining the physical and chemical forms of the contaminants as well as a fair estimate of the exposures of employees to the respiratory hazards. If employers are unable to identify or properly estimate the exposure of their employees, they must consider whether the atmosphere poses an immediate danger to life or health (IDLH).
The employer shall provide the following respirators for employee use in IDLH atmospheres:
- A full-facepiece pressure demand is SCBA certified by NIOSH for a minimum service life of thirty minutes.
- A combination full-facepiece pressure-demand supplied-air respirator (SAR) with an auxiliary self-contained air supply.
- NIOSH certification is required for respirators intended solely for escape from IDLH atmospheres.
- All oxygen-deficient atmospheres shall be considered IDLH. Exception: If the employer demonstrates that, under all foreseeable conditions, the oxygen concentration can be maintained within the ranges specified in Table II, OSHA Oxygen-Deficient Atmospheres
,for which the employer may rely on atmosphere-supplying respirators.
Employers must provide respirators that are good enough to protect workers' health and meet all OSHA rules during normal situations or expected emergencies in non-IDLH atmospheres. Employers must choose a respirator that meets or exceeds the necessary level of employee protection using the assigned protection factors indicated in Table 1 Employers must make sure that the protection factor provided to a combination respirator (such as airline respirators with an air-purifying filter) is suitable for the mode of operation being employed.
1910.134(e) Medical Evaluation
OSHA states that the physiological load that a respirator may cause a worker varies depending on the kind of respirator used, the job and working circumstances, and the worker's health. OSHA thus requires that before an employee is fit tested or compelled to wear a respirator at work, the employer must conduct a medical review to ascertain the person's suitability for the device. The employer has the right to cease the employee's medical assessments once they are no longer required to wear a respirator.
Here is what OSHA requires in the medical procedure:
- The employer shall identify a physician or other licensed health care professional (PLHCP) to perform medical evaluations using a medical questionnaire or an initial medical examination that obtains the same information as the medical questionnaire.
- The employer shall ensure that a follow-up medical examination is provided for an employee who needs it.
- The follow-up medical examination shall include any medical tests, consultations, or diagnostic procedures that the physician or licensed health care professional (PLHCP) deems necessary to make a final determination.
- The medical questionnaire and examinations shall be administered confidentially during the employee's normal working hours or at a time and place convenient to them. The medical questionnaire shall be administered in a manner that ensures that the employee understands its content.
- The employer shall provide the employee with an opportunity to discuss the questionnaire and examination results with the PLHCP.
In determining the employee's ability to use a respirator, the employer shall obtain a written recommendation regarding the employee's ability to use the respirator from the PLHCP. The recommendation shall provide only the following information:
- Any limitations on respirator use related to the medical condition of the employee or relating to the workplace conditions in which the respirator will be used, including whether or not the employee is medically able to use the respirator.
- The need, if any, for follow-up medical evaluations.
- A statement that the PLHCP has provided the employee with a copy of the PLHCP's written recommendation.
1910.134(f) Fit Testing
OSHA mandates that an employee be fit tested using the same brand, model, type, and size of respirator that will be used before requiring them to wear any respirator with a tight-fitting facepiece that can withstand negative or positive pressure. This section outlines the types of fit tests that OSHA has permitted, how to perform them, and how to utilize the test findings.
- The employer shall ensure that employees using a tight-fitting facepiece respirator pass an appropriate qualitative fit test (QLFT) or quantitative fit test (QNFT).
- The employer shall ensure that an employee using a tight-fitting facepiece respirator is fit tested prior to initial use of the respirator, whenever a different respirator facepiece (size, style, model, or make) is used, and at least annually thereafter.
- The employer shall conduct an additional fit test whenever the employee reports, or the employer, PLHCP, supervisor, or program administrator makes visual observations of changes in the employee's physical condition that could affect respirator fit. Such conditions include, but are not limited to, facial scarring, dental changes, cosmetic surgery, or an obvious change in body weight.
- If after passing a QLFT or QNFT, the employee subsequently notifies the employer, program administrator, supervisor, or PLHCP that the fit of the respirator is unacceptable, the employee shall be given a reasonable opportunity to select a different respirator facepiece and to be retested.
- The fit test shall be administered using an OSHA-accepted QLFT or QNFT protocol.
- QLFT may only be used to fit test negative pressure air-purifying respirators that must achieve a fit factor of 100 or less.
- If the fit factor, as determined through an OSHA-accepted QNFT protocol, is equal to or greater than 100 for tight-fitting half facepieces or equal to or greater than 500 for tight-fitting full facepieces, the QNFT has been passed with that respirator.
- Fit testing of tight-fitting atmosphere-supplying respirators and tight-fitting powered air-purifying respirators shall be accomplished by performing quantitative or qualitative fit testing in the negative pressure mode, regardless of the mode of operation (negative or positive pressure) that is used for respiratory protection.
- Qualitative fit testing of these respirators shall be accomplished by temporarily converting the respirator user's actual facepiece into a negative pressure respirator with appropriate filters, or by using an identical negative pressure air-purifying respirator facepiece with the same sealing surfaces as a surrogate for the atmosphere-supplying or powered air-purifying respirator facepiece.
- Quantitative fit testing of these respirators shall be accomplished by modifying the facepiece to allow sampling inside the facepiece in the breathing zone of the user, midway between the nose and mouth. This requirement shall be accomplished by installing a permanent sampling probe onto a surrogate facepiece or by using a sampling adapter designed to temporarily provide a means of sampling air from inside the facepiece.
- Any modifications to the respirator facepiece for fit testing shall be completely removed, and the facepiece restored to NIOSH-approved configuration, before that facepiece can be used in the workplace
Achieve OSHA Respiratory Protection Compliance with Ease
Compliance with the laws set out by the Occupational Safety and Health Administration (OSHA) may pose quite a challenge. Most companies still largely rely on traditional, paper-based methods for administrative and documentative processes around these regulations. If we really pay attention to the hours and resources consumed by this method, it reveals its demanding nature. It takes a lot of office space, paper, and ink, as well as time that might be spent on other crucial tasks, to build documents from scratch, upload data to generate insights, and then print them again for documentation. In summary, this process is really not ideal for both productivity and the environment.
Fortunately, technology has paved a way for us. Using the Respiratory Protection Plan App, you can now streamline your safety processes to make your workplace safer and your processes more efficient and compliant. With the versatile safety app, you can easily digitize any of your respiratory protection safety forms, papers, or processes. Using an intuitive drag-and-drop builder, create personalized templates for safety meetings, safety inspections, lock-out-tag-out processes, risk assessments, checklists, and safety reports. Using this app does not only ensure compliance and standardization but also eliminates laborious processes and tedious paperwork. By going digital, you have more time to devote to other important tasks, reduce costs on resources, and improve productivity, all while keeping your workplace safer, compliant, and more efficient.
Summary of OSHA Respiratory Protection Requirements
It is always the employer's responsibility to ensure workplace safety. Hazards and dangers must always be placed with controls and precautions to keep the employees free from them, especially when they can potentially have ill effects on the lungs. Fortunately, OSHA has provided standards that can guide employers on how to safeguard their employees from these respiratory hazards. Furthermore, establishments must enforce procedures on controlling these hazards and make ways to implement these standards to better secure workplace safety. Making use of a respiratory protection program will help companies achieve such things.
Frequently Asked Questions
Are the OSHA respiratory requirements required in the construction industry?
Yes- All construction companies,contractors, and subcontractors must comply to the regulations on respiratory protection.
In what ways does technology streamline respiratory health and safety compliance?
Technology is transforming the ways to stay complaint by replacing the manual pen-and-paper method with digital solutions like Dashpivot. Teams can now complete tasks faster, automate steps, and improve compliance. This leads to better processes around administrative workflow and make more rigid database for records on safety.
Does Sitemate offer usable templates and documents for respiratory protection?
Yes - Sitemate offers ready-to-use and editable templates for respiratory protection. We also offer a Respirator Medical Evaluation Questionnaire App that can also be edited for your workflow. Companies of all sizes in the every industry are using these templates right now to streamline their medical evaluations for respiratory protection.
Related resources
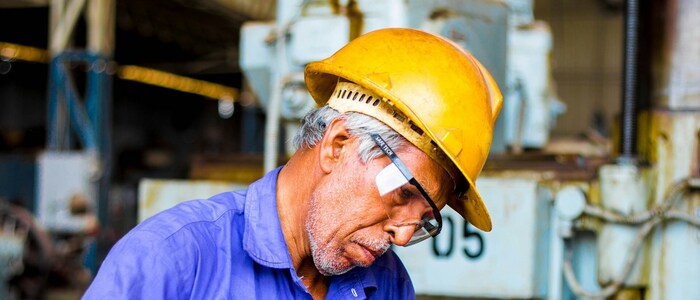
Eye Protection Toolbox Talk
Manage eye protection PPE and eye hazards with this digital Eye Protection Toolbox Talk template.
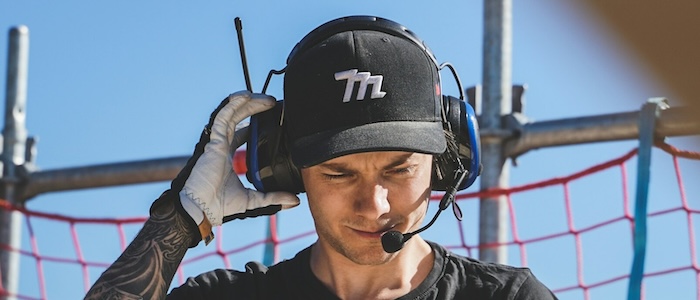
Hearing protection toolbox talk
Keep your team's ears safe using this Toolbox Talk Hearing Protection Template.
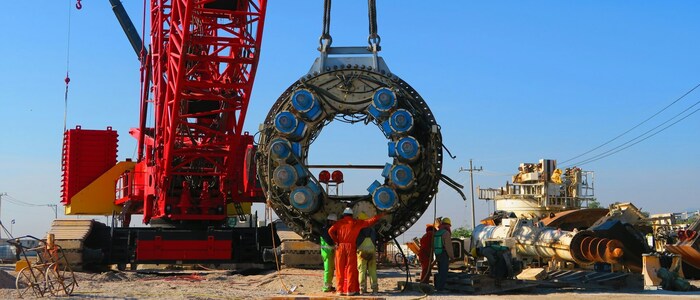
Line of fire toolbox talk
Keep your team safe from Line of Fire incidents by following this toolbox talk template.