Safety – PPE record keeping
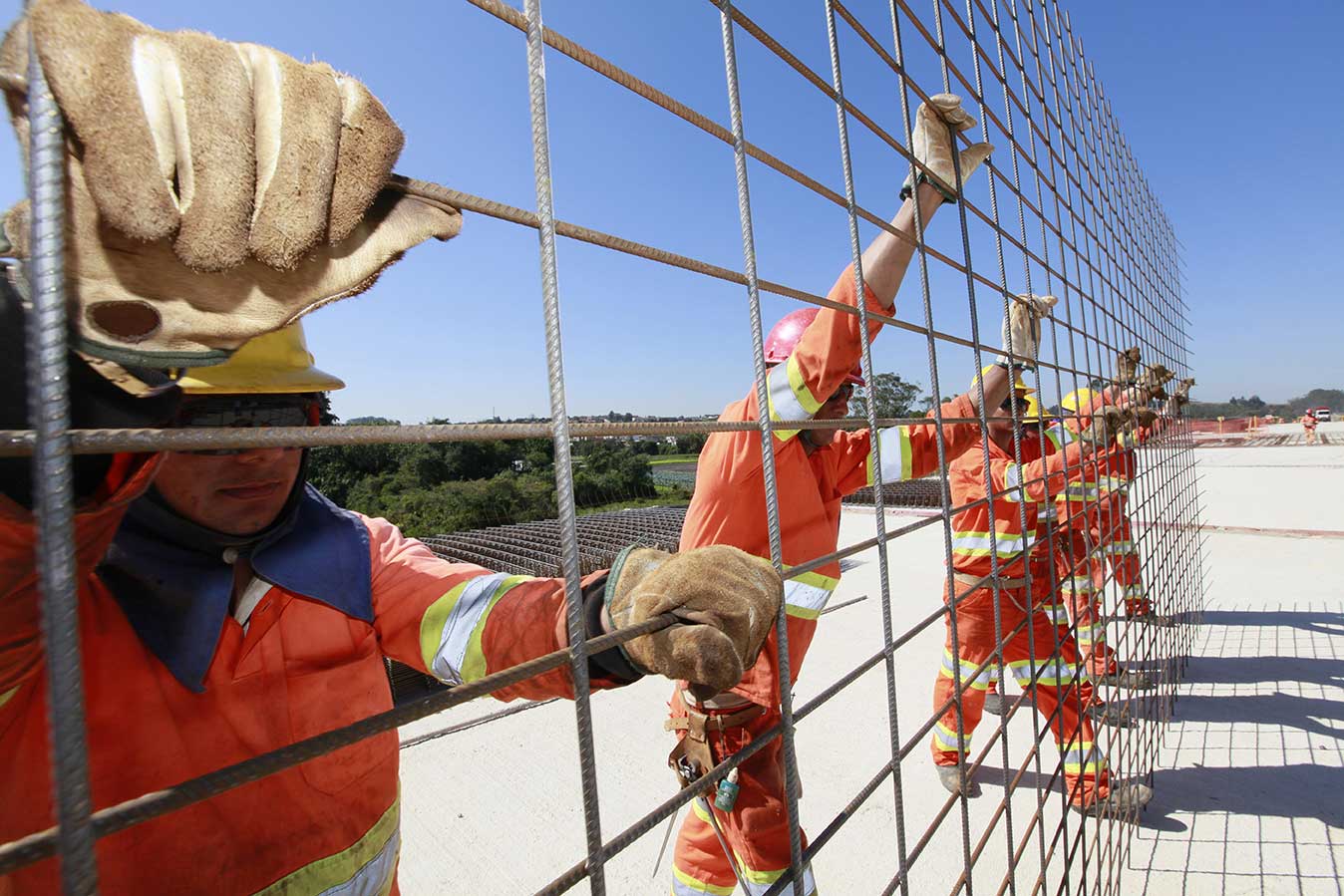
PPE Record keeping: The best example of PPE record keeping
About PPE record keeping
For very obvious reasons, personal protective equipment, commonly abbreviated to PPE, is a very important part of workplaces all over the world, particularly in the heavy industries like construction, oil and gas, mining, manufacturing and more.
In these industries, PPE has been a focus for authorities, companies and workers over the years, as safety has slowly and incrementally improved, thanks in part to better PPE practices.
While the most important element of PPE practice is concerned with using it and using it properly, there is a lot of work which goes on behind the scenes in terms of PPE record keeping in order to ensure that:
- People have the latest and greatest PPE
- The PPE is applicable and relevant to the specific job at hand
- The PPE is in good working condition
- That people have been adequately trained in how to use PPE
The key to ensuring all of these things and avoiding mistakes is to practice good PPE record keeping - which spans the entire PPE spectrum from buying and issuing equipment all the way through to disposing of it and replacing it.
The best PPE record keeping example
Most companies and workers have become very competent in ensuring that everyone on site or in the workplace has the PPE they need to get their job done safely. They have also become increasingly at many other aspects of PPE management and enforcement.
But one area where many companies still struggle when it comes to PPE is in PPE record keeping. The scale, lifecycle and frequency of PPE use makes it a bit of a logistical nightmare.
So below you'll find a couple of great examples of how you can streamline and improve your PPE record keeping through a few smarter forms.
The PPE record keeping examples below highlight how the flow of PPE record keeping information dictates how well a company can keep up with what is going on.
Slow and delayed PPE records equate to delays in PPE issuing, over-issuing PPE and wasting money, and delays and non-compliances on projects.
Documenting and issuing PPE
There are two main dimensions of PPE record keeping; one dimension is how PPE is ordered and requested and can be considered forward and backwards; the other dimension is the static and horizontal 'storage' of PPE records so that things can be looked back at and reconciled.
On the first dimension, the two most critical flows of PPE record keeping information are PPE requests and PPE issuing.
PPE requests involve workers requesting specific PPE items, while PPE issues are the records which highlight when PPE was issued. They are often linked (the request comes before the issue), but sometimes PPE needs to be issued because it has expired, because teams have expanded etc. etc.
How PPE is requested and formally issued has a massive impact on how effective your PPE record keeping is, and how much time and effort people must take just to order or issue a piece of equipment.
The PPE request form you see below is an example of a digital PPE request form which can be filled out and sent directly on site with a mobile or tablet.
When a worker requires some PPE, they can simply open their mobile device, access the form, and complete the request. Once requested, the form is automatically sent to a designated person with the authority and power to purchase the PPE, who can then simply approve the order.
Because the document is cloud-based, all of the records created are instantly pushed to the cloud, so no person or administrator needs to spend their time reconciling PDFs or paper-based forms.
You can see how powerful this type of simple automation is compared to using paper and verbal orders.
These PPE record keeping practices leave a real-time audit trail of everything which has been ordered, and guarantees that every request or issue is seen and actioned by the right person.
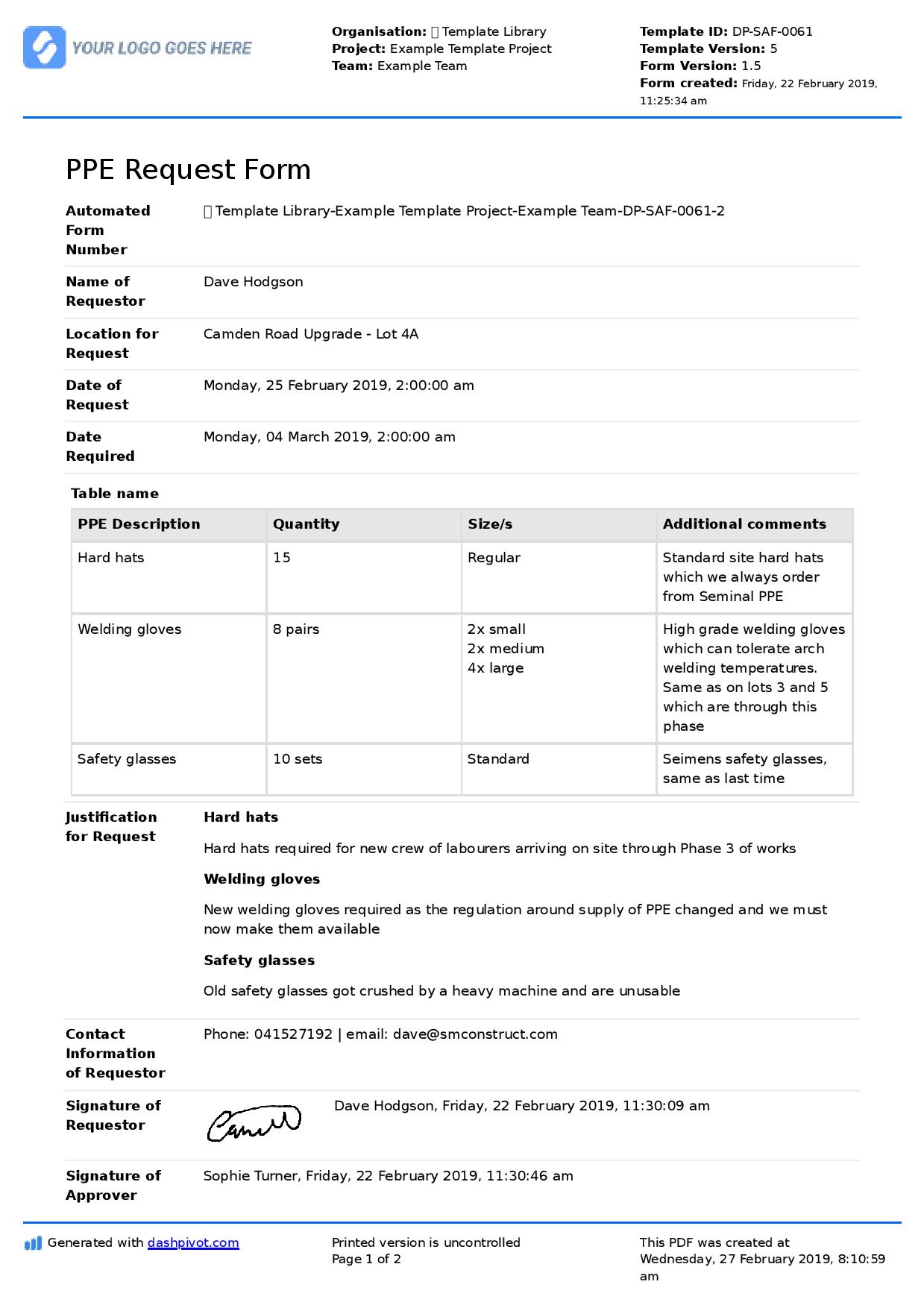
Use this PPE record keeping form for free.
Maintaining strong PPE records
So what happens when all of these records are captured and organised?
Most companies use PPE registers to maintain an accurate database of their PPE records.
The purpose of this database is multi-faceted. In part, it's so that companies know how much PPE they have in inventory and how much is actually being used. But it's also a living database which indicates to companies when PPE needs to be replaced, or when new training is required.
Without a single source of truth which someone or multiple people can quickly reference, it's almost impossible for management and safety teams to quickly identify when PPE actions are required.
This increases the risk on the company and workers, by increasing the chance that expired and inadequate PPE is being used, which can be catastrophic for health and safety as well as legal and financial issues.
Most companies are very familiar with using and maintaining registers or spreadsheets, but you'll want your register to have a few smarts as well.
Ideally, you register will be able to notify the responsible person when PPE is expiring. In addition, having a collaborative sheet which multiple people can work on and update ensures that there aren't multiple versions of your master PPE record keeping sheet floating around - so you have a single and reliable source of PPE record keeping truth.
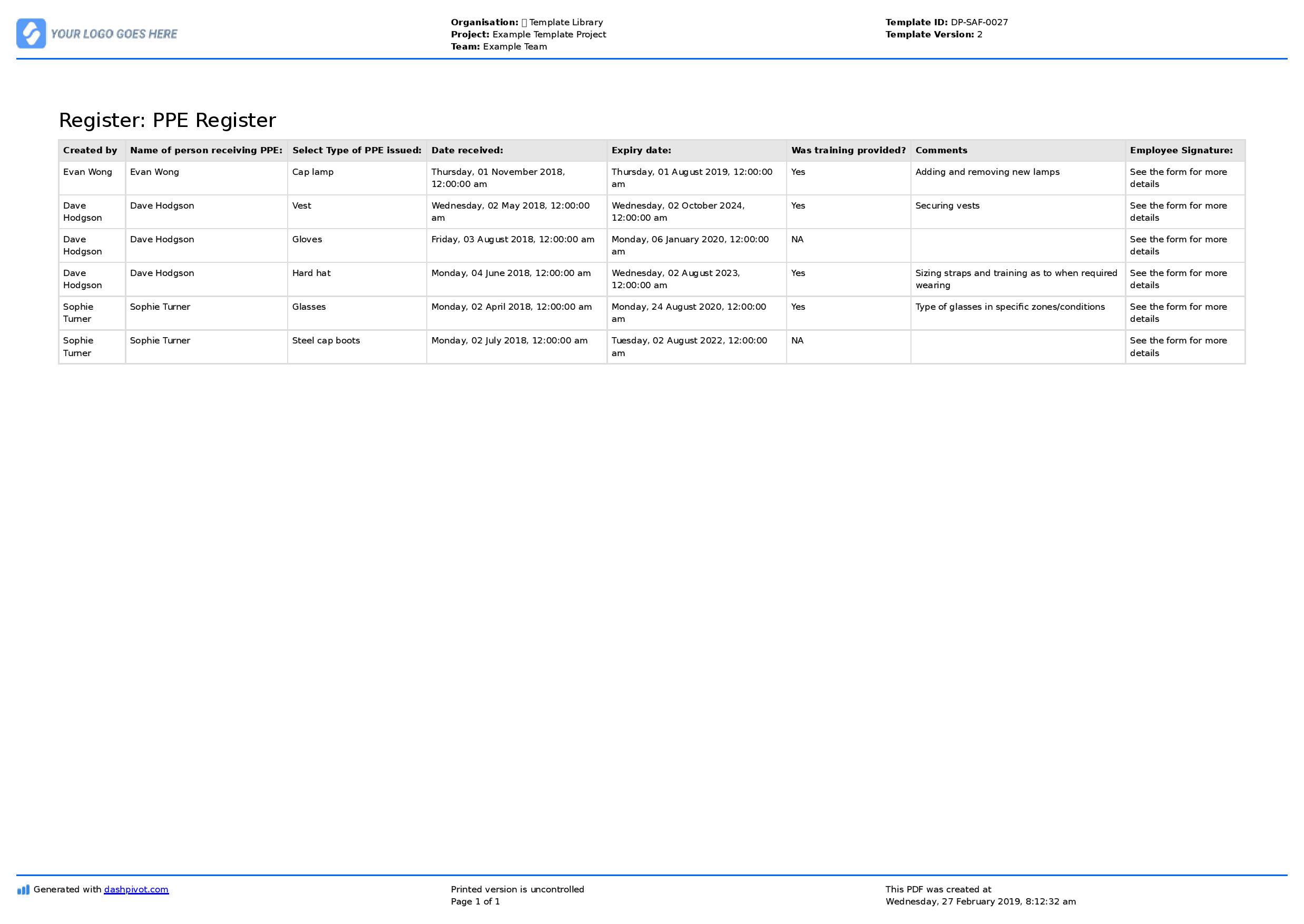
Use this PPE record keeping sheet for free.
Bringing these PPE record keeping best practices together
Even if you have all of the perfect workflows and PPE record keeping forms in place and all of your ducks in a row, there is still some human input required to keep your PPE recored keeping reliable and secure.
Because of this, you need to focus on the mechanics of your communication, collaboration and workflows, but also need to focus on building a culture of safety, whereby people feel obligated and encouraged to follow these best practices.
You can do this by keeping people up-to-date on these PPE record keeping practices, by running safety moment and toolbox talks which enable the company to cover important topics like PPE record keeping (and for people to provide feedback as to why or why not it is working), and by ensuring people know what PPE record keeping is a priority.
Companies lose millions of dollars a year in wasted PPE purchases because of poor PPE record keeping, but more importantly, many companies and people in the world are managing PPE 'blind', because they don't have the tools and mechanisms in place to best manage and organise their PPE records.
Improve your PPE record keeping with some of the free resources below - and you'll be on your way to streamlining your records and your safety outcomes.
People in 80+ countries use this safety management system to improve their safety processes and outcomes.
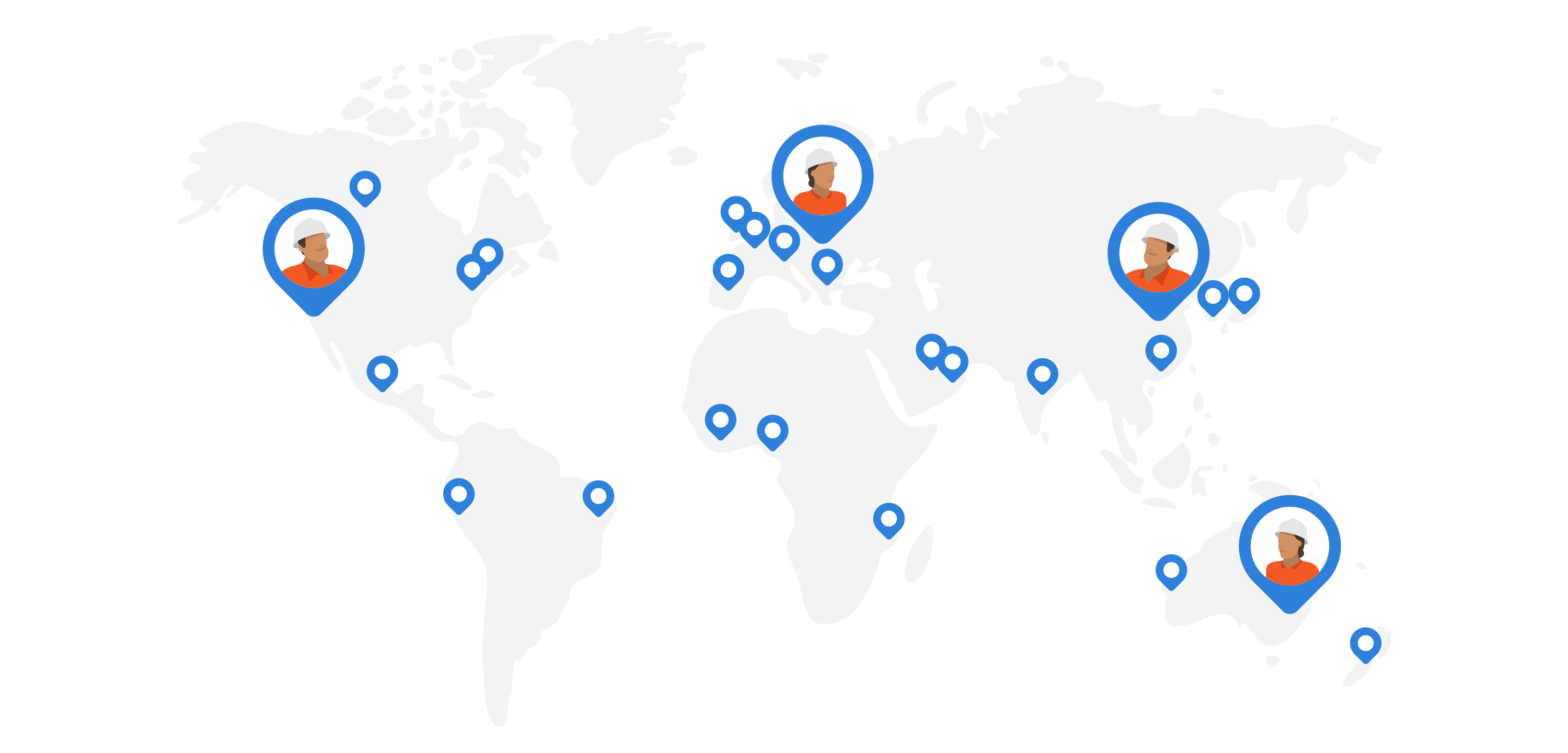