Dashpivot Article – What Are Pinch Points?
What are Pinch Points?
In this article, we will comprehensively answer the "what are pinch points? question, explain their hazards, and provide common examples and best practices to mitigate them in the industry.
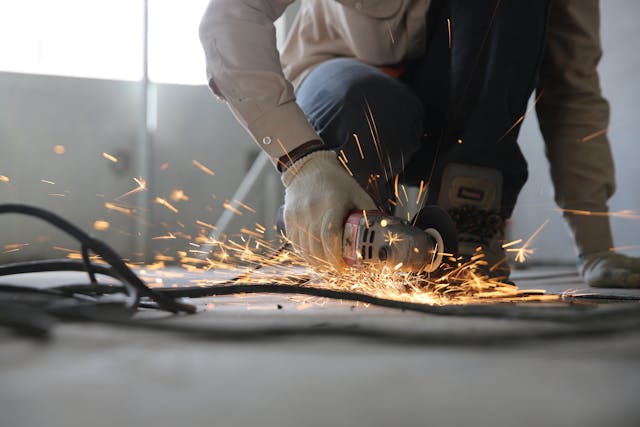
Today, every modern industry uses a multitude of machines. These machines help us achieve projects and quotas by providing a faster and more precise execution of certain tasks. Take this task, for example: a mechanical saw cuts metals faster and more precisely compared to a person. Furthermore, the mechanical saw doesn’t feel any strain or exhaustion when cutting metal pieces, unlike humans, who need to rest every now and then. Given that, we can say that machines have truly restructured the industry to have more efficient processes.
However, these machines have a hidden danger. They contain hazards that companies need to identify to implement appropriate measures to safeguard workers from them. One common hazard that workers face is pinch points. A pinch point is any location where a person or a portion of their body might get trapped between two objects. Pinch points are common in machines, since most of them contain moving parts that have the potential for a person to get caught in. It is important that these are seen so that appropriate measures can be provided.
Pinch Point Hazards
In this section, we will discover what situations lead to pinch point hazards. This will also provide you with a guide to structure your safety measures around pinch points, since this will provide scenarios that could help you plan on how to prevent it.
Pinch Point Hazard - Unguarded Machines
Machine manufacturers often already provide machine guarding on the pinch points found in their product. However, there are instances where maintenance activities remove these guards and fail to put them back after the activity concludes. These situations significantly increase the risk of pinch point injuries. Machine guards are designed to prevent anything from getting caught in the rotating, reciprocating, and oscillating mechanisms of the machine, which are the parts that are likely to have pinch points. Without the guard, human body parts, clothes, and accessories can easily get into contact with the moving parts and cause injury. To make sure that these machine guards are always present, make sure to include them on your equipment inspection forms.
Untrained Personnel
To operate machines, workers need to undergo training to understand how the machine works, to get to know the procedures in operating it, and to know the dangers of the equipment. Training is necessary to ensure a smooth and safe operation of the machine. Untrained personnel operating a machine could pose numerous potential dangers. They may take shortcuts, potentially missing an important safety step that could lead to accidents and injuries. To avoid this, the training should introduce a safe work method statement on the procedures on how to operate the machine to avoid and control hazards, like pinch points.
Loose clothing and jewelry
Loose clothing and jewelry should not be worn when working with machines. The machine's moving parts and pinch points can easily trap these objects, potentially leading to dangerous and fatal situations. Aside from loose clothing and jewelry, another thing to look out for is PPE. While these things protect us from hazards, there are situations where they can be the cause of accidents. One certain example is working gloves. Working gloves protect the hand from sharp and hot objects, but wearing them while operating a working machine, there is a chance that these gloves could get caught in between the moving parts and injure the worker’s hands.
Small working spaces
Machines should be installed in areas where there is adequate space to move around when the machine is running. Limited working spaces could prove to be dangerous, since workers need to move around while being in close proximity to the machine. Having said that, the chances of getting caught by the pinch points drastically rise. Companies and establishments should take into consideration where machines are installed. Additionally, the working spaces should also be free from obstruction that can limit the working space of the personnel. It should also have enough light ventilation for the operators to have enough visibility around the surroundings of the machine.
Pinch Point Hazard - Inattentiveness
Believe it or not, this is the number one reason for pinch point accidents. Personnel around the machine tend to get complacent and do other activities while the machine is running. When doing these activities, they would often lose their awareness of their proximity to the machine. These situations are dangerous because personnel might accidentally get too close and get caught by the pinch points, leading to injuries and, in some dire cases, fatalities. It is important to understand that when operating machines that are constantly running, full attention is required. If there are other activities that don’t involve the running machine, it is best that they are done at a safe distance from the machine.
Hazard Awareness on Pinch Points
One important safety measure that companies should take advantage of is to provide awareness of hazards in the workplace.
This is a simple yet effective measure that can greatly contribute to maintaining a safe and healthy working environment. There is even a cost-free method for spreading awareness about these hazards. We refer to this method as "toolbox talks.”
Toolbox talks are informal meetings where safety issues, such as workplace safety dangers, are discussed. Additionally, it provides a channel for employees to express and get answers to their safety concerns.
To conduct a successful toolbox talk, a toolbox talk form is necessary. The form assists the meeting presiding officer by outlining the safety topics for discussion. The form also includes a section where the presider can record the raised concerns in the meeting. Compiling these forms also brings enormous benefit to the company. These forms could be used as a resource for process improvement and as a document that could be shown to regulatory bodies as evidence for continuous practice of safety. To know how a toolbox talk form should look, take a look at a good example of the form below.
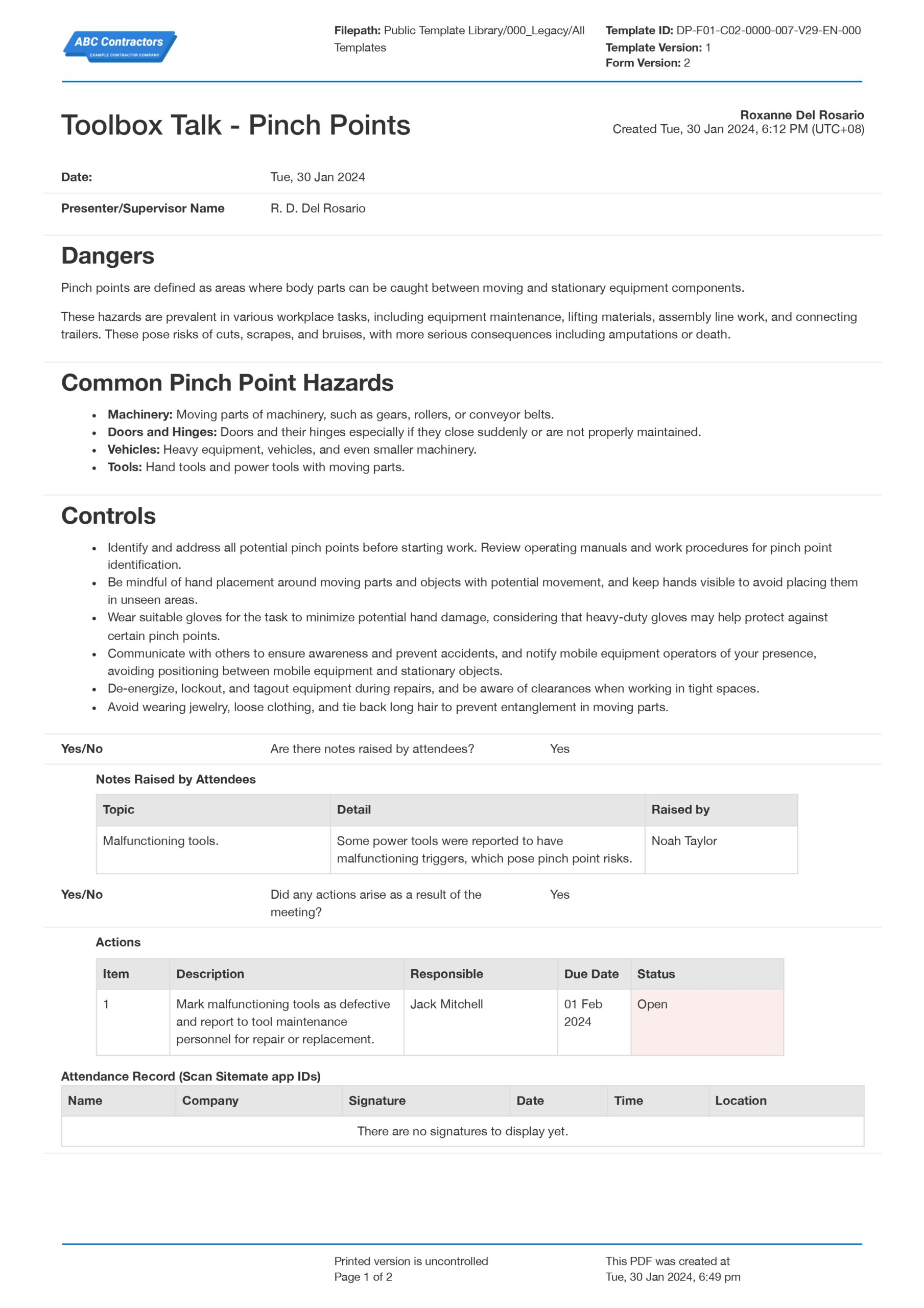
Explain what pinch points are using this doc for free
Examples of Pinch Points
To understand better which machines or parts of the machines contain pinch points, we will provide a few examples to help you paint a picture of what you should set your eyes on when looking for pinch points.
Examples of Gears Pinch Points
Gears are common machine parts. They transmit motion and force from one element of the machine to another and can alter the speed and direction of motion. The process involves gears meshing to accomplish these. Gears are considered pinch points because body parts or objects can get caught in between meshing teeth and can cause injuries like lacerations and bone fractures.
Belt and Pulleys Pinch Point Examples
There are machines that use belts and pulleys to transmit power and rotational motion from the electrical motor to the machine. One common example is the centrifugal pump. During operation, a tight contact zone exists between the belt and the pulley that can potentially trap fingers and clothing. Furthermore, the strong rotating motion adds significant force that could prove difficult to escape when something gets caught. Belts and pulleys are regarded as pinch points for these exact reasons.
Actuators
Actuators are machine elements that convert energy to mechanical motion. There are three common actuators used in the industry. These are electrical, pneumatic, and hydraulic actuators. Industrial machinery, robots, and medical equipment extensively make use of these actuators. Since actuators move between two surfaces, there is a chance that objects and bodies can get caught and get crushed in these machine elements, making them a strong contender for being a pinch point.
Robotic Arms
These days, robotic arms are a common sight in manufacturing industries. They are fast, precise, and efficient when it comes to executing repetitive tasks. Like actual human limbs, these robotic arms have joints that help them move like our arms do and sliders that transfer them into the position they are needed. These joints and sliders are excellent examples of pinch points that companies should provide proper guarding for.
Press Machines
Press machines make use of force to shape or form workpieces into a desired output. These machines are an example of a critical pinch point since the force used to shape objects can be so strong, it can be fatal for a person to get caught in. The working area between the ram and die is a narrow gap that can be ideal for objects or limbs to get caught in. Proper safety precautions are needed when operating press machines.
Forklift Pinch Point Examples
Forklifts are very common in many industries. The workplace uses them to haul and move heavy objects. These powerful vehicles contain several pinch points, which establishments should take note of. Forks and loads, steering and rear-end swing, confined spaces and narrow aisles, mass and fork movement, and cylinders and chain systems are all examples of pinch points found in forklifts.
Conclusion
Any industry may use machines that contain pinch points. However, pinch point hazards may be controlled and provided with the correct safety measures if personnel are aware of them and know where to look for them.
To provide knowledge on this, companies may make use of toolbox talks as avenues to educate their workers about pinch point hazards.
Making use of this method helps companies maintain a safe and healthy workplace.
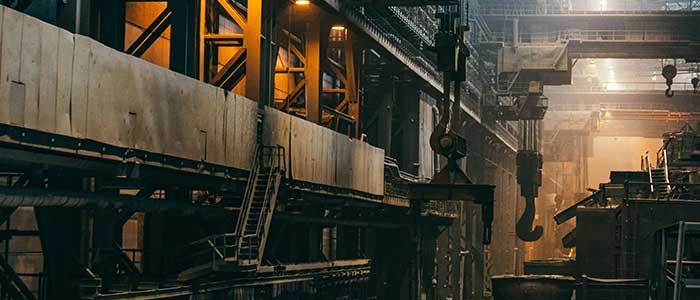
Machine Guarding Checklist template
Easily complete, manage and action your machine guarding checklists using this proven framework.
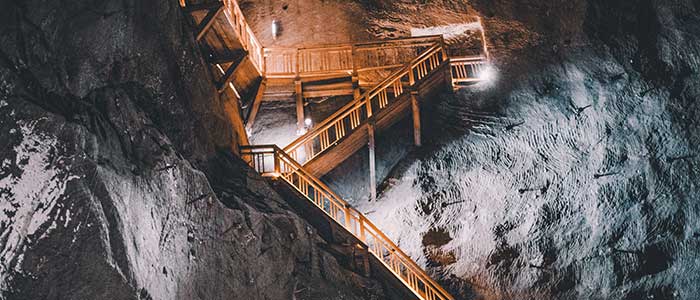
Safety Audit Checklist template
Conduct and manage your safety audits like a pro using a smart digital audit template.
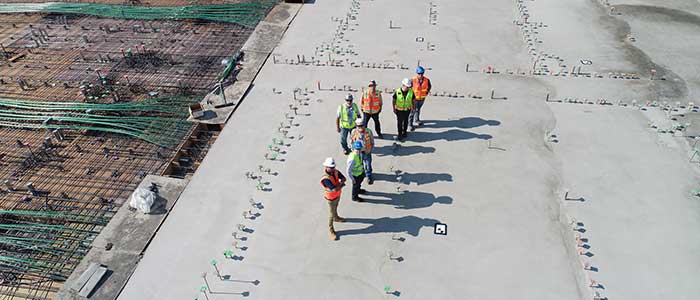
Safety Toolbox Talk template
This toolbox talk template is quick and easy to complete and signoff on site, and keeps all of your toolbox talks neatly organised and professional.