GEARBELT CASE STUDY
Burton Contractors
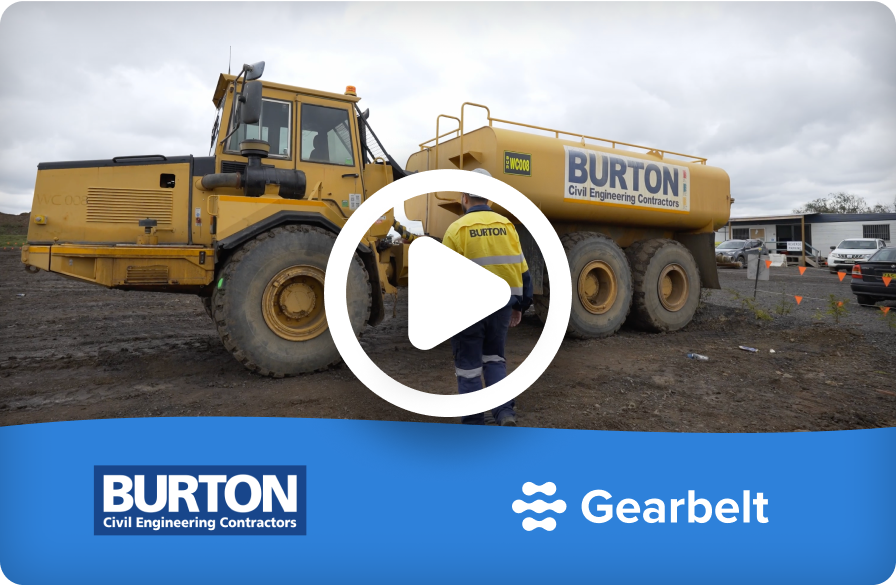
Burton Contractors is a Sydney-based civil contractor company with over 50 years of experience delivering major earthwork, subdivision and infrastructure projects. Their 100-person team operates a diverse fleet of nearly 100 machines, including bulldozers, graders and excavators.
With a strong focus on efficiency and safety, Burtons is committed to continuous improvement across both field and office operations. As long-time users of Sitemate’s Dashpivot platform for field reporting, Burtons further streamlined their systems by transforming their fleet management processes with Gearbelt.
Customer:
Burton Contractors
Industry:
Infrastructure
Sitemate platform/s used:
Case study focus:
Daily plant inspections, maintenance schedule, work orders and more
Or book a quick call for more info
Key improvements for Burtons by using Gearbelt
Automate fleet management process
Burtons previously used a mix of Excel spreadsheets and project management systems to track their plant and equipment. This manual method required them to move information across different systems and made it difficult to stay on top of servicing, inspections and fault reporting, often resulting in reactive maintenance and excessive admin time.
Glenn, Plant Manager, described how time-consuming the process had become:
“We used to use manual methods to capture the fleet… I was spending four to five hours per week on just moving information.”
With Gearbelt adoption, Burtons consolidated and automated their entire plant inspection and maintenance workflow. What used to require multiple systems and manual data entry is now done directly on-site through simple inspections and forms.
“This automated asset management program has reduced my admin time by a good 80%.”
Real-time visibility
With a large and valuable fleet, one of the biggest risks for Burtons was unplanned downtime due to missed servicing or undetected faults. Under their old methods, issues were sometimes communicated too late or missed entirely leading to costly delays on site.
Gearbelt transformed this by capturing real-time data directly from operators during daily inspections. Faults are now automatically logged and sent to the right person instantly, making sure no issue slips through the cracks and everyone involved stays informed.
Automated fleet system for built world companies
Eliminate manual fleet management and clunky apps with Gearbelt Assets Cloud.
Paul, Managing Director, explained how the visibility across teams has improved:
“Everyone knows what needs to be fixed and when. We can prepare the day better because faults are logged and sent to the right person in real-time.”
With data captured, the team can now act proactively, moving away from reactive maintenance which improves service scheduling.
Nathan, Maintenance Support Officer, highlighted the change:
“Before Gearbelt, it was impossible to do preventative maintenance. Now I can track servicing and maintenance easier and it saves me one to two days of admin work a month.”
This connected workflow ensures everyone involved stays aligned, preventing miscommunication and unplanned downtime.
Seamless integration with existing systems
Because Burtons was already using Dashpivot for field documentation across all their projects, Gearbelt integrated seamlessly into their existing ecosystem. The rollout was smooth, with minimal onboarding required for operators and teams on site with intuitive and familiar user interfaces.
Easily streamline any HSEQ or field reporting process
Replace manual paperwork, messy spreadsheets and clunky apps with streamlined digital workflows.
Bella, Application Systems Officer, explained:
“Like Sitemate’s other products, Gearbelt was very easy to implement from a systems perspective… we can customise it ourselves to suit our requirements.”
Burtons now use all three of Sitemate’s products, Gearbelt for fleet management; Dashpivot for QSE; and Flowsite for automation and integration. This allowed Burtons to build a unified and integrated system for their daily operations, all without writing code or relying on external developers.
“As an application systems officer, I’d recommend Sitemate’s software tools to anyone looking to improve their systems in these industries.”
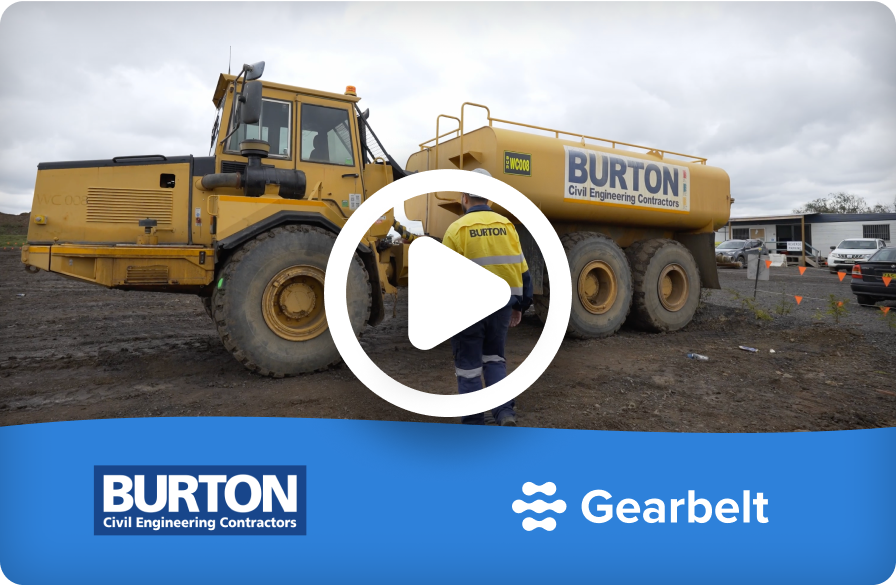