Dashpivot Article – Crane Safety Requirements
Crane Safety Requirements
Let's walk you through the most critical crane safety requirements so you can feel comfortable knowing your company level safety compliance, and knowing your team is across these requirements.
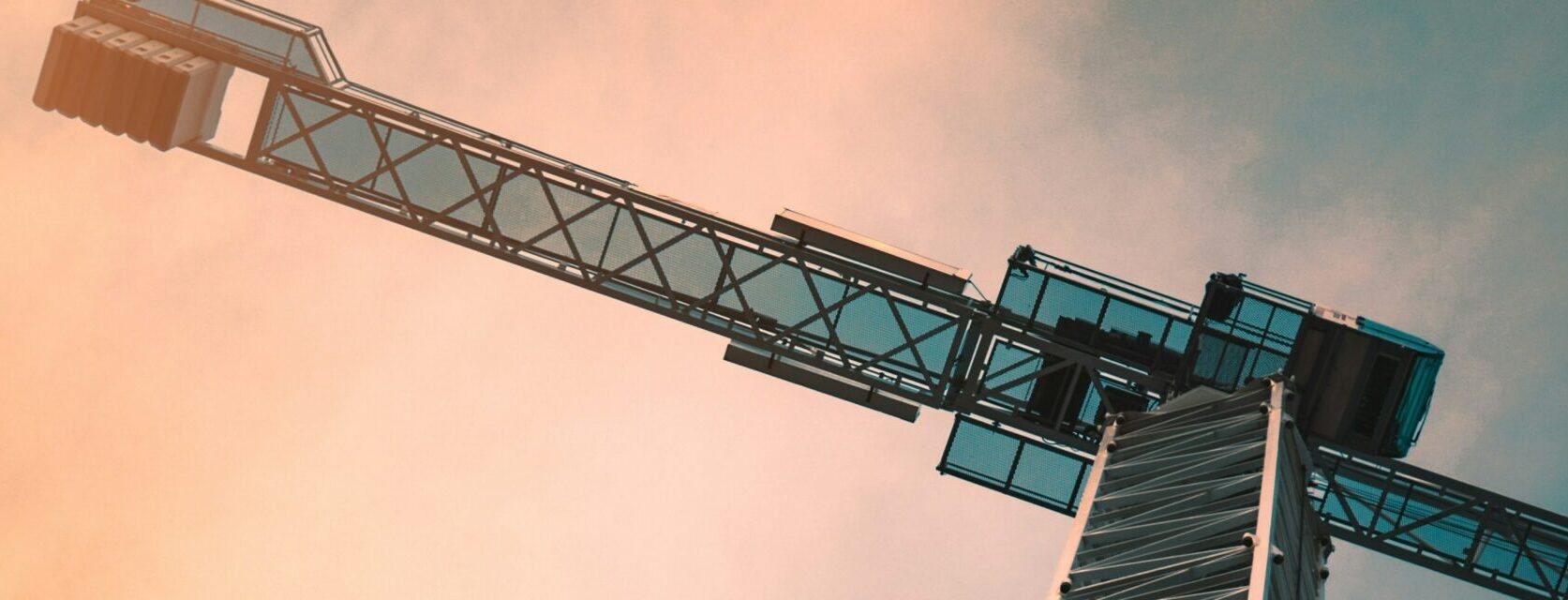
Crane Safety in Construction
Cranes are common on construction sites. These gadgets lift and lower construction materials and heavy goods. Construction sites employ a variety of cranes. Vehicle-mounted, transportable, and tower cranes are most common. However, despite their huge help on the field, cranes often present hazards that could potentially injure or take somebody’s life.
Having said that, establishing crane safety in construction is a priority for maintaining a healthy and safe workplace. To ensure crane safety on construction sites, businesses should first identify and learn about the hazards. Identifying and learning about these hazards is important for implementing appropriate measures to eliminate them.
It is also important to have all your workers be aware and knowledgeable about the hazards so that they can know when, where, and how to establish the measures that are going to be provided.
Crane Safety Requirements
Cranes are known to pose risks, and we need to take action to eliminate these risks. One of the measures that companies and establishments can take is to provide safety requirements before, during, and after operating the crane. These requirements will make sure that whenever a crane is used, safety is always established. Here are some requirements that you could adopt in your crane operations.
Crane Safety Requirements Before Operating the Crane
Choosing the Right Crane: As previously mentioned , cranes have different variants. Each of them has a specific purpose and use. One must consider the load characteristics, lift height and radius, site conditions, and lift duration when selecting the appropriate crane. We must seriously consider all these factors, as selecting the appropriate crane is crucial for ensuring safety. Choosing the wrong crane might lead to situations like crane failure, which could prove dangerous for everyone working around the crane.
Choosing the right person: In construction, there are usually three people involved in operating the crane. They are the operator, the rigger, and the signal person. These 3 required personnel should not be just anyone you could pick out in the field. Personnel with training and certification should perform the roles of the operator, rigger, and signal person. These certifications are required by regulations to protect the workers working around the crane and the other properties.
Crane Inspection: Before operating, the crane must be pre inspected to ensure it is the right one for the job and is working properly. Crane inspections are preventive maintenance procedures that thoroughly evaluate the parts of the crane and see if they are working optimally. The majority of the crane's inspected parts are those that significantly impact its functioning. These inspections are important to help identify issues that might lead to malfunction, which can be a dangerous situation in the construction site.
Providing the Safety-Related Documents: This action is an administrative step needed to make sure that everything is ready for the safe operation of the crane. These documents provide proof that regulatory safety steps were done and proper planning was conducted. These are usually the documents needed to be present and approved before operating the crane.
- Lift Plan
- Risk Assessment
- Task Hazard Analysis
- Operator, Rigger, and Signal Person Certification
- Crane Inspection
- Permits
- Emergency Action Plan
During the Operation of the Crane
Following Safety Procedures: The establishment of safety protocols is obligatory for businesses whenever there is a machine operation involved. These protocols, acting as guidelines, will govern the successful functioning of a specific piece of equipment. It is essential that these safety procedures integrate all of the appropriate safety measures in order to ensure that the equipment is operated safely.
Understand the Radius of the Load: The load of the items being transported from one location to another determines the crane's radius. Recognizing load limitations and adhering to safety SOPs and procedures can simplify the use of cranes for steering, carrying, and extending a material load. Crane operators and riggers must be well informed on how to maneuver a large load in both restricted and open areas. Although cranes have different lifting capabilities, controlling the weight and load dimension is still essential while the operation is underway.
Clear Communication: We established that more than one person is required to operate the crane. Clear communication must always exist between these people. One of the important steps in establishing clear communication is to have roles clearly defined. This will ensure that everyone understands their responsibilities and removes any misunderstandings during the crane operation. With this, the activity involving the crane will proceed safely and smoothly without delay.
Crane Safety Requirements After Operating the Crane
Post-Operation Inspection: The purpose of post-operation inspections is to determine whether or not the crane has been damaged or if there are any issues that have arisen after it has been used. It is expected that this inspection will swiftly offer the appropriate maintenance in the event that any discoveries have been made during the examination. By taking prompt action to address the concerns, it prevents them from developing into more significant problems and prevents the crane from being put into operation.
Housekeeping: Any construction site needs excellent housekeeping. It means keeping a clean and tidy workspace and storing equipment and supplies correctly. Good housekeeping improves safety and many other aspects of a building project. One example of a successful housekeeping method is the 5S. 5S is a workplace organization strategy, which is based on a Japanese quality management idea, to create a neat and orderly workspace. It gives a methodical approach to maintaining proper housekeeping as well as chances for ongoing development and increased output.
A Talk About Crane Safety Requirements
To contribute to creating a safety culture surrounding using cranes on construction sites, all employees must be aware of the crane safety requirements.
In order to accomplish this goal, a toolbox talk on crane safety would be a great setting for holding such meetings to educate employees on crane safety requirements .
This discussion is a casual gathering that focuses on safety procedures and provides a platform for individuals to voice their concerns.
Creating a toolbox talk form is the first step towards doing toolbox talks more successfully. This form clearly outlines the safety subject and includes fields for noting any issues raised during the discussion. You can use these issues to enhance safety and make crane operations more secure. See the following example of a well-designed toolbox talk form to get an idea of how the form should look.
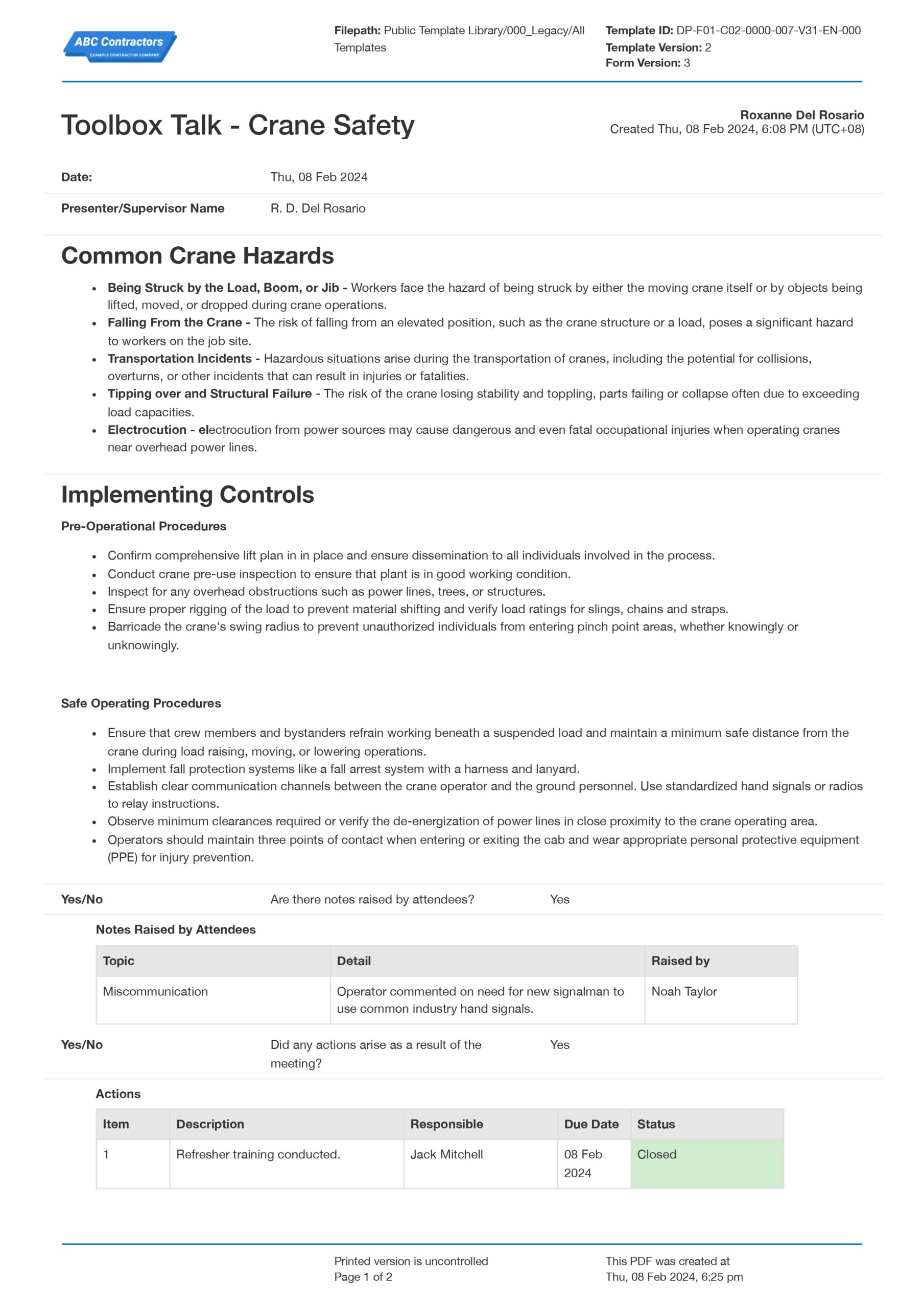
Strengthen crane safety protocols on site with this crane safety toolbox talk template
Crane Safety Hazards
Dropping Loads
One of the most prevalent and potentially hazardous risks that might occur while working with overhead cranes is the possibility of falling loads. A falling load has the potential to cause a severe amount of structural damage to structures and property, as well as several injuries and even deaths.
Overloading
Someone overloading a crane is the cause of the vast majority of structural failures and incidents that occur in cranes. Exceeding a crane's operating capacity will likely cause irreparable structural damage. This is also one of the primary reasons for the first hazard that was mentioned. Overloading has a high potential to snap cables, which causes the loads to fall.
Non-certified personnel operating the crane
Without the proper knowledge and skills, non-certified personnel pose a threat to the health and safety of everyone in the event that they were to operate the crane. Crane. Crane operation requires intricate understanding of the load to be lifted to properly rig it and transfer it to the correct position. Without this understanding, a lot of dangerous possibilities could happen. The crane might tip over, the loads might fall, cranes might crash with one another, and mechanical failure could occur.
Electrical hazards
Most modern cranes now operate with computer automation. This means that there will be more electrical components in the crane. Having said that, the risk for electrocution also becomes more prevalent. Another electrical hazard that cranes are exposed to is power lines. These live lines can get in contact with the boom, and electricity can travel from the line towards the entirety of the crane. When a person is inside the crane or touching the crane, they can get electrocuted.
Poor Ground Conditions
Ground conditions play a giant role in keeping mobile cranes stable. When ground conditions are not solid or even, these factors can cause the crane to tip over, especially when loads are lifted. When operating mobile cranes, ground conditions must be included in the pre-operation checklist to ensure a safe operation of mobile cranes.
Crane Safety Requirements Summary
One of the most crucial pieces of equipment in construction is the crane. However, there are risks associated with this equipment that might harm both employees and business property. Safety precautions must be taken in order to eliminate these risks. Understanding the safety requirements before , during, and after crane operation is one of the best ways to reduce risks.
These specifications are in place to guarantee that the proper crane is being utilized, that the appropriate personnel are operating the crane, that safety documentation is available, and that the required protocols are constantly followed.
These crane safety requirements will provide a safe, healthy, and contented workplace by enforcing a commitment to safety.
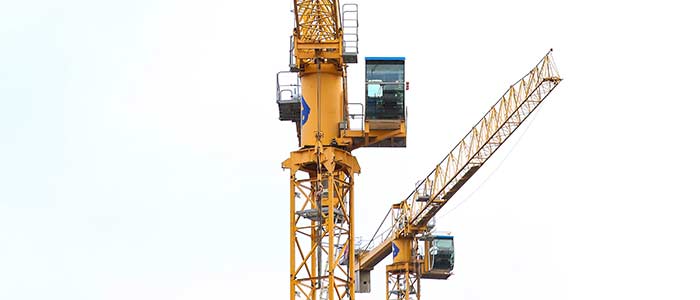
Daily Lift Plan for Cranes template
Get your daily lifts planned approved, and keep everyone and everything safe.

Safe Work Method Statement for Cranes template
Cranes are powerful and incredibly valuable pieces of kit on construction and industrial sites. Make sure you take care of them and your people properly.
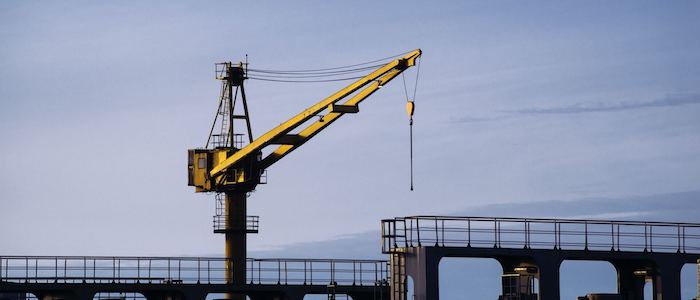
Crane Job Hazard Analysis template
Keep crane work safe with this digital Crane Job Hazard Analysis template.