Article Page – Reactive Maintenance Meaning
Reactive Maintenance Meaning
Here's an all you-need-to-know guide about reactive maintenance - its purpose, process, type, examples, disadvantages and strategies to make it work for you.
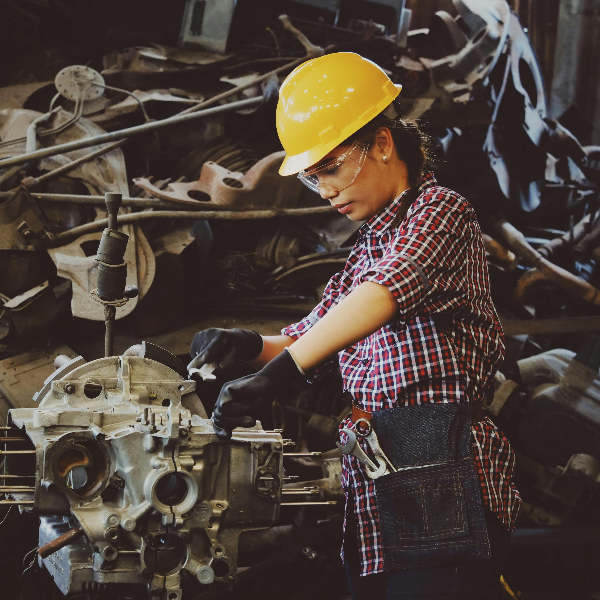
Reactive Maintenance: Definition and Purpose
In the logistics and trucking industry, for the business to flourish and continue, apart from getting customers and serving clients, you also need to make sure goods are delivered complete and on time. A lot of unexpected things can happen in a day’s work. While you can avoid starting the route with a flat tire or having breakdowns, a breakdown can still happen on the road. And this is where reactive maintenance comes in—it’s literally how you respond to a breakdown.
Vehicle maintenance is necessary for the business continuity of a fleet. Maintenance extends the life of the vehicles, keeps passengers and goods safe, and restores the vehicle to a good working condition.
Reactive maintenance, sometimes called corrective maintenance or breakdown maintenance by definition is the process of performing repairs after the vehicle fails or breaks down rather than proactively preventing vehicle issues.
The operation’s purpose is to ensure that it can repair the vehicle back to its operational state after a failure. While this should not be an ideal setup because, arguably, it lacks foresight and can potentially increase the downtime and repair cost, reactive maintenance is still in practice to this day, especially in situations where vehicle issues were not detected during routine inspections.
In some cases, reactive maintenance is practiced because it lacks proper fleet maintenance scheduling and the operations just functions reactively and this can be due to poor fleet management, limited resources or a lack of initiative.
In this article, we’ll do a thorough walk-through of reactive maintenance in a fleet, its purpose, and how it is done, covering as well as the types, examples, and the disadvantages of reactive maintenance, and finally, some strategies on how to effectively utilize reactive maintenance.
Reactive Maintenance Example
Reactive maintenance occurs when an unexpected breakdown happens or when a fault is discovered during relevant inspections. This is considered “fix-on-failure” approach because the timing is exactly after a failure. Despite its nature, a well-managed fleet would still make sure, the process is structured, and that quality is still maintained.
To get a good grasp on how reactive maintenance works, let’s look at an example work scenario:
A delivery van on a fleet during a route had a flat tire, the first step should be, pulling over and securing the van by parking nearby. Next is communicating the incident to the dispatcher or fleet manager to generate a work order and this is done by either a quick phone call or remote incident reporting to log the reactive maintenance performed.
Now, depending on how well-trained and experienced the driver is, if the driver can perform the replacement or repair of a new tire then the next step would be conducting visual damage inspection, and checking for puncture, blowout or sidewall damage. If the driver is unable to perform this then a technician or roadside contractor assigned by the fleet manager should be dispatched to perform this.
After the necessary repair has been performed, part of the reactive maintenance task is to inspect the installation or repair, confirming air pressure and no other interference and finally documenting the repair. This whole process ensures accountability, safety, and continuous improvement in fleet maintenance operations.
Reactive Maintenance Documentation: Importance and Example
A reactive maintenance document or form should have all the necessary details to document the incident that occurred. It is a record of the cause of the incident, the correction done, the date and time it happened, and who performed the reactive maintenance.
Decreasing breakdowns in the fleet
This document is important because it will be part of root cause analysis and additional data to consider when planning proactive or predictive maintenance—for example, identifying recurring component failures or scheduling parts replacements before breakdowns occur. While breakdowns are unexpected if there is a significant pattern or observed trend of repeated issues then the documentation is going to be a very valuable tool.
Downtime reduction
One important aspect in reactive maintenance documentation is the downtime consideration. If the breakdown is inevitable, calculating the time it took to repair, including the time it took for help to arrive, will be a means to improve the process of reactive maintenance should it happen again, thereby improving the delivery schedule and decreasing breakdowns in the fleet through better planning and faster response strategies.
Legal or Regulatory Compliance
As far as it’s applicable having a good record of fleet maintenance document addressing vehicle issues promotes accountability and will be advantageous in legal or regulatory compliance. Regardless of whether the maintenance is reactive, the document will serve as the recorded intervention by the company to ensure safety and compliance.
Tracking repair cost
Reactive maintenance documentation is also necessary to track the repair cost, which is crucial for calculating the cash flow of expenses in a company and for gaining a better focus on cost reduction efforts—such as when identifying high-cost repairs that could have been avoided with earlier detection or when deciding to replace frequently failing components with more durable alternatives.
Improve Parts Sourcing and Inventory
Parts sourcing and inventory management benefit from proper incident or maintenance documentation, as it details the parts replaced in a vehicle during repairs. Similar to tracking repair costs, documentation helps monitor which parts are frequently replaced or repaired. Take flat tires, for example—while still an unpredictable breakdown, it's good practice to always carry a reliable spare and ensure the inventory is well-prepared for such recurring issues.
Reactive Maintenance Meaning in the documentation
Here is an example of reactive maintenance document to get you started as a basis in documenting maintenance after a breakdown.
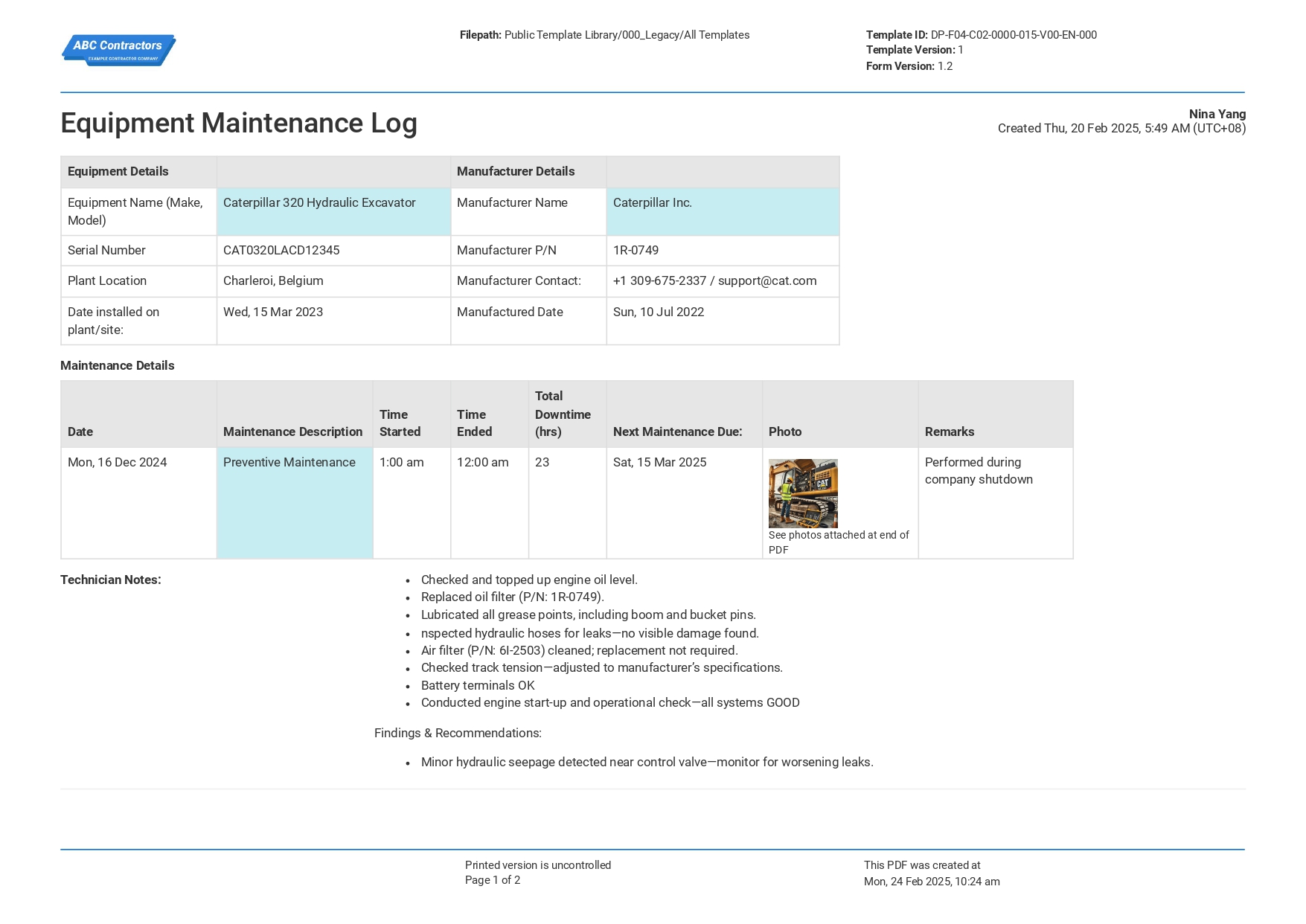
Use this free Reactive Maintenance document structure
What are the types of Reactive Maintenance?
Reactive maintenance is conducted without prior planning, and its maintenance performed in response to an issue encountered by the vehicle. For instance, a container truck may suddenly break down due to a failed alternator, requiring immediate repairs to restore functionality and get back on route.
Its urgency is the reason why it’s called reactive maintenance, which generally falls into two types– emergency maintenance and corrective maintenance that differs according to the timing of which the fault was discovered.
Emergency maintenance
Emergency maintenance is conducted in response to urgent safety issues that need to be dealt with, such as a flat tire or a dead battery while on the road. This can also easily escalate into a breakdown, which is basically when the vehicle or the equipment cannot be used but is still repairable. This maintenance causes serious downtimes and can be a huge hassle to daily work activities.
Emergency maintenance and responses in fleet management should be designed to cover all possible emergency situations that can happen in a vehicle because when accidents happen you cannot choose which one would hit you.
Unpreparedness can worsen into dangerous and costly situations that can put both the people and the operations at risk. Emergency issues in a vehicle can be catastrophic such as the real-life incident in Cleveland, United States when a school bus with 15 students bursts into flames during morning route.
Corrective Maintenance
Corrective maintenance is a reactive maintenance that is conducted when a fault is discovered in the equipment or vehicle before an incident has occurred. At times the fault is discovered after a routine inspection and correction is done to repair the fault either by replacing the faulty component or by performing necessary repairs to restore functionality. This makes this more advantageous to the company because the effects are not as severe than when the fault is discovered after the vehicle has already stalled.
Corrective maintenance also involves diagnostics and inspection, meaning that it doesn’t only correct the malfunction but should also identify its root cause to figure out if there are even more serious issues that can potentially lead to breakdowns such as a worn-out bearing that could damage the motor if left unchecked.
Corrective vs reactive maintenance
Corrective and reactive maintenance are often associated with each other and are sometimes interchangeably used. In essence, they are the same such that they are maintenance performed when a fault is discovered, but reactive maintenance covers a broader picture like responding to unexpected failures on the road, managing emergency repairs, and addressing issues that arise without prior planning.
Emergency or breakdown maintenance and corrective maintenance are both types of reactive maintenance. Both involved repair that is done after a failure is detected.
What are the disadvantages of reactive maintenance?
Vehicle restoration after failure detection is necessary in fleet maintenance especially in the event of a breakdown in the middle of work but as much as possible because of its known disadvantages the fleet manager usually aim to avoid relying on reactive maintenance methods and focus more on proactive maintenance improvement efforts because it minimizes downtimes, reduces costs, and prevents major issues before it escalates.
The leading disadvantages of reactive maintenance in fleet management are:
1. It incurs high uncontrollable costs
2. It is time-consuming
3. It reduces vehicle lifespan
4. It increases safety risks
Let’s go through each of them and look at them in detail to gain better insight as to why reactively responding to failures instead of proactively manage them within the fleet is disadvantageous to a company.
High uncontrollable costs
Due to its unpredictability reactive maintenance can cause high uncontrollable costs both in direct and indirect expenses. Direct, as in from actual repairs, and indirect costs are related to operational disruption, as they can cause loss of revenue and reduced productivity, missed deadlines, potential penalties, and even safety risks.
It is challenging to plan accurately for the fleet when frequent breakdown occurs on vehicles due to differing reasons that were not detected prior. The parts that failed may not be readily available and this can lead to added spare parts and higher expenses due to the rush procurement of needed component. Ultimately, it will all depend on the situation, which is unfortunately unpredictable.
Time-consuming
Reactive maintenance takes more time than routine maintenance, even though it aims to be finished as quickly as possible–especially for an emergency repair. However, many factors can still trigger it to be more time-consuming such as the time required to figure out the issue, delays due to the sourcing of spare parts, and the potential travel time for the designated technician to reach the vehicle’s location wherever it broke down or the time it took for the vehicle to be transported to the repair shop.
One of the effects of a time-consuming maintenance in the event of a breakdown is that this delays the service the vehicles a fleet business is offering, which can escalate to unrealized earnings in a day or a week. This is crucial for fleets whose business revenue relies on strict deadlines and vehicle readiness such as logistics, delivery services and public transportation.
Reduced vehicle lifespan
With frequent use it is inevitable for a vehicle’s lifespan to deteriorate, however frequent reactive maintenance can speed that up. When reactive maintenance is performed to an equipment, the goal is just to make it work or run again not necessarily to have the system to be in it’s ideal or optimal condition since the trigger of this type of maintenance doesn’t call for much time to perform such modifications.
In many cases, reactive maintenance is carried out without a comprehensive assessment, leaving the root cause undetected. Even when routine inspections are conducted, underlying issues may remain unclear and overlooked causing breakdowns to recur and the vehicle’s condition to gradually worsen and not reach its ideal economic life.
Safety Risks
Frequently responding to fleet asset failures reactively instead of proactively can lead to increasing safety risks, especially for the passengers. It’s like a domino effect of constantly neglecting quality maintenance. When you allow the vehicle to degrade, you subject the driver and the passengers to unsafe working conditions, endangering their lives and subjecting the company to potential liability and major losses, both financially and reputationally.
These disadvantages are the main reasons why fleet managers tend to steer away from reactive maintenance. However, it is still necessary—especially in the event of a breakdown or emergency issues. So, how do you maintain the quality of your management and hit your fleet maintenance KPIs even while having to perform reactive maintenance?
Making the Meaning of Reactive Maintenance Work for You
Reactive maintenance has built-in challenges that are disadvantageous for fleet operations. Still, instead of dismissing it, it can’t be denied that reactive maintenance needs to happen, as it effectively addresses vehicle issues as they arise. It is an immediate response, simple in nature, that—when done right and efficiently—gets the job done and helps your vehicle get back up and running to complete your operational obligations. Therefore, what are we going to do is to provide a few important strategies that we need to work on to manage reactive maintenance to make it work for you.
Take advantage of reactive maintenance records by utilizing an app
We’ve addressed in this article the importance of reactive maintenance documentation in decreasing breakdowns and reducing downtime. However, it’s also worth noting that you can handle documentation to make it more results-oriented by investing in fleet maintenance software like Gearbelt and applications that enable you to track repairs as they happen, monitor vehicle history, schedule the next maintenance or overhaul, and generate reports—all in one centralized system.
Perform follow up inspection or “aftercare”
There’s often a tendency to approach fleet maintenance reactively when there’s no appropriate follow-up inspection after emergency maintenance, driven by the mindset of, “The issue was fixed already—why dwell on it again?” and it’s right to ask this because it does take an additional time but if you were to lessen reactive maintenance you must monitor why it keeps happening, and you can only do this by performing follow up inspection.
It’s an aftercare approach that quality checks the repairs made, with the goal of avoiding the issue from happening again.
Follow up inspections can be done by attentively looking into the records: what repairs were done and how effective it was, see if there are any patterns of issues and trace the root cause of the breakdown. In this way, the reactive maintenance efforts will be useful in fleet management.
Schedule corrective maintenance
Although corrective maintenance is done as soon as the issue was discovered, in cases where the issue is not critical like minor fluid leaks or worn-out wipers, implement scheduling corrections before a truck goes to long runs and note it for the visibility of the drivers. Ideally, a fleet must aim to address all issues of a vehicle as soon as it’s discovered but scheduling corrective maintenance allows for good time allocation for diagnosis and correction.
This practice transforms corrective maintenance into a predictive maintenance because it predicts when maintenance is likely to fail but also in the case of failing equipment components, you make sure you reach to the end of its economic life before you replace it–this is also cost-effective.
Reactive Maintenance Meaning Conclusion
Reactive maintenance is a procedure that is in fire-fighting mode, but it still gets the job done when you need it to. With proper documentation, the right mindset, and efficient aftercare you can transform reactive maintenance work into a good strategy for the improvement of your fleet maintenance.
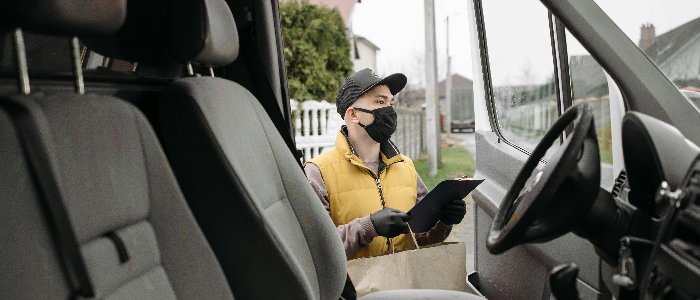
Fleet inspection
Conduct streamlined and organised vehicle fleet inspections.
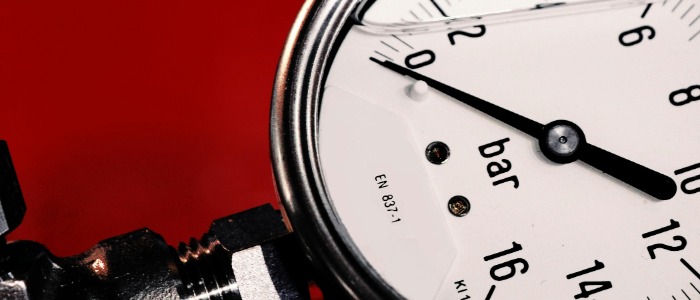
Equipment calibration
Document, monitor and schedule calibrations using this form and register template.
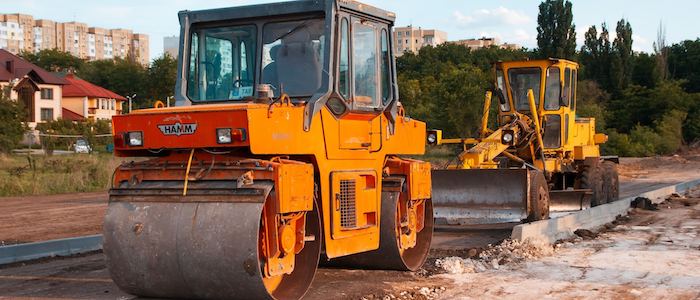
Equipment maintenance log
Improve how you log, track and conduct maintenance on your equipment.