Dashpivot Article – Fire Sprinkler Inspection Requirements
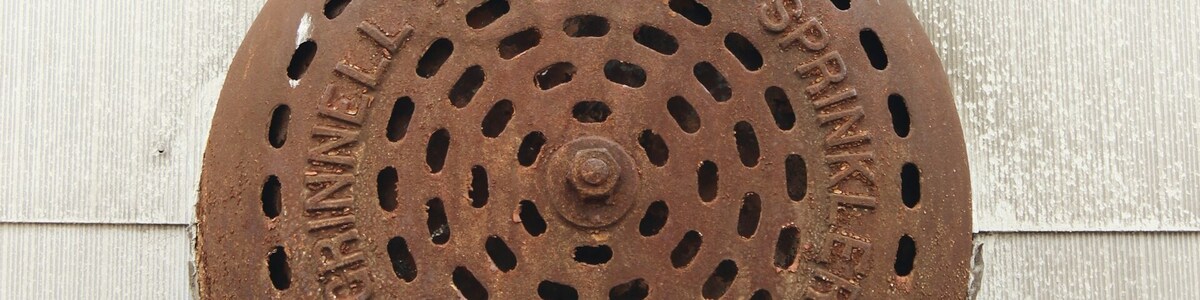
Fire Sprinkler Inspection Requirements
What are Fire Sprinkler Systems?
Fire sprinkler systems are both a fire suppression system and a fire detection system. They are installed in residential, commercial, and industrial settings as part of the fire protection system in buildings. Fire sprinklers slow down the fire and smoke, thus providing individuals inside the building more time to escape. Because of their critical importance, there are strict fire sprinkler inspection requirements and legislation you need to be aware of.
Fire sprinklers are designed to be interconnected by pipes and are placed strategically on ceilings and walls. The temperature of the fire will cause the sprinkler to activate. Having said that, it is important to note that only heat will activate the sprinkler. Smoke and smoke alarms neither trigger the activation of a sprinkler. Furthermore, fire sprinkler heads activate individually. Only sprinklers near the heat will activate.
What is the Importance of Fire Sprinkler Inspection Requirements?
Fire sprinklers are vital to a building's fire protection system. Like what was formerly said in the previous paragraph, they function both as a fire suppression system and a fire detection system. Fire sprinklers are fast when they activate, which controls or extinguishes a fire before they spread. Having a mechanism that only activates near heat, a fire sprinkler system can be used to locate fires inside a building, which makes it a great fire detection system. All of these are for the purpose of reducing the risk of injury or death by controlling the heat and smoke whenever a fire occurs. Having said that, it is essential to keep fire sprinklers in optimum condition to preserve lives and assets. The best way to do this is to conduct and inspection based on the NFPA requirements.
Who Established the Fire Sprinkler Inspection Requirements?
The National Fire Protection Association, commonly known as the NFPA, established the fire sprinkler inspection requirements through their established and world-accepted standards in NFPA 25. The NFPA was founded in 1986 and became a leading authority on fire, electrical, and building safety. Its mission is to reduce the impact of fire and other related hazards globally, and the organisation's goal is to reduce the number of deaths, injuries, and property damage caused by fire and other hazards. Developing and publishing fire safety codes and standards is one of the NFPA's most significant responsibilities. These standards and codes offer guidelines for the design, construction, and maintenance of buildings and other structures, as well as for the use of life safety and fire protection equipment. They are widely embraced by state and local governments, as well as private sector organisations, and are frequently the foundation for building codes and regulations.
This is just one of the fire safety regulations that organisations and companies should take note of to maintain a healthy and safe work environment. To have a broader perspective about other fire regulations, take a look at: OSHA Fire Safety Regulations
Fire Sprinkler Inspection Frequency Requirements
Frequent inspections are required to be carried out in order to guarantee that the fire sprinkler system will continue to function normally. This will ensure that the sprinkler system is operating at its highest level of efficiency and will guarantee the system's dependability. Having a fire suppression system that is well maintained reduces the risk of harm to both people and property. In this section, we will demonstrate what the National Fire Protection Association requires at specific intervals.
Weekly Fire Sprinkler Inspection Requirements
In accordance with NFPA 25, this inspection takes place once per week within the calendar. Because of this, it is necessary to make arrangements for the components to be inspected once per week. In addition to the foregoing, the NFPA suggests that the following things be examined at least once each week: Control valves, backflow preventers, and the pump house.
Monthly
As per NFPA 25, monthly inspection is detailed as occurring once per calendar month. This means that scheduled inspections should be held at least once per month. The following items that NFPA recommends to be checked at least once per month are gauges and dry pipe valve exteriors.
Quarterly
As stated by the National Fire Protection Association (NFPA), a quarterly inspection is defined as an inspection that takes place four times a year, with a minimum of two months and a maximum of four months. Therefore, the period between inspections should be at least two months and should not exceed four months. This is the minimal requirement. The following items that the NFPA suggests to be inspected quarterly are alarm valve exterior, fire department connection, valves and other supervisory devices, and water flow alarms.
Semi-Annually
The National Fire Protection Association (NFPA) defines this as inspections that are carried out twice a year, with a minimum of four months and a maximum of eight months. For this reason, the time that passes between inspections needs to be at least four months and should not go over eight months either. Tests are carried out for semi-annual inspections. This is an examination of whether or not the whole system or a portion of the system is functioning as it should. The following tests that NFPA recommends are control valve supervisory devices and water flow alarms.
Annual Fire Sprinkler Inspection Requirements
NFPA defines this inspection as a routine that needs to be done once per year, with a minimum of 9 months and a maximum of 15 months. Therefore, the period between inspections should be at least nine months and should not exceed fifteen months. The following items that the NFPA wants to be checked yearly are dry pipe valve internal, sprinklers from floor levels, hangers and braces, and hydraulic information signs. Aside from the inspections, the NFPA also requires some tests that should be done annually. The following tests are to be conducted on the following items: control valves, backflow preventers, and main drain tests (quarterly if the system is supplied through a backflow or pressure-reducing valve), a dry valve drip test, and other supervisory devices.
As required by manufacturer
There are several components of a fire sprinkler system that are not defined by the National Fire Protection Association (NFPA) regarding the frequency with which they should be examined. It is recommended that inspectors consult the handbook provided by the manufacturer in order to identify the appropriate inspection frequency. This will allow them to get information on the inspection needs of the product. This sort of information is often included in the manual that is provided by the manufacturer.
Regardless of the frequency of your inspections, all fire sprinkler inspection requirements and documentation centre around proper fire inspection procedures and checklists, like the below. You can use the fire sprinkler inspection checklist template for yourself here.
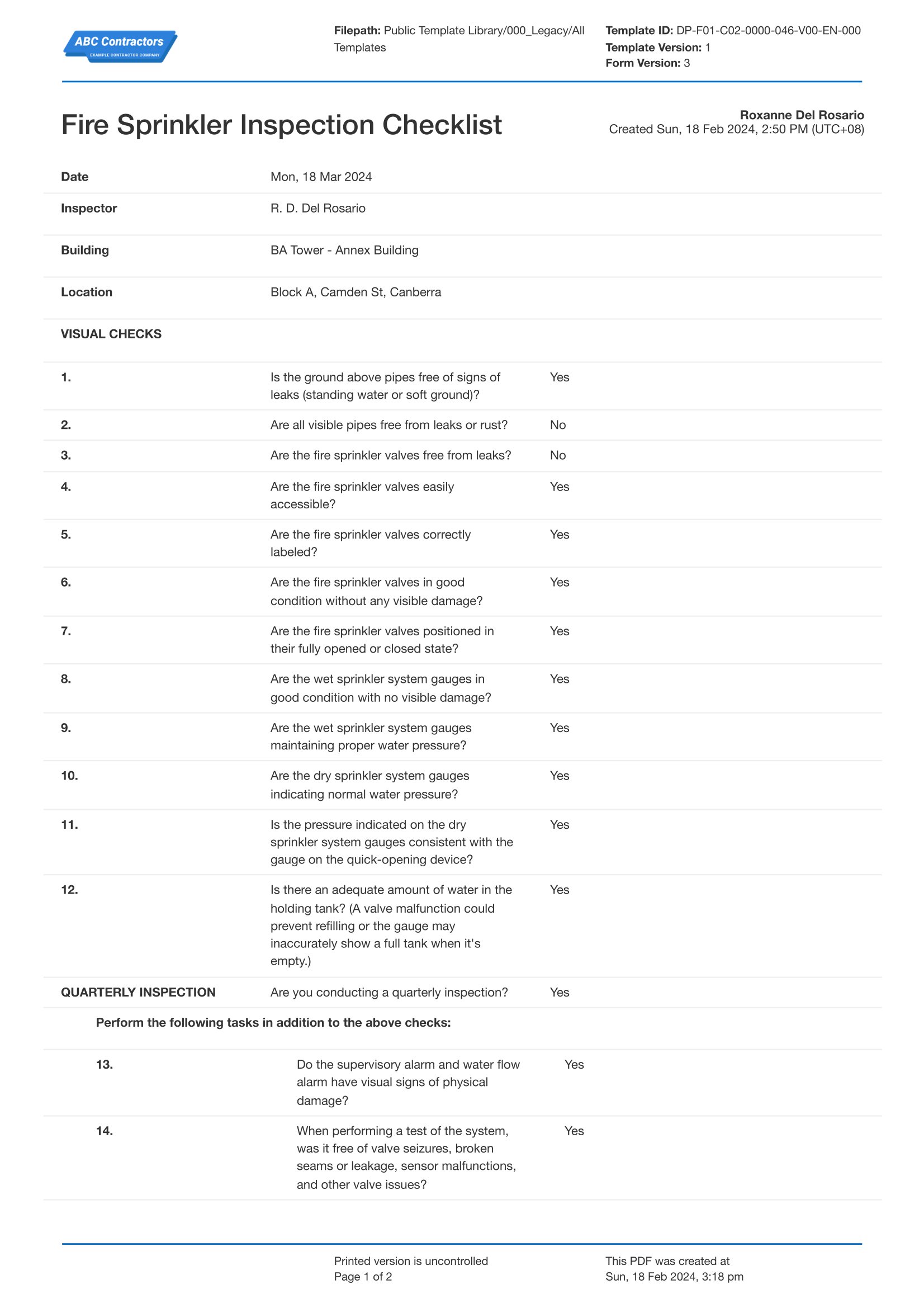
Use and customise this better site instruction template for free
Fire Sprinkler Visual Inspection Item Requirements
At this point in time, we are going to have a conversation about the fire sprinkler systems and specifically what needs to be examined.You may use this as a reference to create the things that are included on your inspection checklist. This is also based on the NFPA 25 visual inspection requirements.
Leakage
It is necessary to replace sprinklers that are leaking or that have been damaged without first doing proper testing. It is possible for dissolved minerals and other residues in the water to solidify while the sprinkler leaks. This may hinder the functioning of the sprinkler by altering the internal clearances or serving as an adhesive, which prevents components from moving as they were supposed to. The text that is included in the NFPA 25 Annexe establishes a difference between water that is "spraying or running" and water that is "dripping." There is a possibility that the sprinkler is damaged, such that it does not function as it was designed to. Whatever the case may be, this scenario would need taking action since the device's functioning is being called into doubt.
Physical damage
Deflectors that have been damaged should not be ignored, despite the fact that it may be difficult to pinpoint their location from the ground. The dispersion of the spray pattern and the density of the water that is supplied may be significantly altered by even what seems to be just little damage to the deflector. This can have a significant influence on the product.
Corrosion
The sprinkler's performance may be negatively impacted by corrosion on the seat, accumulation on the deflector that may alter the spray pattern, or accumulation on the working parts that may impair the sprinkler's functionality. If the samples are chosen for testing in accordance with NFPA 25 based on worst-case situations and the samples pass the tests, sprinklers that are lightly loaded or have little corrosion that does not affect the water distribution characteristics may remain in operation. Surface discoloration that doesn't affect the sprinkler's functionality shouldn't be enough to justify testing or replacement.
Paint (Those not included in package or design)
The sprinkler shouldn't have paint on it that differs from what the manufacturer applied. It is never permitted to clean or replace painted sprinklers due to the significant danger of damaging the assembly. A "light" overspray or loading could be allowed once a representative sample is analysed to make sure the sprinklers will operate as planned.
Loading
The criterion for replacing sprinklers in subsequent editions has changed from requiring the replacement of any loading to determining if corrosion or loading is impairing sprinkler function. This adds a degree of subjectivity to sprinkler inspections and further clarifies why competent individuals must do the inspections in accordance with NFPA 25. Sprinklers that exhibit indications of malfunctioning upon examination must be replaced. However, a vacuum or a burst of compressed air may be used to clean those with little loading.
Sprinklers installed in the incorrect orientation
Sprinklers that are put in the improper orientation, such as an upright sprinkler that is positioned in the pendant position, will not generate a spray pattern that is effective. Whenever anything like this occurs, the problem has to be rectified by either relocating the branch line, drop, or sprig, or the sprinkler needs to be replaced immediately. This is something that has to be fixed whenever it is seen, even though it is not always simple to discern from the floor level.
Minimum clearance to storage is maintained
The efficiency of sprinklers can be hindered by obstructions to sprinkler distribution patterns, such as storage that is located in close proximity to spray deflectors like in the example shown. When it comes to distribution patterns, barriers that are positioned closer to the sprinkler than 18 inches (457 mm) have a bigger influence than obstructions that are located further away. NFPA 25 is the only one that makes mention of these obstacle lengths because, in contrast to many of the other obstruction distances prescribed by NFPA 13, these are very simple to identify visually.
Streamlining your Fire Sprinkler Inspections
When it comes to doing preventative maintenance on equipment or any object/s, inspections are the most effective method to use, particularly in situations when the things in question are essential to the preservation of both lives and assets. A comprehensive examination of the fire sprinkler system, provided that it meets the standards, will confirm that your system is really fully optimised to operate once a fire starts. This will ensure that your workplace is safer and more healthy, even in the event that there is a risk of danger.
However, there are several stages involved in creating and conducting your inspection by hand using the pen-and-paper approach before you can get any results. Everything is formatted by hand, which makes the creation of your inspection form take a lot of time. Furthermore, printing it frequently only to record a few items on the inspection uses a lot of resources. This doesn't help the environment, especially nowadays, where we should be trying to save the planet.
There are several processes involved in performing the inspection by hand, particularly when location markers, checklists, and photos are documented using various techniques. If you do it by hand, your phone takes pictures, and you write locations and checklists on paper. There are also several processes involved in encoding this in order to create a single inspection report, and we have yet to transmit these inspection reports, which is another time-consuming procedure if done manually.
Fortunately, there is now a smart way to do these fire sprinkler inspections. With the Dashpivot fire sprinkler inspection app, there is no need to move between paper and digital devices since you can do digital inspections with ease and record all required data on a single device. You can customise the pre-built fire sprinkler inspection to meet your project needs, or you can create your own form using the drag-and-drop form builder, adding any necessary fields or sections. This will remove the effort of creating your forms manually.
Additionally, by sharing your standardised form in the app, you can make it simple for your staff to complete fire sprinkler inspections on location. They may do the fire sprinkler inspection on their phone, and once they submit it, it will instantly sync back to the office. You can also take photos inside the fire sprinkler inspection app on your phone or tablet on-site as you're conducting the inspection. The hassle of manually encoding data from different sources will now be removed when using this app.
All these and more when using the Dashpivot Fire Sprinkler Inspection App. To know more about it, click here: Fire Sprinkler Inspection app
To provide you a guide on creating your inspection form, check out our digital fire sprinkler inspection example below.
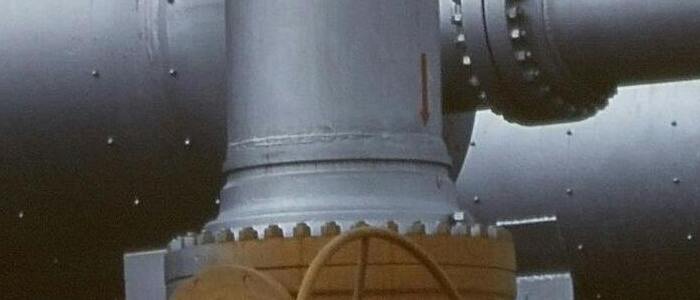
Gas safety check
Cover all of your fire sprinkler and gas safety checks
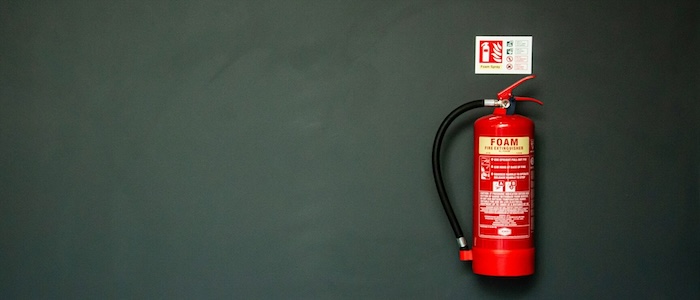
Fire extinguisher inspection
Cover your fire extinguisher inspections with this form
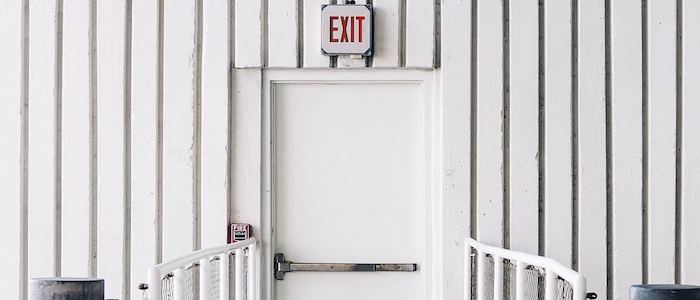
Fire door inspection
Fire doors also have firm inspection requirements. Meet them using this framework