Dashpivot Article – Lockout Tagout Safety Tips
Lockout Tagout Safety Tips
In this article, we focus on some of the most important lockout tagout safety tips as well as provide you with some best practice free resources, as the LOTO process is riddled with hazards.
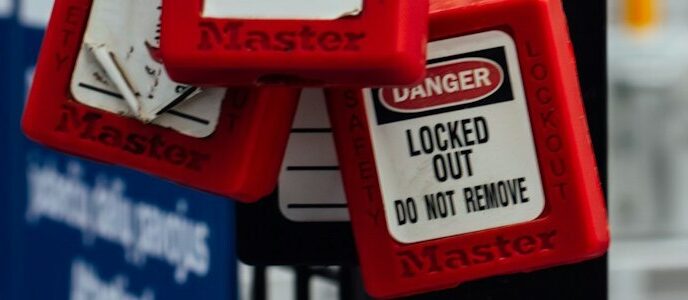
What is LOTO?
LOTO, short for Lockout Tag-out, is a critical procedure used in many industries to ensure equipment and machines are properly shutdown and de-energised before any maintenance work is carried out. This term was coined because of the two main steps involved in any lockout tagout procedure, which are: Lockout, which requires placing an actual lock on the energiser and keeping it in an off position to prevent sudden energy release, and Tag-out, which requires placing a tag that provides awareness that a machine or equipment is under maintenance and should not be started. Both lock and tag are necessary to keep workers safe and enhance the protection during maintenance activities.
Why is Important to be Thinking About LOTO Safety Tips?
According to the Occupational Safety and Health Administration (OSHA), failure to provide LOTO or failure to follow the correct LOTO procedures, contributes to 10% of industrial accidents. OSHA also stated that a Lockout Tag-out Procedure prevents an estimate of 120 worker fatalities and 50,000 injuries in the United States alone.
Performing the correct 6-step LOTO procedure is a necessary step in every maintenance activity to protect workers from the hazards that come with it. Here are some common hazards due to improper Lockout Tag-out procedure.
Accidental Power Restoration
A hazard where a machine is unexpectedly energised due to accidental power restoration. This is mostly the outcome of having no lockout tag-out procedures or improper lockout tag-out. The potential impacts could result to electrocution, fractures, impact injuries, crushing and fatality.
Stored Energy
In situations where pressure vessels and pressurised systems are involved, improper isolation could lead to sudden releases that can cause injury and damage to property. These injuries and damages scale on how much energy is stored. The larger the energy being stored the more dangerous it is.
Chemical Exposure
Chemical control valves, chemical containers, and chemical processing systems already contain potentially hazardous contents themselves. Improper isolation of these during maintenance work could lead to a leak which could result to burns, acute and chronic effects to human bodies due to exposure of toxic substance, and fatality.
Fire and Explosions
There are activities which requires hot works and the presence of highly flammable materials. Reenergising a machine in the presence of these activities and materials could potentially trigger fires and explosions. The consequences can be severe if lockout tag-out procedures are compromised or neglected.
Mechanical Failures
Improper Lockout Tag-out can lead to mechanical failures, causing machinery parts to break off or lead to a more catastrophic breakdown. This will drastically increase repair time and maintenance costs contributing to a huge production loss. Broken down machines integral to a company’s production could greatly affect on the company’s revenue.
Good Lockout Tag-out Safety Tips
Here is a list of Lockout Tag-out safety tips that could help reinforce awareness in safety and health within your organisation making regulatory compliance a breeze.
If you are looking for ways to standardise how your team approaches LOTOs, then you can also use a proper lockout tagout template to ensure each step is followed every time.
Lockout Tagout Safety Tip #1 - LOTO Training
Locking out and Tagging out should be considered as a permanent procedure in any maintenance activity where energy or flow isolation is needed. It is important that this procedure is carved into the minds of the workers to avoid loss time accidents and damage to crucial assets.
To eliminate such adversities, workers should undergo comprehensive training with the lockout tag-out procedures to help them understand the hazards and potential impacts if not done properly. Procedures should be discussed step-by-step during the training to ensure that all workers will have a similar understanding and avoid confusion during actual practice.
Additionally, The training should be done periodically for continuous learning and help close gaps to help workers be confident in applying knowledge into actual practice . Workers who undergo training will have a good understanding on the dangers of their work and will develop a sense of responsibility towards themselves and their coworkers. The training will also help promote a safety mindset among workers generating a good safety culture. An organisation with a good safety culture enhances its reputation and improve’s the company’s image with its customers and partners.
Regular Audits Reviews, and Updates
Regular audits, reviews, and updates are essential for maintaining the effectiveness of the safety objectives, plans, programs, and procedures in an organisation. Organisations can maintain a good regulatory compliance record if these actions are performed frequently. By thoroughly examining the organisation's current safety management documents, they can identify and rectify non-compliance issues. Audits, reviews and updates also help organisations identify gaps, errors, discrepancies and potential areas for improvement. This strengthens existing safety controls and enhances the safety management system. Conducting regular audits, reviews, and updates improves the effectiveness of the current safety and health management system, enhances safety controls, and ensures regulatory compliance.
Surfacing LOTO Safety Tips via Toolbox Meetings
Toolbox meetings, commonly known as toolbox talks, are informal meetings that focus on safety issues related to the activities laid out for the day or week. This is used to remind the team of the safety measures, why they are needed, and when they are needed.
Meetings like this are perfect for sharing lockout tagout safety tips (or any safety tips), which really keep the tips front of mind.
Toolbox talks should highlight incident prevention, safety instructions, equipment use and who has the authority to use them, personal protective equipment, and specific hazards in the workplace.
The more detailed the toolbox meeting, the greater the sense of safety responsibility instilled into the minds of the workers. One of the most important agenda items or topics for a toolbox meeting, for industries with moving machinery, is the Lockout and Tag-out procedure toolbox talk.
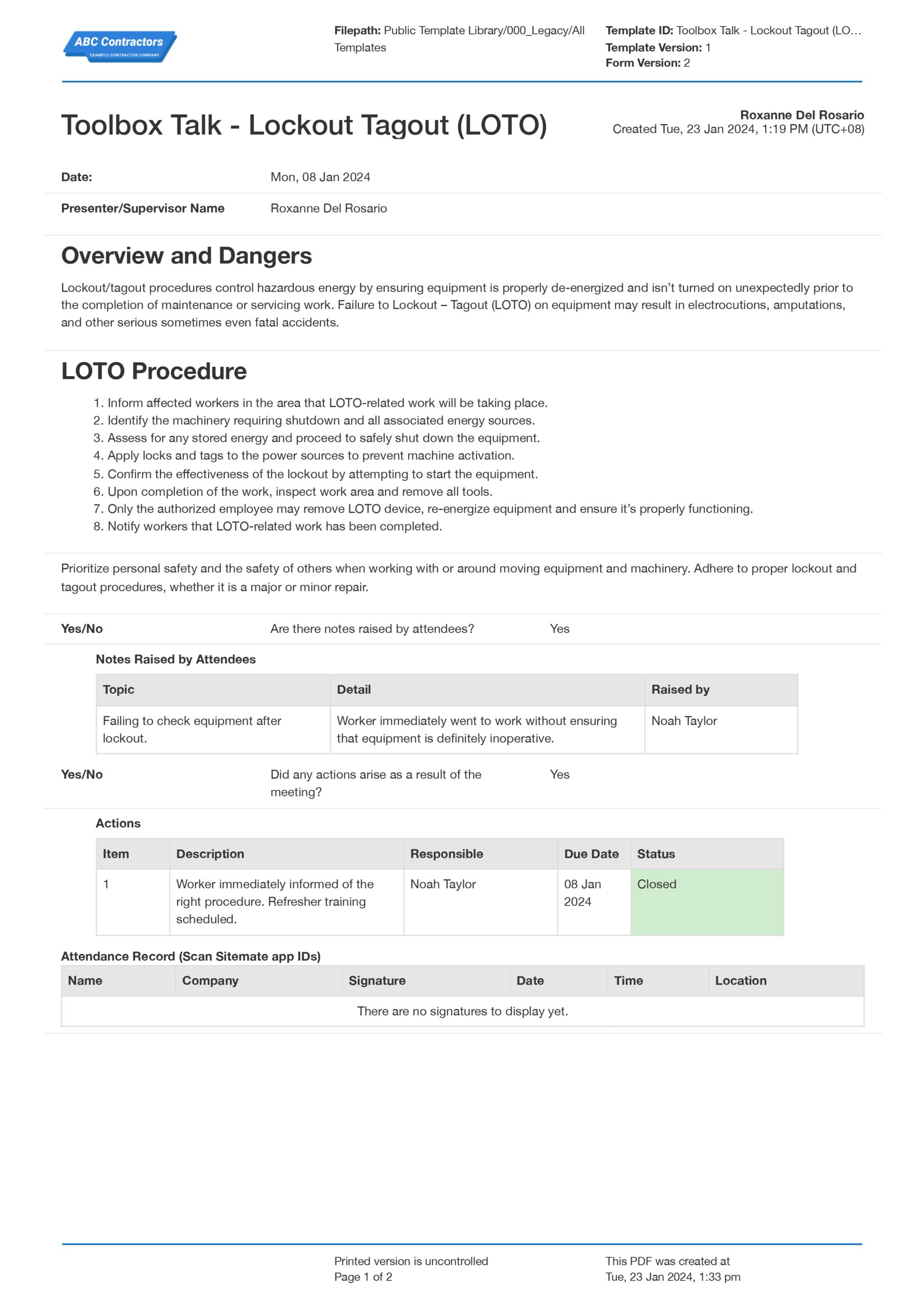
Provide lockout tagout safety tips to using safety forms like this
It is always vital to remind the workers of the correct LOTO procedures to safeguard themselves against the risks. One way to do this is to discuss the flow of the Lockout Tag-out permits and why it is crucial to have it done step-by-step. Toolbox meetings are generally done weekly but could be done more frequently depending on the size, nature, risks and location of the activity.
Toolbox talks are beneficial for organisations because they promote workplace safety. By providing a platform for discussing safety topics, these meetings help raise awareness, improve communication, enhance training, and foster a safety culture within an organisation.
Critical Lockout Tagout Safety Tip - Standardised your Locks and Tags
Providing standardised locks and tags ensures that workers properly isolate the energy source of machines or equipment before any maintenance or repair works. Having a secure lock and a clear tag eliminates all the risks that come with accidental re-energisation.
Standardised locks are locks that are durable, have unique keys, and are substantial enough to prevent removal without excessive force. This is to make sure that the only person who can remove the lock is the one who attached it, and nobody else. This eliminates the risk of re-energizing the machine or equipment by another person. Having a lock with duplicate keys could compromise the safety of the workers performing the maintenance activity. Knowing this, it is also paramount that all workers performing maintenance on a de-energised machine or equipment should attach their own lock and tag.
Tags are supplementary to the locks. They tell the workers who are not involved in the maintenance activity that a machine is under repair. Standardised tags have a consistent colour (i.e. red, yellow, or depending on the organisation’s decision), and are uniform in size and shape. The content of the tag should highlight the person who attached the tag, details of the maintenance activity, and have clear warnings on them (i.e. DO NOT OPERATE, DO NOT START). Lastly, tags should be able to withstand the environment they are in. This is to ensure that the tags are always visible and provide awareness to the workers surrounding the area.
Establishing a clear LOTO sequence
It is a requirement for organisations to establish and provide clear instructions on the Lockout Tag-out procedures to have a uniform and consistent understanding of the required steps. These instructions should be accurately and throughly documented and easily available. A well-structured LOTO procedure should have the following key steps: Preparation,Shutdown, Isolation, Notification, Verification, and Maintenance Activity.
During preparation, it is important that all necessary permits and records are readily available before starting the activity. Employees should identify the energy sources, the workers involved in the activity, and those responsible for verifying the proper attachment of locks and tags. This preparation ensures that employees will have clear guidance on where to attach their locks and tags and who to notify for verification.
Once the machine or equipment is shutdown, workers attaching their locks and tags must to inform the personnel overseeing the activity and request verification. During the verification process, personnel overseeing the activity must confirm that the lock and tag are securely fastened, accurately labeled and clearly visible. This process is best managed through a structured LOTO workflow permit, ensuring that all actions are properly documented and the steps strictly followed. After verification of all workers involved, personnel overseeing the activity can now provide clearance for activity to start.
Once an employee completes their task, they must remove their locks and tags, notify the person overseeing the activity, and have the removal verified and documented. This approach helps maintain safety, accountability, and compliance throughout the process.
Reduce your Reliance on Lockout Tagout Safety Tips by Leveraging technology
LOTO sequences and 'workflows' can be dramatically simplified and streamlined using lockout tagout software packages, which actually automate a lot of the lockout tagout safety tips we have covered by baking them into how your workers conduct LOTOs.
These systems has a centralised database for forms which multiple users can access and use vs. paper forms, which don't even have a central access point. Having a centralised form helps with uniformity and avoids confusion amongst workers, and also enables you to properly track the status of your LOTOs in real-time.
This is helps users with forms that require signatures for notifications and or verifications before proceeding to the next step of their activity. Using technology, you can set up simple and powerful automated workflows which streamline these processes to save everyone time and ensure important project information gets to the right people straight away using automatic notifications.
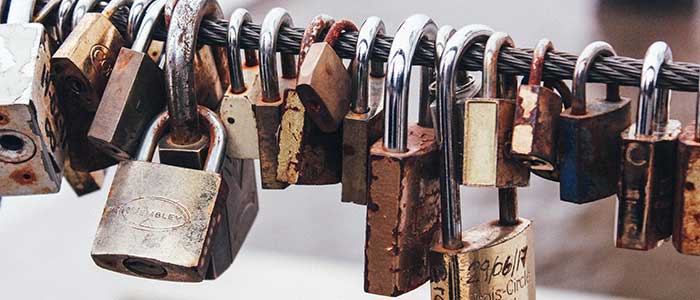
Lock Out Tag Out template
Use this LOTO template as a framework for doing all of your lock and tag outs properly and safely.

Lockout Tagout Periodic Inspection Form template
Streamline your lockout tagout inspections and ensure your LOTO program and records stay up-to-date and compliant with this template.
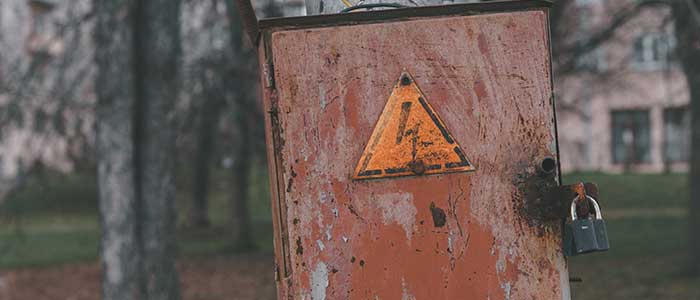
Lockout Tagout Program Audit Checklist template
Complete and organise your daily diaries more efficiently.