Dashpivot article page – What is a Task Hazard Analysis
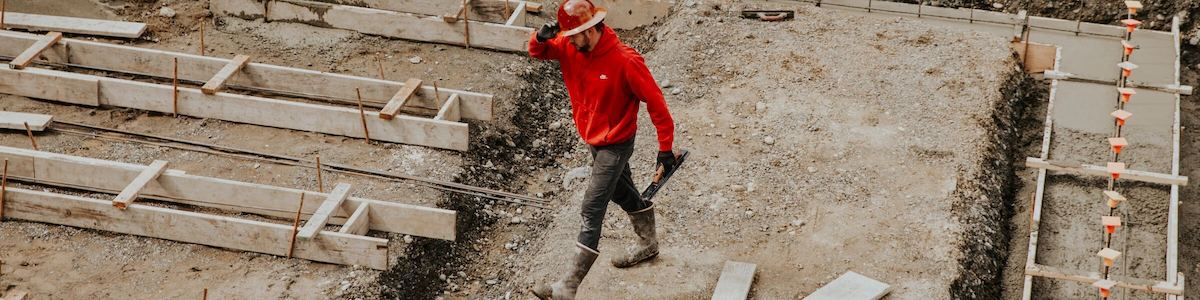
What is Task Hazard Analysis?
What is a Task Hazard Analysis (THA)?
Task Hazard Analysis (THA) is a structured process for identifying, analysing, addressing, and controlling the potential hazards that are related to workplace tasks. It may also otherwise be known as Job Hazard Analysis (JHA), or Job Safety Analysis (JSA), but there are a few differences. It promotes a culture a safety in the workplace by providing a step by step method that encourages workers to proactively recognise risks and address them before they turn into incidents. It breaks down the task into actionable steps in order to uncover the risks involved and implement controls that mitigate or eliminate them. In this article, we'll drill into the question of what is a task hazard analysis so that you fully understand this critical safety process.
When Task Hazard Analysis is incorporated and implemented in the workplace safety practices, hazards can be identified early on. It prevents injuries among employees directly involved in the task, reduces the disruptions in the operations and workflows, prevents additional expenses from accidents like medical expenses and legal liabilities, and it also maintains compliance with regulatory standards. Incorporating THA in practices is a legal responsibility and a necessary measure to promote workplace safety and employee well-being.
Read on to understand more about what a task hazard analysis is, or skip to this article to view a task hazard analysis example.
Why is THA Important in Promoting Workplace Safety?
The Task Hazard Analysis is usually filled out by supervisors, managers, safety officers, or team leads who are responsible for overseeing a specific work task. The workers who are responsible for performing the task are directly involved in the process. They collaborate with their team leads because they have the direct and first-hand knowledge of the task, so they can pinpoint the potential risks and the solutions to mitigate them. This type of collaboration fosters a culture of safety, and accountability. The collaboration between the workers, supervisors, and safety officers ensures that the entire process is structured, and thorough. With everyone involved and collaborating, it provides a more realistic and proactive approach in identifying and addressing hazards, ultimately promoting workplace safety and is a component of workplace safety itself.
The primary purpose of a Task Hazard Analysis is to empower the implementation of protective and preventive measures and controls that eliminate and mitigate risks associated with the work task, enhancing operational efficiency and workplace safety. For example, before workers conduct a maintenance check on an equipment or heavy machinery, the safety officer must first conduct a THA. Upon assessment, they may identify hazards like electrical hazards, fire hazards, and moving parts. With the findings from investigation and directly involving the workers, they can implement safety measures like the lockout/tagout procedure, or PPE checking.
A Task Hazard Analysis is most especially essential in industries where workers are often exposed to risks from hazards that involve heavy machinery, hazardous materials and surroundings, or physical labour. It’s highly used in the construction, engineering, manufacturing, oil and gas, mining, transportation, and healthcare industries.
Implementing a Task Hazard Analysis is beneficial in workplace safety, for both the employers and employees. THA ensures compliance with safety regulations and industry standards and for employees, it ensures enhanced safety and protection from hazards and reduced stress. With active involvement, employees are given a sense of ownership and responsibility for their own safety, and employers can lead a safe work environment with fewer interruptions and disruptions from accidents.
What are the Steps in Performing a Task Hazard Analysis?
The goal of a Task Hazard Analysis is to provide a breakdown or step-by-step procedure to identify and mitigate risks and hazards. It involves manageable and achievable steps as described below. With this type of structure, safety officers and workers can easily identify risks and implement precautions.
Selecting High-Risk Tasks: How to Identify Tasks Requiring Analysis?
To start, supervisors or safety officers select tasks that require THA. More often, these could be the common or routinely tasks. For new tasks, the safety officers need to know if these are high-risk tasks that have unknown or foreign hazards. Some common factors to consider are whether these tasks involve complex procedures, hazardous materials, heavy equipment, and places with known or unknown risks. THA can also be performed in tasks that have already caused incidents before. If the industry is in construction, manufacturing, engineering, oil and gas, or other high-risk industries, most tasks undergo THA. For less risky industries, tasks that are also performed in high-risk industries need to undergo THA.
Breaking Down Into Steps: What are the Steps to Break Down a Task Into Smaller Components?
After the supervisor or safety officer selects the task, they break it down into manageable and achievable steps. This is particularly important to ensure that no part and hazard are overlooked in the task. After breaking down the steps in performing that task, they should be described and outlined in detail so that the safety officer and workers can identify where the hazards may lie. Take, for example, the chosen task involves using a heavy machinery. To break this task down, there is pre-inspection, set-up, operation, post-inspection, and shutdown. The safety officer and workers can now identify focused hazards in each step and address them accordingly.
Hazard Identification: How are Potential Hazards Identified and Documented?
For each step in fulfilling the task, the safety officer and workers must think about what could go wrong between the worker, equipment, materials, and the environment. That way, it’s easier to identify the hazards and put them in categories, or the other way around, use categories to identify hazards. There are physical, chemical, biological, ergonomic, and environmental hazards.
Risk Assessment: What Criteria are Used to Assess the Risk Level of Each Hazard?
By using a Risk Matrix, safety officers evaluate the likelihood and severity of the hazards identified to occur. If the results indicate that they have high likelihood and severe consequences, then those would be given priority to address. This helps safety officers and the management to organise hazards according to importance and address priorities first.
Developing Controls: How to Develop Control Measures?
There are typically three categories of control measures: (1) engineering controls, meaning changing the environment and adding safety barriers; (2) administrative controls, meaning changing procedures, implementing protocols, training staff, and more, and; (3) personal protective equipment, meaning wearing protective gear to reduce exposure to hazards.
Reviewing, Communication, Documentation, and Monitoring: What is the Best Way to Communicate and Document the Analysis?
Once the THA has been completed by the supervisor or safety officer, the document should be reviewed by the team and all workers involved or performing the task. It’s important to share the results of the analysis to them, as they can provide valuable insights and feedback, most especially with workers who have first-hand experience on the tasks. They know and understand the potential risks from years of experience. Through clear communication, they are fully aware of the risks involved and control measures being placed by the safety officers.
The THA should be well-documented and easily accessible to the workers involved, supervisors, and safety officers. It’s highly recommended to use digital forms so that the safety officer can streamline the entire THA process, and easily share to the workers and management. Involving the workings in feedback ensures continuous improvement in workplace safety.
It doesn’t only end with THA implementation, it’s important to constantly monitor the task and make sure the control measures are effective and that no new hazards arise afterwards. The supervisors and safety officers are in charge of overseeing the tasks even after THA-implemented. And if there are any changes or new hazards discovered, the THA should also be updated. Digital forms are much easier to use to document and monitor tasks. Safety officers can easily retrieve the data and edit the files or create new versions for the changes.
If you are struggling to get your team to follow a standardised THA process, then you can use a JHA Template like this to streamline how THAs are performed and documented.
How can Organisations Integrate Digital Forms in Dashpivot Into THA?
Organisations can integrate digital forms into their Task Hazard Analysis to streamline the process. This ensures that all THA are well-documented, easily filled out, accessible, and collaborative in the workplace. By using Dashpivot as a digital tool, you and your team can achieve all of that in a single application.
With Dashpivot, all Task Hazard Analysis documents are stored in a centralised database. This makes it easier to access documents and files, retrieve them for further analysis, or create versions for change management. Dashpivot features a flexible folder system where you can control how it looks like, and layered permissions ensuring top-notch security. Only workers directly involved, supervisors, and safety officers can access THA documents. This makes sure that no one else can accidentally edit or delete essential files. With easy data retrieval, you can collect all THA documents and export them when compliance reports and audits are near.
Dashpivot mainly features a drag-and-drop form builder. You can develop customisable digital forms tailored specific to your organisation to standardise the THA workflow. You can include essential fields like creating a table to input the steps with a column for descriptions and hazards identified. Include a risk matrix and create another table where you can add entries for hazards and controls. Creating your own makes sure that you wont miss critical details important for the organisation. Attach matrixes, photos, videos, attachments, and more. There are text, number, date, formula, and signature fields. There are formats for checklists, drop down menus, and many more. Add e-signatures and make approvals faster. Workers, supervisors, and safety officers can sign off THAs electronically.
With mobile accessibility, safety officers can access the THA forms and fill them out using their mobile device or tablets on site. This allows real-time data entry, hazard identification, and updates. This accessibility and convenice is more dynamic and adaptable to any condition. Even offline, data will be saved and synced later on when you’re connected to the internet.
Digital platforms encourage real-time collaboration. Employees not in the field can access the THA documents in their computers, mobile phones, and tablets even when they’re in the office. With THA requiring feedback and comments from experts, collaboration is made easy with a centralised database.
Dashpivot overall automates rigorous steps and makes it easier for everyone. Additionally, there are analytics and dashboards that support further analysis. You can use charts and dashboards to track trends and identify which areas need improvement.
You and your team can leverage Dashpivot as your digital tool and modern solution provider to streamline the entire THA process. Enhance operational efficiency, data accuracy, and ensure compliance with regulations through Dashpivot.