Manufacturing Safety Audit Checklist Template and PDF
Start with a free 30-day trial. No credit card required.
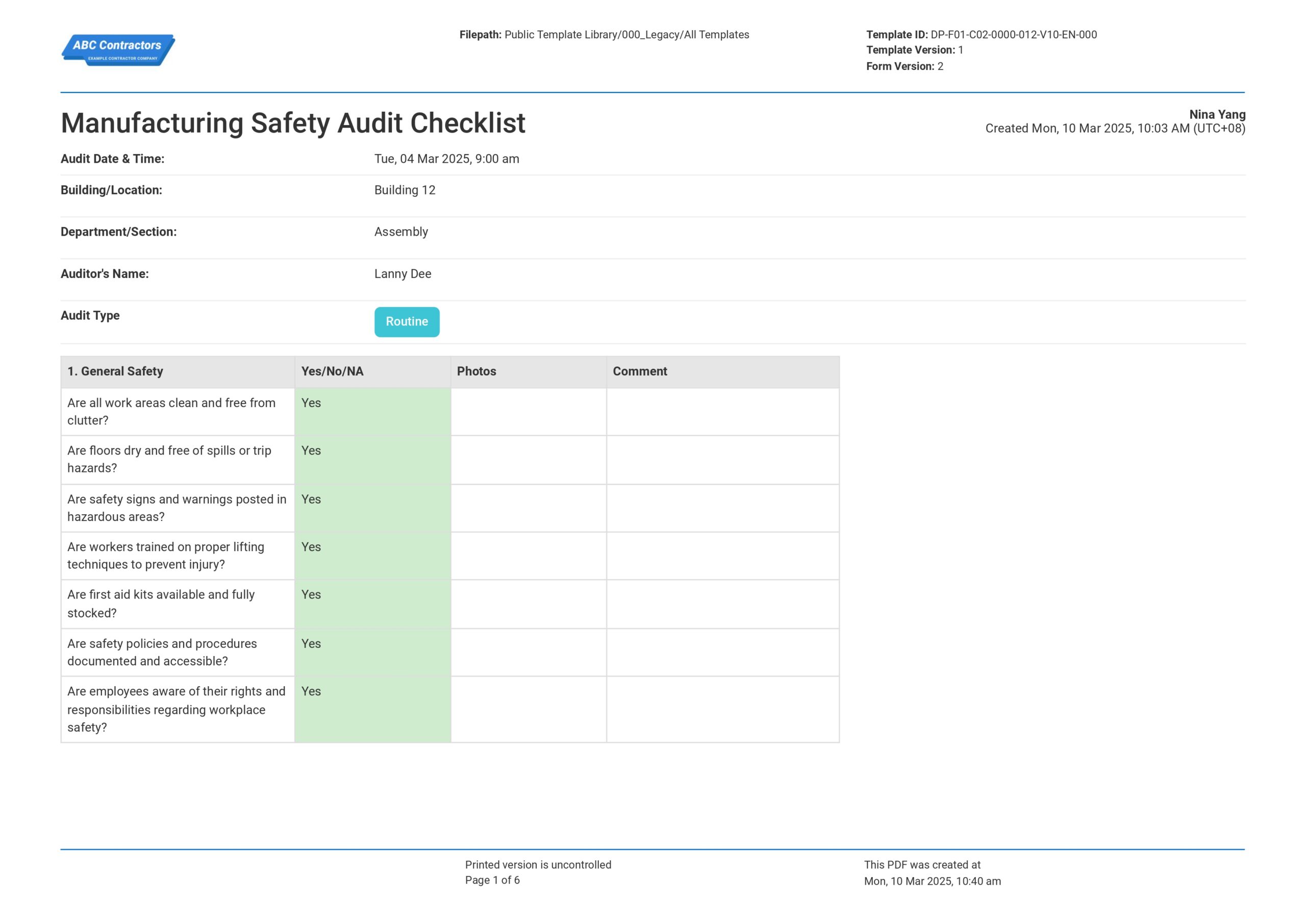
~200 employees
~20 employees
~25,000 employees
~40 employees
~10,000 employees
~1,500 employees
~35,000 employees
What is a Manufacturing Safety Audit Checklist?
Manufacturing Safety Audit Checklist template is a framework of standard safety inspection in a manufacturing production line. The inspection aims to callout potential hazards in the production line that could put the workers at risk to workplace accidents. It can cover various aspects such as general safety or relating to housekeeping in production, personal protective equipment, emergency preparedness, and more. There are many types of safety audit checklists, and this template is designed specifically for manufacturing companies.
Compare this smart checklist to Word, Excel or PDF versions
Use this Manufacturing Safety Audit Checklist template for free.
What is the purpose of a Safety Audit Checklist for a Manufacturing Company?
The purpose of manufacturing safety audit checklist template is to support an auditing team in ensuring the manufacturing workplace is safe and compliant to regulatory standards. Manufacturing safety audits are done to verify if there are any potential safety issues in the production line that need to be corrected and to verify if the workplace is compliant to company-wide and local safety regulations at the same time reinforcing operational efficiency.
A manufacturing safety audit checklist can be used internally or by an external organization who develops safety audit tools like OSHA, ISO and ANSI which sets regulatory framework for workplace safety. The requirements for internal safety audit should be similar with the external safety audits.
What is included in a manufacturing safety audit checklist?
When conducting manufacturing safety audit checks, the document should have the essential details to ensure the report is reliable and structured to have accurate representation of the production line’s safety status. It should include the following details:
• Time and Date of Audit
• Location of Audit
• Name of Auditor
• Audit Type
• Aspect of Audit
• Findings and Corrective Actions Required
• Signatures of Auditors
A manufacturing safety audit checklist can focus on different aspect of production that involve potential safety hazards. Below are key safety aspects the checklist should include and their purpose.
- General Safety – to inspect if housekeeping protocols are followed or in place, confirming if there is adequate and functioning lighting, and if emergency procedures are straightforward.
- Personal Protective Equipment (PPE) – to confirm if PPEs are available or well-maintained, right fitting, correct or appropriate according to the process involved, and to check if the operator understand what’s it for.
- Machine and Equipment Safety – to confirm if the equipment in use has the appropriate machine guards and other safety controls to ensure safety of machine operator. Additionally, safety hazards in connection with equipment use has international standards that must be followed by a company such as Safety of Machinery – Safety-Related Parts of Control Systems in ISO 13849-1:2023
- Fire Safety and Emergency Preparedness- to confirm if the manufacturing site is equipped in term of fire safety supplies and ready in case of emergency. Fire accidents are one of the most workplace accidents that can result to human and property loss.
- Chemical and Hazardous Material Safety – to confirm if Manufacturing Safety Data Sheet (MSDS) is available, if hazardous materials are labelled and handled properly.
- Electrical Safety – to identify potential electrical hazards in the manufacturing site. For example, to confirm the access of electrical panels, if workers are trained in electrical safety, and if circuit breakers are properly labelled.
- Ergonomics and Manual Handling – to verify if workplace accidents relating to manual handling and ergonomics issue are eliminated or minimized. The checklist will include questions relating to seating, training of workers in proper lifting techniques and if heavy loads are properly stored.
- Noise and Air Quality – to check if the noise and air quality in the production line is within the safety standards of occupational noise exposure.
- Incident and Accident Reporting – to check if incidents and accidents are all reported and documented. Auditors would need to verify previous records and if there are any hindrances for workers to report an incident in the workplace as soon as it occurs.
The manufacturing safety audit checklist in each company may vary in terms of content as it will depend on the focus of the safety inspection. Usually, inspection items are in a yes/no question form to make it easy to go through. This is where using a digital tool comes in as it helps to use a software that will make checklist creation and modification effortless. This checklist is made from a software that allows you to build and edit using a drag and drop system.
How can Digital Checklists and Data Streamline Your Inspections?
There are apparent advantages in using a digital checklist as it is built to provide a structured approach when conducting inspections. Below are the top reasons that could help you and your organization to make the switch.
Seamless walk through in the production
As audits essentially require auditors to walk through in the production area to find potential safety issues, using a digital tool which you can access from an app can make this process seamless and efficient.
Real-Time Data Entry and faster reporting
Instead of using a separate form for inspection and then transferring data in Excel or Word to put together for reporting, you can use this checklist as it is and submit it as an official audit report in one step–complete with the ability to add photos and videos on the go. This template is powered by an app that can quickly generate a PDF or CSV form or even send it directly via email.
Central Data Storage
One of the challenges when using paper-based forms is retrieving incident and accident reports or past audit results from physical storage. Even when records are stored digitally, this can still be an issue when only one person is managing data on a personal computer and not in a central storage system. This digital manufacturing safety audit checklist can be built, stored and access in one software platform allowing for prompt data retrieval.
Shifting to paperless audits is a breakthrough for a manufacturing company with all its numerous advantages. It instantly improves efficiency, ensure compliance and enhance the accuracy of manufacturing safety audits.
Other popular templates you can use and customise for free

5S Checklist for Manufacturing
>5S originated in manufacturing for good reason. Make sure your manufacturing operations are meeting your 5S standards
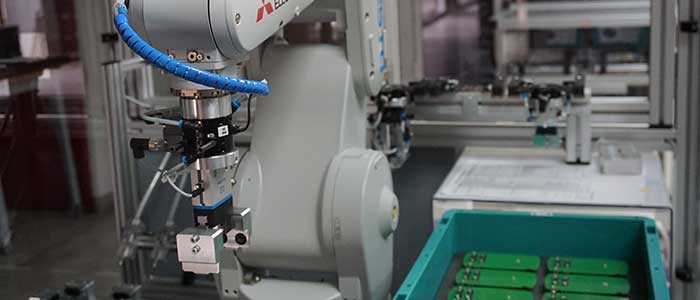
Manufacturing Process Audit Checklist
Improve how you complete, organise and action these critical process audits and process audit checklists.
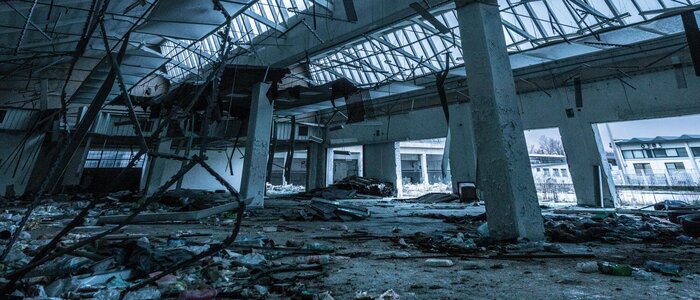
Damage Assessment Report
Use this damage assessment report to properly document and assess damage in any event, including disasters.
This Manufacturing Safety Audit Checklist was generated with Dashpivot software
Make the switch and improve your safety audits with digital solutions. Conduct seamless audits, enjoy real time data entry and faster reporting, and create audit forms–all within a software platform that securely stores your digital records.
- Access, edit and complete Manufacturing Safety Audit Checklist from any device - mobile, tablet or computer.
- Print, download or send your Checklists as perfectly formatted PDF documents with your company logo/s.
- Store your Manufacturing Safety Audit Checklist securely online, where they can be searched and found in seconds
- Invite internal and external parties to see, edit and sign off on audit records online.
Sitemate builds best-in-class software tools for built world companies.