Dashpivot Article – Forklift Safety Procedures
Forklift Safety Procedures
This article covers the essential forklift safety procedures, and to make it easier to digest to workers and relay relevant information, see at the end how digital solutions can reinforce safety procedures and practices related to using forklifts.
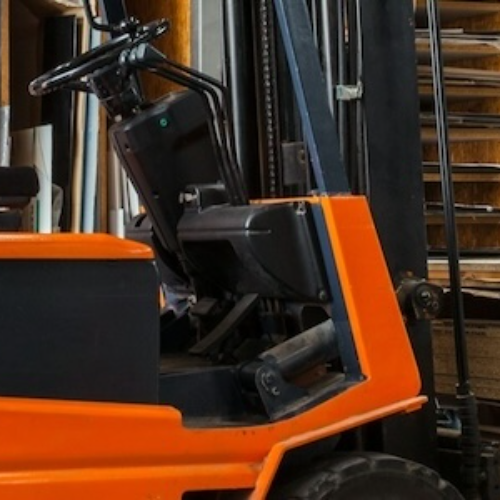
OSHA forklift safety rules
Forklifts are powerful equipment in various industries, most especially in the construction industry, and are also extremely helpful in work environments where lifting and transporting heavy materials are needed, like for example, a warehouse. It might seem like you’re just easily starting a car that has the capability to lift heavy items, but it’s more than that. There are numerous risks involved, especially if you’re carrying fragile, too heavy, or expensive materials – not to mention, there might be surrounding items or pedestrians involved.
The Occupational Safety and Health Administration has set clear and strict guidelines about forklift safety in their safety and health topic, OSHA’s Powered Industrial Trucks - Forklifts. In fact, they refer to forklifts as powered industrial trucks, which is an umbrella term for reach trucks, pallet jacks, order pickers, terrain forklifts, and other trucks that are used to carry, push, pull lift, stack, or tier materials. They highlight the necessity of having proper training and certification for forklift drivers and operators, conducting regular inspections on the truck, and preventing accidents during operation by following the safety protocols.
See OSHA 1910.178 - Powered industrial trucks a more detailed explanation about powered industrial trucks, and for a quick summary about forklifts see OSHA’s Safe Forklift Operation quick card.
In this article OSHA Forklift Safety, you’ll also know the essential requirements OSHA has mandate to promote safe usage with forklifts.
Forklift safety checks before starting
Before starting any machine or equipment, it’s common knowledge to do quick but thorough checks on them. It sounds overkill to check a forklift before using it or before your shift, but remember, OSHA considers them as powered industrial trucks, meaning they’re heavy and powerful machines that can potentially cause injuries (and fatalities in worst-case scenarios), damage to materials and surroundings, and what businesses worry about, expensive downtime. It’s best to be safe and have quick pre-inspection checks so you’ll catch issues early on and not worry about expensive repairs, replacements, or others.
Here are the three important reasons why a pre-inspection of your forklift is necessary:
You don’t want the smallest things to cause accidents: Whether it is a worn-out tire, a broken seatbelt, a failing break, or a broken horn – these can cause serious accidents and injuries. Everything should check out and safety should be at the top of the priority list.
You want to protect workers, pedestrians, and the environment: Forklifts are trucks, but they are often used or operated near people and work directly with items to be carried and transported.
You want to comply with the law: OSHA mandates pre-operation inspections before using or before every shift. In a way, this mandate prevents legal issues (and fines), and also helps the business prevent expensive repairs and replacements in the future.
Tips for forklift drivers and operators
It doesn’t matter whether the driver or operator are new, in training, or professionals with experience in the field, the number one requirement is that they always follow the safety tips as mandated by the local regulations and their company’s safety policies.
Inspect before driving: As mentioned, it’s a requirement to conduct pre-operation inspections before using a forklift. Catch problems by doing visual (before you start the engine) and operational checks (after you start the engine).
Know the forklift’s load capacity and limits: Know the load capacity of the forklift you’re driving, and always check the total load you’re about to lift as well. Keep the load below the load capacity, and tilt the carry back if you’re driving around the area.
Stay cautious and alert when driving: Don’t drive like a racecar, keep it slow if you’re carrying heavy loads. It’s not a competition. Keep the loads protected and the pedestrians safe. If you’re driving along intersections, blind sports, or even turns, make sure to drive slowly and use your honk to alert nearby pedestrians you’re driving through.
Be wary of pedestrians: Always keep in your mind that you’re going to be driving in a workplace with people. Stay alert, use your horns, set a perimeter if you have to, and never carry extra passengers.
Here are two relevant articles you also need to read if you’re a forklift driver, operator, or just a concerned pedestrian: Lifting Operations and Lifting Equipment Regulations and The right lifting equipment inspection procedure for you.
Most common forklift dangers and how to stay safe
Whether you’re a new operator, in training, or an experienced on, if the safety procedures are ignored, then forklift dangers are likely going to happen. Safety procedures are placed to make sure that the equipment, the driver, the pedestrians, and the items are safe and secured. But just to be sure, here are the top most common forklift-related leading causes of injuries, damages, and worst, fatalities you should be wary of:
The forklift tipping over: If you’re putting load beyond its load capacity, then it’s likely going to tip over. Other causes are the operator drives it too fast relative to the weight it's carrying, or you’re driving it in uneven surfaces. If it’s tipped over, the driver might also fall over or be crushed with the weight of the forklift and the items you’re carrying are damaged. It’s best to stay alert where you’re driving, how much you’re carrying, and what speed you’re going.
Colliding/getting crushed or pinned by the forklift: Driving the forklift, with experience, might be easy, but you need to be careful when you’re turning in corners or blind areas, or even reversing. The operator or the pedestrians/nearby workers who are not visible on the mirrors might get crushed in between the forklift and walls/obstacles. Make sure that you’re using your horns, there are visible signs that the forklift is being operated, and you’re driving with extra precaution to turns and reverses.
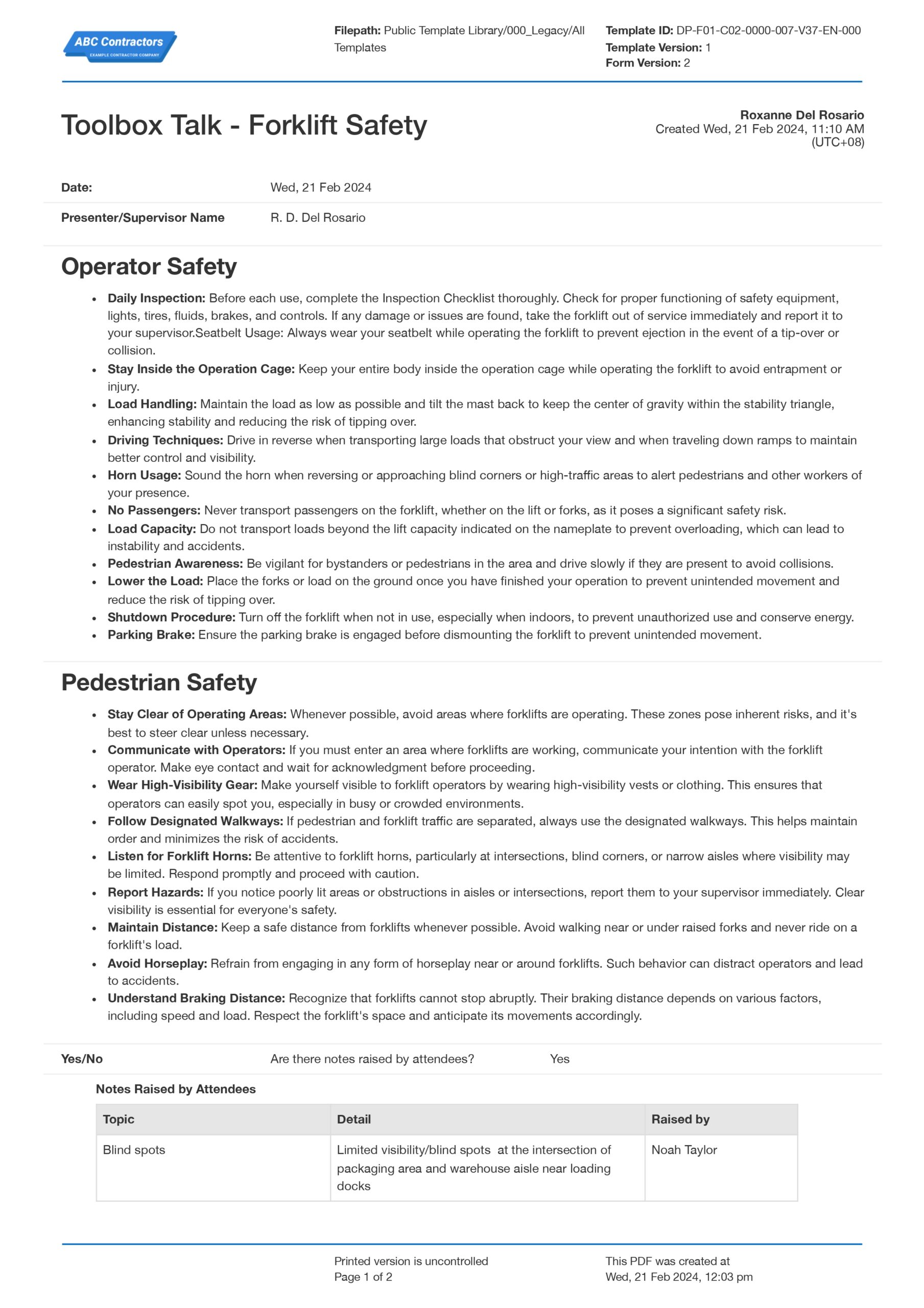
Use this free Forklift Pre Start Checklist for free
Reinforcing forklift safety through digital solutions
Industries are getting more dynamic and demanding, and workplaces continue getting more and more complex and fast-paced, and it’s harder to implement safety procedures in a larger scale, or in a bigger work area, or with more employees coming in.
To ensure that updated compliant forklift safety procedures are continuously practiced across the entire work area, using digital solutions can significantly reinforce stricter safety procedures and best practices, fully streamlining how operators conduct their pre-inspections, for example, by using this Forklift Pre Start Checklist or when there’s a need for audits and regular inspections, you can use this Forklift Inspection Checklist and easily have auditors and inspectors conduct their inspections digitally via a mobile device or tablet. In a hazardous workplace, supervisors and managers can easily generate this Forklift Job Hazard Analysis to plan for projects in advance that use forklifts more often than necessary, or this Safe Work Method Statement for Forklift to identify hazards early on.
It’s the digital solutions that make everything quicker and more convenient for workers. Even with all the tips and best practices coming from regulatory bodies and company safety policies, if they aren’t thoroughly and religiously practiced, and streamlined, then they won’t be effective.
Modern technology for enhanced forklift safety
Use modern technology to improve visibility across team members, fully enforce your safety protocols, and provide real-time insight. Going digital just doesn’t only mean you can use forklift-related documents and forms using your mobile devices or tablets, that also means when you hit that save button, data is automatically stored in the cloud, giving your team members in the office have real-time access to view, edit, and share the reports.
Additionally, you can enforce forklift safety and keep records secure and protected in a single platform. When you’re doing a toolbox talk, use this Toolbox Talk Forklift Safety and easy log concerns and suggestions from the toolbox talk. And this very same form also allows digital signoffs and digital IDs, making it extremely easy to record attendance and know who have been actively participating in forklift safety meetings.
There are even more packed digital solutions that make asset management and safety enforcement much easier and better in this Plant, Equipment, and Asset Library.
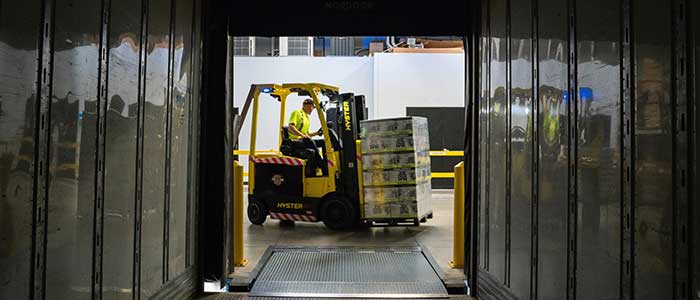
Safe Work Method Statement for Forklifts
Standardise your documentation and general approach to forklift safety using this template.
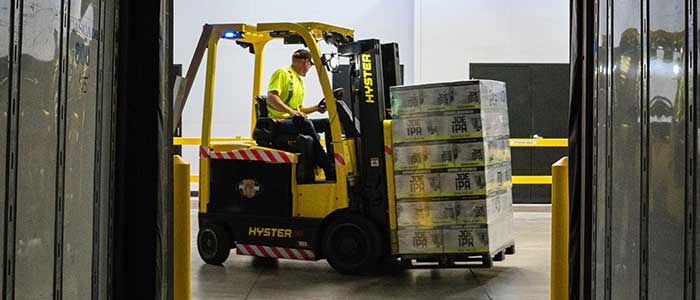
Forklift Job Hazard Analysis
Maintain safe forklift working practices with this Forklift Job Hazard Analysis template.
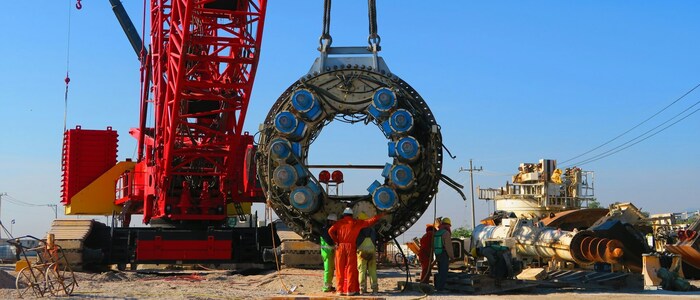
Line of Fire Toolbox Talk
Keep your team safe from Line of Fire incidents by following this toolbox talk template.