Dashpivot Article – Hazards From Improper Use of Hand Tools Causes
Hazards From Improper Use of Hand Tools Causes
In this article, learn about the common hazards from improper use of hand tools, including the causes, potential risks, and practical steps to prevent accidents and injuries to ensure the correct use of hand tools, promote workplace safety, and minimise the likelihood of incidents caused by misuse or negligence.
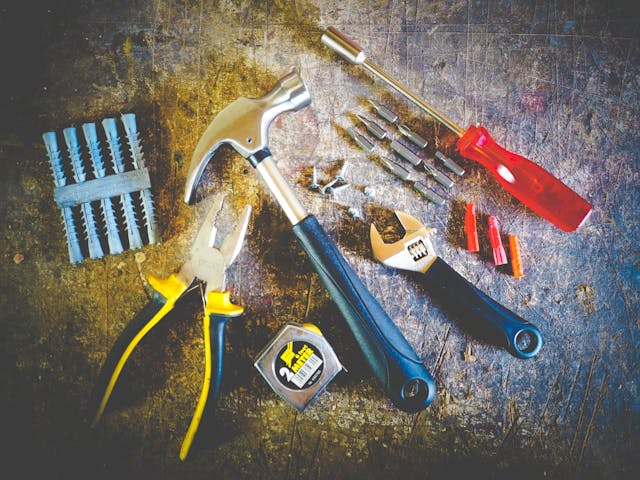
Why is it Important to be Aware of the Hazards From Improper Use of Hand Tools?
There are two types of equipment which has been essential in multiple industries worldwide. These equipments are the hand tools, which are tools we use manually, and power tools, which are electrically and battery operated. From then till now, these tools have helped workers finish jobs more efficiently and productively. These tools also protect workers from the danger when working with their hands, but sometimes the danger comes from using these tools. They can be a hazard when used improperly, which results in obstruction in production and company loss time. In this article, we will uncover the main hazards from improper use of hand tools causes.
What are Hand Tools and Power Tools?
Before we get into the topic, let us discuss first the difference between these two types of equipments. While most of the power tools are derived from hand tools, it is still essential to know where they differ and where they are mostly used. Knowing to use is these tools is the first step in protecting yourself from the potential hazards these tools bring.
Hand Tools
Humanity has progressed because we learned and crafted tools to help us in our daily lives. The earliest tools made were 3.3 million years ago in the Pliocene Epoch. These manually operated tools had made its way from hunting mammoths to different works in industries today like in construction, power plants, and industrial plants. These tools are simple yet flexible, which makes them easier to manoeuvre and use for extended periods.
Unfortunately, these tools are labour extensive, which consumes a lot of time and is dependent on human power. Some common examples of these tools are hammers, wrenches, screwdrivers, and manual hand pumps. These tools are safer to use than power tools, but that doesn't mean that the possibility of a hazard is eliminated.
Power Tools
Power tools were made around the eighteen hundreds. This was revolutionised to provide a solution to the rigorous and repetitive process of using hand tools. In the early years of its revolution, power tools were motor operated until 1961 where the first battery operated drill was introduced. Unlike hand tools, power tools are more specific and rigid in use.
They have the advantage compared to hand tools since they have more power and are faster. But, power tools are harder to control compared to hand tools. They aren’t also flexible in nature, since they were made to handle specific tasks. Misuse of power tools bring a lot of hazards, so it is important to stick to their work specification.
Why is it Important to be Aware of the Hazards From Improper Use of Hand Tools?
Awareness and knowledge of the hazards from these tools gives us an understanding on why we should stick to the parameters on how these tools are supposed to be used, and help us provide the appropriate measures to completely eliminate these hazards. Improperly using these tools could have dire impacts on company property and the human body.
Hazards could lead to muscle and skeletal damage that ranges from a minor cause injury to a surgical case, and sometimes even death. When these unfortunate things happen, this could cost a company operational disruptions leading to financial loss.
Additionally, using these tools the right way can help with promote safety in the workplace, which helps the company in complying with regulatory standards and avoiding any legal issues.
What makes these Tools Hazardous?
Poor Tool Maintenance
Tools need to be treated and cared for properly so that they can work effectively and efficiently. To properly take care of them is to inspect them, clean them, maintain them and place them in an appropriate storage that minimises the effect of corrosion. When a tool has poor maintenance, it could pose a lot of dangers. One of the most prominent dangers would be a tool malfunctioning.
This type of hazard jeopardises the safety of the user and the assets and workers around him. It is also important to note to not use tools that are defective. It is best to inform your superiors about this so that these can be replaced and avoid any unwanted injuries.
Wrong Tool for the Job
As humans, we tend to get a little creative when placed in a situation where the right tools are unavailable for a certain job. We often resort to using other tools which are not properly fit for the job but still does the job. Ingenious as this might sound, but this actually brings a lot of hazards. For instance, using a screwdriver to tighten a bolt.
The screwdriver can potentially slip due to low surface contact, and in the event you could potentially cut and stab yourself. In the process of using the wrong tool for the job, you not only injured yourself, but also damaged the tool.
Using the wrong tool also leads to poor quality work, since the wrong tools doesn't have the specific design to complete the job effectively. That said, using the wrong tool to complete a job is never really a smart idea since it leads to hazards and danger.
Lack of Proper Training
Danger doesn’t excuse anybody, especially if you do not possess the sufficient knowledge and skill to use a tool. Without proper training, it could exacerbate the risks of hazards in the workplace.
They might use tools in an improper way, which could lead to injuries and accidents.
Organisations, should also always conduct refresher courses in proper tools usage. This could help workers in their retention on how to use tools properly and effectively, while also promoting workplace safety.
Not Using or Wrong PPE
Personal Protective Equipment, or widely known as PPE, are smartly made to help us shield ourselves from the hazards brought by using hand tools and power tools. PPEs are a mandatory to be worn and are strongly mandated by the safety regulations worldwide.
To avoid accidents, it is life-saving to make sure that the PPE used is free from defects. To maintain their job in protecting us from harm, they should be maintained and cleaned at all times. It is also important to make sure that workers should wear the appropriate PPE at all times.
There are PPEs made for a specific reason to help us protect ourselves from the injuries when we accidentally make a mistake. For example, rubber gloves are for hand held works like sawing and hammering, which protects the worker when they accidentally hit their hand. Chemical gloves are for handling chemical products, which protects the worker from accidental spills. Failure to wear PPEs and failure to use them for the right situations compromises the safety of the worker.
Best practice when it comes to knowing the most appropriate PPE is to perform a PPE hazard assessment, which you can read more about here.
Poor Environmental Conditions
Poor working conditions like in environments that are excessively dusty, wet and high temperatures are already a danger itself. Working with hand tools and power tools further increases the danger in these areas. Wet environments increase the risks of slips and electrocution. Dusty places, obstructs the vision when the dusts are disturbed. And, extreme temperatures increases fatigue. Training also inculcates workers to be proactive. They can anticipate problems and actively use
Fatigue and Human Error
Human as we are, there will always come a point in our work where we get tired and weary, therefore, we need to rest and energise before working again. If a person doesn't rest, it increases fatigue. F
atigue can contribute negatively to a worker’s ability to safely use hand tools, so it would be helpful to take breaks or have a worker replace the job.
There are a number of commonly used fatigue management strategies which can help mitigate this hazard, including fatigue management reports.
Mitigating and Eliminating the Hazards
Training
Most of the causes mentioned above can be resolved with proper training. Training helps workers understand the correct and proper way of using hand and power tools safely. This helps in promoting a safe work environment, which helps companies boost their reputation. Tools are always evolving, especially the power tools. It would be beneficial if the knowledge and skills of the workers would be in line with the latest updates in technology. That is why refresher courses or upgrade training would help workers upskill and boost efficiency and safety in the workplace.
Safety Audits and Feedback Sessions
Conducting safety audits regularly is good practice. During these audits, safety officers will observe how workers use the hand tools and power tools, after which they will provide feed back on the positive things they saw and things the workers need to improve on. This is typically documented via a Safety Audit Checklist. Following the audits, they should also hold feedback sessions to discuss findings and further improving ways in tool handling practices.
Ensure that you document any strategies that you implement. The use of hand tools are always dependent based on the project work scope and technology advancement. You will need to review your strategies in the future to ensure they are still adequately protecting workers.
Safety Talks
Toolbox talks are an effective method for keeping your workers aware of the causes of hazards from improper hand tool use. Consider using a toolbox talk to discuss the safe use of hand tools.
It is designed with all the required sections to hold an effective meeting on the topic. You can detail all your discussion points, record any safety issues raised, assign action items, and take meeting attendance in the one form. You can also add photos and other attachments and customise it to suit any further requirements.
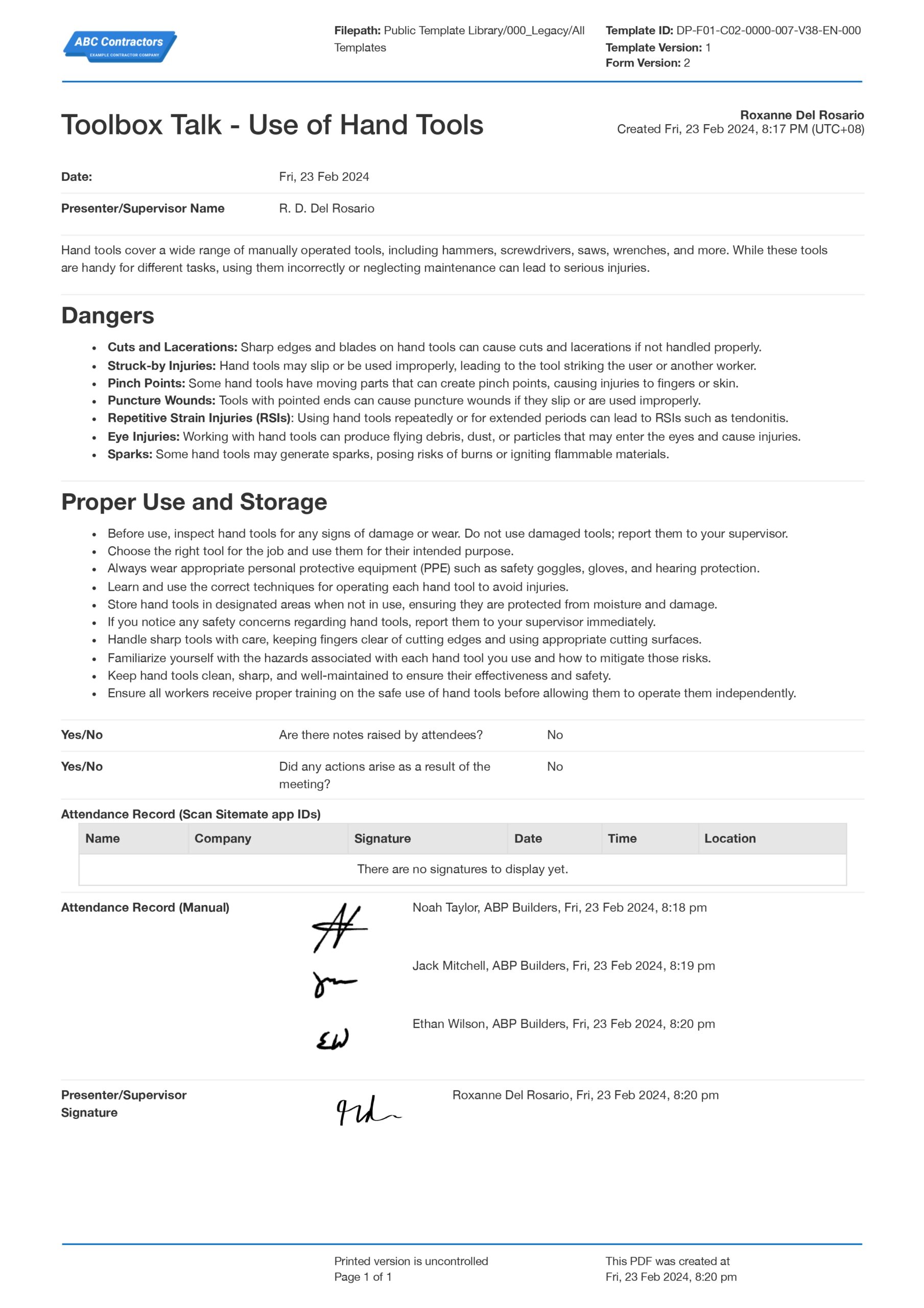
Summarising How to Deal with Hazards from Improper Use of Hand Tools
Hazards are the tradeoff we have to except when using many types of efficiency gaining assets, whether that be something simple like a power tool or something potentially life threatening like an excavator.
These tradeoffs are typically worth it, when good safety practices are applied around the usage of these equipment.
In this article, we have tried to make you more aware of the specific hazards from improper use of hand tools causes, as issues and incidents stemming from these hazards are avoidable, as they stem from improper use.
Making your team/s aware of these hazards can have a big impact on reducing incidents and injuries, and so can ongoing training and risk assessment.
Like all things with safety, it's really about a holistic approach to ensuring work gets done, but that it gets done with safety front of mind.
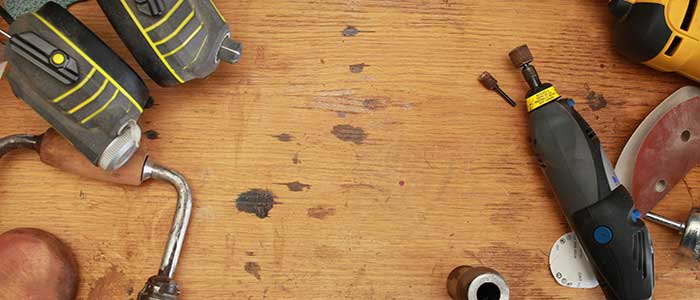
Safe Work Method Statement for Power Tools template
Power tools pose a constant hazard and risk to many workers. Ensure everyone is using and managing power tools properly with a good SWMS.
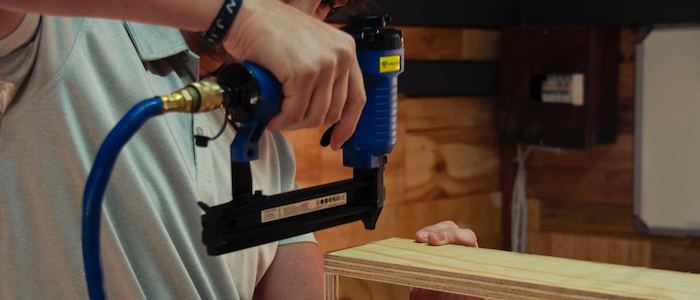
Job Hazard Analysis for Carpentry template
Keep carpentry work safe from hazards and risks with the Job Hazard Analysis for Carpentry template.
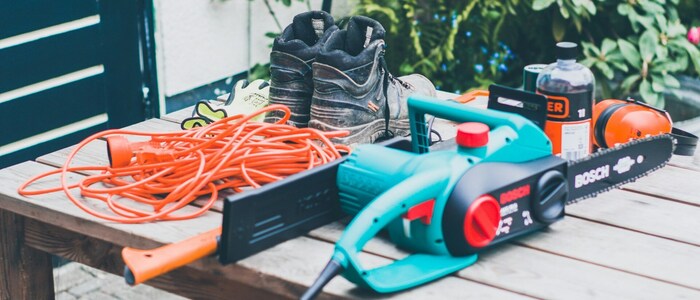
Extension Cord Safety Toolbox Talk template
Avoid incidents involving extension cords, tripping and electrical hazards with this Toolbox Talk template.