Safety – Job safety analysis examples
JSA examples: Use these job safety analysis examples
In this article, we provide you with a number of Job Safety Analysis examples, as well as more detail and resources about JSAs so that you know exactly how to stay professional and compliant with your JSAs.
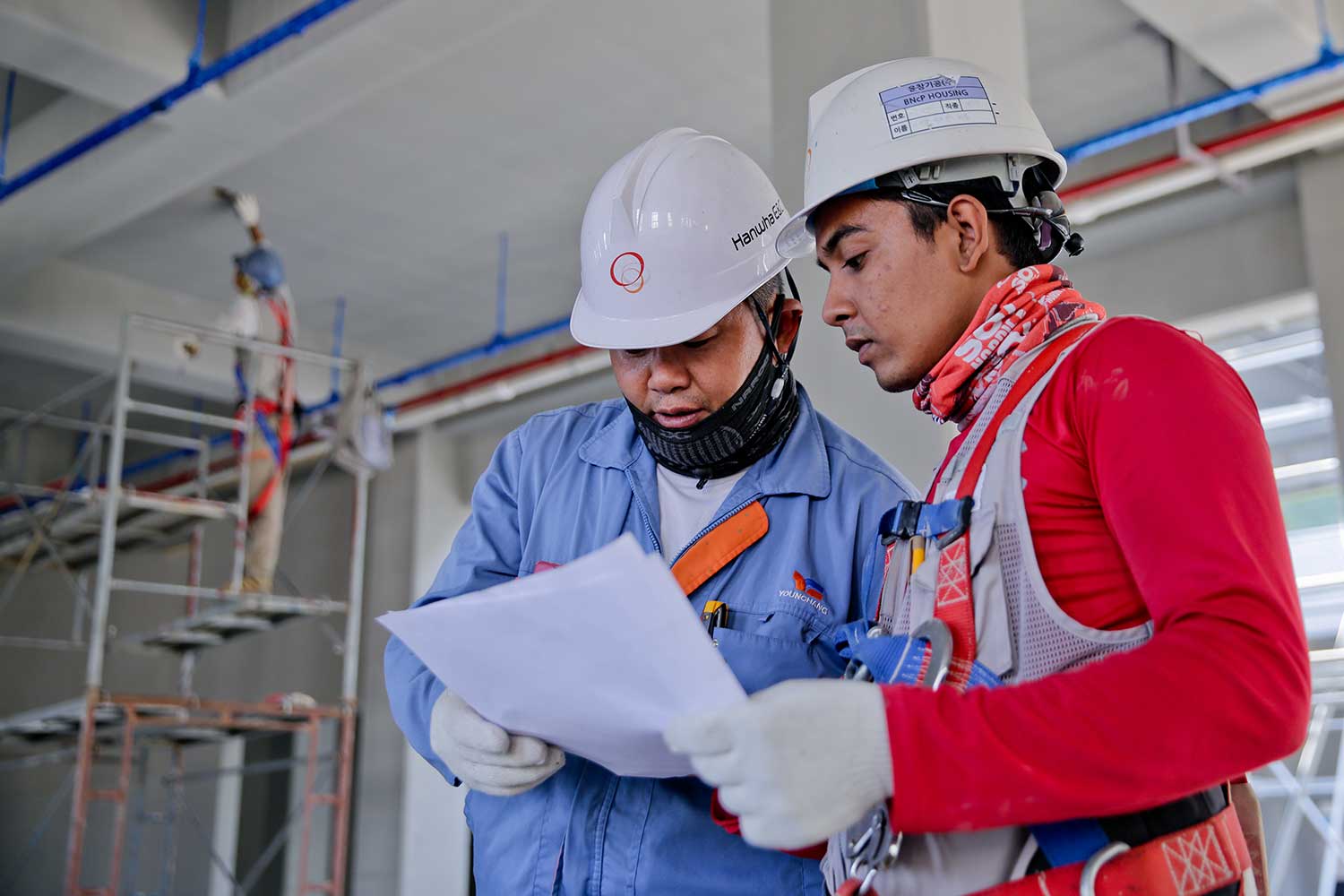
JSA examples
Below, you will find two JSA examples.
One of the JSA examples is for a construction worker and construction activity, and the other example is of electrical work.
You'll note that both examples share the same characteristics and the same framework. Construction and other industrial companies can often use a single JSA framework for all of their JSA's, with each job or task only including slight variations in its makeup.
Job safety analysis example for construction
Job safety analyses are very common place on construction sites because construction work is fraught with safety issues and potential hazards and incidents.
It doesn't make sense to create a JSA for every single piece of work conducted on a construction site - even when most things do carry some inherent danger.
Construction permits - which are created for many high risk construction activities - often take care of the JSA's job by requiring a high level risk assessment and job safety analysis.
But other construction activities and general phases of work may require a JSA, and they may be encouraged in addition to other documentation where instructed.
Take a look at the construction example below to see how the days activities align with the safety analysis performed, and how the analysis of activities and the resulting 'scores' given to each step of the job are intended to help people understand and prioritise safety.
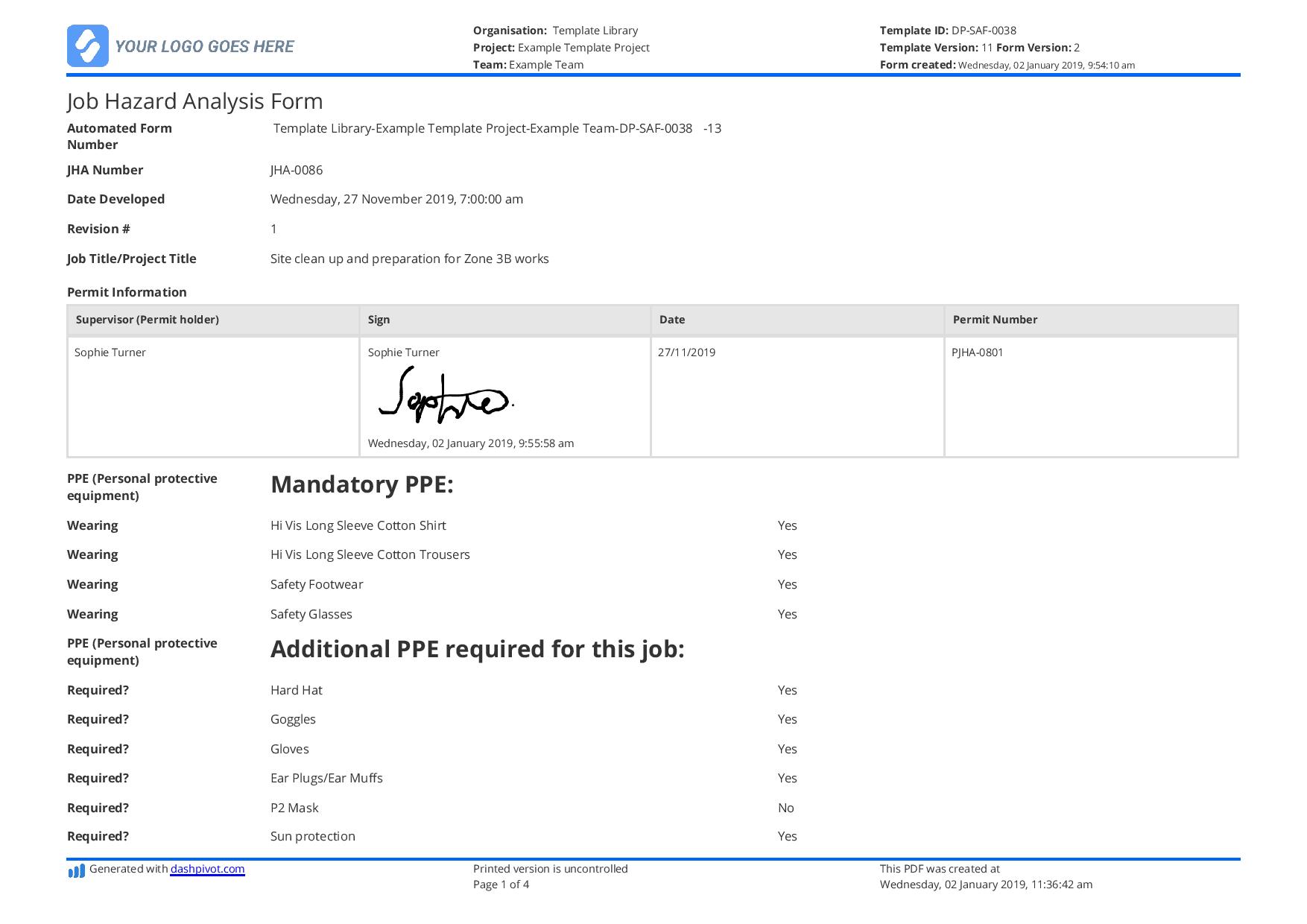
Use this job safety analysis example form for free.
JSA example for electrical work
Electrical work is another area of the industries where workers face a constant threat to their safety. Once again, specific electrical permits and hot works permits may cover some elements of a job safety analysis form - but as is often the case, this example form is looking at the working environment holistically.
This electrical example includes a number of activities involved in performing electrical work in a hazardous area. A JSA is required to cover the steps involved in the days or activities work - as well as the PPE which is universally applicable to this hazardous area.
Different workers can engage with safety in different ways, and it's up to the company to set the procedures, standards and expectations of which which safety processes are required for what work.
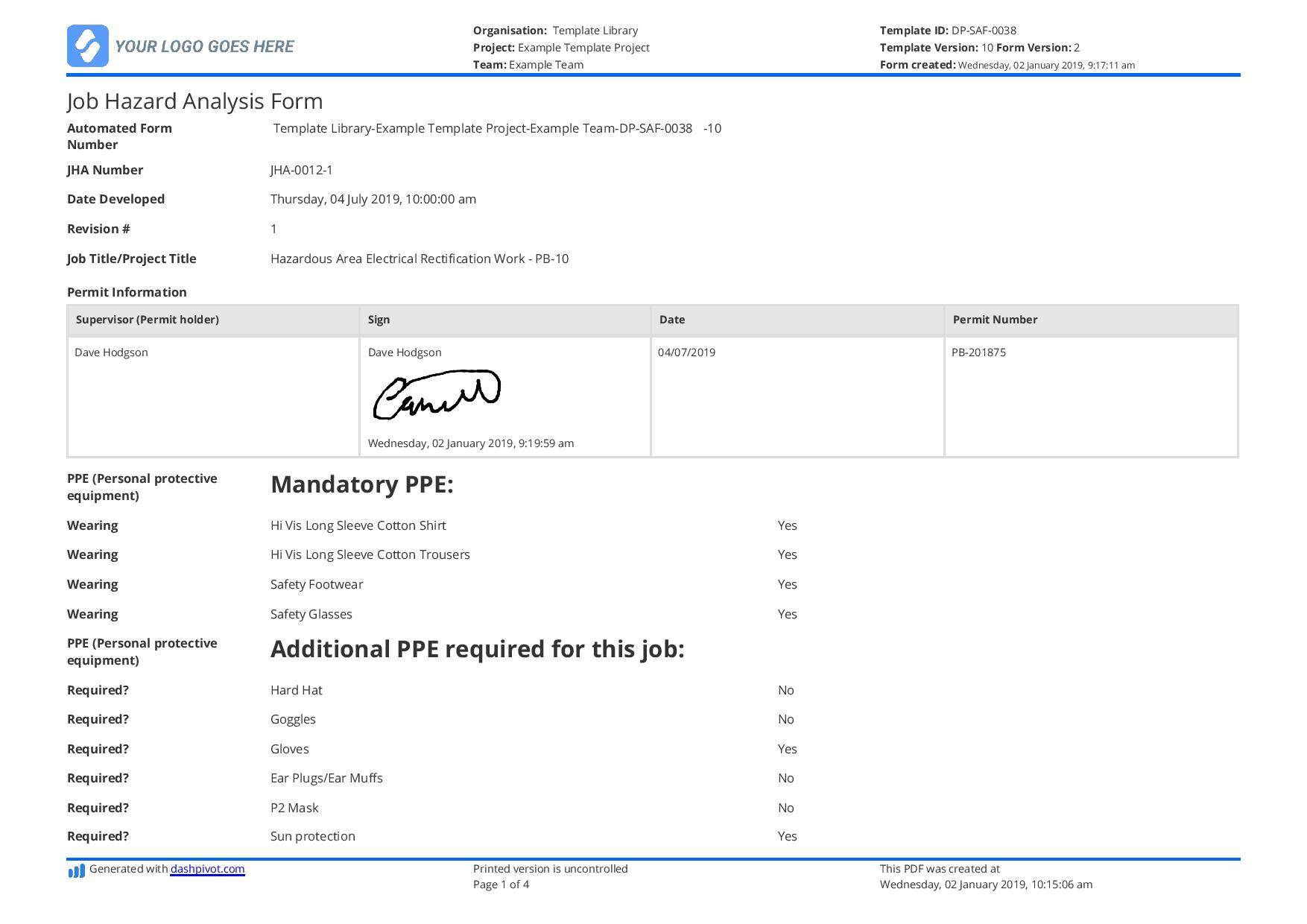
Use this JSA example for your electrical works.
The simple framework you see in the examples above follows a simple format:
Important JSA record keeping information
JHA number
Date developed
Job title/project title
Permit information (where applicable)
Personal protective equipment (PPE)
Mandatory PPE
Additional PPE required for this job
Additional references for this job
e.g MSDS or hazard register
Risk matrix
Job or tasks steps and their associated safety analyses
What is a JSA?
A JSA or job safety analysis is a procedure (usually conducted with a JSA form) which describes the steps required to complete a specific task or job - and then identifies potential incidents and hazards which could arise during the course of this task or job.
The purpose of a job safety analysis is to proactively consider and outline what could go wrong and what safety issues could arise during the course of work, with the goal of reducing the likelihood that these hazards and incidents will eventuate through risk control measures and prioritisation.
A job safety analysis - also referred to as a job hazard analysis (JHA) and sometimes rolled into a risk assessment - can be conducted and used by any workers in an industry, but the most common use case is for industries like construction, oil and gas, mining, forestry etc.
These industries face very real safety issues every day, and workers within these industries need to be constantly vigilant of potential hazards and incidents as well as constantly assessing the relationship between themselves, their tools and the surrounding environment.
Types of work including construction and electrical also work on a specific site and project basis, so every day and piece of work differs from the previous. While some of the tools and processes remain the same, each project or site has a set of unique characteristics and set of challenges which need to be factored into a job safety analysis.
A job safety analysis can be conducted in a multiple ways:
- A JSA can be filled out by an individual prior to conducting work
- A JSA can involve a person or group of people observing and documenting someone else perform the job or task
- A JSA can be completed through a group discussion - whereby everyone comes together to perform a thorough 'risk assessment' of sorts based on that specific activity
Why is a job hazard analysis important?
Job hazard analyses are an important tool for workers and companies alike.
For companies, worker safety has become more and more important, as any incident or safety issue today is highly scrutinised. The expectations for workers and the public is that people come home the same way they went to work - safe and sound. Making JSA's a requisite part of performing jobs which involve higher than normal risk mitigates the likelihood and severity of avoidable incidents - which impacts the reputation and bottom line of companies.
For workers, the JSA serves as a frequent check and balance on the complacency which naturally creeps into workers' minds when they do a specific type of work or are exposed to a consistent environment. Workers can often go into autopilot when performing similar tasks, but slight variations and changes in fatigue, focus, the environment and other variables can have a dramatic impact on safety.
There are a number of tangible benefits which workers and companies derive from performing a job safety analysis in any of the above formats:
- Performing a job safety analysis prompts the recognition of hazards which otherwise would have been ignored or overlooked
- Job safety analyses surface undetected hazards and incidents over time which lead to increased personal, job and company knowledge over time
- Making JSA documentation a required part of performing certain works improves communication between workers on site and safety teams or management in the office - who may not understand or recognise the risks associated with a particular task
- Companies keep detailed records of safety processes which can become extremely important in the face of an incident or audit
JSA's are extremely important for for any high risk activities - and many companies who always operate in a high risk environment such as around explosive materials or gas require a job safety analysis for any work performed.
Improving how job safety analyses are completed, organised and actioned
Safety is the priority for all people and for all companies. The problem with job safety analyses and all of these proactive and reactive safety processes and documentation is that they do take time away from moving projects and work forward.
Finding the balance between conducting work safely and not swamping yourself and your team in red-tape and safety information is important. You want to keep everyone safe, but you also need to get the job done.
There are a number of steps you can take to improve the efficiency and organisation of your safety documents and efforts - and one of the most obvious in 2019 is to digitise how your safety analyses and other processes are captured, organised and actioned.
We've seen many companies and workers maintaining thick binders and folders of their job safety analyses. Using paper-based methods to document JSA's results in a few problems:
- Companies don't have oversight or insight into the JSA's being completed and how well safety is being managed
- Workers lose interest in JSA's as they become a tick and flick exercise, because they are not held accountable to what they are doing and it appears that no one is looking at them or caring
Using software to manage your safety and JSA processes means that all of your information is standardised and stored securely in one place.
Workers on site access and complete their JSA's (on computer, mobile or tablet), and then all of their records are instantly uploaded to the cloud. Project managers, management and safety teams can then see the JSA's which have been completed, action specific items and sleep soundly knowing that their safety records are secure, searchable and audit proof.
Organising your safety processes in the right way saves time - and also results in continuous safety improvement for your workers and your company.
You can get started with a digital form below to try the software for yourself, or learn more about JSA software here.
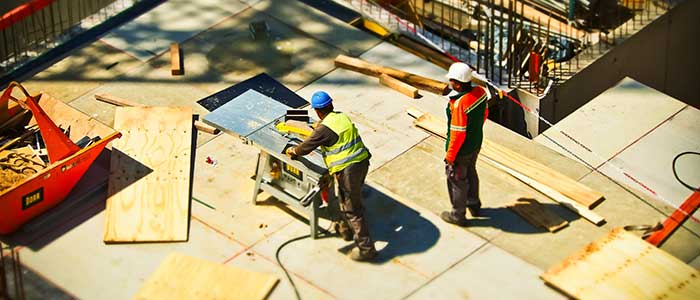
Job Safety Analysis (JSA)
Make JSAs easier to complete on site for your teams
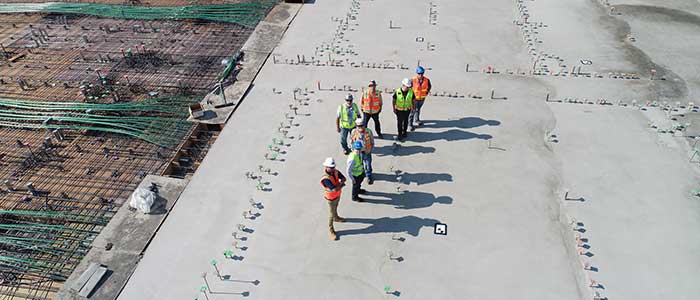
Toolbox Talk
Capture, record and organise those meeting minutes.
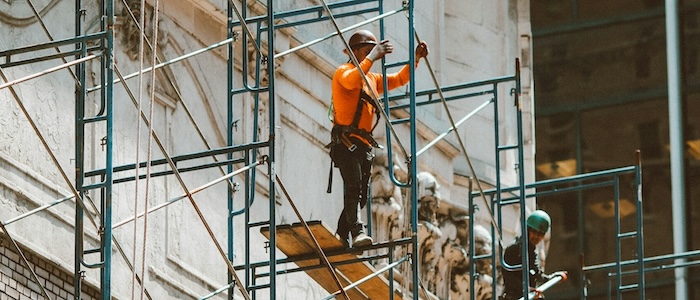
Working at Heights Permit
Know that you are working at heights compliantly