Here’s why lean construction techniques still can’t scratch the surface
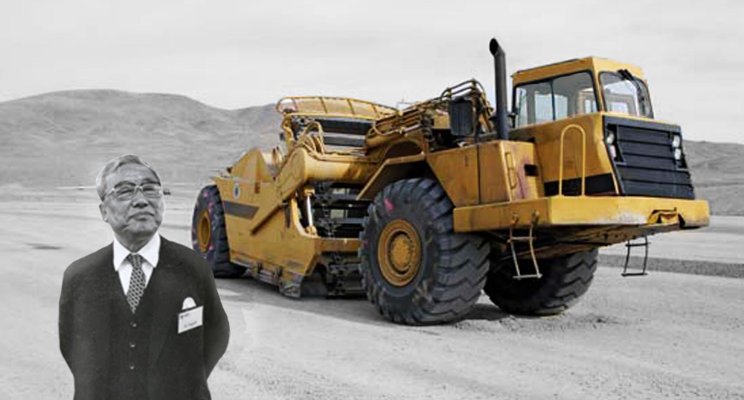
Here's why lean construction techniques still can't scratch the surface
Taiichi Ohno
'Stand in that circle and watch the process.'
Engineering Manager
'Here?'
Yes.
Now what?
Think for yourself.
How long for?
Until you see it.
See what?
The waste.
The waste?! I’ve watched this process thousands of times, I would see it straight away!
My feet did not move for the next 8 hours…
~The Toyota Way, by Jeffrey K Liker
An Ohno Circle, named after Taiichi Ohno.
Experienced managers stand on the inside of a circle painted on the ground of their facility. This process can last for hours on end - the goal is to gain a deep understanding of how your process works.
Researching lean construction techniques revealed complex planning tools.
Then I read The Toyota Way, and it confused me.
Why was implementing lean principles in the construction industry so complex?
Why hadn't anyone focused on what happens at fundamental process level?
Pouring concrete, steel fixing and pipe laying - why fundamental process level?
In manufacturing, lean principles originated here.
Down to the second:
Bolt tightening.
Thread tapping.
Washer placing.
As a civil engineer, it made me question the source of lean thinking in our industry.
The measurement of standard production processes in minutes and seconds acts as Toyota's foundation for continuous improvement.
A ‘fresh set of eyes’ allowed me to mirror Ohno's approach without subconscious bias.
Applying the Ohno circle to civil construction processes lead to remarkable results.
Disclaimer: this article does not suggest that benefits from applying lean in construction top down do not exist. It argues that lean must come from the ground up to make a meaningful and sustained impact.
For those who read BIM Has Reached The Final Frontier, And Is Losing The Battle [800 reads], this article follows a similar bottom up + missing link theme.
Rewind a second again, Hartley!
What the hell do lean principles have to do with construction?
Ok, before we look at:
Why lean construction can't scratch the surface
Proof that an alternative application works
What we can do about it
Let's dive into Toyota's not so secret for success...
Taiichi Ohno and Eiji Toyoda developed 'lean' principles between 1948 and 1975. They created a framework for their manufacturing shop floor observations, and this framework grew into the Toyota Production System (TPS).
TPS has been the foundation for Toyota to grow Earnings Per Share from $32.19 in the 1990s to $160 this year.
Manufacturing since 1994;
Productivity (value added per worker) has nearly doubled.
Traditional construction project management theories were first scrutinised by Lauri Koskela in 1992. Koskela challenged the time | cost | quality trade off paradigm. In 1994 Glen Ballard defined a project as a temporary production system. Ballard placed a new emphasis on managing variability throughout a project’s lifecycle.
The 'Lean Construction' term followed these investigations, which originated from academia.
Construction since 1994;
Productivity (value added per worker) has either gone down or flatlined.
UPFRONT APOLOGY.
Sorry for including this McKinsey graph - you've probably seen it before.
And also for those who read Project Directors Suppressed By Gantt Charts Want Dashboard Analytics [400 reads] - sorry for another McKinsey reference.
But, the writing is on the wall.
1. Here's Why Lean Construction Techniques Can't Scratch The Surface
This article argues that a disparity exists between the origin of lean principles in manufacturing when compared against the origin in construction.
For evidence supporting an alternative application framework see point 2 below. This alternative framework matches Taiichi Ohno's early work on the shop floor.
Ohno did not hypothesise.
Ohno did not have a career centred around academia.
Ohno transitioned from a shop-floor supervisor to a businessman in his later years.
Ohno actioned issues immediately and made measured adjustments with continuous workforce engagement.
Walking the shop floor endlessly. Searching for process steps that did not add value from the customer’s perspective.
Lean should be bottom up.
‘Lean Construction’ gained support by many professional institutes across the globe as a flow on from early academic research.
These institutes rely on a range of engaged members, private sponsors and consultants.
No driving force exists within the industry.
We are missing Ohno's framework.
Down to the second:
Pouring concrete.
Tying steel.
Laying pipe.
'Lean Construction' is top down heavy.
Contrasting these two approaches reveals the disparity.
The honest question that we need to ask ourselves is;
How many people involved at fundamental process level are aware of lean principles?
What about the lean tools we have at the moment?
The tools, theories and processes associated with the lean body of knowledge include:
- BIM [Building Information Modelling]
- LPS [Last Planner System]
- Modular Construction / Building
- Yet, tools, theories and processes do not equate to instant culture change.
Below the success, the manufacturing industry holds a graveyard of failed lean implementations.
These failures occurred due to implementation of stand alone tools without culture change.
Short term gains die down when champions and consultants leave. Old habits remain and the underlying culture does not change.
Referring to an annotated page from the Toyota Way below:
Lean construction techniques can't scratch the surface and experience widespread adoption because the current application framework sits at the top of the iceberg.
But factories create controlled environments for manufacturing work, and we deal with many variables during construction project work - including the natural environment. Can you compare these industries?
It's true, manufacturing is different to construction. But manufacturing and construction do have a lot of similarities.
What if we stripped lean back?
What if we started in exactly the same way that Taiichi Ohno did on the shop floor?
No complex tools project management tools. But an alternative mindset.
And a stop watch.
2. Here's Proof That An Alternative Application Works
Using the Ohno circle, my construction process was broken into various components. Value-adding, non-value adding and waste components were measured.
We tested it - live.
Changes made based on empirical data, collected hand in hand with the work crews.
Lean Construction Testing Results
30% reduction in process time. Safety and quality unchanged.
The most remarkable part - a single team without any lean training or qualification completed this experiment.
And it lasted only 8 weeks.
Imagine the impact over 3, 4 or 5 years on a multi billion dollar mega project...
How many unnecessary productivity hours are being burnt on your site today?
Do you have a construction project dashboard to measure your construction key performance indicators?
3. Here's What You Can Do About It
Educate. Educate. Educate.
Motivation must come at the level of the individual - light bulb moments.
Smart phones, cloud technologies and improved equipment - none of them have changed the McKinsey productivity graph.
BIM, AI, IoT, blockchain and all other hot topics will come and then pass on.
None will have as great of an impact as culture change at fundamental process level.
Culture change will take leadership from unexpected sources, education and a powerful message.
Personal experience at fundamental process level is a prerequisite to the application of lean principles in construction.
Deep process understanding coupled with education - the recipe for success.
The parting question:
How can technology support massive open education and positive cultural change?
If I have seen a little further it is by standing on the shoulders of Giants.
~ Isaac Newton
Key takeaway: benefits exist through the application of lean tools, theories and processes from the top down. But, for this body of knowledge to become habit the application needs to originate from the field. We will see similar improvements in our industry when we start thinking bottom up.