Dashpivot Article – What is a Facility Condition Assessment?
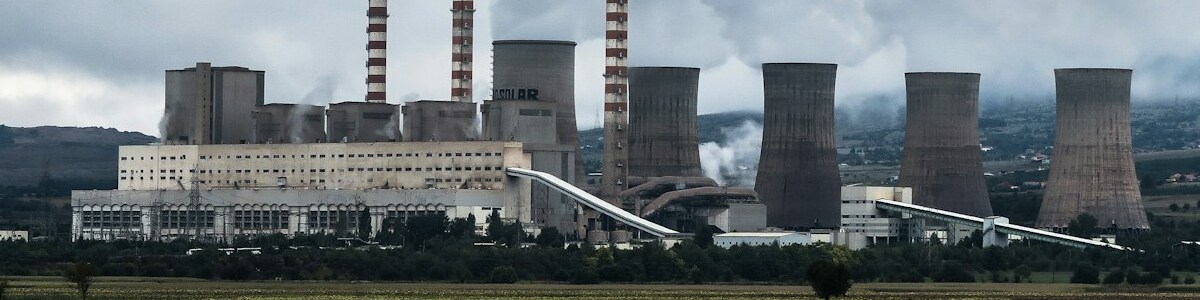
What is a Facility Condition Assessment?
Do you remember the last time a critical system in your building failed-for example the air conditioning shut off during a heatwave or that mysterious leak turned into a full-blown plumbing disaster? These are not just inconvenient; they are wake-up calls that remind us how important it is to really know the health of our facilities. This is where Facility Condition Assessments, or FCA's, come in, which is why we are setting out to answer the question of what is a facility condition assessment in this article.
These assessments are like a check-up for your building, helping to find problems before they become costly catastrophes and allowing facility managers to address these issues before things go really wrong, just like medical checkups can catch health problems before they get serious. Industry data shows this proactive approach isn’t just smart- it’s cost-effective, with regular assessments helping organisations cut unexpected repair costs in half.
As you read this article you will be going through each step of doing an FCA-from building the right team of experts to using modern technology to get more insight. Whether you manage one building or multiple facilities you will find practical tools and strategies to turn complicated inspection processes into simple, actionable steps. This will be your guide to doing facility assessments, a guide that will take you from reactive maintenance (fixing things when they break) to proactive management (dealing with problems before they become issues. The best part? We will be showing you how to do it all with digital solutions.
What is a Facility Condition Assessment?
What is a Facility Condition Assessment (FCA)? An FCA is a critical tool for understanding the health and operational capacity of physical assets in industries that require high durability and reliability from their infrastructure. This involves a detailed examination of a facility’s systems and components including but not limited to its structural integrity, mechanical, electrical and plumbing systems, safety features and interior and exterior conditions.
By doing an FCA stakeholders get insight into the state of their facilities. FCA's identify existing deficiencies, maintenance requirements and potential compliance issues that can impact operational efficiency or safety. In industries with lots of infrastructure and high capital investment, the importance of an FCA can’t be overstated.
These assessments provide a basis for informed decision-making and allow for prioritisation of maintenance, renovations and upgrades to keep facilities running. An FCA also helps with risk management by identifying areas that pose risk to personnel or could cause significant operational disruption if not addressed.
FCA's also play a key role in long-term planning and resilience in infrastructure-heavy industries. By understanding the life cycle of facility components and infrastructure organisations can plan for replacements and upgrades in advance, minimize downtime and ensure operations meet industry standards and regulations. When physical assets impact the bottom line this foresight is critical.
How to do a Facility Condition Assessment
Doing a Facility Condition Assessment (FCA) requires a structured approach to cover all critical components and systems in a facility. Here is a process outline for doing an FCA:
Planning and Preparation
Define the scope of the assessment and which facilities and systems will be assessed. Gather existing facility documentation such as blueprints, previous assessments, maintenance records and compliance reports. Set clear objectives for the assessment to guide the whole process to ensure it meets the specific needs and goals of the organisation.
Building the Right Team
An FCA requires a multidisciplinary team of experts that can include engineers, architects, safety specialists and maintenance personnel. Each brings specific knowledge to ensure a comprehensive evaluation of structural, mechanical, electrical and safety systems. External consultants may be engaged for specific expertise.
On-Site Inspections
The core of the FCA process is the on-site inspection of the facility.
Segmentation
Divide the facility into smaller sections or zones based on function, system type or location. This will ensure thorough coverage and help with the inspection process.
Checklists
Use detailed facility condition checklist templates for each area and system being checked. These checklists should cover all components to be checked including structural, HVAC, electrical, plumbing, safety systems and any specialised equipment related to the facility’s operations.
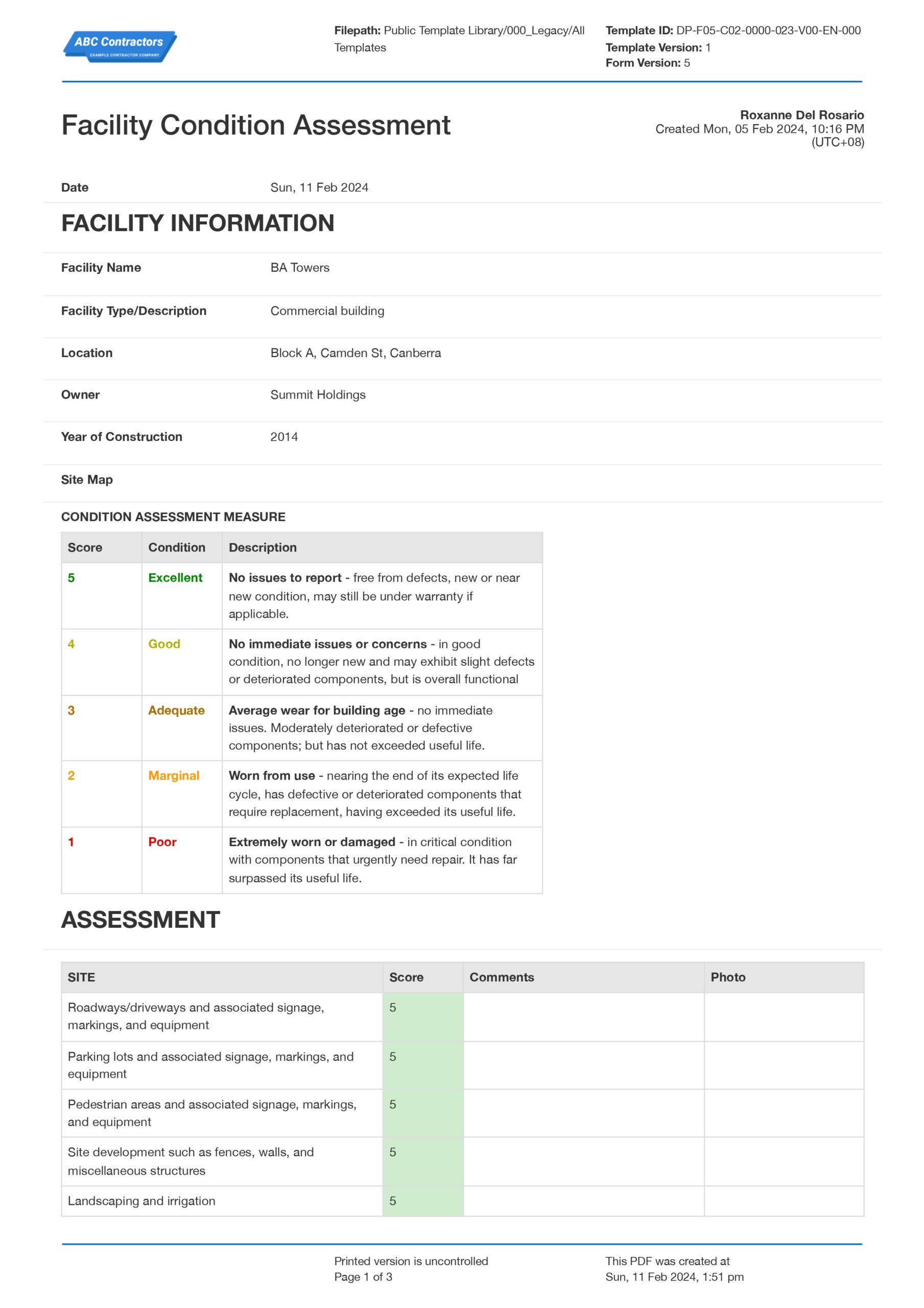
Use and customise this free facility condition assessment form
Visual and Functional Testing
Start with a visual check, and look for obvious signs of wear, damage or decay. This includes checking for cracks in structural, water damage, corrosion on electrical and the condition of moving parts in mechanical systems.
After the visual check perform functional testing on systems to test their operation and detect hidden problems. This may include testing alarm systems, and checking that HVAC units are working, electrical systems are grounded and circuits are intact.
Technology
Use technology such as thermal imaging cameras, moisture meters and structural scanners. These tools can detect problems not visible to the human eye such as overheating electrical components, moisture behind walls or hidden structural weaknesses.
Recording and Data Collection
-
Documentation: Documentation is key at the on-site inspection. Notes can be taken using digital tablets or smartphones, and photos and videos taken of issues found. All findings should have a location identifier so that data can be linked to the area or system it relates to.
-
Condition Rating: assign a condition rating to each of the components or systems based on what was seen and functional testing. Ratings are usually excellent, good, fair and poor and help to qualify the severity of the issue and the overall condition of the facility’s assets.
-
Data Organisation: Organise the data collected during the inspection in a logical order according to the section on the checklist. This will help in the analysis phase and make it easier to see trends, identify problem areas or prioritise issues.
-
Immediate Feedback Loop: If it finds critical issues that pose an immediate risk to safety or could cause major disruption to operations, the report of these issues goes straight to facility management so action can be taken to mitigate the risk before the full report is completed.
Analysis
Documentation: Documentation is key at the on-site inspection. Notes can be taken using digital tablets or smartphones, and photos and videos taken of issues found. All findings should have a location identifier so that data can be linked to the area or system it relates to.
Condition Rating: assign a condition rating to each of the components or systems based on what was seen and functional testing. Ratings are usually excellent, good, fair and poor and help to qualify the severity of the issue and the overall condition of the facility’s assets.
Data Organisation: Organise the data collected during the inspection in a logical order according to the section on the checklist. This will help in the analysis phase and make it easier to see trends, identify problem areas or prioritise issues.
Immediate Feedback Loop: If it finds critical issues that pose an immediate risk to safety or could cause major disruption to operations, the report of these issues goes straight to facility management so action can be taken to mitigate the risk before the full report is completed.
After the on-site inspections, the analysis phase is where the raw data is turned into usable information. This phase looks at the condition of each facility component, the severity of the issues found, the impact on operations and what maintenance is required now or in the future. The condition ratings assigned during the inspection are a quantifiable measure of the component’s health and will guide the prioritisation of repairs and maintenance activities.
Analysis involves estimating the remaining life of the components which is key to strategic planning and resource allocation. By knowing which components are reaching the end of their life facilities can schedule replacements or refurbishments and mitigate the risk of unexpected failures that could impact operations.
Repair and Maintenance Prioritisation
Based on the analysis create a list of repair and maintenance recommendations in priority order. Prioritisation is usually based on factors such as the component’s criticality to facility operations, its condition and the risk or impact of failure. This is important for resource allocation so the most critical and impactful issues are addressed first.
Long-Term Capital Improvement Plan
The final step is to use the data collected and the insights gained from the assessment to develop a long-term capital improvement plan. This plan should outline the maintenance schedules, repairs, upgrades and replacements over a set period. It will be a roadmap to ensure the ongoing reliability, safety and efficiency of the facility taking into account future growth and technology.
When doing a facility condition assessment it’s best to use a standardised checklist with a consistent measure for each section. Below is an example of a facility condition assessment that has been done using a structured checklist:
Digital facility condition assessments
Facility condition assessments involve a lot of information and data. While using standardised checklists gives your inspections some structure, individual documents become unmanageable as an organisation grows. It’s also hard to distribute checklists to all stakeholders when using individual documents.
To make the process of doing, distributing and analysing facility condition assessments easier use a facility condition assessment app to manage all your assessments. This app allows you to create and conduct all your assessments digitally and store them in one place. You can send digital copies to stakeholders through the app and print hard copies if needed.
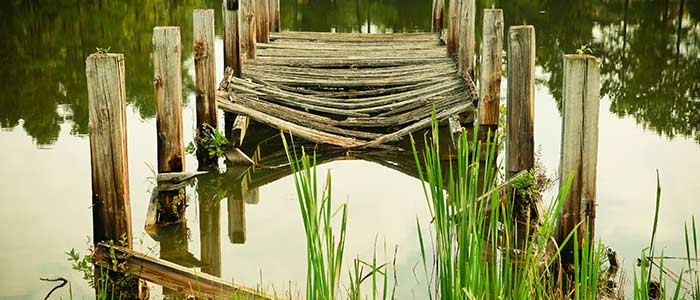
Dilapidation report template
Record and monitor the condition of exisiting assets efficiently.
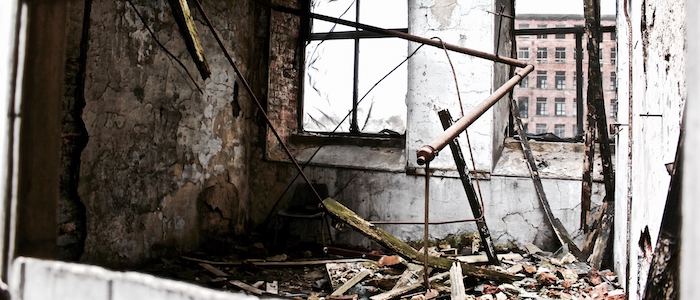
Existing Conditions Report template
Properly document conditions before any work is undertaken to build full photographic evidence.
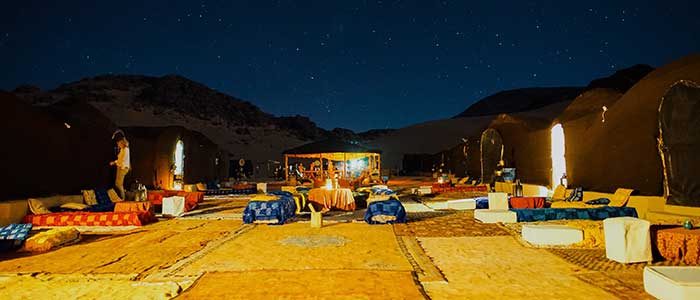
Site Observation Report template
Capture everything from those site observations in an organised and easily shareable form.