Safety – Hazard reporting procedure
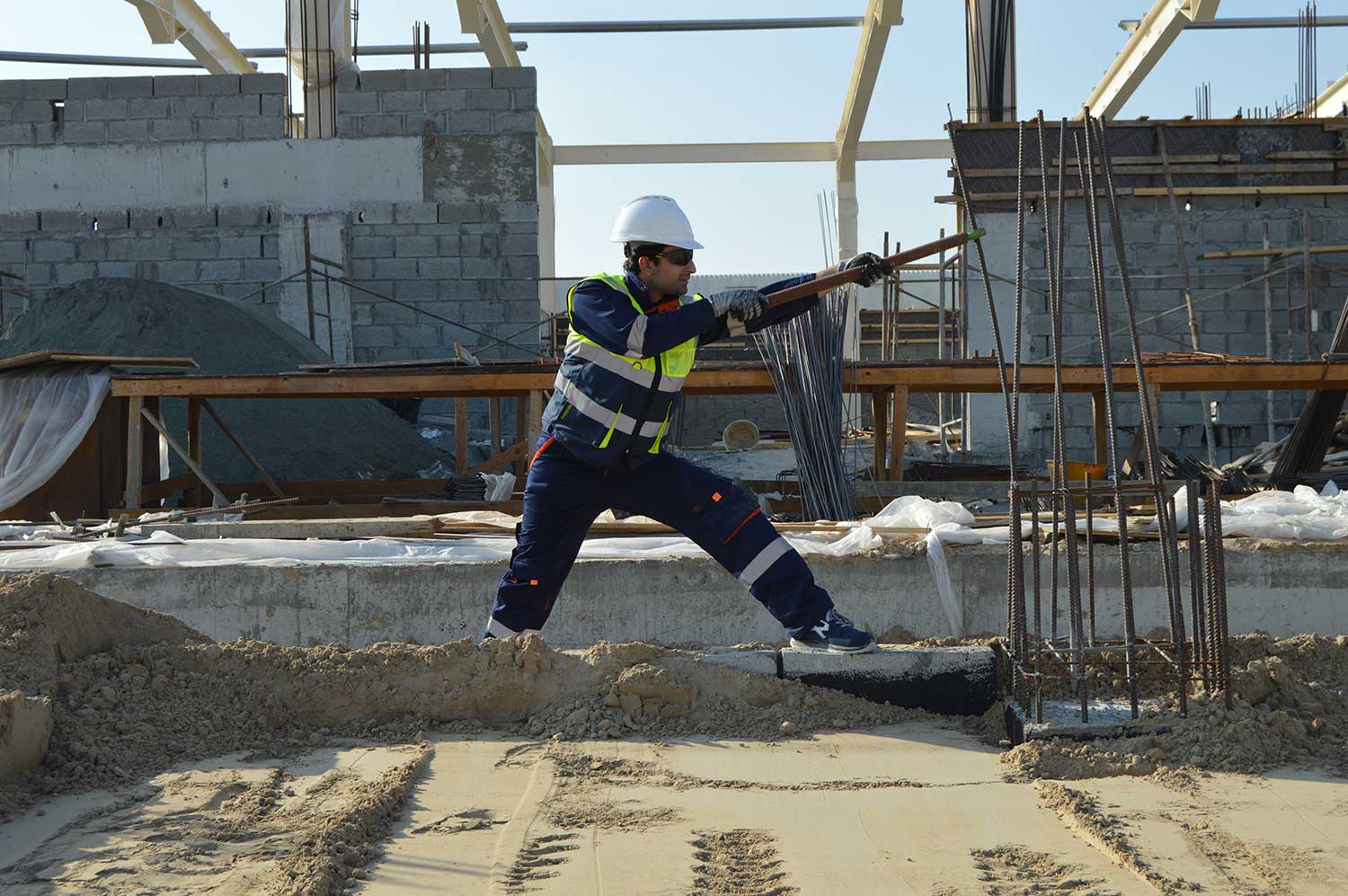
Hazard reporting procedure: The right procedure for you
Why is your hazard reporting procedure important?
Your hazard reporting procedure is your first line and one of your most important lines of defence when it comes to workplace safety.
Lots of companies and people focus on incidents and lagging indicators when assessing safety performance and safety KPI's, and they fail to place a large enough onus on critical leading indicators like hazard reporting.
There are two main bottlenecks for every company or project when it comes to reducing risk and preventing hazards:
- The friction and effort associated with documenting a hazard
- The friction and logistics of information passing from site (or any workplace) into a place where it can be properly assessed and actioned
A good hazard reporting procedure negates many of the issues associated with these two bottlenecks by (1) making it easy for people to document hazards, (2) streamlining the flow of hazard reporting information and (3) aggregating and displaying that information in such a way that a person or people can make informed decisions about what to do about those hazards.
Without a good hazard reporting procedure, hazards will get ignored, documented hazards will get misplaced or lost, and more hazards will turn into incidents which could have been avoided.
The mechanics of your hazard reporting procedure isn't the only way to affect how hazards are reported either. Even if it is incredibly easy for people to document hazards, they still must feel comfortable taking the time to do so - which comes back the culture of safety which you have built at your organisation.
In addition to having the right tools and procedures in place, you also need to develop the right culture on site and in the workplace where workers feel the need to document hazards - even if they aren't obviously serious or urgent.
But for our purposes today, we are going to focus on the actual hazard reporting procedure, what a good one looks like, and how to implement the perfect procedure for you, your projects and your teams.
The best hazard reporting procedure starts with...
In today's workplace, the best hazard reporting procedure starts with digital tools. The main issue with most ineffective hazard reporting procedures is that they are premised on paper forms, PDFs, excel spreadsheets and emails back-and-forth.
Managing a hazard reporting procedure using these rigid tools and slow communication methods is a recipe for disaster.
At the site level, workers need to actually find and grab a piece of paper and fill it in on site or remember to fill in a hazard report back at the office.
Once documented, this hazard report must then be scanned and uploaded and then emailed to a safety manager or responsible person.
And once it gets here, it must be re-formatted and transferred to a tracking sheet like a risk log or risk register where it can be assessed next to other risks and the right mitigating actions can be prepared.
You can see how many transfer points there are in the hazard reporting procedure where information can be entered wrong, formatted wrong or lost. Not to mention the time it takes that information to get from site and into the hands of the person who needs to make a call on the hazard.
By the time it gets there it might be too late and an incident or event may have already occurred.
So how can digital tools help? Quite easily actually.
We're going to have a look at a good hazard reporting procedure which enables the flow of real-time and standardised information every day. And the procedure will be broken down into the four (4) core phases of hazard reporting: capture, organise, track and share.
Capture
The first part of almost any hazard reporting procedure is of course to 'report' the hazard, which involves capturing or documenting it.
In most industries where these hazard reporting procedures are critical (construction, mining, oil and gas, forestry, manufacturing), most hazards are found in the field or on site.
There aren't too many hazards identified in an office setting, but there are hundreds on site where big and heavy machinery, large open trenches, power tools and other inherently dangerous activities are ever-present.
When it comes to the capturing phase of your hazard reporting procedure, you'll want to enable your workers to document hazards on site as well as in the office. You can do this by giving them access to a cloud-based software like Dashpivot or dedicated hazard identification tools.
These tools enable you to build digital versions of your hazard reports and customise them to suit your needs. You can deploy these digital forms to different workers working on different projects and teams, and they can simply open the report which has been built for them and capture the hazard.
They can easily fill in the form, take and attach photos and videos directly to the form and build a full picture of the hazard directly on site. The minute this record is created, it is automatically and instantly synced to the cloud where it is stored securely.
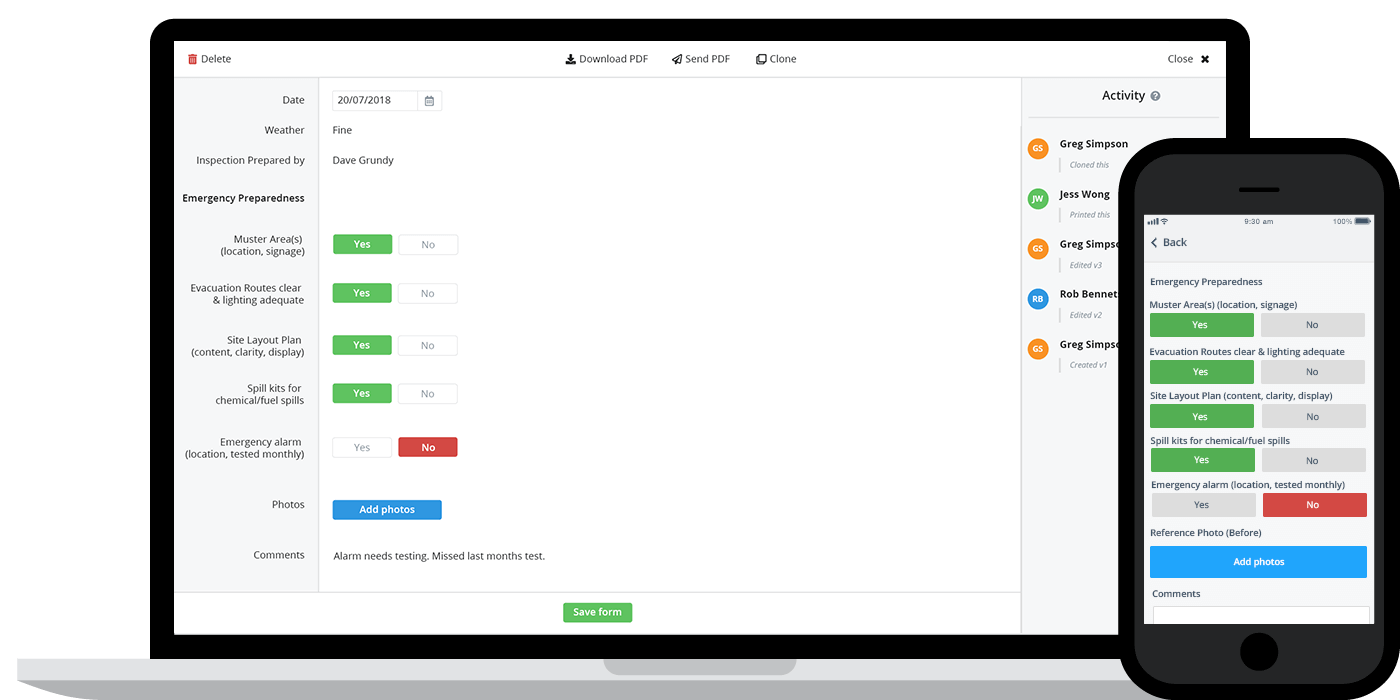
Organise
The next phase of the hazard reporting procedure is critical, and it is where a lot of the wasted time and hazard reporting mishaps take place.
Organising all of the information being captured and collected out on site can be overwhelming, but it can be streamlined and improved through the right procedures.
Many of the problems associated with this phase of the hazard reporting process are solved when the capture of information is standardised through a digital tool. This means that all of the information is also standardised and doesn't need to be re-formatted or manipulated.
The other main part of the mechanics behind any hazard reporting procedure are the workflows and flowcharts behind these processes.
Many of these can also be automated through digital workflows using a hazard reporting app or similar tool.
For example, as you can see in the example below, a hazard identification workflow is automating the escalation of hazards. An engineering or foreman identifies a hazard and signs it off for 'approval', the project manager then gets an instant notification and can sign it off if no action is required or create a new corrective action.
While some companies use posters and sheets to identify their hazard reporting flow charts, companies who take advantage of these systems can build these flow charts into their processes so that they can guarantee that their hazard reporting procedure always follows the pre-determined flow chart and remains compliant.
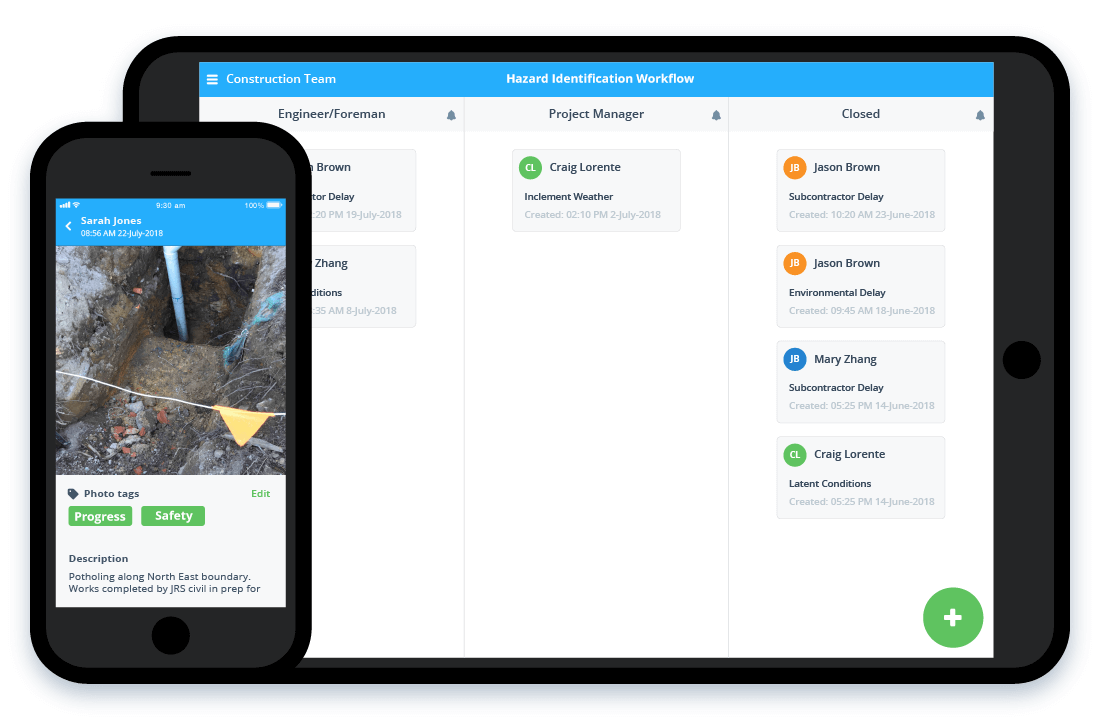
Track
One of the main challenges associated with any hazard reporting procedure is making all of that information digestible and actionable. All of the hazard data in the world isn't valuable if it can't be aggregated and organised in a way to give real insights which can be actioned.
The best format for digesting and understanding the information being collected and aggregated during your hazard reporting procedure is a dashboard.
Dashboards give you a high level view of your data which enables you to make sense of it and drill down into specific analytics charts and hazard outcomes.
A good example of the 'end goal' of information aggregation during this hazard reporting procedure is below.
This specific safety dashboard has example charts for the number of hazard reports which have been documented as well as the outcome of those hazard reports. In this case, this tool is automatically aggregating all of the data being collected during the capture and organisation phases of hazard reporting.
The person controlling this dashboard has then setup some specific dashboards and charts which are designed to give them insights into these two hazard KPI's.
The person controlling this safety system could also dive into the number of hazards on specific sites, the number of hazards identified by each person and other findings. They can also spot trends and anomalies way before what was previously possible.
Instead of spending hours and hours sifting through excel dashboards, the project manager, safety manager or person accessing these dashboards can get the insights they need to make informed macro and micro decisions about what needs to be done to reduce hazards and reduce incidents.
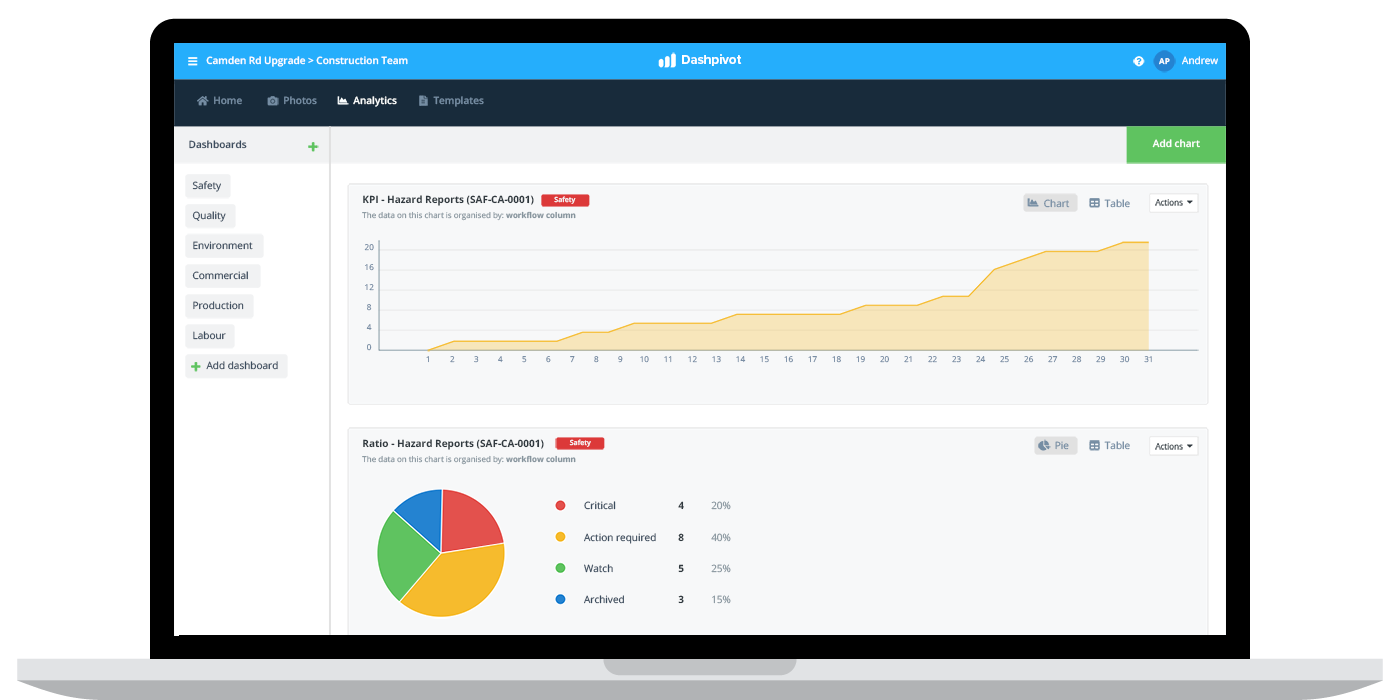
Share
The last phase of most hazard reporting procedures is a phase which is only engaged with when required. For many minor hazards, it's not necessary to share the record or hazard with anyone other than the point of contact or dedicated person on the hazard reporting flow chart.
But when a hazard is urgent or dangerous, it may be necessary to escalate that hazard report to a project director, specific project manager, or even an external party.
With the right hazard reporting procedure, you should be able to generate a PDF or CSV report of any or all of your hazards. This report should be properly formatted, and describe the hazard in good detail with all of the required record keeping information - as you can see below.
It's also critical to be able to share any of these records in the event of an audit or incident investigation, where people are going to want to know how this incident eventuated, and whether the hazard had been properly identified and documented beforehand.
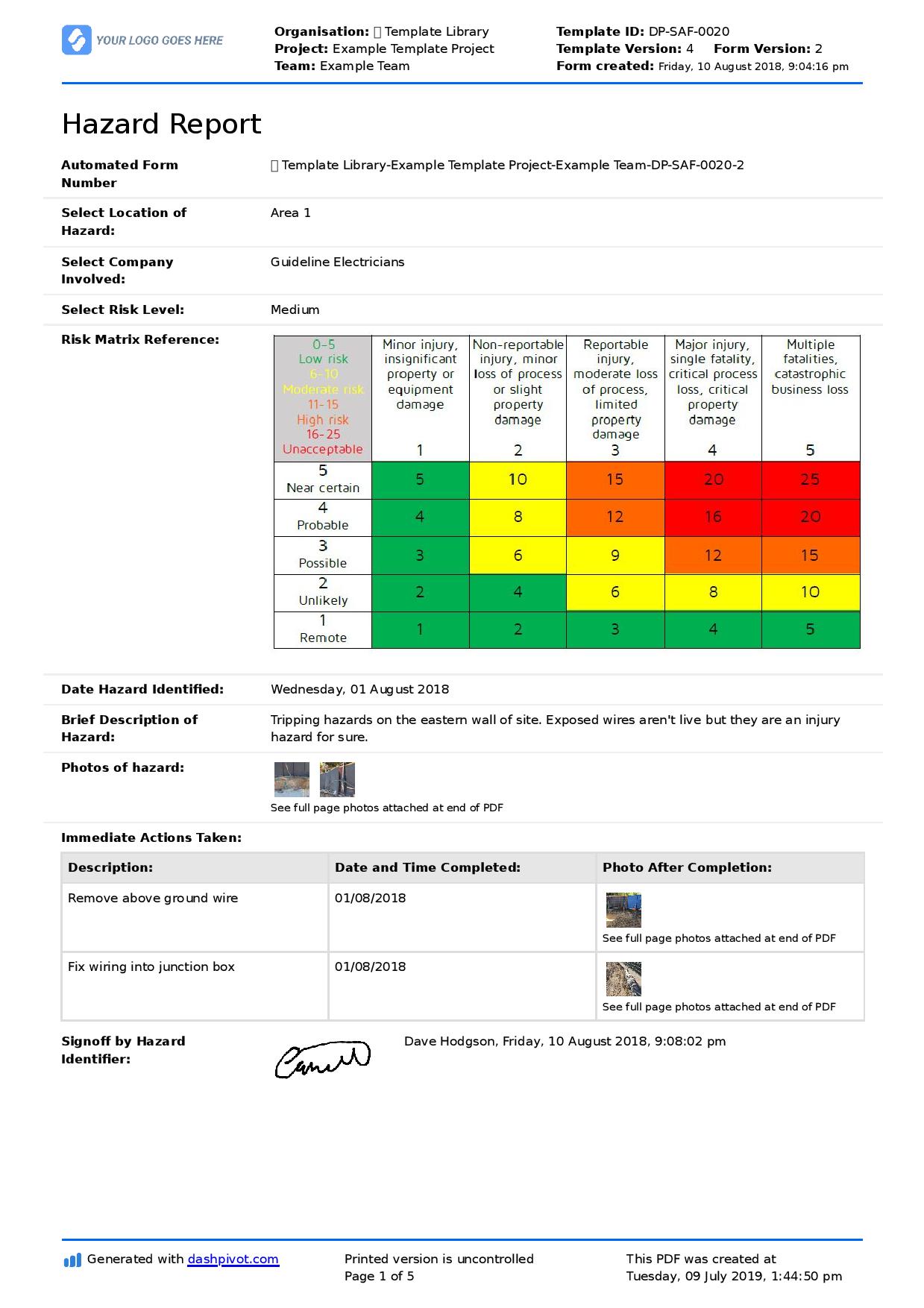
Use this hazard reporting sheet for free now.
Implementing a better hazard reporting procedure
Implementing a better hazard reporting procedure can feel overwhelming at the best of times. Ripping up your old and tired processes is probably what you want to do, but implementing a new system and new hazard reporting procedure can be difficult.
There's the friction associated with changing the procedure at the site level - where workers are used to doing things 'the old way', and then there's all of your existing hazard information which has been accumulated and stored over the years in accordance with your old hazard reporting procedure.
The best way to implement a new hazard reporting procedure is to try it. The time, cost and risk-savings associated with moving to an improved hazard reporting procedure are known and worth it.
Starting on a single project or with a specific site is usually the best approach to getting started with a smarter approach. This way you don't have to overhaul your entire workforce and implement holistic change; instead, you can pick one of your projects or teams, see how it's received, generate some good will and then expand it onto other projects and teams.
Every site and every company will eventually be managing their hazard reporting procedure with tools like this, and it will be even smarter and more automated than it is today.
The standards of safety compliance will continue to increase as human error is removed from the hazard reporting process and as manual data entry is no longer a friction point or bottleneck for capturing any kind and severity of hazard - and you don't want to be playing capture months or years from now. Getting your systems in line today will ensure you remain ahead of the game.
Hazard reporting is a critical safety process, so make sure that your hazard reporting procedure does it justice.
People in 80+ countries use this safety software to easily build smarter safety processes and procedures.
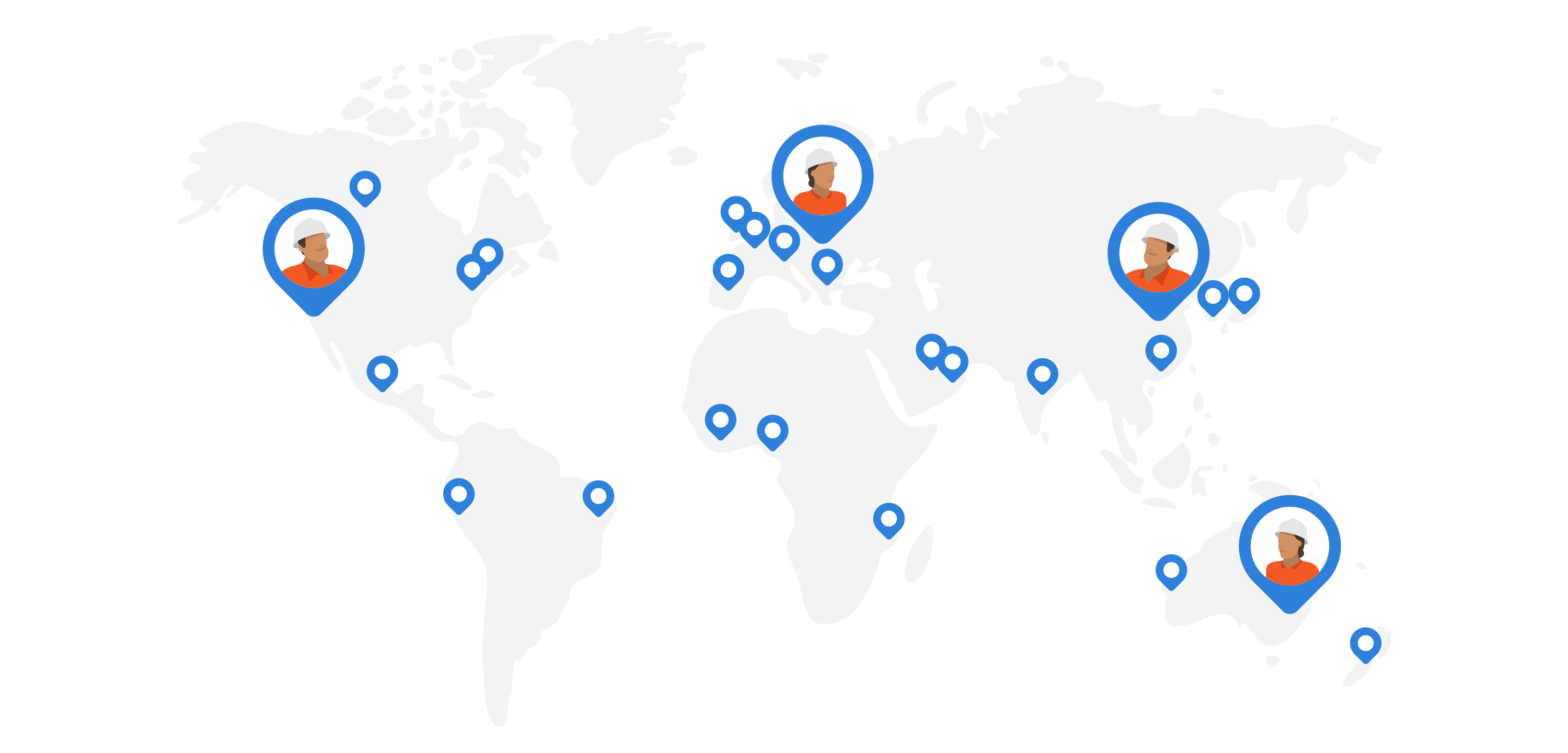